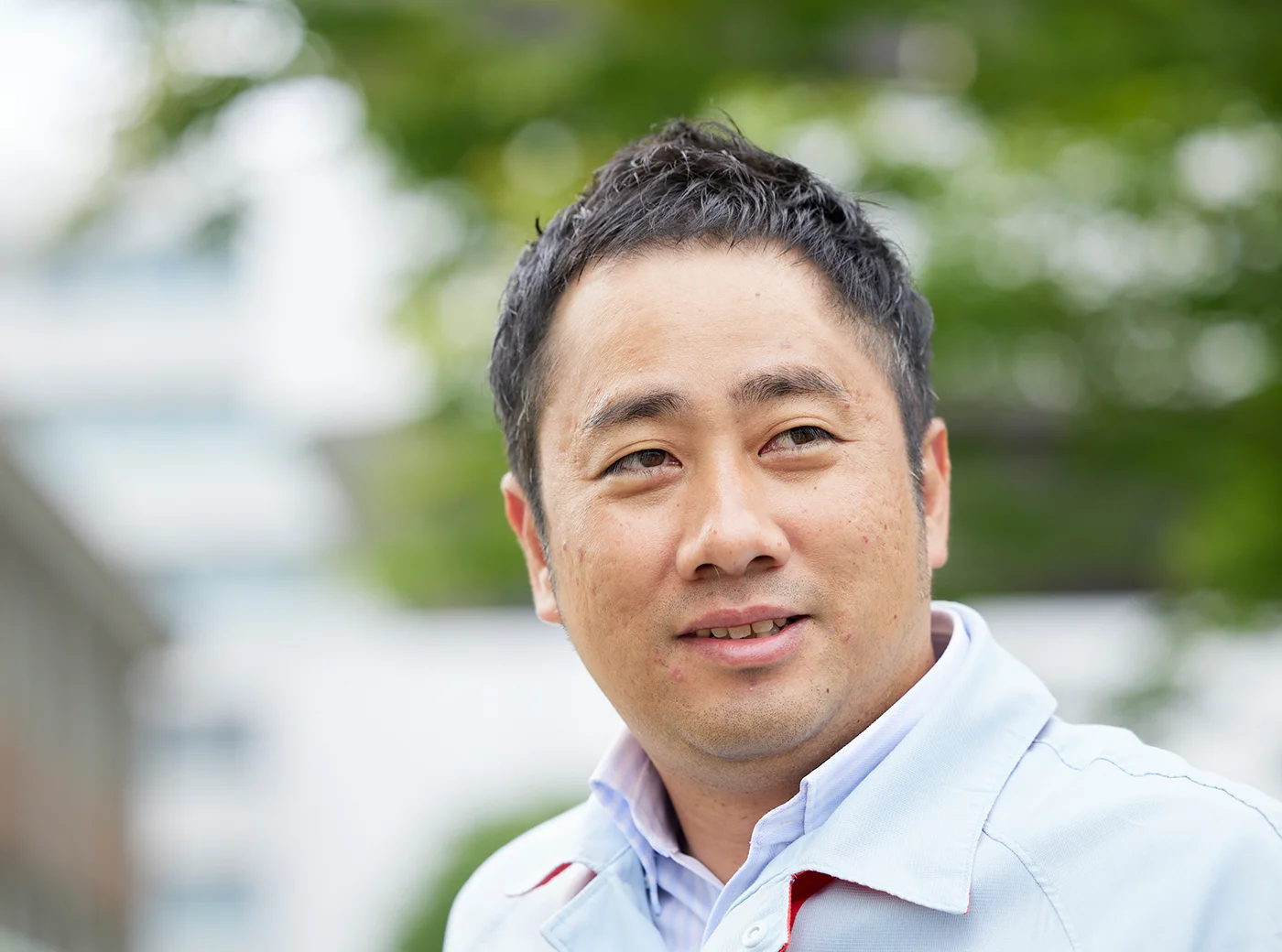
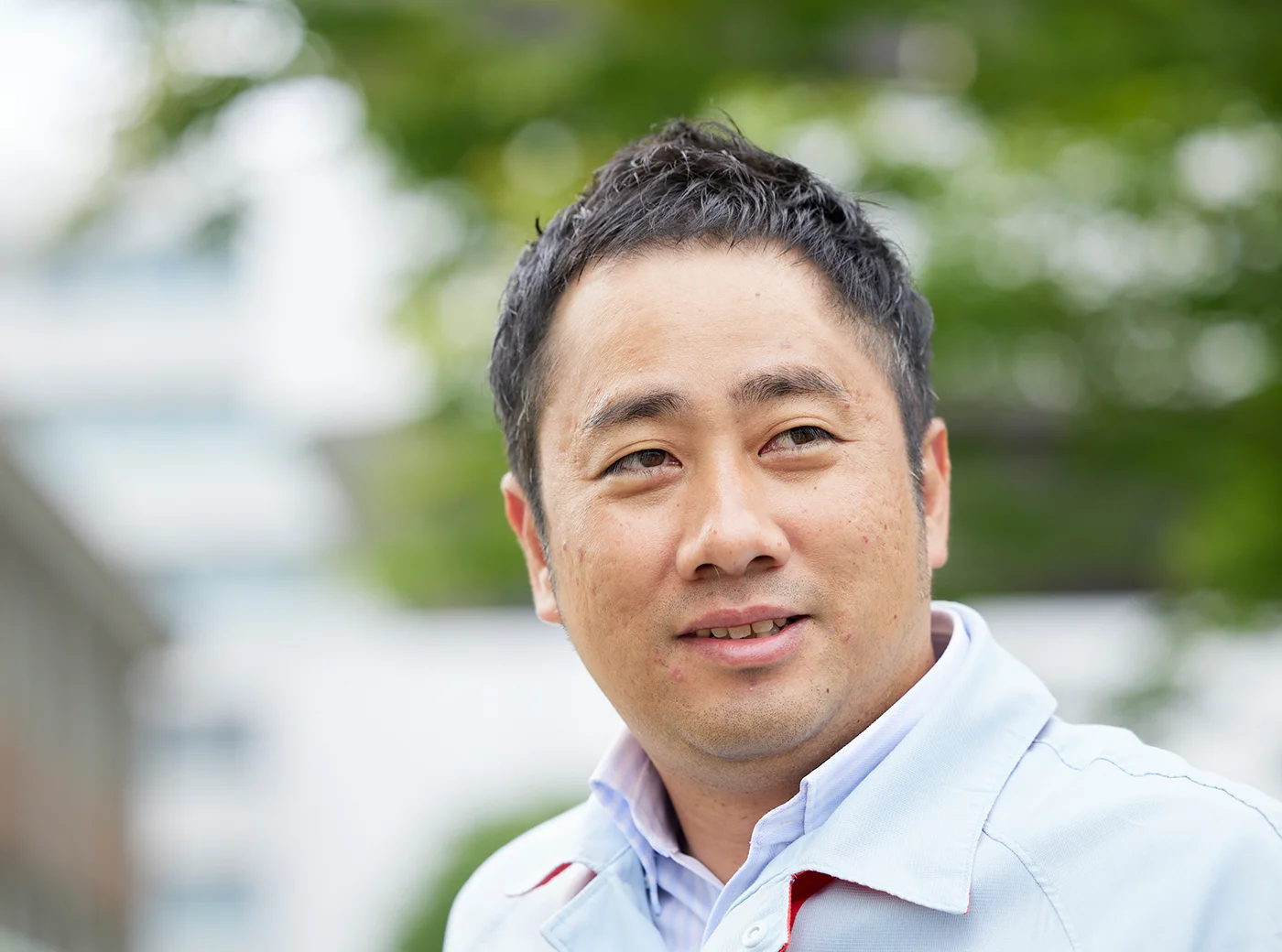
Feb 27, 2024
CAREER & LIFE“Even one out of 170,000” is an important piece to support DENSO.”
Leader's belief in improving on-site productivity through communication and listening skills.
Parts for internal combustion engines are on the market and support society. While electric vehicles (EVs) are surging, some of the manufacturing lines are required for optimization of the resources they are provided with. Hiroshi Uchino, a member of the Operations Management Development Div., says refocusing the spotlight on site is key to facing this challenge.
What is Uchino looking ahead to as the future for DENSO?
Contents of this article
Aiming to improve their productivity by focusing the spotlights on sites
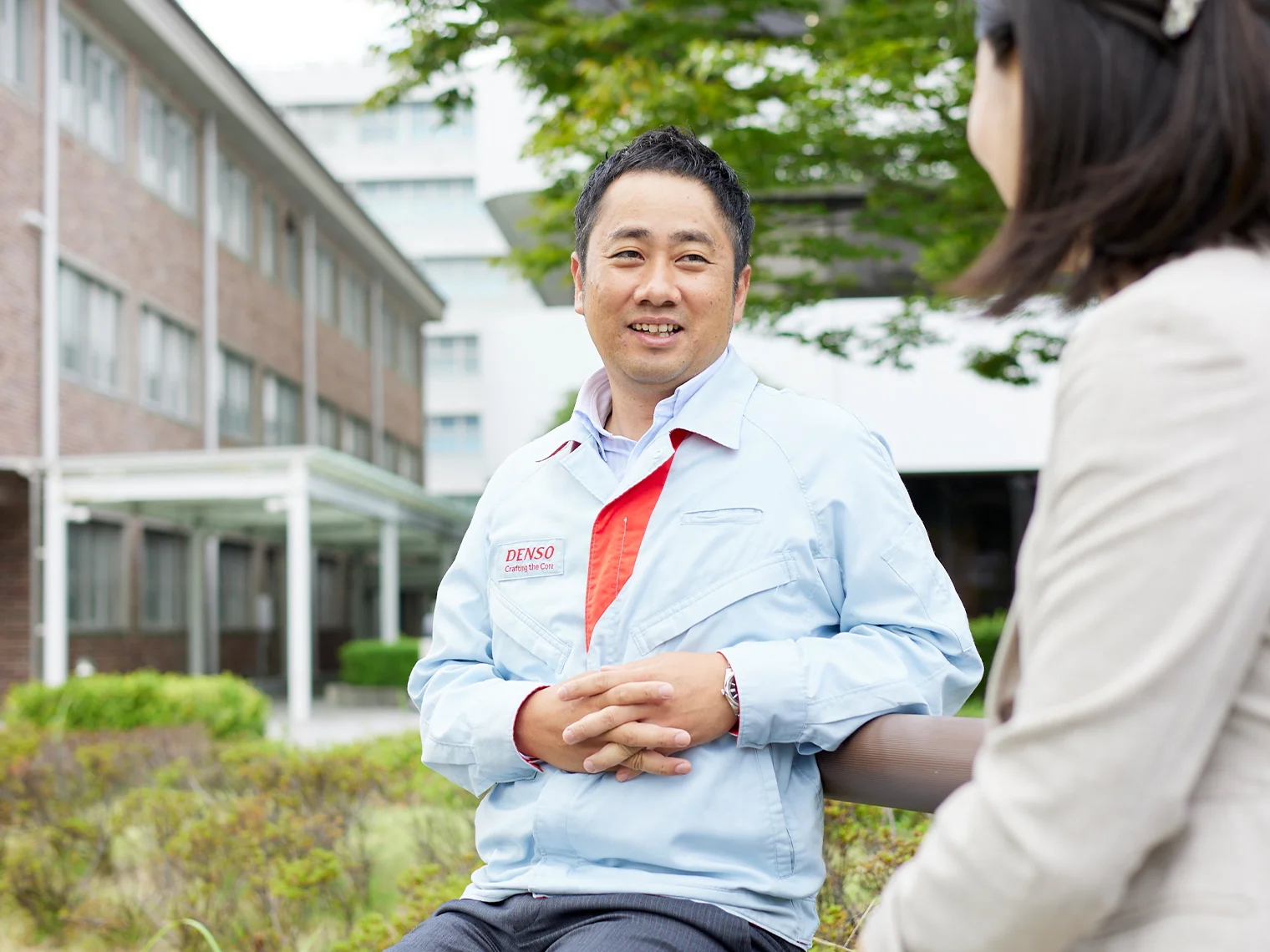
── First, what are you currently working on?
We are promoting “A project to improve output in a short period” for nearly 100 manufacturing lines that are struggling to improve their productivity. As a professional group for productivity improvement, TPM(Total Productive Maintenance)Innovation Dept. of Operations Management Development Div., of which I am the general manager, works together with on-site members of each line to improve their productivity and shorten lead times by efficiently handling all the resources involved in manufacturing, such as associates, machine, products, and information.
But we are not looking for temporary results. Although the duration of the project is limited to two years, the final goal is to create a base on which the manufacturing line sites can improve their productivity on their own.
──What is the background of launching this project?
Productivity is originally an endless theme for us. Our mission is to achieve high quantitative and qualitative output with a small number of associates.
We work through trial and error daily so that on-site members can strive to improve their productivity on sites that are always operating at full capacity. For example, if a machine breaks down, many manufacturing lines cannot take time to analyze the cause of the breakdown and prevent it from happening again. If the cause of the breakdown is not identified and addressed, the same thing may happen again.
To avoid such a situation, we support the lines because we have the expertise to help on-site members improve their productivity.
── So you are the professional group that supports the manufacturing site. What kind of manufacturing lines are targeted specifically?
We are particularly focusing on the manufacturing lines of internal combustion engine products. As the shift to EVs accelerates, some of the manufacturing lines for internal combustion engine products are due to be transferred or downsized, making it difficult to make major capital investments.
But thinking about the needs of the market, they are still in high demand and an important field that supports DENSO today. We have established a system that can improve their productivity without significant capital investment, and we are working towards stable operations with high quality.
──We heard that the members who work with you are assigned from various divisions and have different skills. This object-type of team formation is quite rare in DENSO. Can you tell us about the background behind the creation of the team?
One year before the current team was formed, we created a team of about 10 in-house experts to improve output at lines that were struggling to improve their productivity in two manufacturing divisions (hereafter, struggling lines.), This team is the predecessor of TPM Innovation Dept. of Operations Management Development Div., which I lead currently.
While I was being assigned in India and Thailand, I had the experience of working together with a small group of people with expertise. We improved and learned from each other to achieve a single goal.
After I returned to Japan, I meant to work on the improvement of productivity by collaborating beyond the frame of departments/divisions, functions, and businesses.
Meanwhile, I consider myself lucky to have such great opportunities and fellows as we managed to achieve certain results even though we started small. Based on the achievements, we established the current team in June 2023, which has increased its number to 50 to expand the target lines.
Showing “my true self” gave me positivity
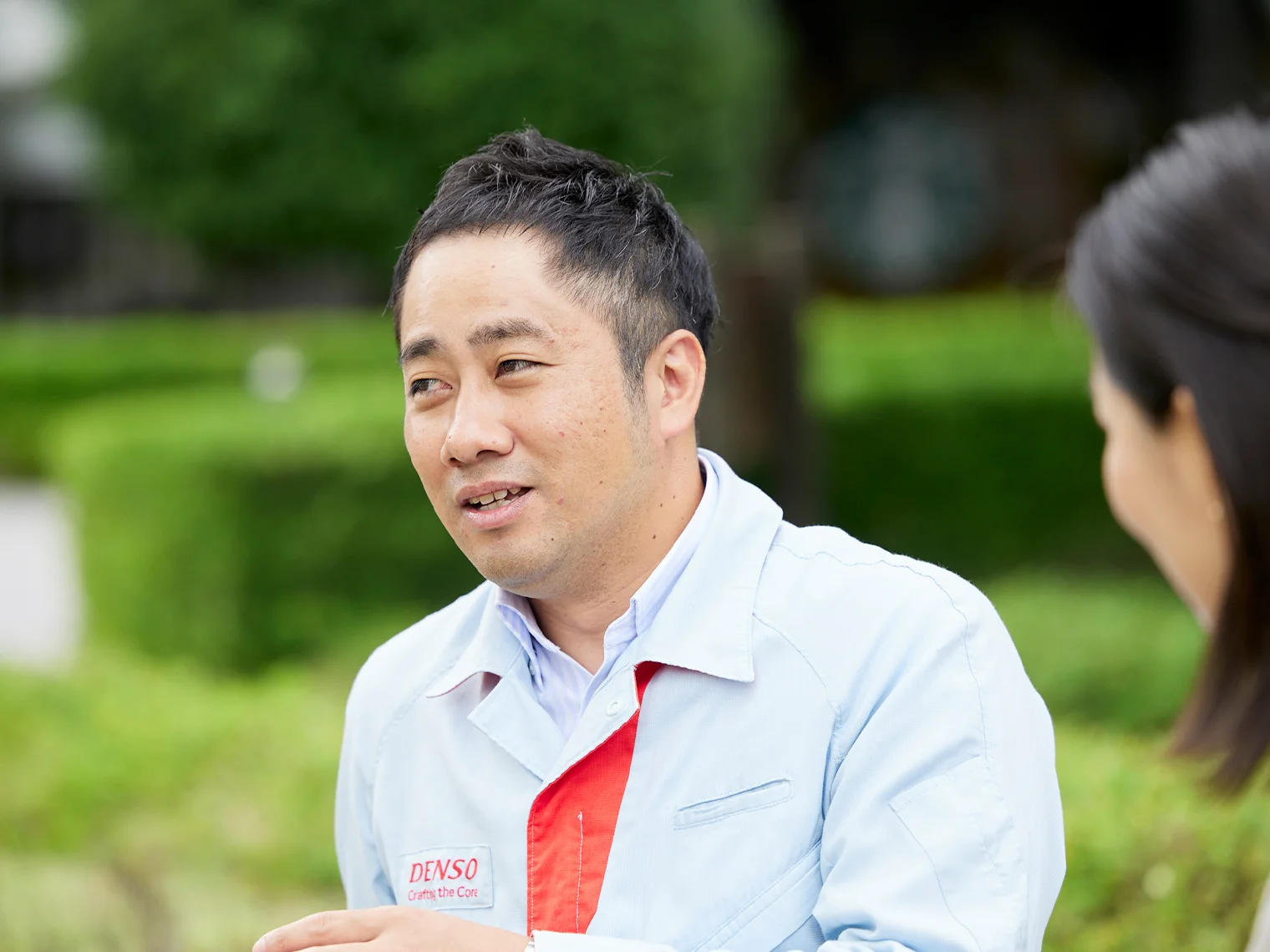
──Coming up with a project and creating an object-type team is inspiring. You seem very positive as a leader. Have you always been positive or was there a turning point that made you positive?
Originally, I worried too much about the atmosphere and carefully picked words to say. Because of that, there were quite a few moments when I could not say what I should say or express my intention clearly. In such a situation, I took internal management training. During the training, an instructor said to me,
"Uchino, you are taking the safe way.”
I thought, "Oh no, I have been exposed."
He saw right through that I always defended myself, searched for words that people wanted to hear, and chose bland answers. I knew this myself, but it was the first time that someone pointed it out to me. The words hit me, and I felt myself burning with shame. I thought that people would get hurt by what I said if I showed my true self and something negative would come out by doing so. But I was afraid of myself being hurt.
During the training, I was reminded of the words repeatedly, and I concentrated on working with my weaknesses, I tried not to be afraid of expressing myself. In the second half of the training, I could have a real discussion with other people by showing my true self. I had no idea what I had been afraid of. I realized that what I was worried about was very small things.
After the training, I could see myself changed and started to act positively to things.
Of course, I have had more conflicts with people than ever, but I have noticed that things move forward better in the end.
Each member is an important piece of DENSO that can make changes for the better
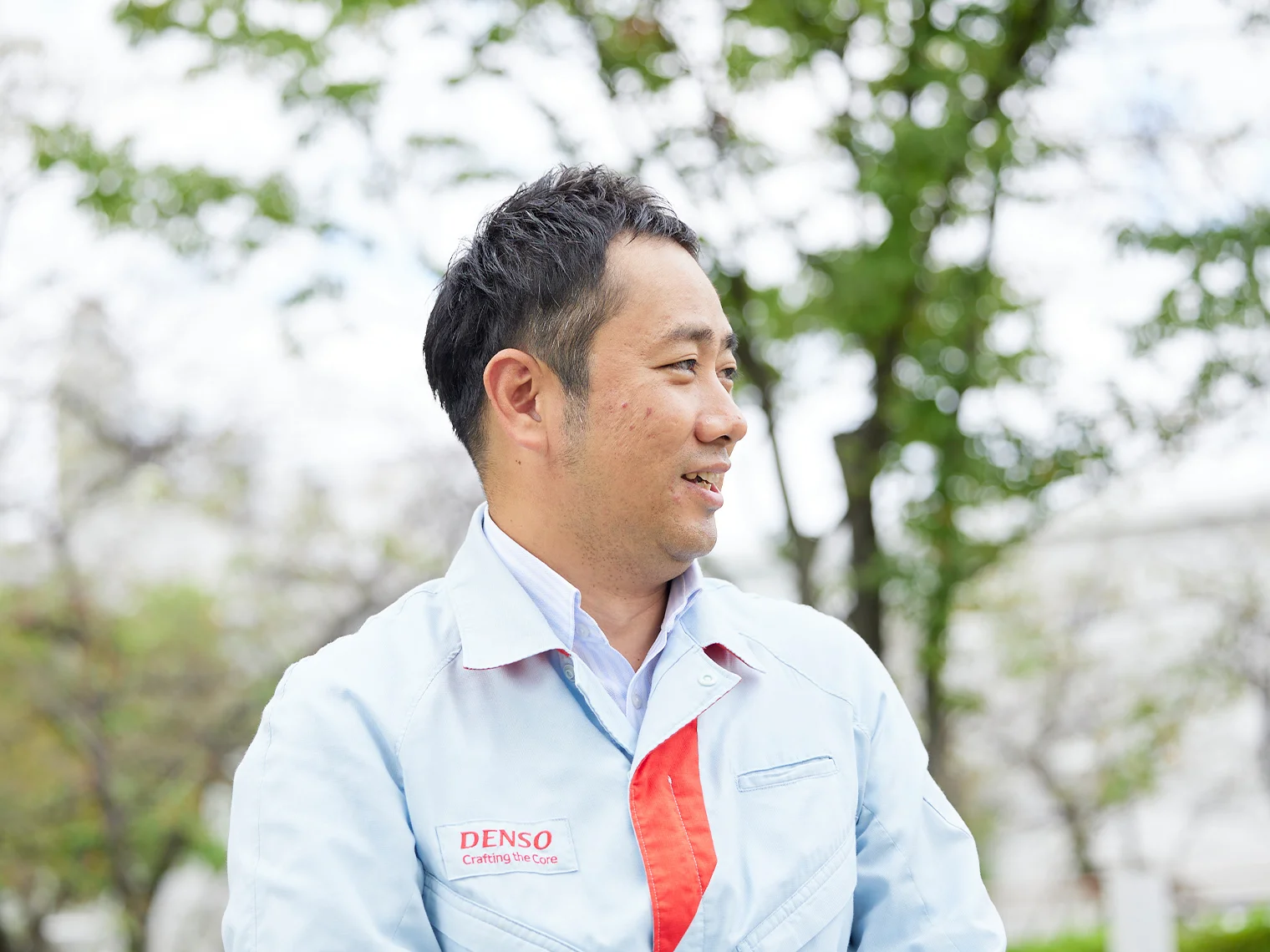
──What was the process that led you to start the project from there?
Through the training, I learned that we could aim higher by not letting our feelings go unchallenged and by having the courage to speak up and express our thoughts about our work, even if it means going against the flow of the situation.
DENSO has 170,000 employees worldwide. In the past, I used to think very negatively about what I could do for the company being only 1 out of 170,000, but I have come to believe that I am an important part of supporting this company by thinking of myself as one of 100 or 1,000 people who also have a passion to make DENSO better.
I reorganized my thoughts about work one by one. I think that was my turning point.
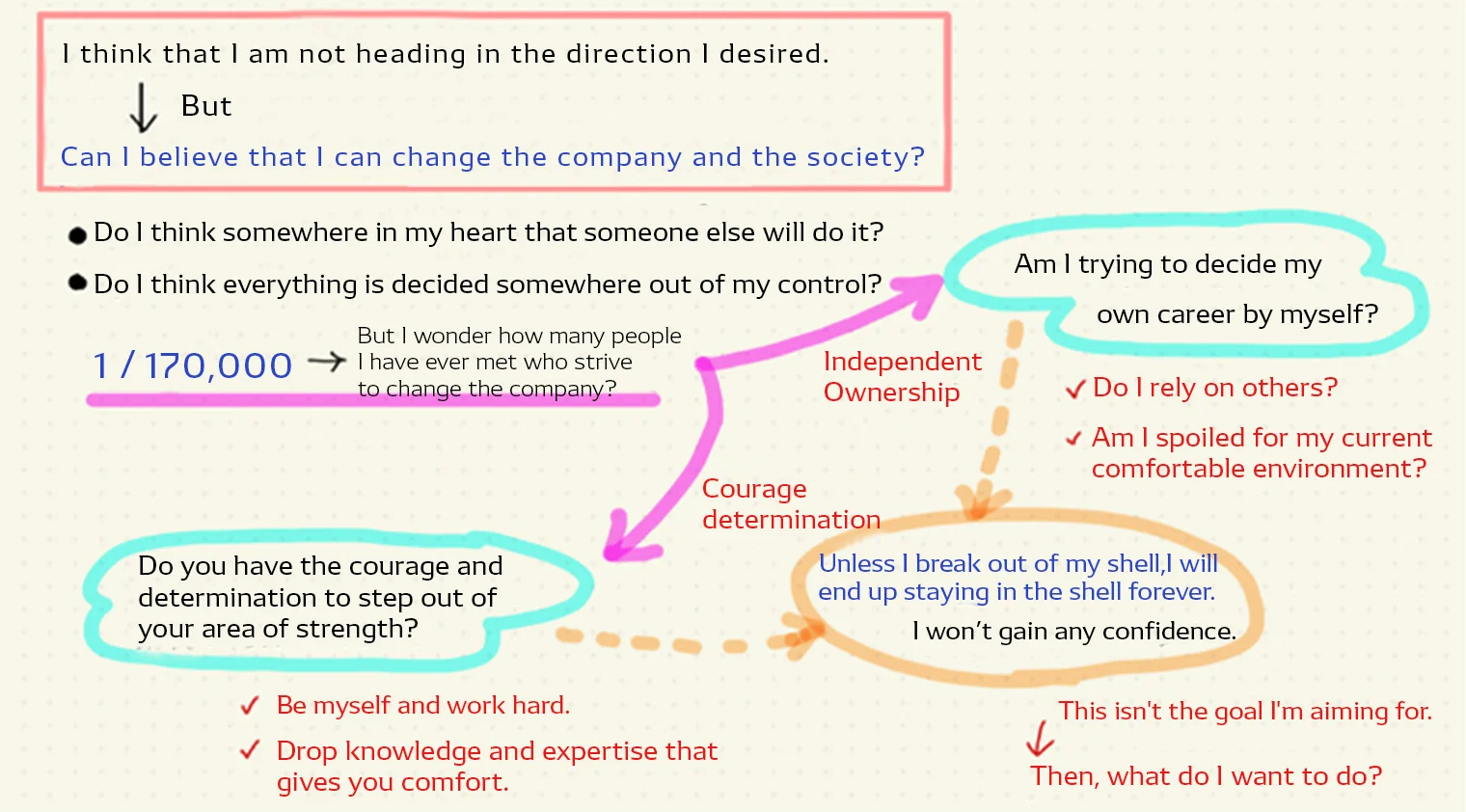
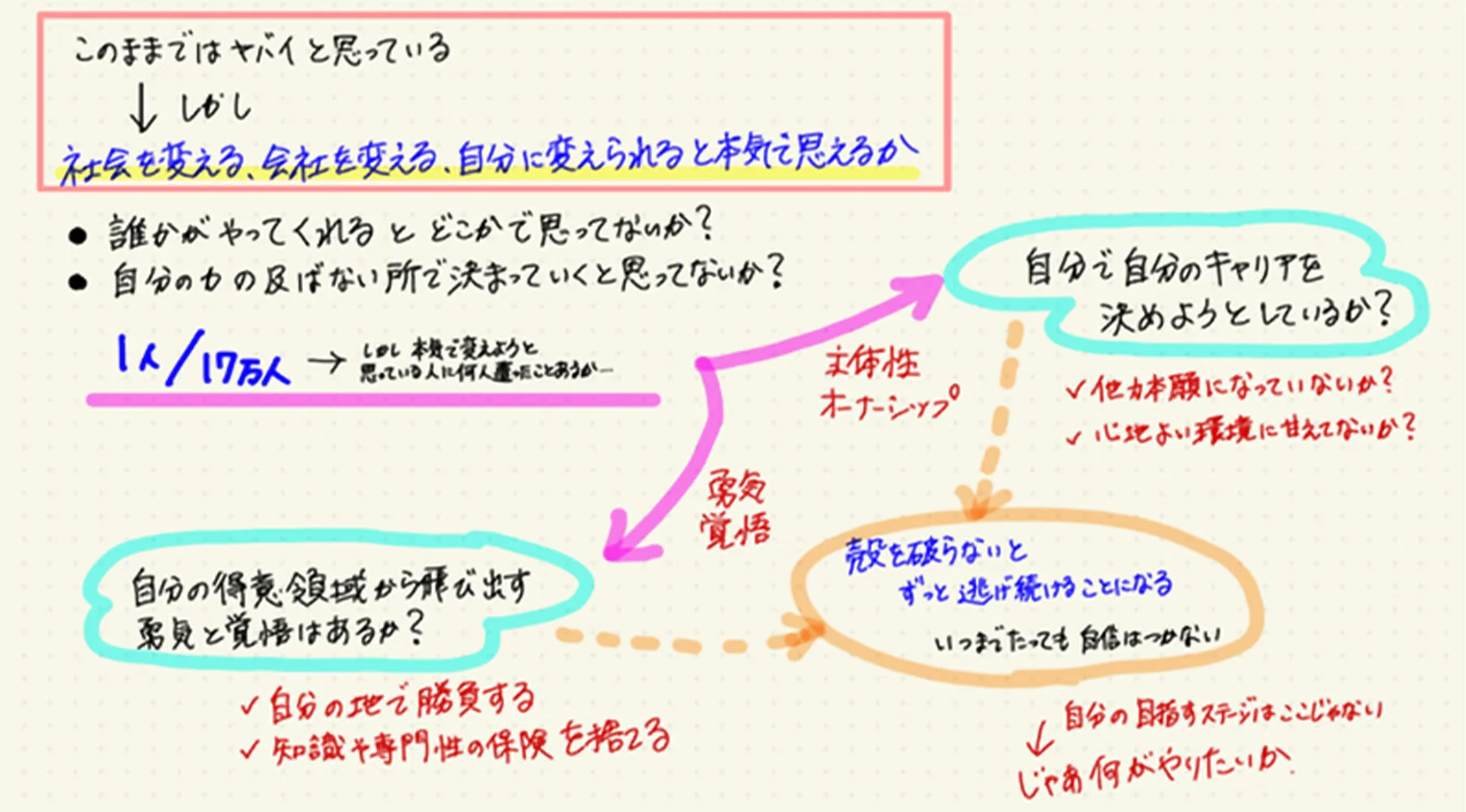
──So you gained the courage to take the lead.
Gradually, I came up with various ideas that I wanted to try out and I became more motivated and proactive.
Then I told the division's director and executive officers, "I would like to take the lead in improving the output of the struggling lines if the company can approve the project. I want to take the initiative to scale up this project."
As a result, my passion and energy were acknowledged, and the project was approved.
The best members needed for this project were assigned and the department has been established.
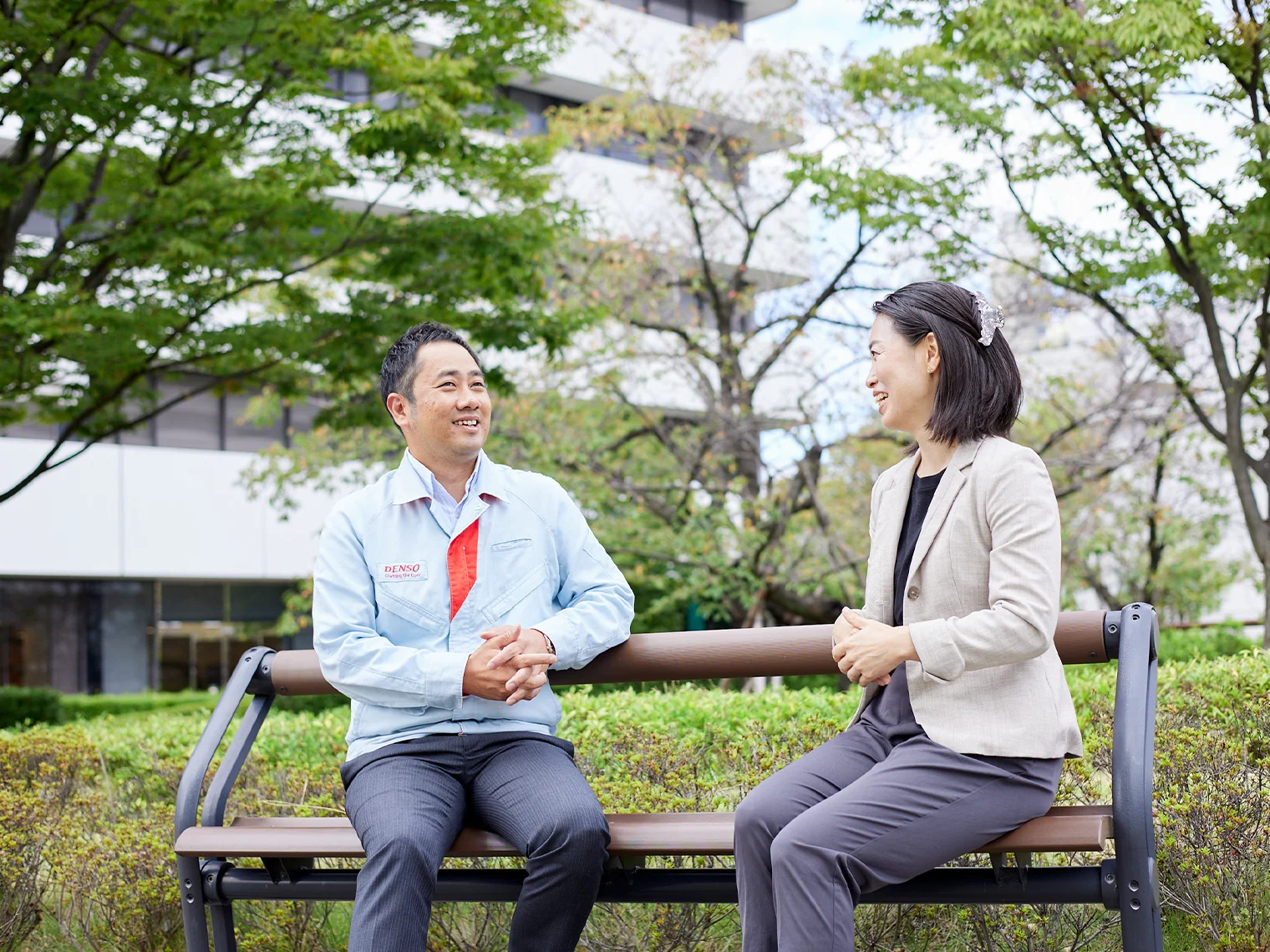
──Do you feel that you are making the most of the courage and passion you have in the current team?
Yes, tremendously. The team I lead improves productivity by focusing on machine improvement, but I have no practical experience in machine improvement, such as machinery and tools, production engineering, and machine maintenance.
I think I lack the knowledge and experience the most in the team.
If I had been my old self, I might have pretended that I knew everything because I used to be very conscious about my position as a general manager of the department. But now, I can admit that I don’t know what I don’t know and ask for an explanation.
Some people might think, "Doesn’t he know such things?" But I’m afraid of making the mistake of judging in a critical phase by pretending to know what I don’t know.
As a general manager, I believe that it is important to create a base that maximizes the potential of our members because we have gathered excellent members from various fields by adopting object types.
The courage to “doubt the obvious” will pave the future for DENSO
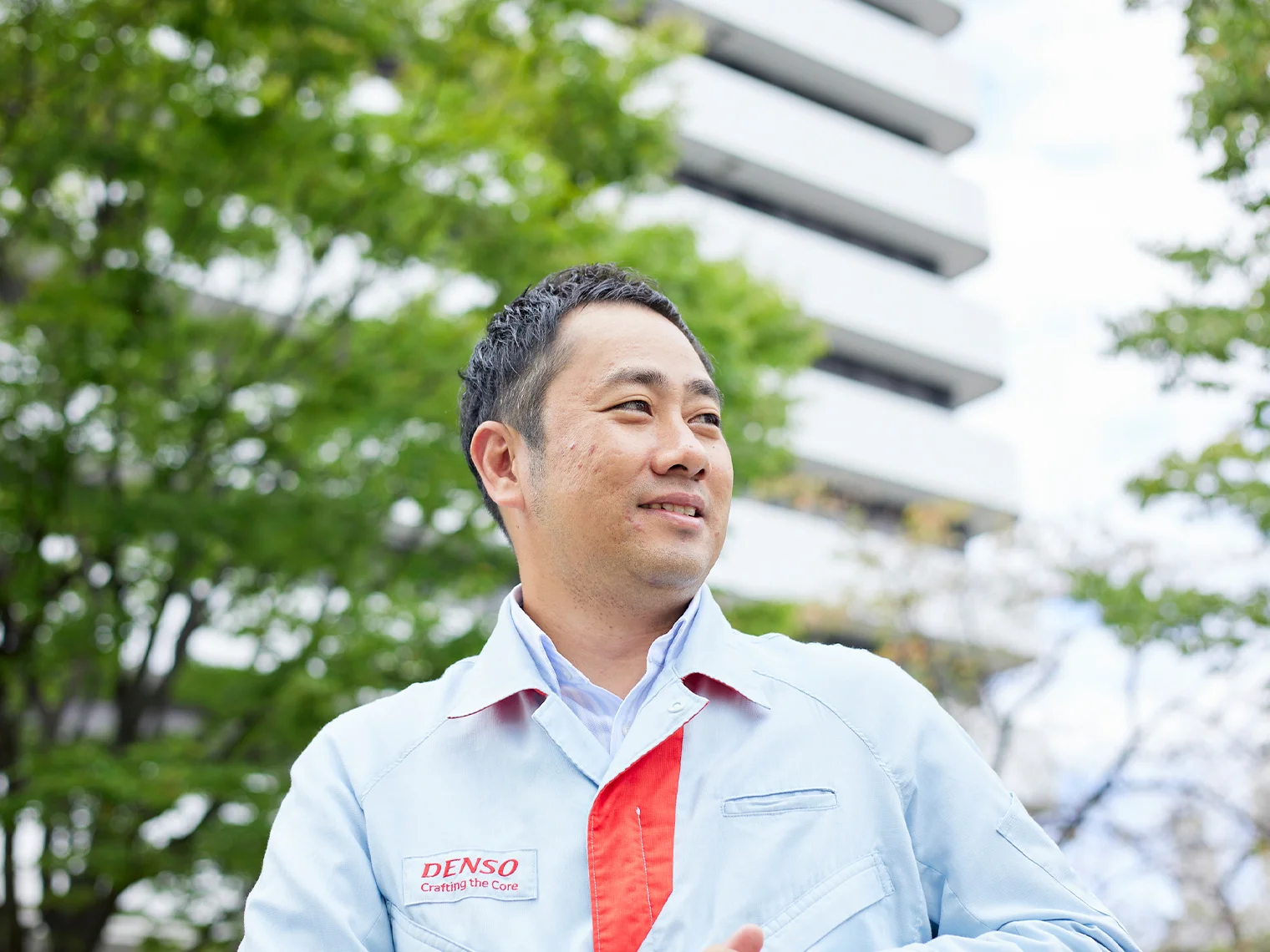
──I think the team has just been launched. What do you feel the challenge is to make your project successful?
Since we are currently in the phase of building a system from scratch, the project often doesn’t work well, to be honest. It is also true that some members can tackle such situations positively, while others are struggling to show their ability.
To bring everyone together, I try to take the initiative in speaking to the members, have a 1 on 1 meeting with each member, and learn their concerns or hidden thoughts they keep to themselves. I hear their thoughts and hopes before I let them know my opinions, and I reflect them on their goals.
In addition to having 1 on 1 meetings between my members and me, I also train my members to gain “communication skills” and “listening skills” to communicate with each other among my members more smoothly.
──That’s very interesting. What kind of training is it exactly?
To help them learn the ability to communicate, I hold a meeting once a month where members share topics in their areas of responsibility. Also, I encourage them to take the opportunity to speak in front of others at regular meetings with the manufacturing division.
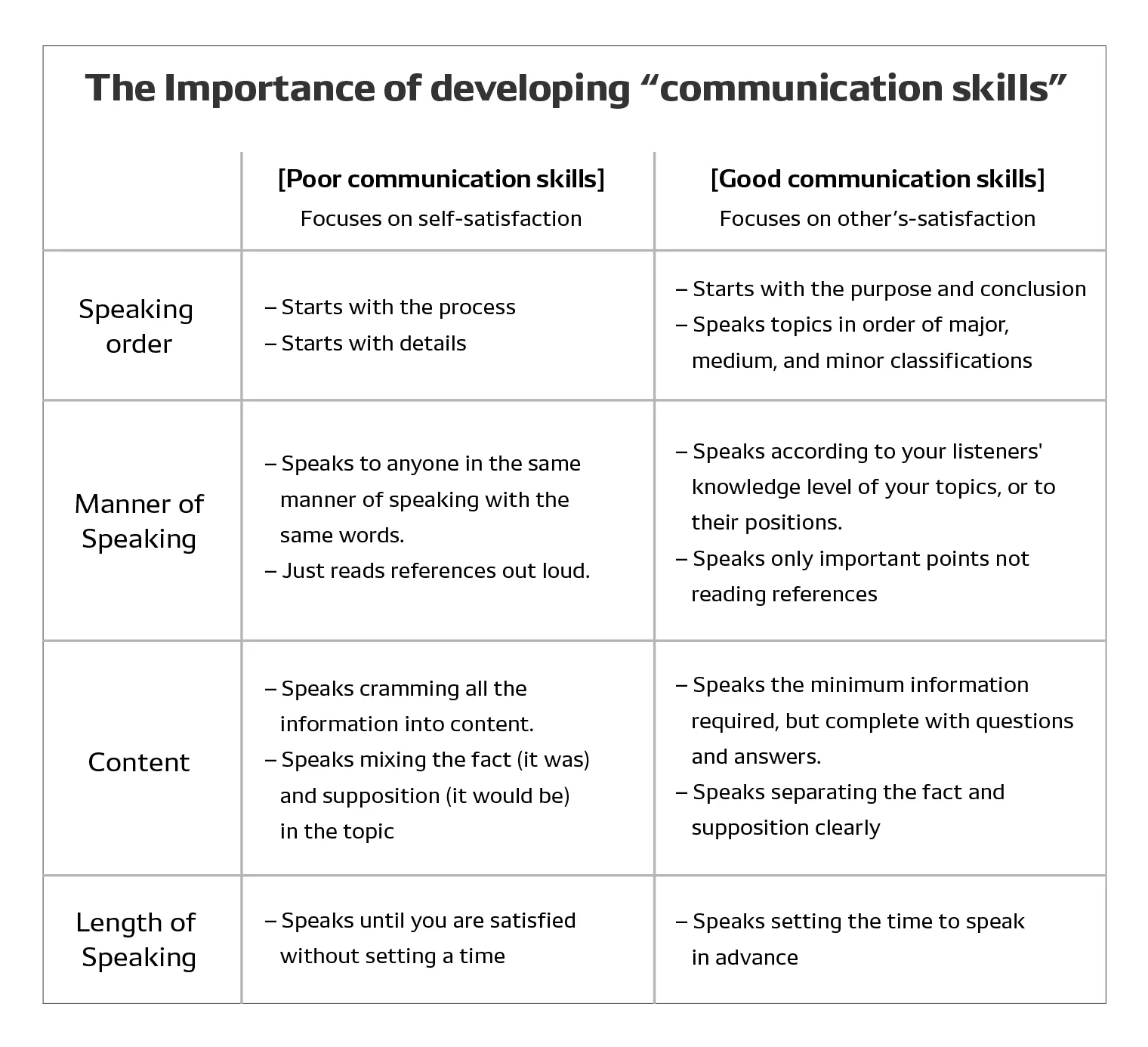
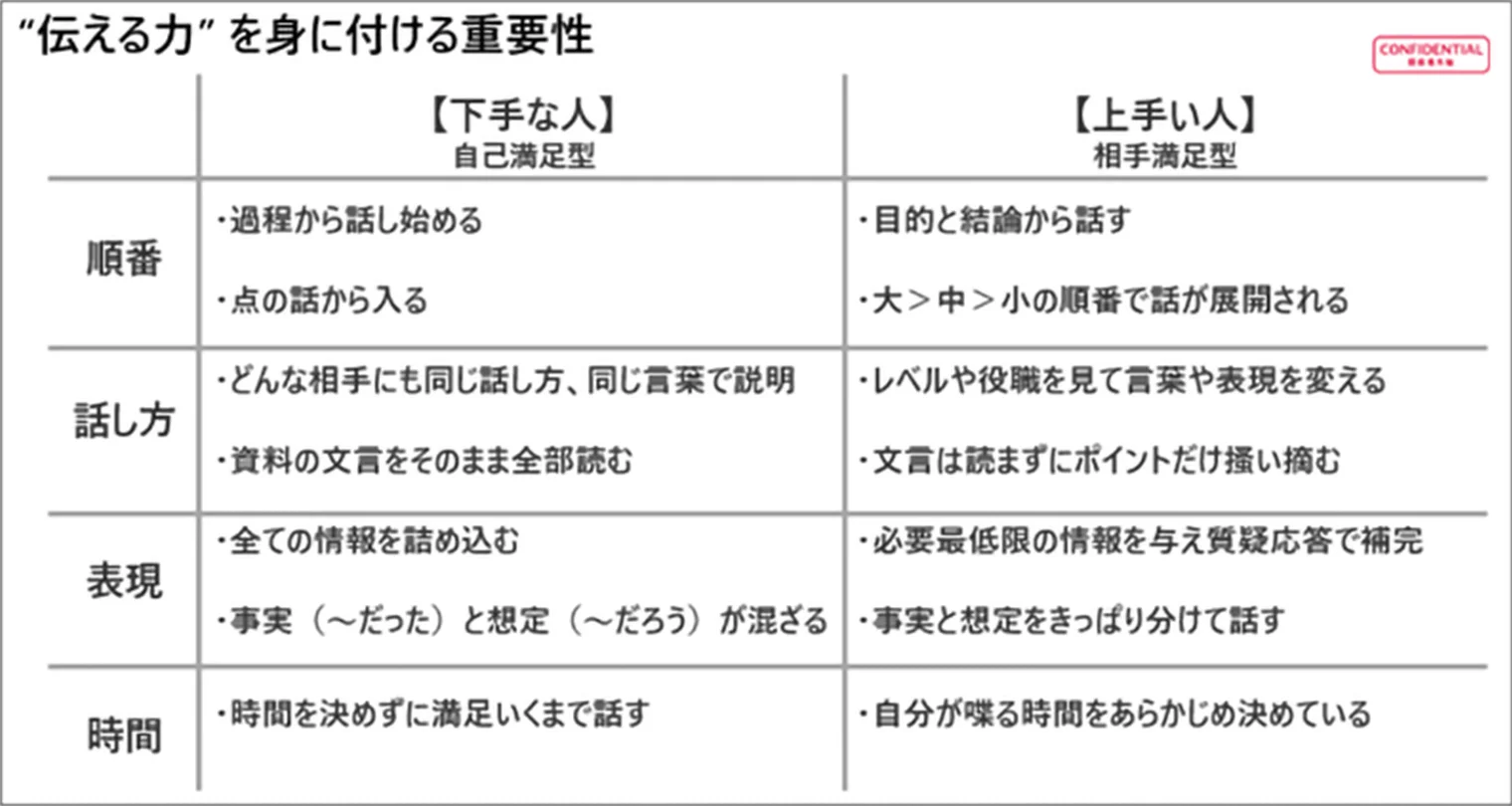
Because we are talking about a highly specialized area, only a limited number of people can understand the technical part of the machine, and those who do not understand it will be left behind without understanding. You cannot achieve your goal unless you can share what you want to realize with the on-site members you are working with.
For that, each of our members needs to develop the ability to organize his or her thoughts and communication skills for smooth communication. If they can’t communicate, they cannot improve the on-site lines or make fellows.
In addition, "listening skills", or the attitude of respecting and trying to understand others are important to improve the team. Different backbones have different justices. If we use our justice as a weapon, we will never understand others’ justice and no synergies will come from it. I believe that you will see different worlds stepping out of your own "frame" and stepping into the "frame" of others.
──I feel that the training is an essential part of not only the success of the project but also the future of DENSO. What do you think will be important for the future of DENSO?
DENSO has many excellent human resources. I believe we can show even more power when each of our specialties blends well to work towards a single goal.
To do that, each associate must have the courage to doubt yourself. Even if your justice comes into conflict with others, you should first doubt and face yourself by making a habit of thinking "I might have been wrong," or "Probably, I didn’t do it right." instead of denying the other person without listening to them.
This will help broaden your horizons and expand your relationship. Also, this may bring you something unexpected. One more thing, show your true self and don’t be afraid of telling people what you feel.
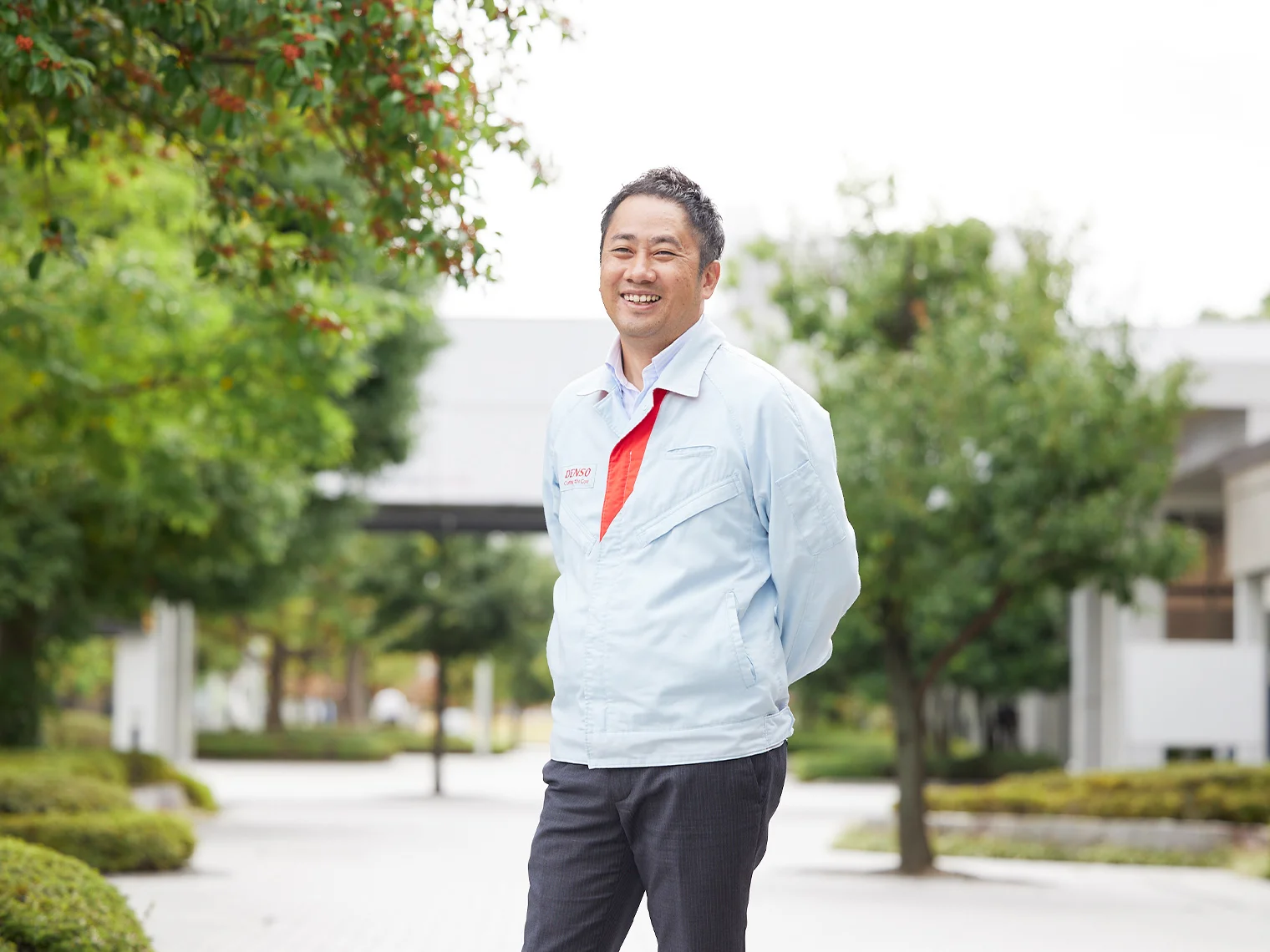
*The contents presented in this article are as of January 2024.
-
Hiroshi Uchino
Joined the company in 2003. Based on his experience in launching procurement centers and leading productivity improvement projects in Japan and overseas, he initiated "Activities to improve the output of struggling lines,", established the division to promote the activities to reform the lines, and became the head of the department. He has the personality to challenge anything that interests him, for example, he has ever lived in a village of Native Indians in Canada and participated in the M-1 Grand Prix which is a popular stand-up comedy competition in Japan.
REACTION
Changing your "Can'ts" into "Cans"
Where Knowledge and People Gather.
Leave a comment