Did you find this article helpful for what you want to achieve, learn, or to expand your possibilities? Share your feelings with our editorial team.
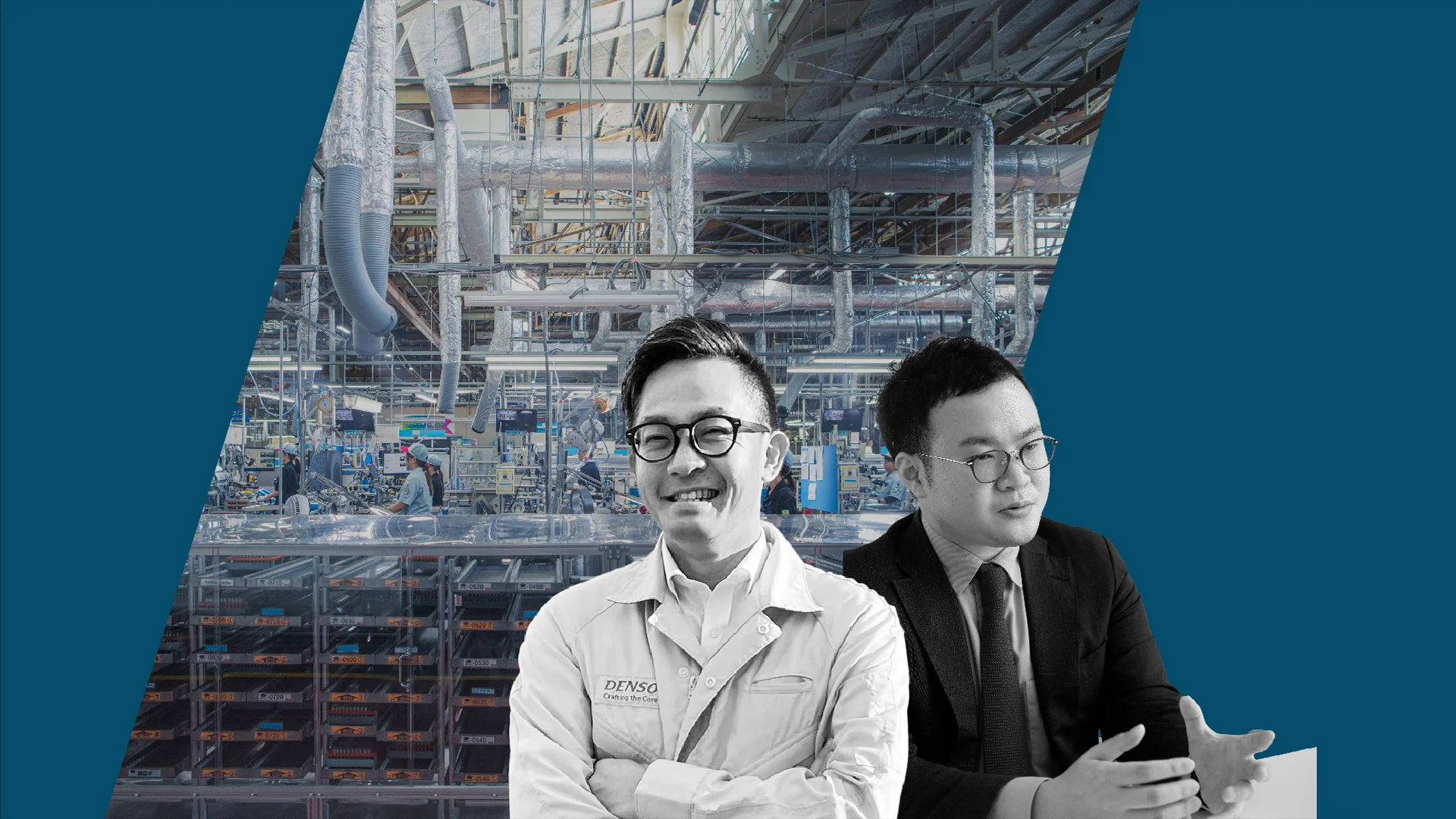
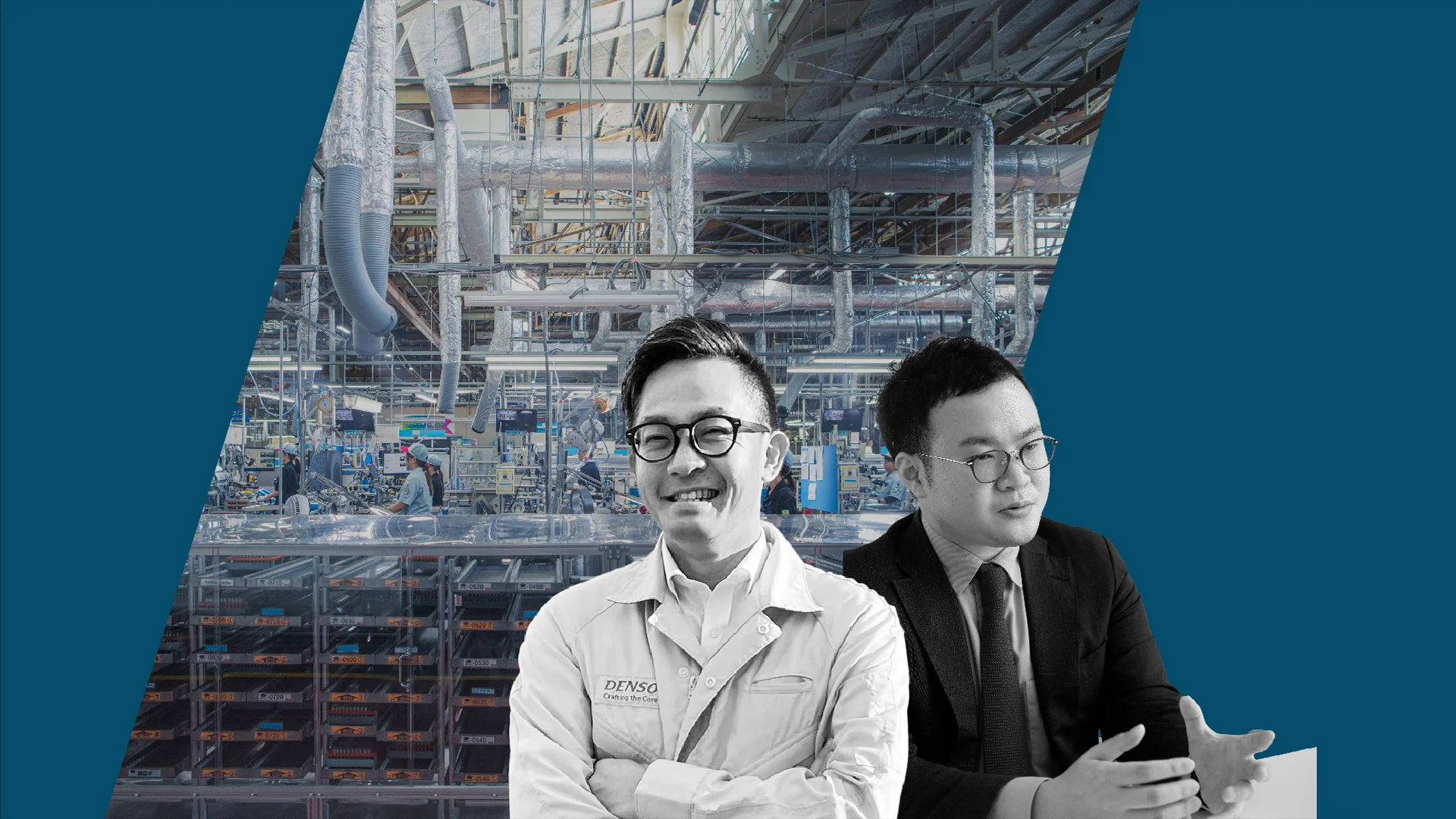
Dec 8, 2023
TECH & DESIGNCommitment to Pursuing the World’s Best Products and Rolling Out Externally the System to Develop the Necessary Human Resources
DENSO’s monozukuri (manufacturing) to revolutionize global manufacturing through upward spiral of value
-
FA Business Development Div., DENSO CorporationKenshin Yokose
-
Innovation Strategist, JIC Venture Growth Investments Co., Ltd.Masahito Komiya
DENSO Tech Links #18 featured lectures by engineers and a panel discussion with a special guest regarding the future of monozukuri (manufacturing) envisioned by DENSO on the theme of digital transformation (DX) at manufacturing sites. Mr. Kenshin Yokose of the FA Business Development Div. and Mr. Masahito Komiya of JIC Venture Growth Investments Co., Ltd. explained DENSO’s efforts to deliver value through its business.
Contents of this article
Self-introduction of the Speaker
Kenshin Yokose: I will give a presentation on the theme of “Upward Spiral of Value through Business.”
I am in charge of the FA Business Development Div. I come from the same production engineering background as the two previous presenters. While developing new products, I experienced starting up overseas production lines in a manufacturing division, and I then served as a production engineering supervisor in North America.
Later, I compiled DENSO’s automation techniques as a teaching material and launched a joint project with the Thai government. I then launched a new business based on this project in Thailand. I will focus on these activities in my presentation.
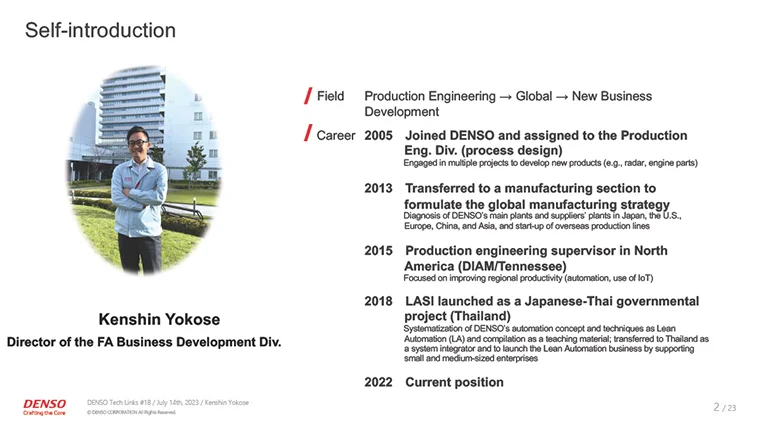
Efforts to Achieve Upward Spiral of Value
Today, I will explain DENSO’s efforts to switch from analog to digital, and the challenges to be addressed.
To achieve this goal, formalization and standardization are extremely important. It is also necessary to compile a teaching material to share information and develop human resources. These efforts help convey our accomplishments outside DENSO. The Lean Automation School and robotic cells, which are cellular robots, are two examples of our solutions, which I will explain.
We contribute to the development of human resources and improvement of productivity by delivering these solutions to customers. At DENSO, we acquire expertise through these activities and promote an upward spiral of value.
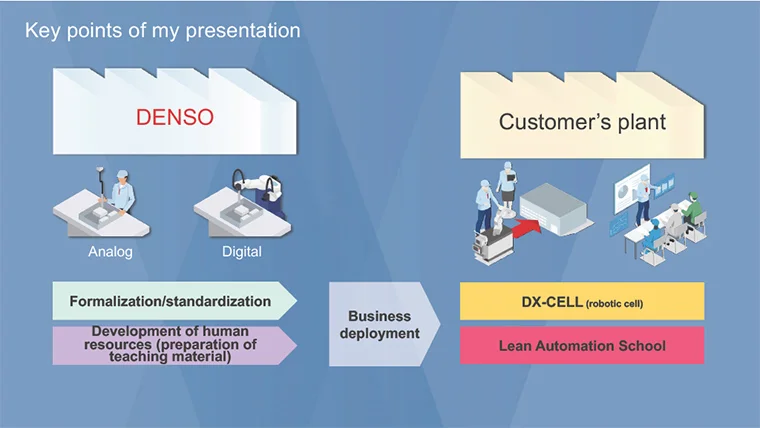
DENSO’s Systems That Evolved Based on Thorough Formalization and Standardization
Let me give some examples. The first is “the world’s best products from the world’s best production lines,” to which we have always committed.
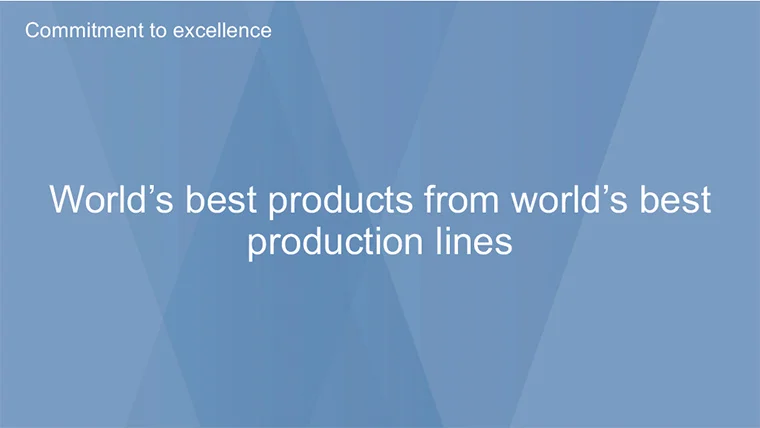
Let’s look back on the history of DENSO’s production systems. We started to rationalize respective processes in the 1950s and spread the activities across production lines and plants. The development of flexible production systems, which the two presenters introduced today, started in the 1990s and has finally borne fruit thanks to technological advancement.
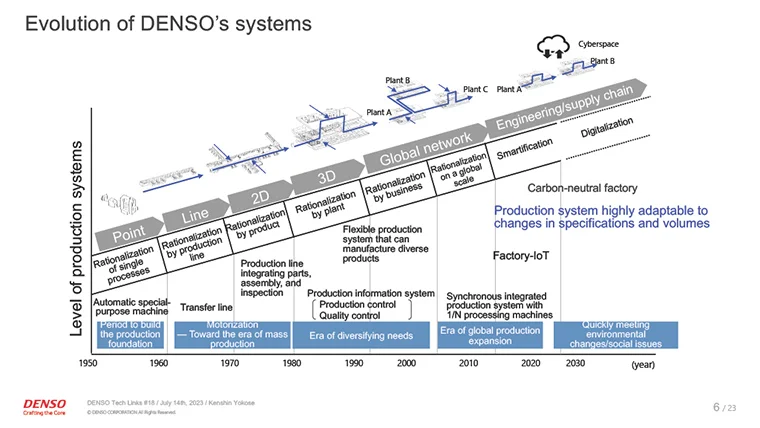
Regarding production rationalization during the founding period, we copied technologies developed in Europe and the U.S. in the 1950s and 1960s and manufactured machines in-house. We came up with innovative ideas and worked on the development of inexpensive but reliable production lines.
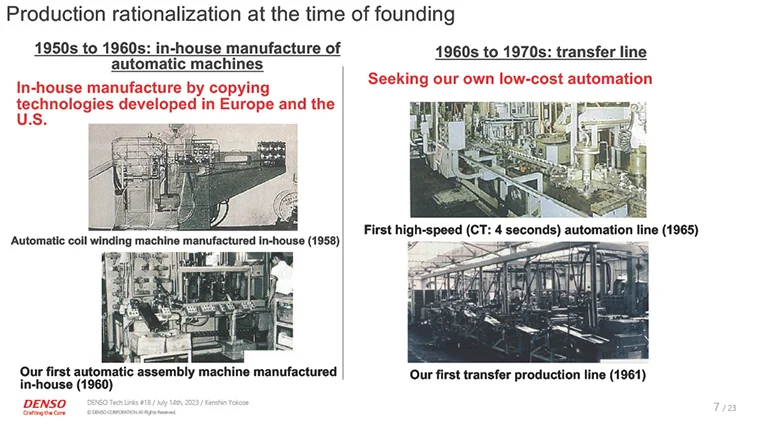
(While pointing to the slide) Katsuo Aoki, General Manager of the Production Engineering Div. at the time of founding who was later promoted to Executive Vice President, used the term “low-cost automation like home-cooked meals.” He also advocated “differentiation of products from those of competitors by manufacturing and using machines not commercially available.” Such “DNA” has been inherited throughout the history of DENSO. These activities have been undertaken by the machinery and tools section, which manufactures equipment in-house, and DENSO WAVE, which manufactures robots in-house and sells them (while pointing to the slide).
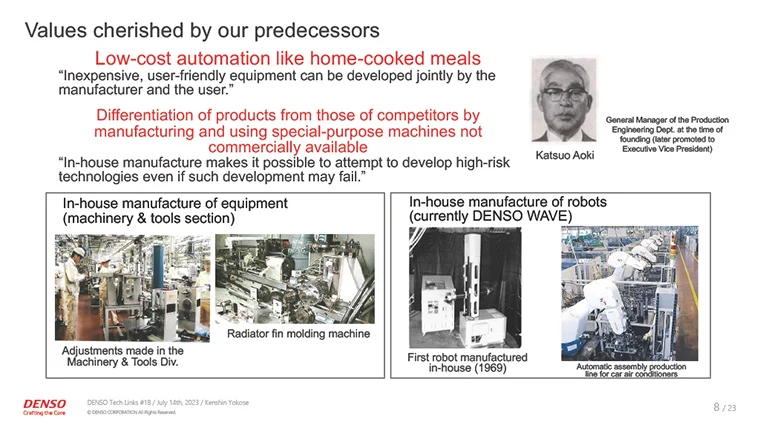
The term “concurrent engineering” was used in the first session. Improper designs during production preparations can result in serious problems. In concurrent design, front loading is done before the design phase in order to design good production equipment and products at the same time.

Our commitment to excellence is thoroughly formalized and standardized to develop human resources. After all, “Monozukuri is hitozukuri (our performance relies on our people)” is deeply engraved in our “DNA.”
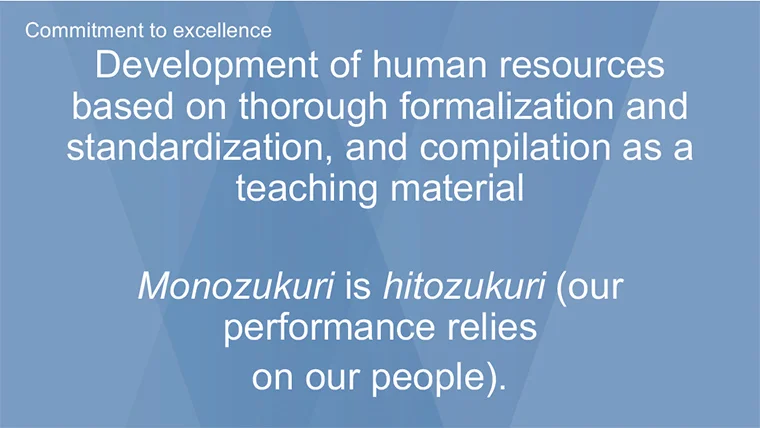
Spreading Lean Automation, an Approach to Eliminate Waste of Equipment and Work
We wondered whether such efforts enable DENSO to deliver value externally and share our know-how clearly, and came up with the “Lean Automation” concept.
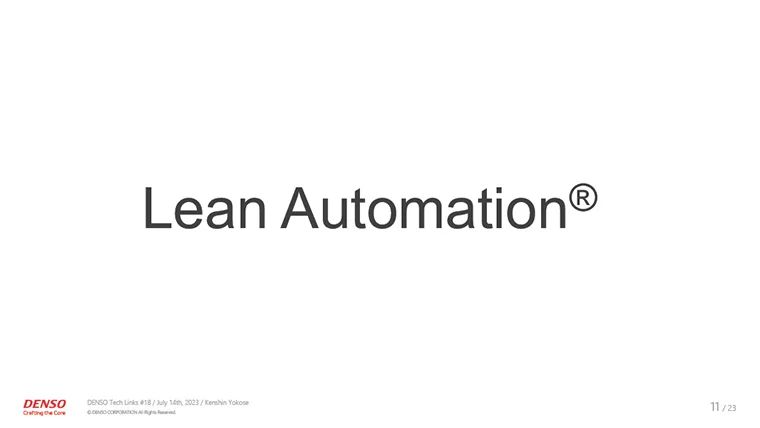
(While pointing to the slide) This is an approach to attaining a production system without waste, which is the basis of lean manufacturing, through automation.
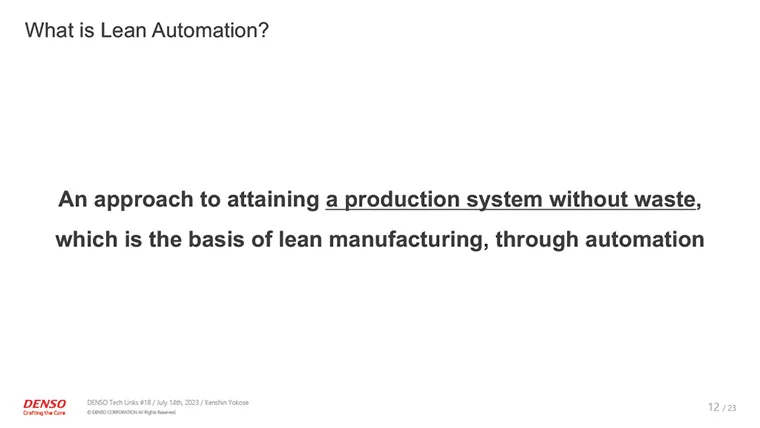
As shown on this slide, production activities include various types of waste. Automating such production activities including the wasted parts would incur significant costs.
The basis of Lean Automation is to reduce waste of equipment and work before automation, and to automate only the actual work.
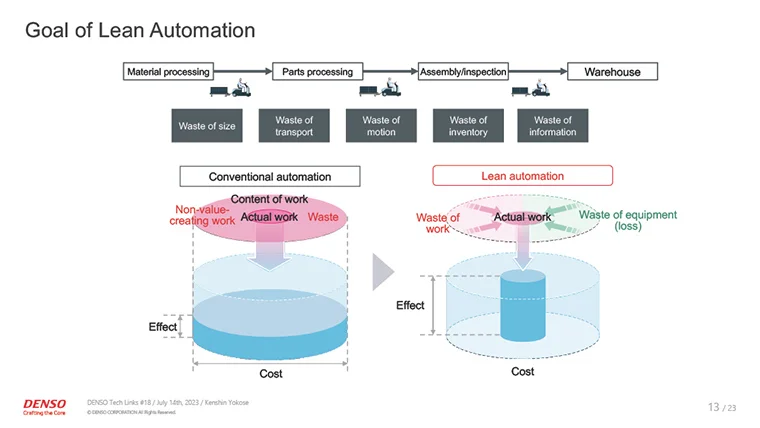
I launched the first project in Thailand to provide training on the concept of automation. With labor costs rising in overseas markets, productivity cannot be increased simply by introducing robots. To share the strengths of Japanese manufacturing, a teaching material was compiled with support from the Thai and Japanese governments, and the Learning Factory was established to provide learning opportunities.
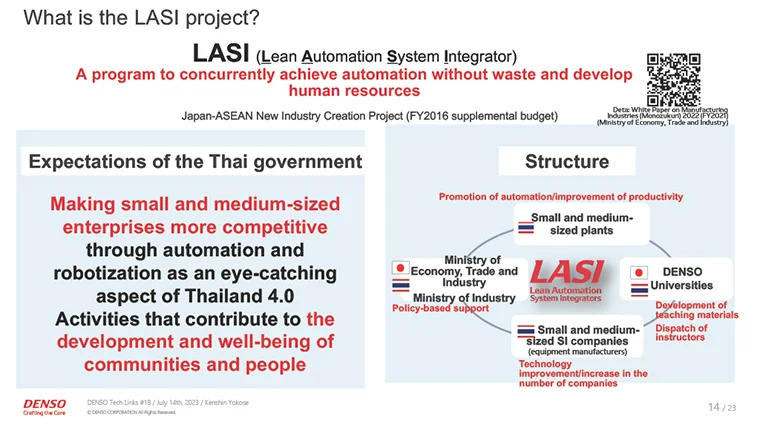
(While pointing to the slide) This slide shows the activities at the Learning Factory. Trainees learn various methods in the classroom, have hands-on experience of the design process, allow a robot to mimic their hand movements, and visit their plant to carry out kaizen of the production lines and achieve automation. Thus, the training program is highly practical.
Through these activities, “the foundation of manufacturing” has been established and will become widely available in Thailand. Thus far, about 1,300 trainees have graduated.
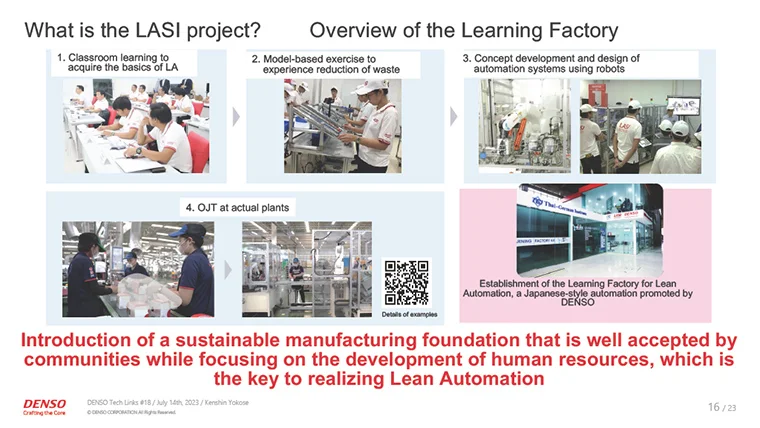
These activities, which started in Bangkok, were highly evaluated and spread to the northern and eastern parts of the country. At present, the Learning Factory is operated at three locations.
Subsequently, the Learning Factory was reimported to Japan. At DENSO, it has become part of the Lean Automation School, which I will explain later. The Learning Factory is also used partly for research at the University of Tokyo.
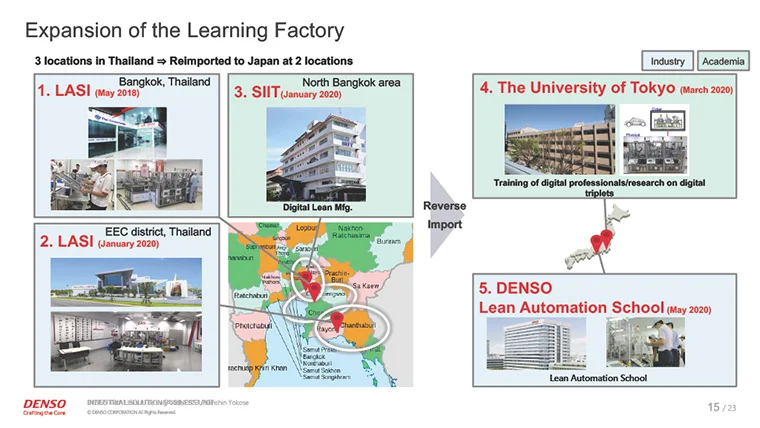
Various Curricula Continuously Upgraded at the Lean Automation School
(While pointing to the slide) This is the Lean Automation School at DENSO. Manufacturing engineers from various industries and business areas attend the school to learn the Lean Automation techniques and hold discussions to come up with ideas for better automation. The curricula are highly practical.
We have received a lot of feedback, such as “We want to rationalize logistics at our plant,” or “We want to use IoT, but don’t know where to start.” We have been upgrading our curricula to meet such needs.
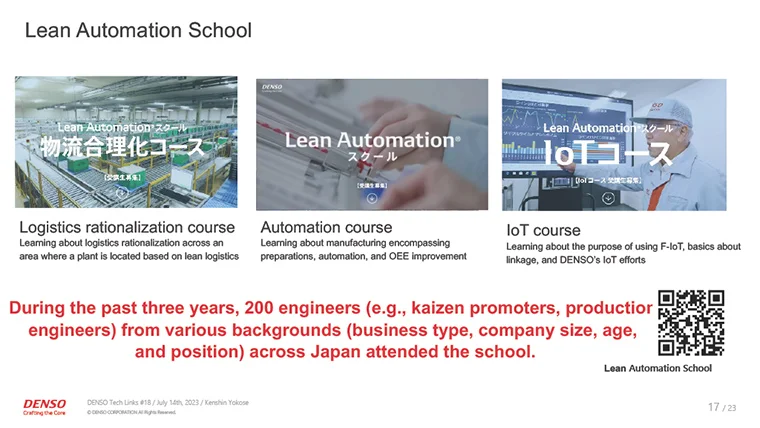
Digital Triplets for AI Modeling of Human Problem-solving Capabilities
Earlier, I mentioned research at the University of Tokyo, where a team is working to develop the Digital Triplet technology to promote formalization and digitalization. The activities aim to turn human knowledge and activities into AI models.
The photograph in the lower left of the slide shows the teaching material equipment used at the school. This is a cyber-physical system, which is similar to those introduced by the two previous presenters. The system enables the user to solve various problems in cyberspace.
We create knowledge models based on the thinking processes through which skilled workers solve problems, and build these models into AI. Our R&D aims to embody the know-how acquired by skilled workers, who are quitting in greater numbers as they reach retirement age, in AI and pass on such know-how to the next generation.
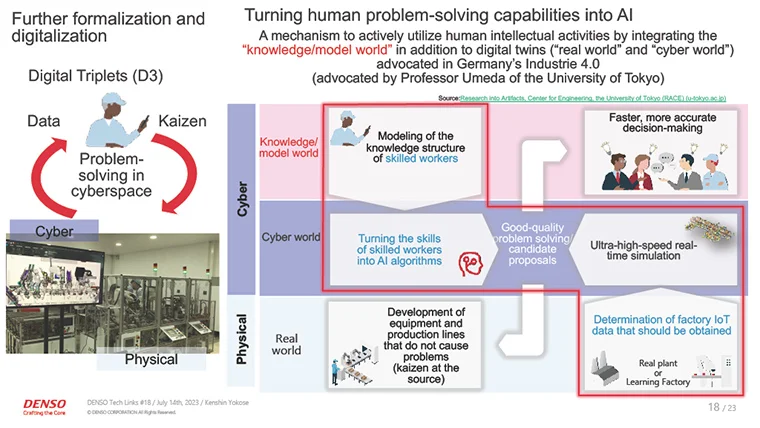
Sales of Robots as Products in the Factory Automation Business
Finally, in the factory automation business, robots are sold as products, as Mr. Matsutani and Mr. Arai explained.
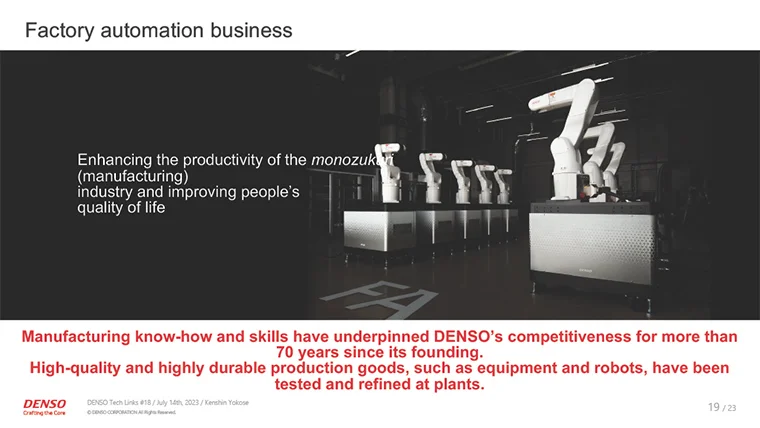
(While pointing to the slide) As shown on this slide, designs in cyberspace are deployed in the real world. As the two previous presenters explained, the situation in the real world is expected to change rapidly. We will be able to manufacture various products by rearranging robots and production lines.
Once designed, a production line is stored in cyberspace and can be easily copied. New production lines can be created quickly either overseas or in Japan. We deploy products based on this concept.
We have group companies which manufacture robots and production equipment, which I explained earlier. We cooperate with these companies to solve customers’ problems.
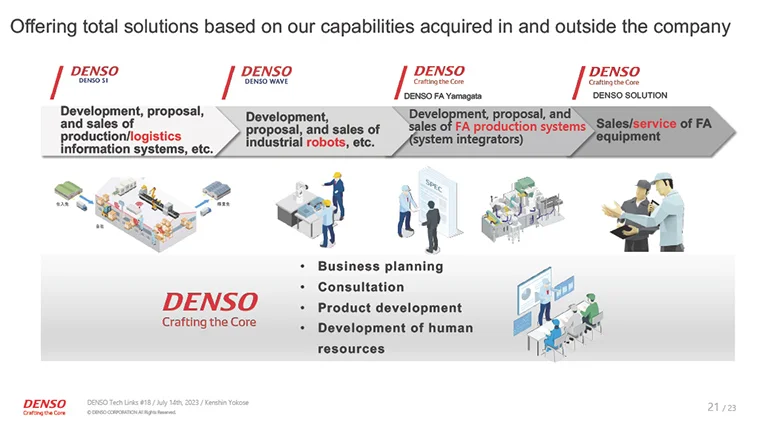
Realization of the World’s Best Manufacturing by Taking Advantage of Our Unique Position as a Manufacturer, User, and System Integrator
DENSO has strengths as a user of advanced production lines, which also undertakes designs and ensures proper use; as a manufacturer to supply robots; and as a system integrator to realize optimal integration. By taking advantage of this unique position, we seek to realize the world’s best manufacturing while enhancing productivity in and outside DENSO.
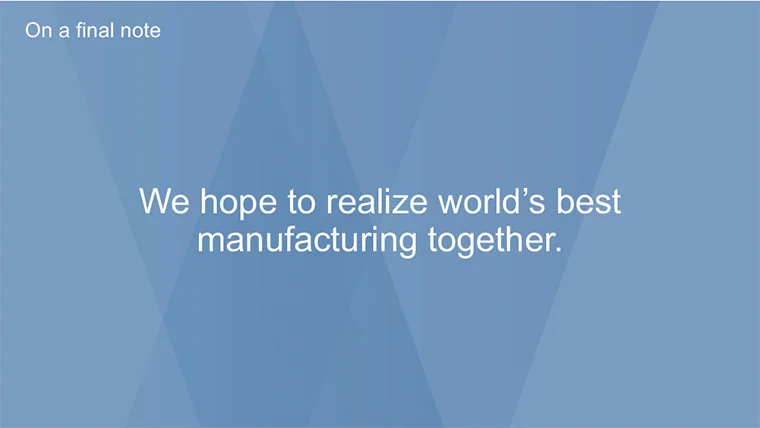
That’s all for my presentation. Next, Mr. Masahito Komiya will give a presentation on what DENSO’s activities look like to the outside world.
Mr. Komiya, please.
Self-introduction of the Speaker
Masahito Komiya: Today I will explain the positioning and unique characteristics of DENSO.
First, let me introduce myself. I work for JIC Venture Growth Investments Co., Ltd., a Japanese government-backed venture capital. We support collaboration and innovation with startups.
Previously, I worked as a consultant for various industries, including the manufacturing industry, and published books on platforms, digital twins, and the metaverse for the manufacturing industry.
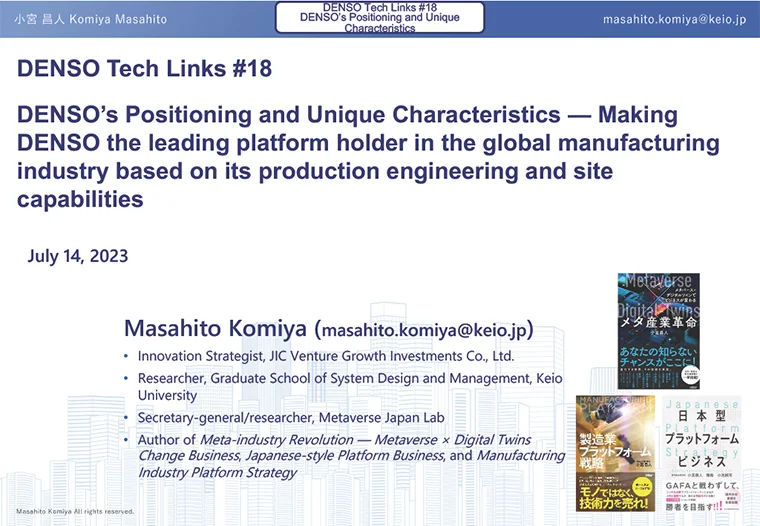
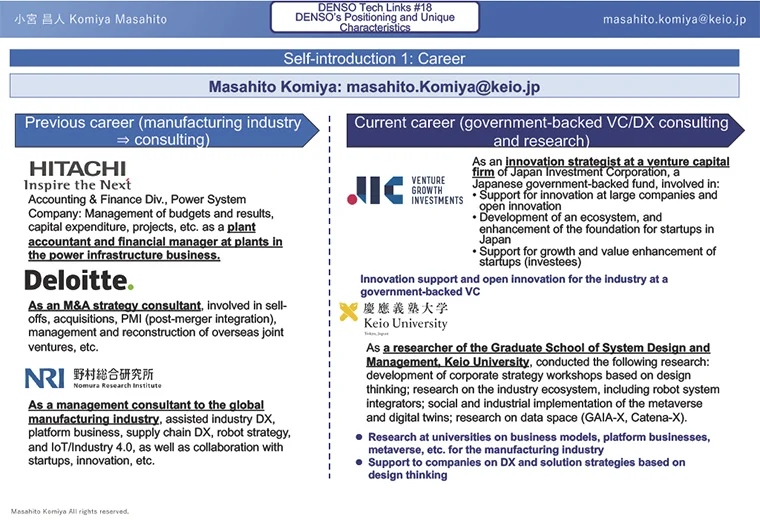
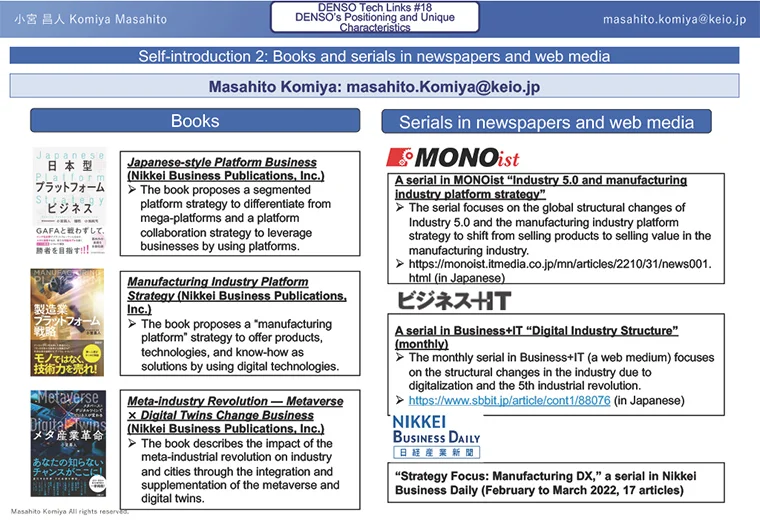
Rapidly Changing Business Model of the Manufacturing Industry
Based on my analysis of global and Japanese manufacturers, I will talk about DENSO’s positioning and developments in the global market.
As explained in the previous presentations, cyber-physical collaboration has become increasingly important due to the digital revolution, which is called Industry 4.0.
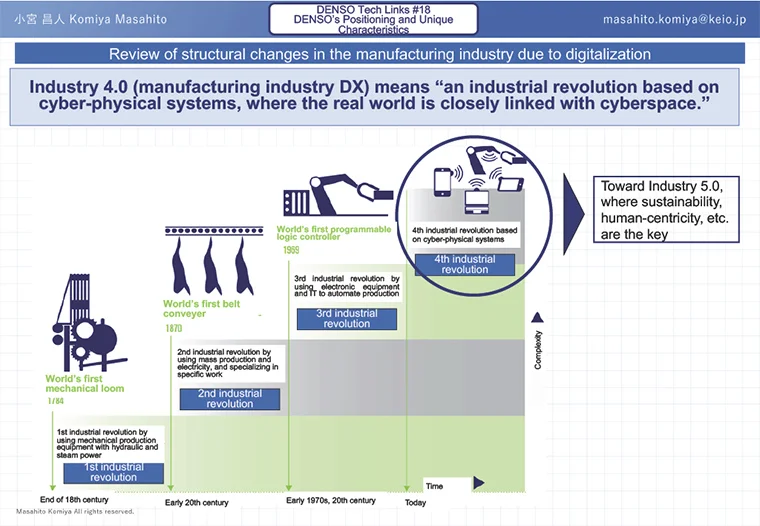
As a result, studies conducted in cyberspace have become closely linked with actual operations.
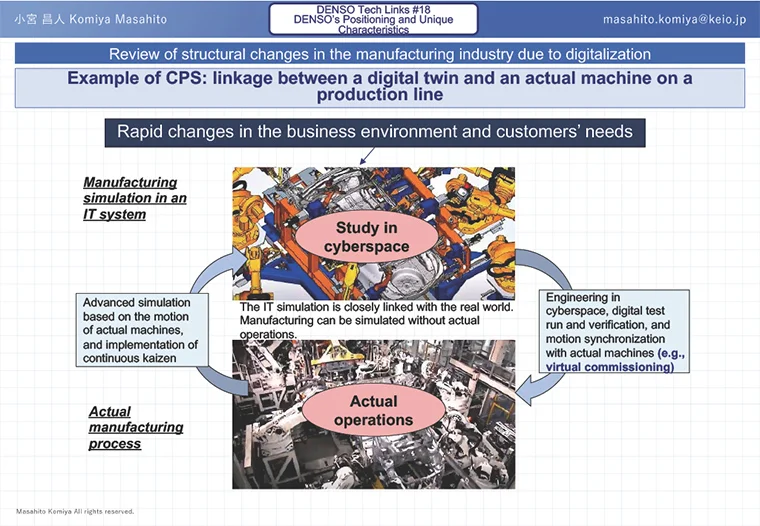
This has brought about changes. Previously, skilled workers were responsible for concept development, design, and practical operations at production sites, and it was difficult to share this workflow as a specific process. Their experience tended to be held as tacit knowledge or by themselves.
Today, their experience can be placed in cyberspace and shared by other members. This helps new members catch up quickly and come up with new ideas, and it also facilitates global collaboration.
The previous lecture mentioned external sales. Companies that have know-how deploy solutions externally. Thus, the business model in the manufacturing industry has been changing rapidly.
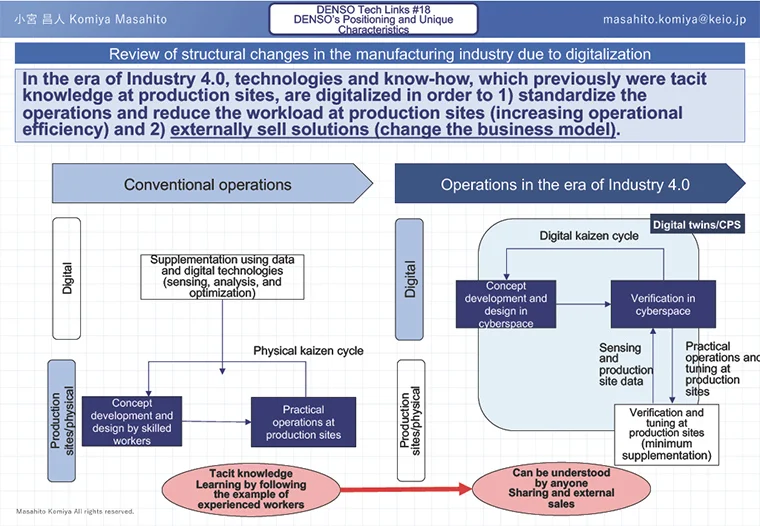
The global market has been undergoing major structural changes. Previously, only companies that had know-how were able to enter the manufacturing industry. However, VinFast, a Vietnamese automaker, purchased a design license from BMW, commissioned the production line builder that had built BMW’s production lines to build the same production line, and used cutting-edge digital tools to catch up.
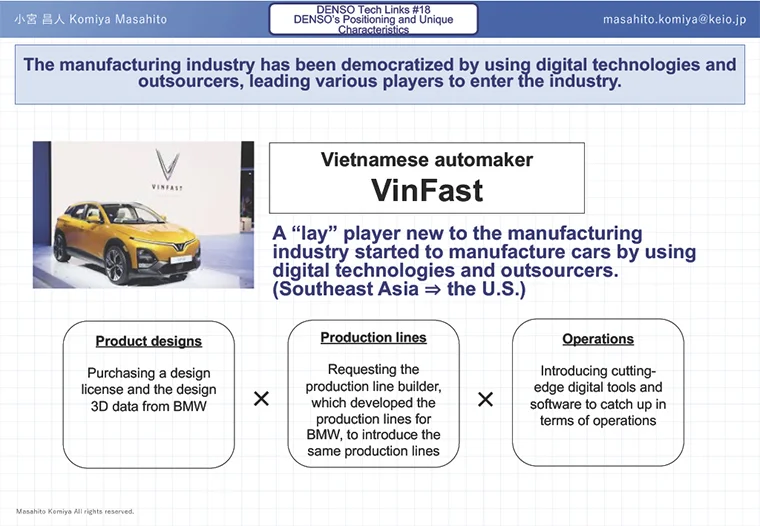
What Do Structural Changes Mean for Japanese Companies?
There are two implications of these structural changes for Japanese companies.
First, with new players entering the manufacturing industry one after another, Japanese companies must consider how to compete with them and which strengths they should focus on to make a difference.
Second, these new players are seeking know-how and technologies accumulated by production sites. Accordingly, a new business model will emerge in which Japanese companies can sell their know-how and technologies in addition to their products.
As the three previous presenters explained, since its founding DENSO has developed technologies based on its commitment to eliminating a loss of even one second or a single defect. By offering these technologies, DENSO can become a platform holder to underpin the global manufacturing industry.
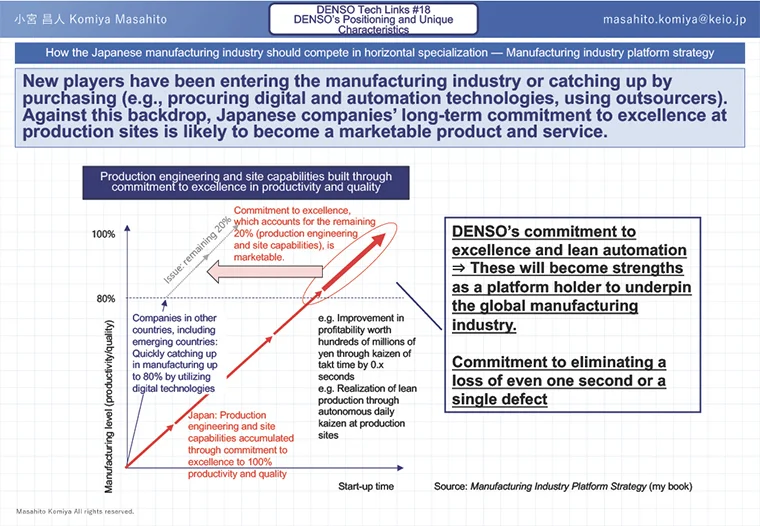
Japanese companies will be able to beat competitors by offering both products and manufacturing technologies. DENSO is the leader in this approach.
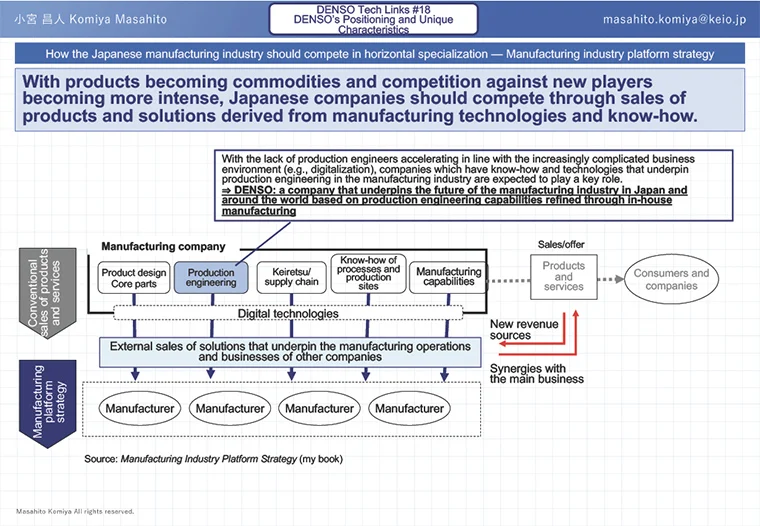
What Matters Most: Production Sites and Technologies Underpinned by Digital Technologies
Specifically, as mentioned earlier, DENSO ensures the proper use of technologies at plants, shares the know-how with other companies, and helps other companies in the manufacturing industry improve their operations. The company provides education about manufacturing and deploys packages and solutions for manufacturing.
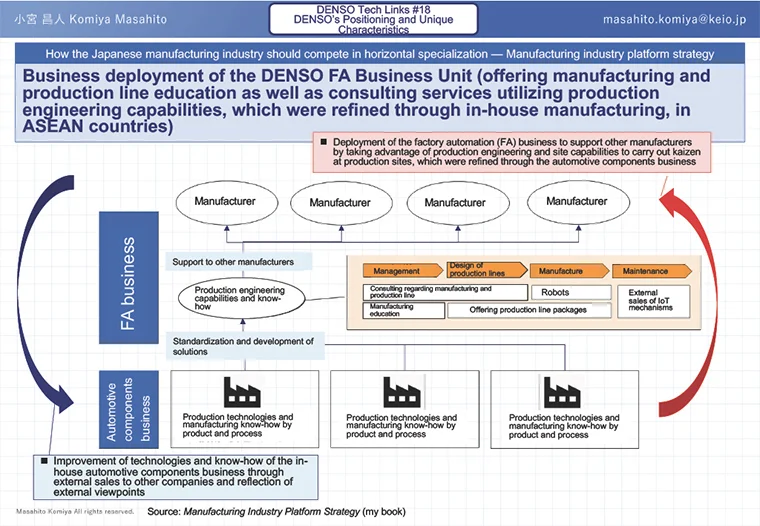
The Lean Automation System Integrators (LASI) in Thailand, which was discussed as an example, is regarded as an important national project by the Thai government. Obviously, cutting-edge robot and digital technologies are important, but the production sites and technologies underpinned by such robot and digital technologies are more important.
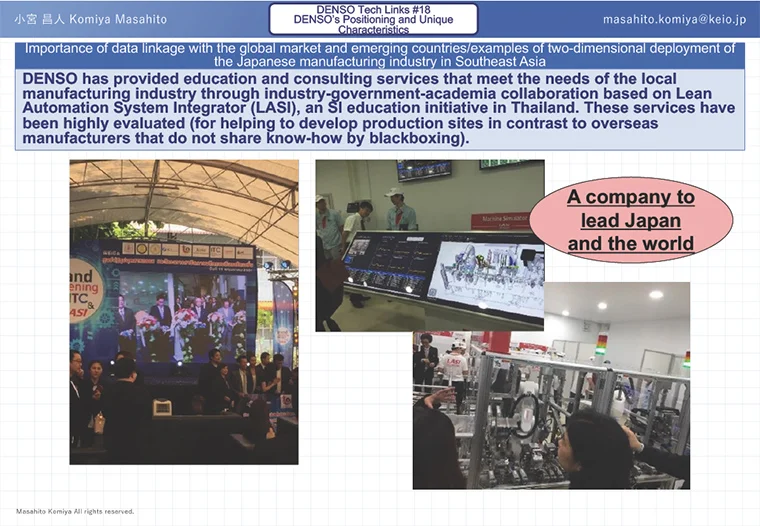
Digital technologies will come into widespread use, and are important as tools. However, other technologies, operations, and know-how to be used in combination with digital technologies are more important.
The previous DENSO presenter explained Lean Automation. DENSO has systematized and refined such technologies, operations, and know-how through trial and error in daily operations throughout its manufacturing history. It is difficult for new players from other industries to build a track record. This is the core of DENSO’s competitiveness to underpin the manufacturing industry. DENSO is likely to become a platform holder to support the global manufacturing industry.
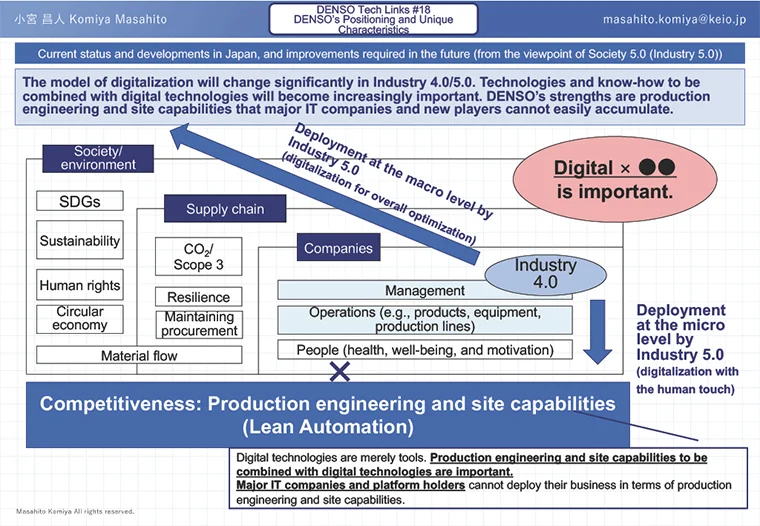
Such strengths are a unique characteristic of DENSO. As mentioned earlier, DENSO improves its technologies, realizes cutting-edge manufacturing, and offers solutions externally through an upward spiral to underpin the global manufacturing industry.
In terms of Japan’s international competitiveness, DENSO can support the manufacturing industry, which is considered a strength of Japan, and can lead Japan, thereby establishing the infrastructure and becoming a platform holder of the manufacturing industry.
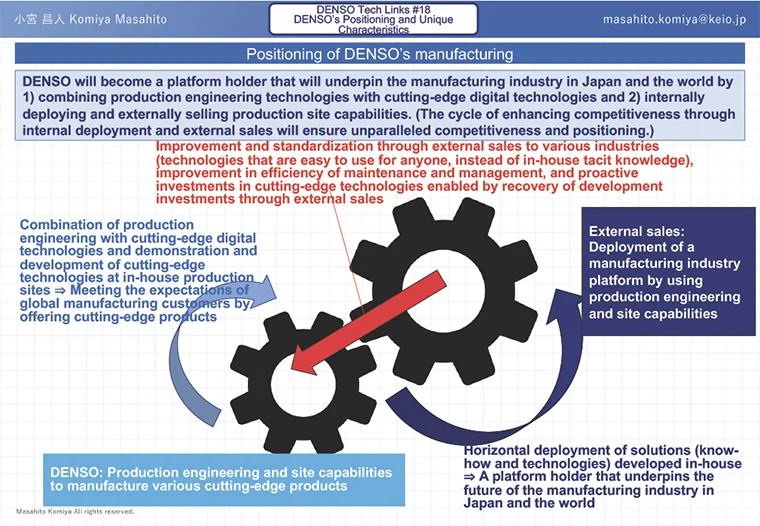
This is an unparalleled model in the world. I have been told that many students are participating in this workshop today. DENSO offers opportunities to work on building a new model for the manufacturing industry, though there is no correct answer. I hope you will strive to change the manufacturing industry in Japan and around the world.
COMMENT
Changing your "Cant's" into "Cans"
Where Knowledge and People Gather.