Did you find this article helpful for what you want to achieve, learn, or to expand your possibilities? Share your feelings with our editorial team.
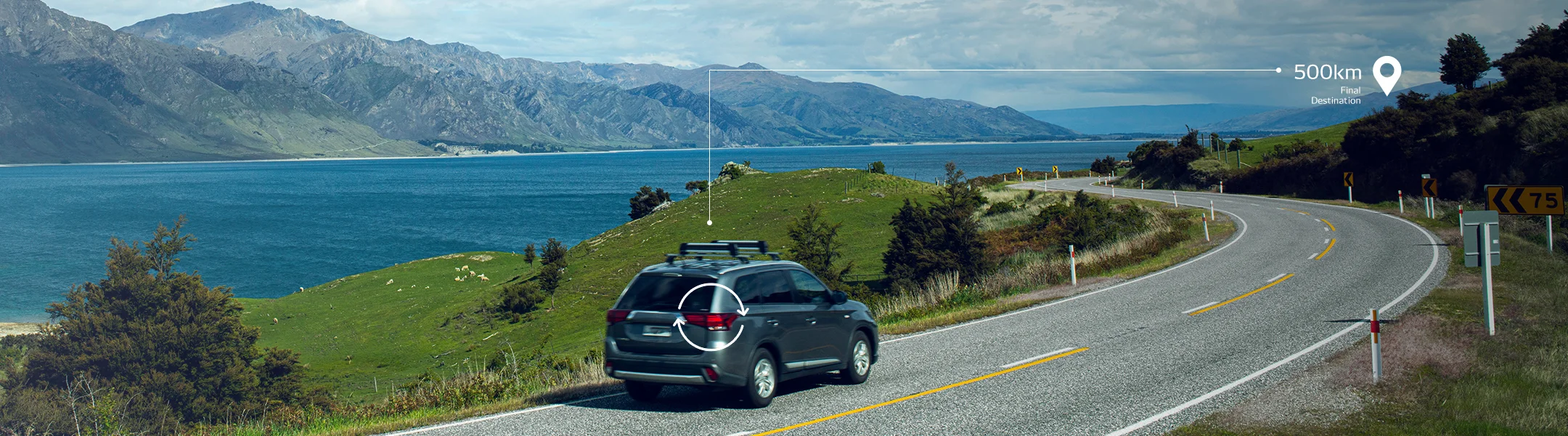
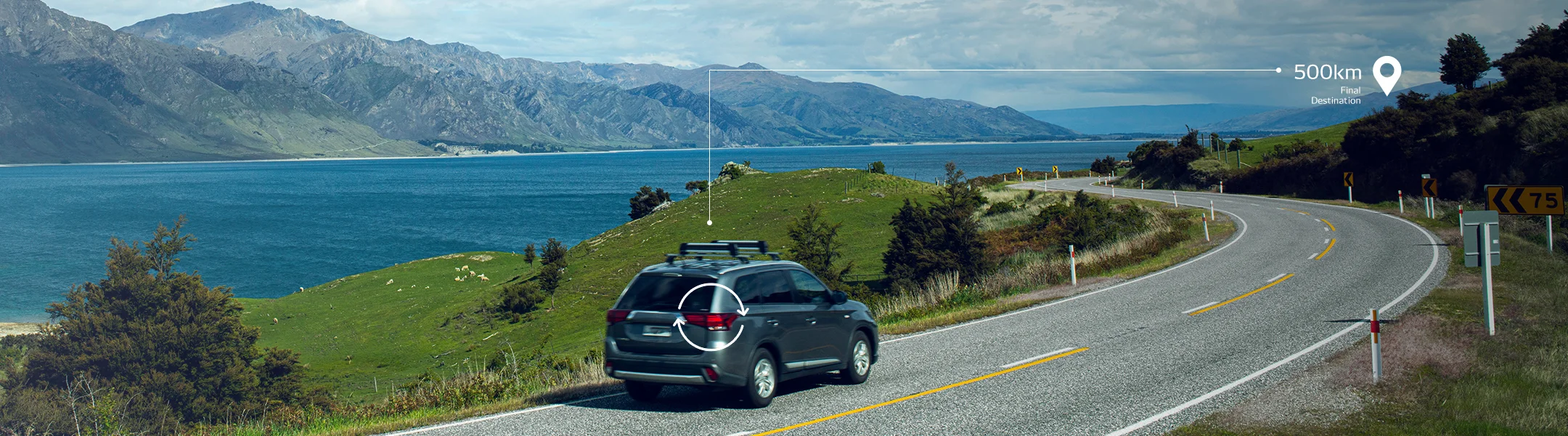
Jul 15, 2021
TECH & DESIGNNext-generation energy management systems can change the future of electric vehicles
Energy management suitable for user needs, and the architecture that makes this possible
-
Thermal Management Systems R&D DivYu Ofune
Yu Ofune studied mechanical systems at university and has pursued fundamental research in computational fluid dynamics (CFD). After joining DENSO in 2004, he took charge of development and design of new exhaust-system heat exchangers. He has been involved in developing thermal management systems since 2017, particularly those for electric vehicles.
-
Systems Development for Smart City DivMitsuharu Higashitani
Mitsuharu Higashitani studied optimization algorithms at university and began working at DENSO in 2007. He currently develops system control architecture and standardized system simulators to facilitate implementation of energy management applications, thus helping to build the foundations for vehicle EMS.
Battery electric vehicles (BEVs) are not just cars in which the internal combustion engine (ICE) of a gasoline vehicle has been replaced with an electric motor. The powertrain which drives the vehicle must be changed, and the energy control framework has to be completely restructured. Let’s take a look at the types of energy management systems (EMS) we can expect to see in next-generation BEVs of the near future.
Contents of this article
How EMS can change BEVs
— BEVs have spread in recent years. Complex air conditioning systems are used in gasoline vehicles powered by ICEs in order to keep the vehicle cabin comfortable. How are these same systems handled in BEVs?
Higashitani: Energy management for air conditioning and other such systems is completely different for ICE-powered vehicles and BEVs. In gasoline vehicles, the ICE is also a powerful heat source, and its heat can be directly used by the car’s heating system. Therefore, ICE vehicles rarely have a problem securing sufficient heat resources. In a BEV, however, battery power must be used to create the heat, which may reduce the power available for vehicle movement and thus reduce maximum travel distance.
― Today’s ICE vehicles incorporate “eco mode” features such as moderate accelerator-pedal response and AC setting changes to improve gas mileage. Is this different than the BEV EMS you’re describing?
Ofune: The eco modes in ICE and hybrid vehicles simply reduce output. With BEVs, we have to consider the unique characteristics of the battery units themselves, infrastructure-related factors such as charging point locations, and many other things. Simply reducing output is not an effective solution.
Higashitani: In particular, BEVs face some major challenges related to battery temperature. Internal resistance causes the battery to heat up, and if it becomes too hot its performance begins to drop. Every battery has an optimal operating temperature range, and the temperature at which it is actually operated can affect its lifespan. The EMS is used to maintain optimal temperature and cool the battery when necessary.
― It seems that gasoline-powered engines tend to heat up a lot more.
Higashitani: With an ICE, even if the vehicle is driven at high speed and the engine becomes very hot, the radiator can be used to release heat and cool it again. The batteries used in BEVs are difficult to cool down once they have heated up, which is why a good balance must be maintained between heat for the AC system, energy used to move the vehicle, and the temperature of the battery itself. Energy management is needed to achieve this balance, and compared with ICE vehicles a longer-term energy plan is required for BEVs. This is my current research area—technologies to achieve comprehensive energy management for the BEV as a whole.
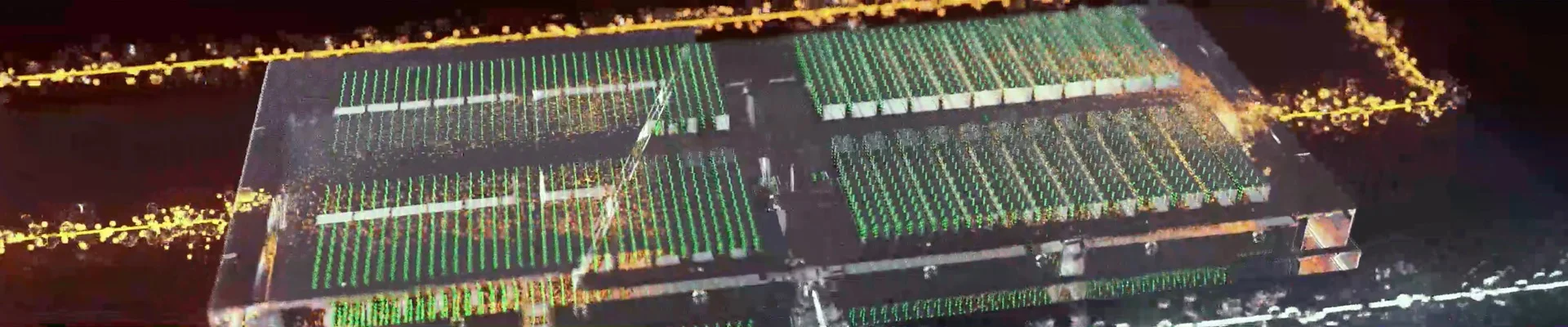
Cleverly designed cars that adapt operations to user needs
— What type of energy usage is involved in your longer-term energy plan?
Ofune: Let’s say you are making a 500-kilometer trip and want to get to your destination as quickly as possible. With an ICE vehicle, the faster you drive the faster you will arrive. But with a BEV, this same logic may not apply, because the faster you drive the hotter the battery becomes. Moreover, when you stop to rapid-charge your vehicle along the way, the high electric current flowing into the battery heats it up even more.
Continuous raising of the temperature in this manner can cause battery malfunction or damage, so with a hot battery it’s necessary to use less current and charge more slowly to keep it within a safe temperature range. In other words, high-speed driving causes the battery to overheat, which slows the charging time. That means driving faster may not get you to your destination more quickly.
EMS can help solve such problems by adjusting to the specific user and usage. One possible solution is to keep the vehicle speed down until the mid-journey charging station, thus reducing charging time and ultimately shortening the total trip time. Rather than simply getting there faster, some users may prioritize maximizing the life of their battery, while others may want to minimize electricity costs. By implementing energy management for the vehicle as a whole, it’s possible to achieve car usage styles that meet a wide variety of user needs.
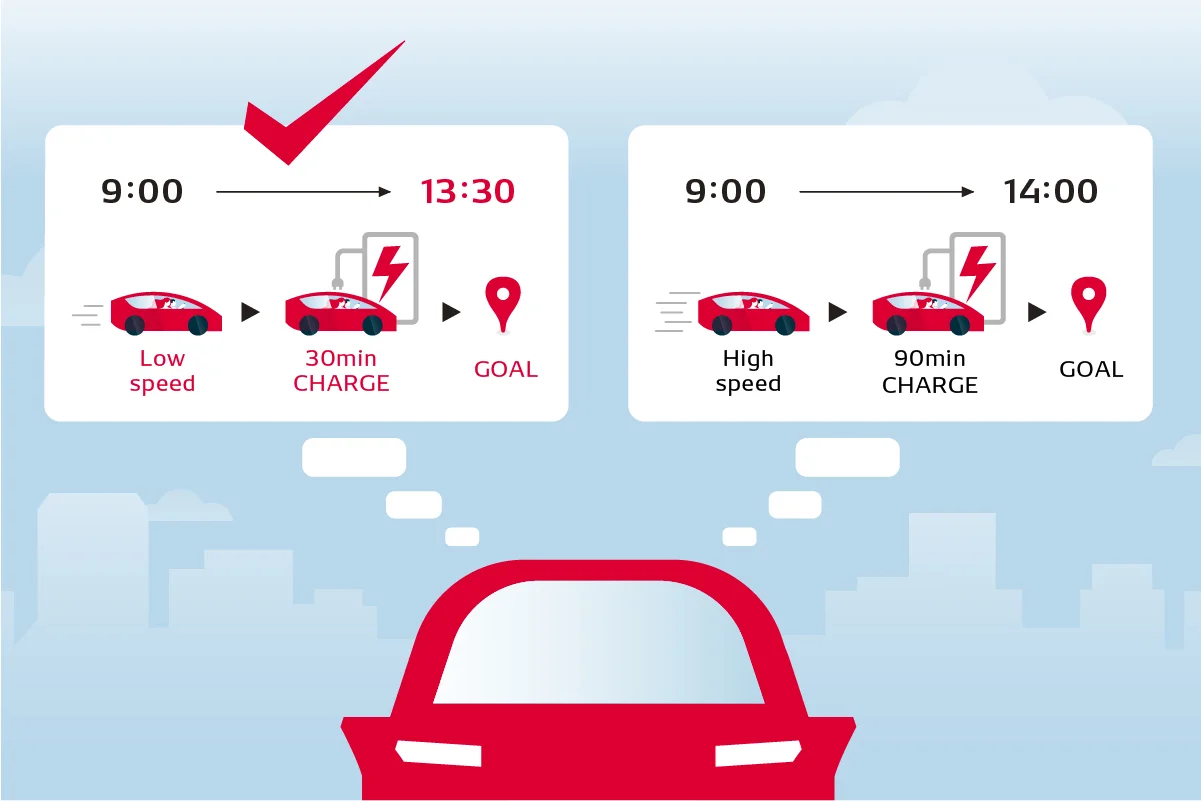
― In order to fully achieve this type of functionality, the vehicle’s architecture itself must be redesigned, correct?
Higashitani: That’s right. Today’s BEVs use electronic control units, or ECUs, for each system or section of the vehicle—the powertrain system, air conditioning system and so forth. Similarly, the battery has its own ECU. Vehicle manufacturers determine battery parameters at the outset based on expected usage conditions and styles for the BEV in question, and ECU control is tailored to these parameters. Battery temperature predictions must be very precise.
Also, in order to suitably manage energy for the vehicle as a whole, a sort of “control tower” is necessary to oversee vehicle system operations. One such control tower is the central ECU, which collects various information from throughout the system and issues operation orders. We’re researching the logical architecture for designing such central ECUs.
― How does central ECU processing work?
Higashitani: Many people think “energy” is a simple concept, but there are actually many different forms of energy. It can take the form of heat or electricity, for example, or kinetic energy which is used to move the car.
With a BEV, we have to think about how much electric power the battery has and how much output it can produce, how much output the powertrain components such as the motor can produce and how much electricity they require to do so, how much electric power the AC system requires to work under various conditions, and so forth. This measure of how much energy can be accessed for these various operations is called energy availability. The ECU in each subsection of the vehicle system measures this availability, and availability information for the vehicle as a whole is brought together in the central ECU which oversees the system.
The central ECU comprehensively analyzes the information it receives from individual ECUs, uses the results to determine how much energy should be allotted to each subsection of the vehicle, and then sends relevant information to individual ECUs. The lower-ranking, individual ECUs then make decisions based on commands from the central ECU.
― So the central ECU doesn’t actually control components such as the motor and battery directly?
Higashitani: Achieving a good balance among the ECUs—determining which should be in charge of which processing tasks—is crucial. Take our earlier example of energy management tailored to specific user needs: the central ECU’s primary task is prediction, but because predictions are not guaranteed, there is much uncertainty in the information. Also, conditions tend to change quite often.
The central ECU does not carry out complex computations; rather, it makes broad decisions about general usage patterns for energy. Imagine a wild driver who, under normal conditions, can only travel about 100 kilometers on a full charge in their BEV.
However, today’s destination is 120 kilometers away, it’s going to be a hot afternoon, and traffic signals along the route are expected to affect travel efficiency. In this case, the central ECU can tell the driver what general travel speed is optimal and recommend keeping the AC low—that’s the level at which it operates.
It’s similar to how a department supervisor handles workers in a company: the supervisor determines broad, overarching goals and sets deadlines for the workers to achieve. Each employee is then responsible for completing the specific tasks needed to achieve those goals.
That’s basically how the energy management architecture we’re developing functions.
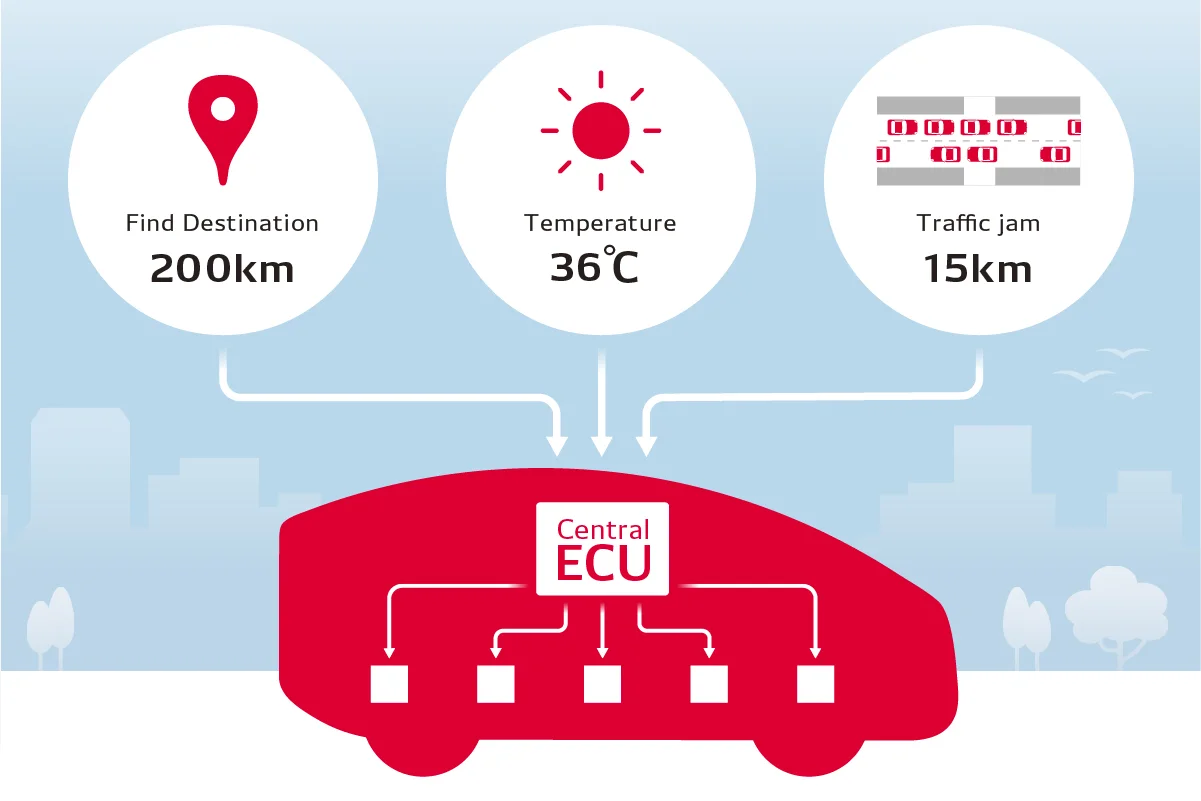
― Do you use technologies like AI and machine learning for predictions?
Higashitani: Technologies like AI and machine learning can be useful when processing huge quantities of data for complex energy management. At DENSO, we have a team that develops elemental technologies in these areas.
But what matters most is not the specific technologies; rather, we want to ensure the product offers value to the customer. EMS development entails making hypotheses, then verifying them, then repeating the process over and over in order to solve problems. Naturally, this involves many different technologies.
― Is energy management for batteries carried out primarily using software?
Ofune: Software is important, but hardware must also be given equal weight. Making good hardware is pointless unless you have effective ways to control it, and even intricately designed software means nothing without proper hardware.
Actually, hardware is very important for controlling battery temperature. As I mentioned, software controls the temperature settings for the battery, but in terms of hardware an effective battery cooling system is required in order to achieve the targets set by the software. For this battery cooling device’s cooling system, we’re developing both the hardware and software simultaneously.
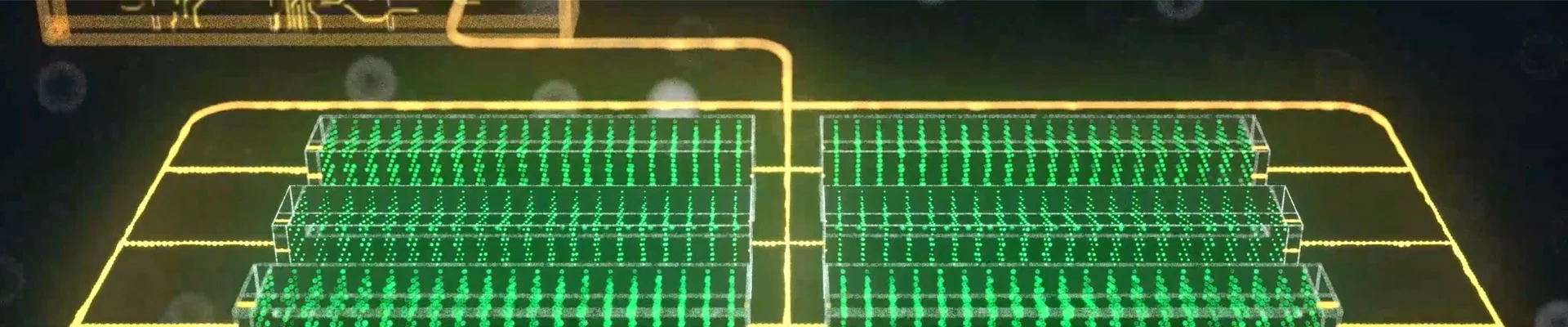
Designing cars as systems
— From your comments, it seems like you’re designing an operating system rather than an automobile.
Higashitani: Moving forward, various applications will need to be added and removed in response to automaker and user needs. In order to make this process easier, we have to imagine the car’s structure rather like an operating system.
― As EMS evolve, will the vehicle development process also change?
Higashitani: At DENSO, we will focus increasingly on what types of value customers are seeking from a car, how the energy management architecture should be designed, what ideal vehicles should be, and then propose our ideas to automakers.
Ofune: These days, automakers are working hard to develop automotive platforms rooted in connected technologies, which enables applications to be added, removed and updated as necessary. I think we can expect connected-type platforms to become really widespread by around the year 2025. By the way, DENSO also plans to propose EMS compatible with this type of platform.
― We discussed cleverly designed cars that adapt their operations to meet user needs. Do you think this type of car will hit the market as well?
Ofune: We hope to propose new, more clever EMS and BMS (battery management systems), and work together with automakers to launch such vehicles.
― I think that energy management can be extremely useful not only in private-use automobiles, but in business-use vehicles as well.
Ofune: I agree. Although we’re still in the brainstorming phase, we are currently considering developing services for delivery companies. By effectively managing battery temperatures, we can extend battery lifespans, reduce replacement costs, and speed up charging to reduce lost time. These improvements are valuable to users.
― I imagine that next-generation energy management will also transform the development framework as well.
Higashitani: DENSO’s development framework is already changing gradually, and we expect that to accelerate. Various divisions within the company—such as those involved in heat-related systems, powertrain systems, and electrical systems—have worked together to design subsystem controllers.
Going forward, we hope to develop a better understanding of logical architecture and use it in subsystem control-specification design. It is important to bring different sections of the company together in this way and collaborate on development.
COMMENT
Changing your "Can'ts" into "Cans"
Where Knowledge and People Gather.