Did you find this article helpful for what you want to achieve, learn, or to expand your possibilities? Share your feelings with our editorial team.
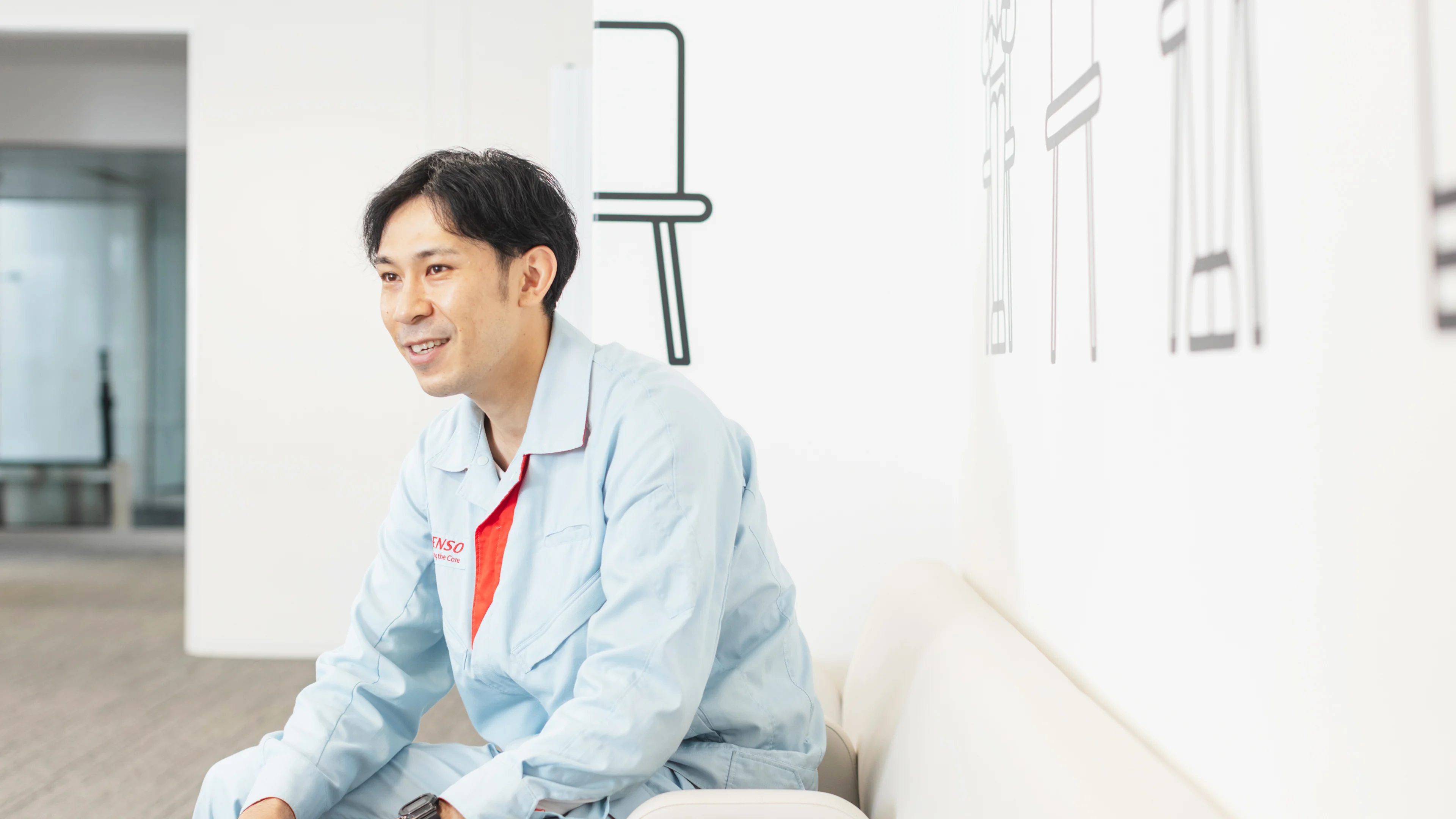
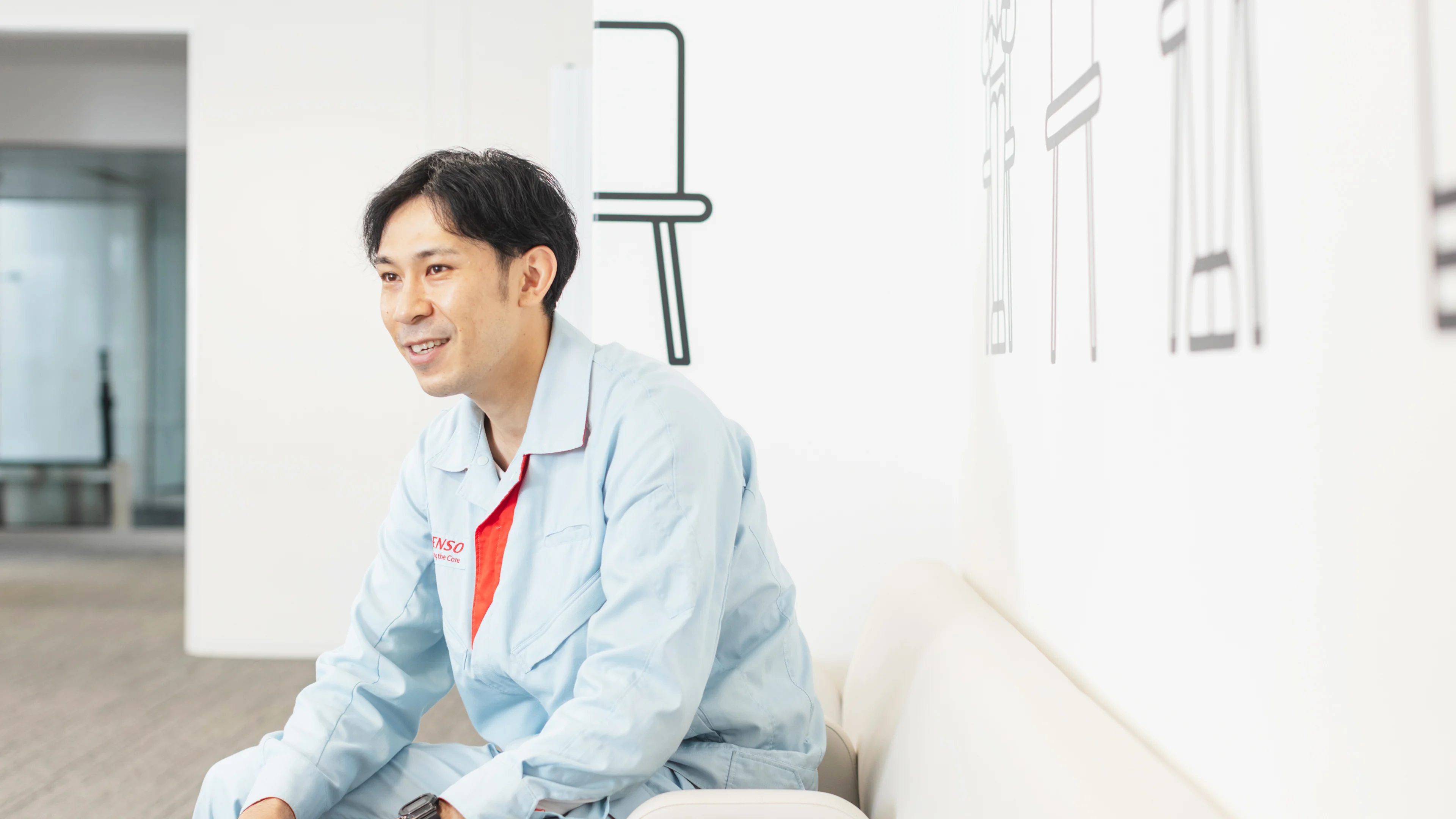
Feb 17, 2023
CAREER & LIFEProducing safety products for the whole world thinking of our families and friends
Building teams that work side-by-side as equals toward shared goals
By meeting outside of the workplace with ambitious, hard-working associates at DENSO—as well as those who just seem to be fascinating individuals—it’s possible to break down the barriers of formality and talk openly, listening to their heartfelt concerns along with their unfiltered dreams and goals.
In this “Interviews with Employees Who Get Results” series, we talk casually with a wide range of professionals at DENSO to learn what truly drives them in their work, as well as their ambitions and dreams.
For this interview, we talked with Daisuke Tanaka from Production Sect. 3, Safety Systems Manufacturing Div.1. Currently, he is involved in kaizen efforts to stabilize production-line operations of millimeter wave radar sensors for GSP3 as soon as possible.
* GSP: Global Safety Package
Since joining DENSO, Tanaka has built his career one after another in new environments, taking part in the setup and actual manufacturing operations of the production line of GSP1 millimeter wave radar sensors, and providing training support for manufacturing operations in Tianjin DENSO Electronics Co., Ltd. (TDE).
However, even amid such changes, his personal guiding principles stay the same.
As Tanaka explained, “The important thing is to adjust your perspective depending on the persons you’re talking to, whether they are my colleagues, my bosses, or overseas team members. By ensuring good communication, you can work effectively wherever you are assigned.”
He added, “It’s all for producing good safety products for the world. I try to approach my younger colleagues as if they are my friends to guide and train them.”
Tanaka brings together his inner core strengths and kindness as he continues to challenge himself looking ahead to a better future for the sake of DENSO and the next generation.
“I’m motivated to my work the most by my young colleagues’ growth.” he said with a bashful smile.
Let’s listen carefully to Mr. Tanaka’s approach to work with feeling for people close to him.
Contents of this article
Pleasure of jumping into new environment, looking ahead to guidance and training of younger colleagues and to better future of DENSO
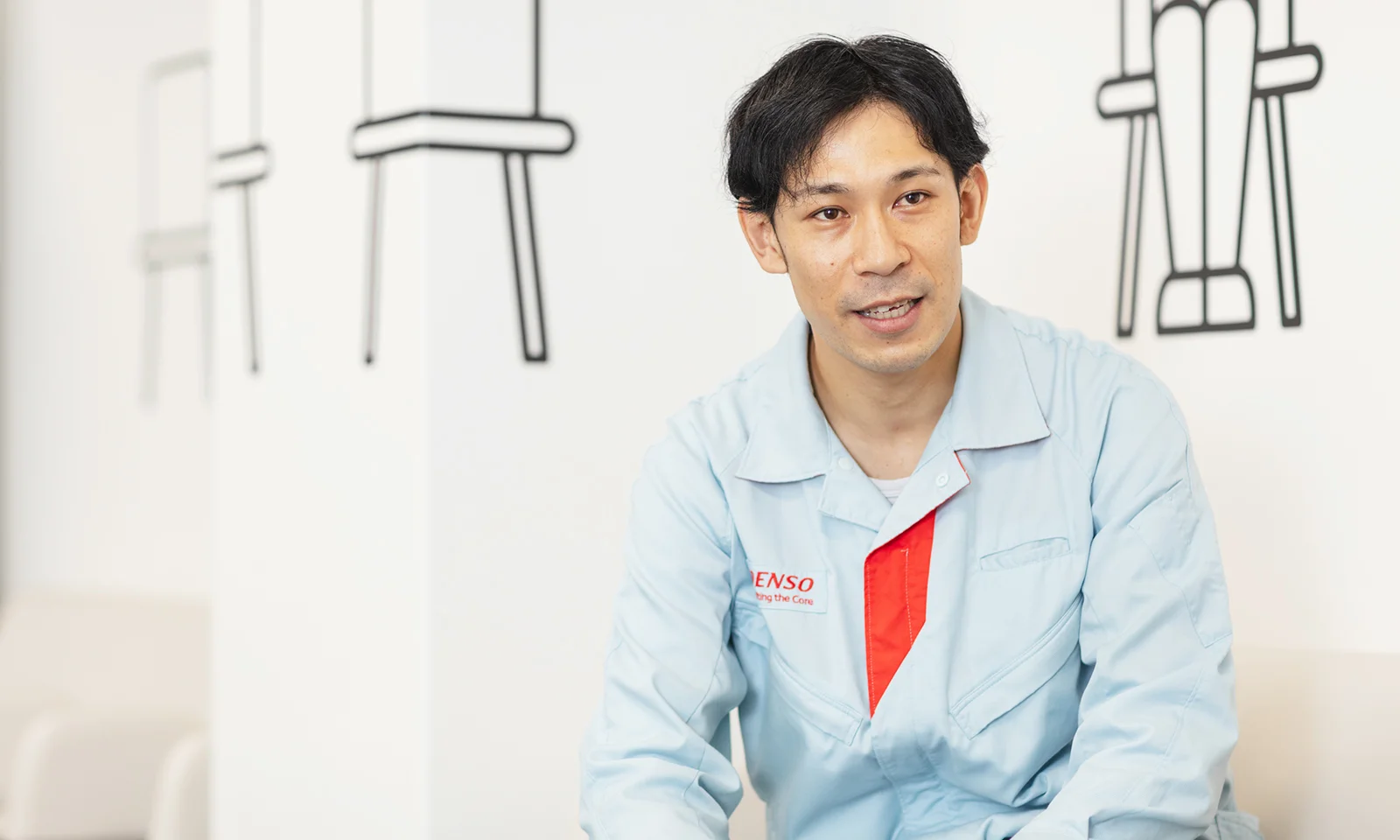
─── First, please tell me about the work you are currently engaged in.
Tanaka: I am involved in kaizen measures in a production section to quickly stabilize production-line operations for millimeter wave radar sensors for GSP3. GSP is a system designed to reduce traffic accidents by preventing collisions of pedestrians with vehicles, and preventing lane departure. GPS3 is the third-generation system. In order to make sure that this safety system can be mass-produced with high quality, I engage in kaizen operations, which include inspections and problem-solving measures, together with other departments at DENSO.
─── I hear you have experienced a wide range of roles within DENSO, not just a single team, such as production-line startup operations for GSP1 millimeter-wave radar sensors and those for GSP3 millimeter-wave radar sensors, and training support for manufacturing operations at TDE in China.
Tanaka: That’s right. I’ve had various experiences changing my environment throughout my career, starting with my assignment to the project team for production-line startup for the GSP series. It was completely different from the production operations I had experienced until then, and the experience taught me that it was fun and interesting to try new things. It gave me the chance to look at how other departments throughout the company carry out their production-line startups, and encouraged me to be more proactive in asking my supervisors to participate in a project. I began taking more initiative in my work overall.
─── What personal changes did you experience?
Tanaka: I discovered the simple pleasure of challenging myself to do entirely new types of work. I got to know that people of the departments I had never been involved with had their own perspectives to the DENSO products completely different from mine. Talking with a diverse range of people enabled me to learn many new things and expand my abilities, which I greatly enjoyed.
In the future, DENSO will probably set up more and more overseas group companies. And my experiencing overseas operations in advance will enable me to give better advice and guidance to my younger colleagues who will lead the overseas operations in the future. Not only was I pursuing personal growth, but also taking on new challenges looking ahead to the future of DENSO and my colleagues.
─── That’s impressive! You have a unique take on work—pursuing new challenges for the sake of the company and the younger colleagues.
Providing safety products for the entire world, starting with my family and my friends
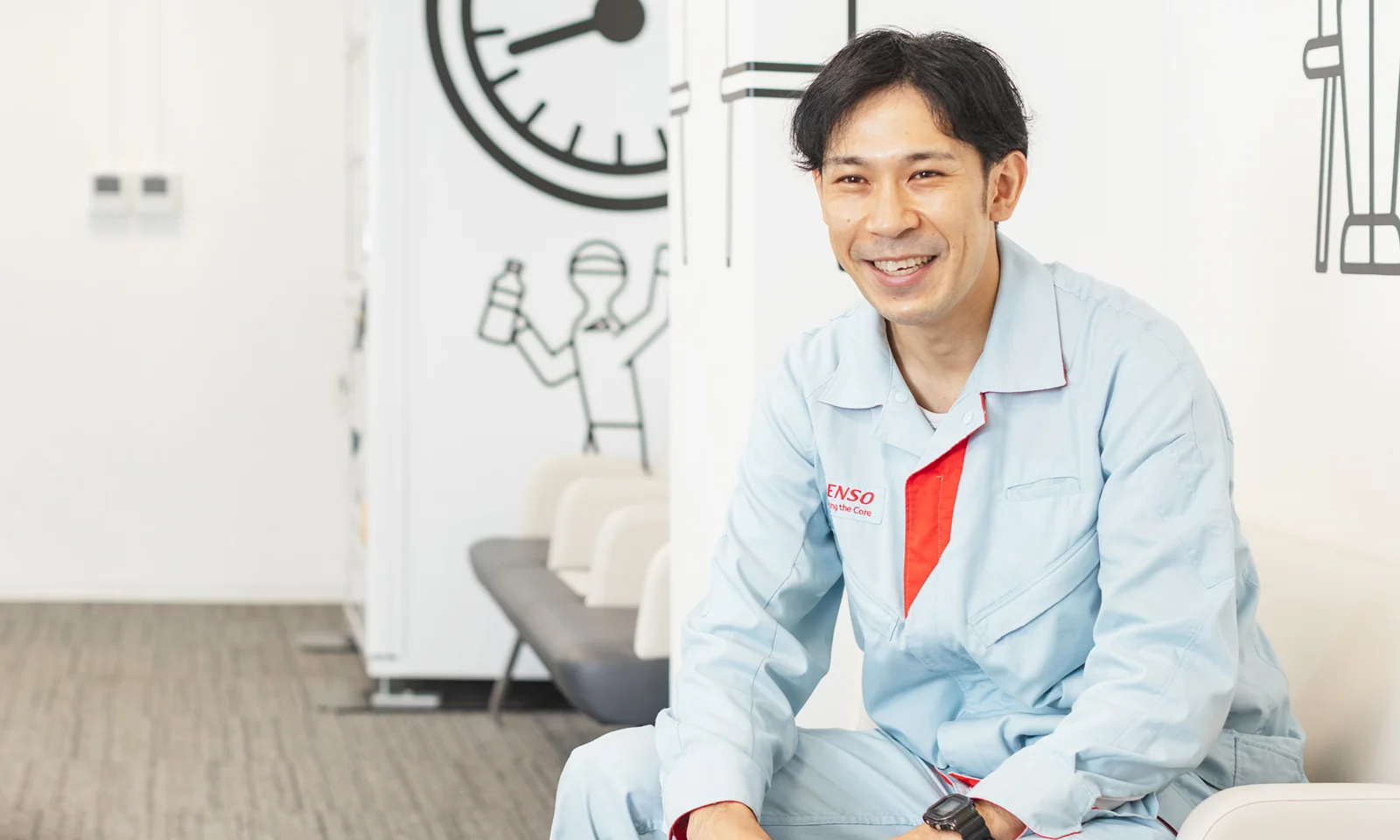
Tanaka: Perhaps I was overselling myself a bit [laughs] … I wasn’t thinking on such a grand scale. It all came from a feeling to protect my family, my friends and other people close to me.
─── Oh! Let me know in detail.
Tanaka: For example, it is the most important for me to prevent my family and my friends from getting into traffic accidents with the perspectives of the DENSO’ goal of zero fatal traffic accidents. If my important persons get injured in accidents caused by defective products I gave OK, it would be unbearable for you. If my wife were to be hurt or killed in an accident, her parents would be sad. If it happened to a friend, their other friends would be sad, too.
It is because people’s lives depend on their relationships with others. So it’s necessary to focus first on making safety products for your important persons. If we all approach our work in this way, I believe that safe, trustworthy products will eventually spread throughout Japan, and then throughout the world.
─── Exactly. We hope our families come home safe and sound every day. It’s the most important thing for our daily lives.
Tanaka: Yes. I work on my manufacturing work every day in order to keep our safety as a matter of course.
─── Do you have such a sense of values in the first place?
Tanaka: No. My former boss had a great impact on it. When I was engaged in the safety product manufacturing for the first time, my boss was incredibly committed to putting quality first. I have ever heard him shouting “Stop the lines If you cannot prevent any defective products!”
Our products are intended to prevent traffic accidents, which means that one defect might result in an accident. Even if it is the only one defective product among many of our products from the point of manufacturer, it is all of our products from the point of its user. My former boss taught me that we must focus on the details in our work without falling into routine habits and patterns in order to produce good products for the society and to protect users’ safety. He taught me the importance of my work, and through my experience I was gradually acquiring thoughts of zero fatal traffic accidents.
Communication with other’s perspective leads to higher quality work
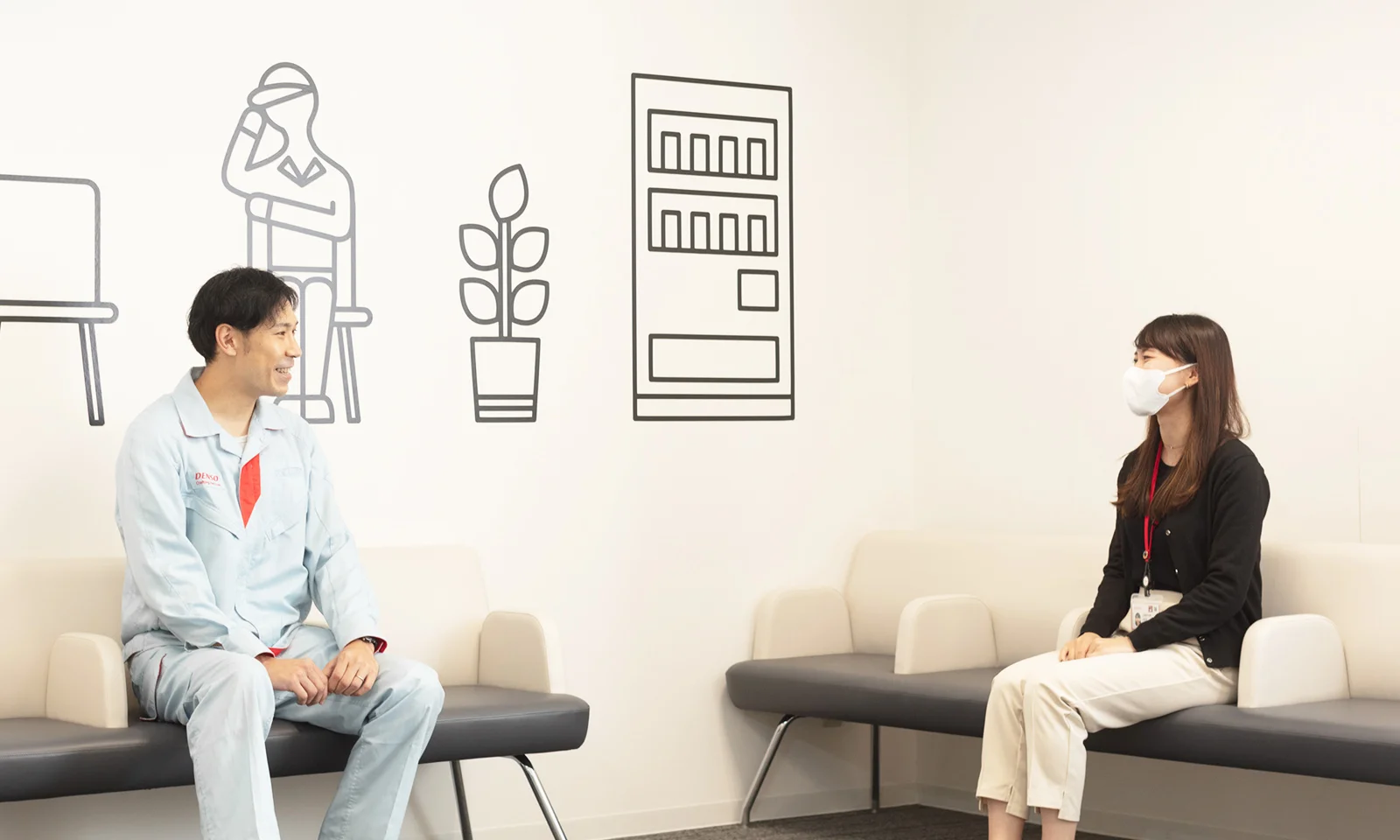
─── You encountered such an inspiring boss. I’ve heard that production sections at DENSO tend to focus a lot on teamwork, and I think good communication is important there. Do you have any personal rules you follow about communication?
Tanaka: Yes. I intend to adjust my perspective to each person’s one, whether it’s your boss or a younger associate.
Let’s say you’re talking to a much younger associate at the company. He or she may not understand your usual jargon and approaches that you assume everybody understands. You should consider how much you should simplify and explain things in order to ensure good communication with them, because they are new at DENSO. In contrast, when talking to your boss, you have to try to imagine what they are thinking and ask them to explain when necessary. I always try to learn new things through communication with my boss.
─── I think it is important to have a communication in a way that you mentioned, but it is difficult in practice to do this approach. What inspired you to do it?
Tanaka: When I was new at DENSO, I didn’t know a lot of things here, and it took some time to understand what my colleagues were talking about. Because I had a difficult time at that time, I can empathize with my young colleagues today. They haven’t yet fixed their views and approaches regarding work, so at first I talk about familiar and everyday things with them, and as they grow accustomed to their work, I adjust my perspective accordingly in communication.
─── In other words, you use your personal experience when interacting with others.
Tanaka: The “right answer” to something varies from person to person, just as their values differ. By having respect for other persons when communicating, it becomes easier to find ways of mix values and ideas of each other.
─── It seems like we could apply similar principles not only to younger colleagues but also any other persons. Could you describe a personal experience when you were able to successfully communicate by adjusting your perspective for other persons?
Tanaka: Well, my younger colleagues come to me for advice quite often. After we had gotten to know each other better, he began to talk to me more casually and even began to call me by my first name! (This is unusual in Japanese corporate hierarchies.) It is as if we are club members in school days or are friends. Now they do not hesitate to talk to me about anything.
─── That’s awesome! It seems like they really trust and believe in you.
Tanaka: They have really grown up, and are currently leading their own teams. Now I see them take similar approaches of adjusting their perspectives to their younger members when communicating with them, and strives to cultivate workplaces where people feel free to state their opinions openly. I’m really happy to know I may be their role model. Their growth motivates me the most to do my work.
─── That’s a great story! In contrast, some people feel it is very difficult to narrow their distance between them and their higher-ranking persons. For example some people feel that it’s not their place to speak frankly to their higher-ranking persons.
Tanaka: That’s true. But I think people’s performance improves if they take the initiative in their work. It is the worst that someone cannot admit their small mistakes, and tries to cover them up instead. In other words, it means that someone cannot say what they want to say, and thus they are patient with their tasks difficult to do.
It defeats the purpose if such a situation leads to defective products as a result. As I am engaged in work where even a single defect is not allowed, it leads to producing high-quality safety products to ensure a comfortable and open workplace for each associate. I believe firmly in this, and that’s why it’s important to create a team where we can talk about anything.
Would like to build not a vertical but a horizontal team where everyone works side-by-side as equals toward shared goals.
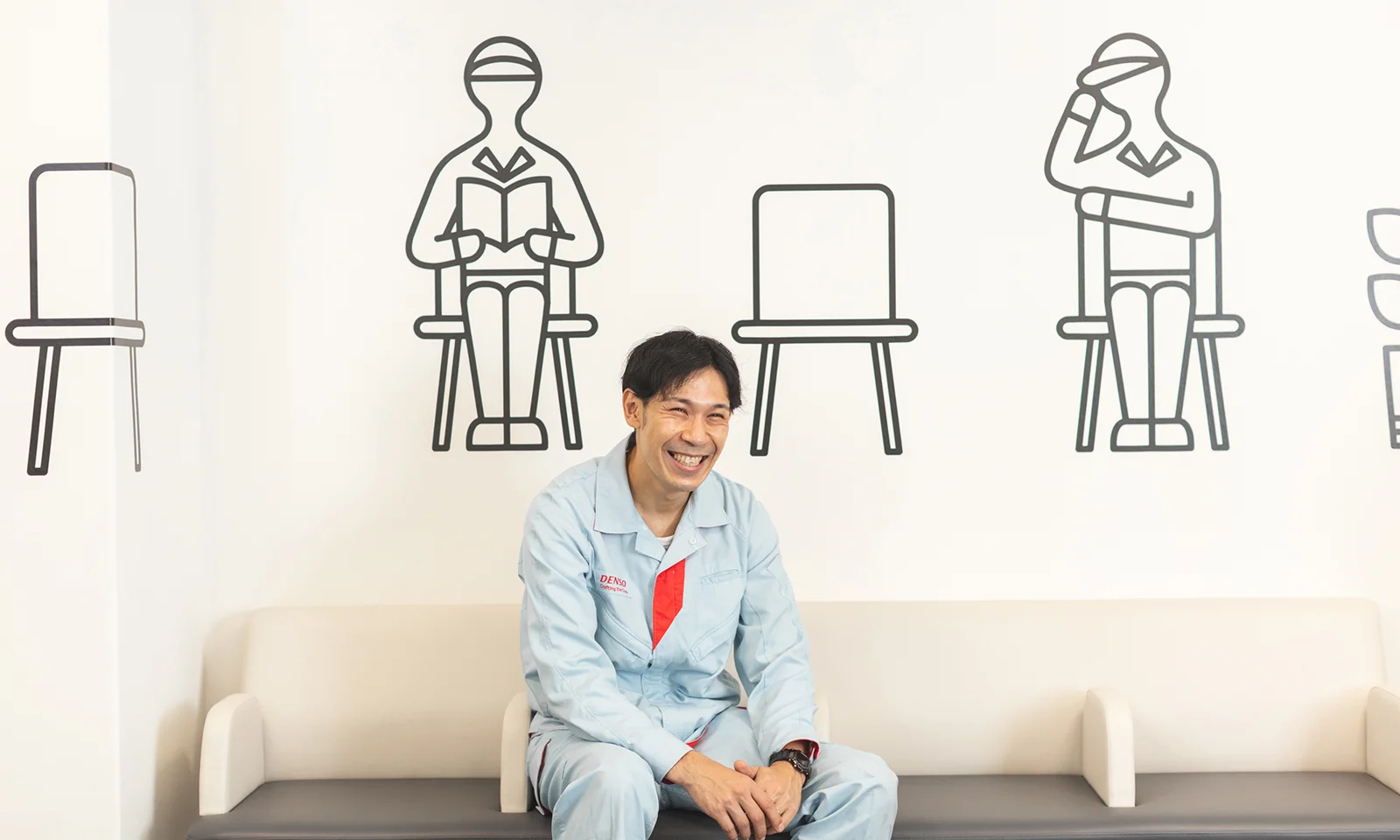
─── That makes sense. In the end, the communication approach you’ve talked about, which entails considering each person’s perspective, as well as your efforts to create a more comfortable workplace for all, are for the sake of producing high-quality safety products to society. Before we finish, could you please tell me about your own ambitions and dreams?
Tanaka: I want to create a workplace where all of my team members go for the shared goal.
For that purpose, it is necessary to usually share the purposes and backgrounds of our tasks in order to think and work for ourselves. I think the final quality of your tasks depends on whether you merely follow your boss’s orders, or you devise a way to accomplish your tasks with their targets and purposes shared in your team.
Unless we fully understand goals, it’s impossible to go for the shared ones.
I think the information of what we are striving for and what your tasks lead to should not be possessed only by your bosses, but be shared among teams. I would like to build not a vertical but a horizontal team where everyone works side-by-side as equals toward shared goals.
For team members who have their own ambitions and dreams, I encourage them to make friends with their colleagues. Many of us remember that we enjoyed spending time at schools together with our friends. In the same way, your colleagues will keep you going in your daily work by sharing your dreams and ambitions with you.
COMMENT
Changing your "Can'ts" into "Cans"
Where Knowledge and People Gather.