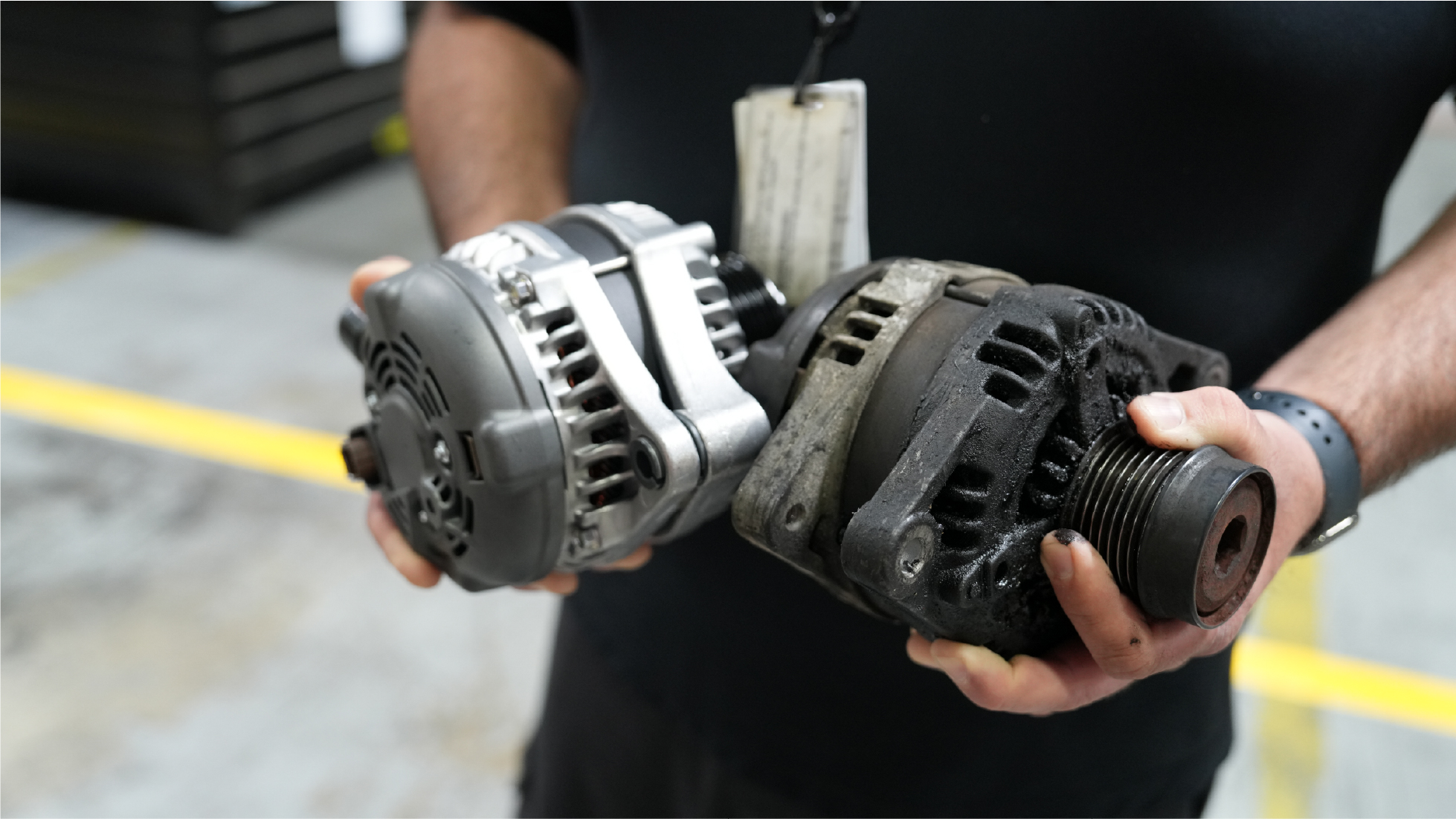
Demand for "Re-man": DENSO Remanufacturing Success
DENSO’s core values of foresight, credibility and collaboration served the company well in the mid-1980s as it launched its remanufacturing operations with a small “re-man” production line in California.
Under the auspices of the DENSO Products and Services America (DPAM) group, a dedicated team began the decade-long process of fine-tuning the engineering, production and marketing capabilities needed to build a successful, high-quality remanufacturing operation.
“We started in 1987 and grew the business deliberately and over time,” said Jaime Franco, Director at DPAM Murietta Operations. “We did marketing research and dealer education, as well as fine-tuned our expertise and production capabilities. Our goal was to focus on DENSO’s quality to separate us from our competitors.”
Changing Business Dynamics
Toyota starters and alternators were the first products DENSO remanufactured in North America. Then, as consumers kept their higher-quality vehicles longer, demand grew, and DPAM expanded to other automakers and a branded option for the aftermarket.
But the challenge back then, and today, was aligning production with periods of market growth and contraction, both in volumes and vehicle production life cycles.
“Remanufacturing is closely connected to OE manufacturing volume,” said Fran Labun, who joined DENSO in 1982 and recently retired as Vice President and General Manager at DPAM. “So, it was important that we built flexibility and responsiveness into our production processes because the market is always fluctuating."
Getting Started in Temecula
DPAM’s first production line was in Temecula, California, where the team developed the essentials of remanufacturing. They identified salvageable parts, distinguished product specifications, established manufacturing quality and efficiencies, and secured customer approval to use remanufactured parts for warranty replacement.
“This was a brand-new activity for DENSO, and DPAM had to understand what could be reclaimed and reused, how products degraded over time, and which items had to be 100% replaced. Our standard was driven first by quality, then by cost efficiencies and resource uses,” Labun explained.
But early customers weren’t beating down the doors for remanufactured parts. In fact, DPAM had to overcome dealer resistance and negative perceptions created by lower cost, lower quality products from competitors.
Show and Tell
Market skepticism wasn’t new to DENSO, and the team understood their products would speak for themselves. Armed with a cutaway parts display, team members went from dealership to dealership, and to dealer open-house events to showcase the OE quality and precision remanufacturing of the parts.
It was classic DENSO face-to-face customer relationship building … and it worked. Once DENSO branded the parts as genuine OEM, the last barrier to a wellspring of business was all but eliminated.
“Our customers were responding to two market dynamics at the time: costlier parts because of import tariffs – DENSO wasn’t manufacturing parts in North America at that time – and increasing parts complexity from electronics. From a marketing perspective, we had to balance the cost savings message with perceptions about quality and educate customers, retail and consumers, that ‘reman’ standards, were like new,” Labun explained.
The Circular Economy
In 2003, DPAM added heavy-duty starters and alternators to its product lineup and has earned, numerous times, the prestigious Caterpillar Platinum Supplier Quality Excellence Process certification.
Today, DPAM’s remanufacturing business is in Murrieta, California, and includes a suite of products – starters, alternators, diesel fuel injection for common rail systems – and is a significant revenue source.
Perhaps most important though are the nearly 700,000 parts recycled annually.
Watch the Company Spotlight video featuring DENSO's Murrieta, California location.
“Remanufactured parts are a key contributor to the circular economy,” Franco shared. “At DENSO, that means we capture DENSO quality components, replace the worn elements and reintroduce them back into the auto parts ecosystem rather than directing them to landfills. In doing so, we support our two Great Causes: Green and Peace of Mind.”