Did you find this article helpful for what you want to achieve, learn, or to expand your possibilities? Share your feelings with our editorial team.
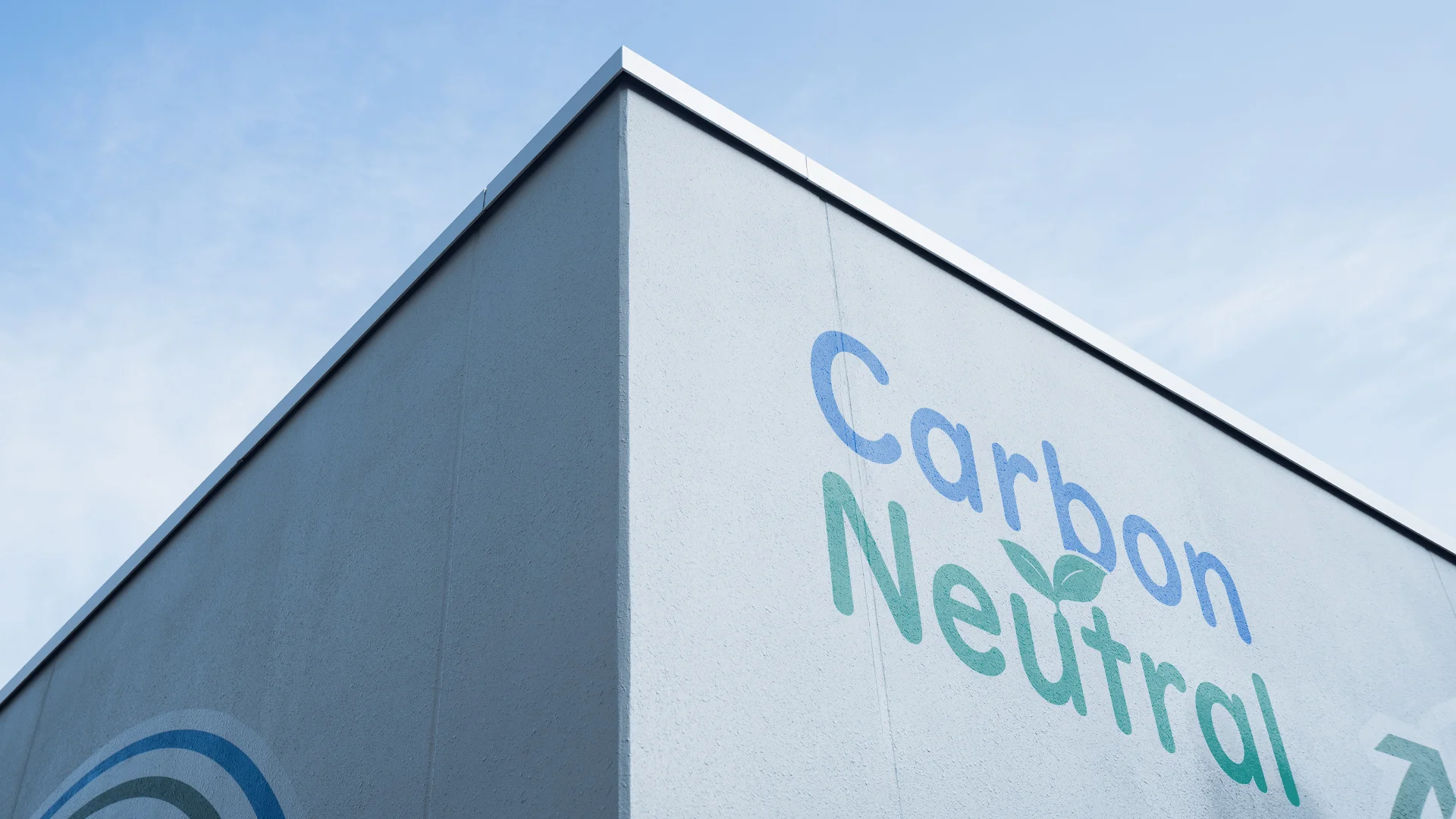
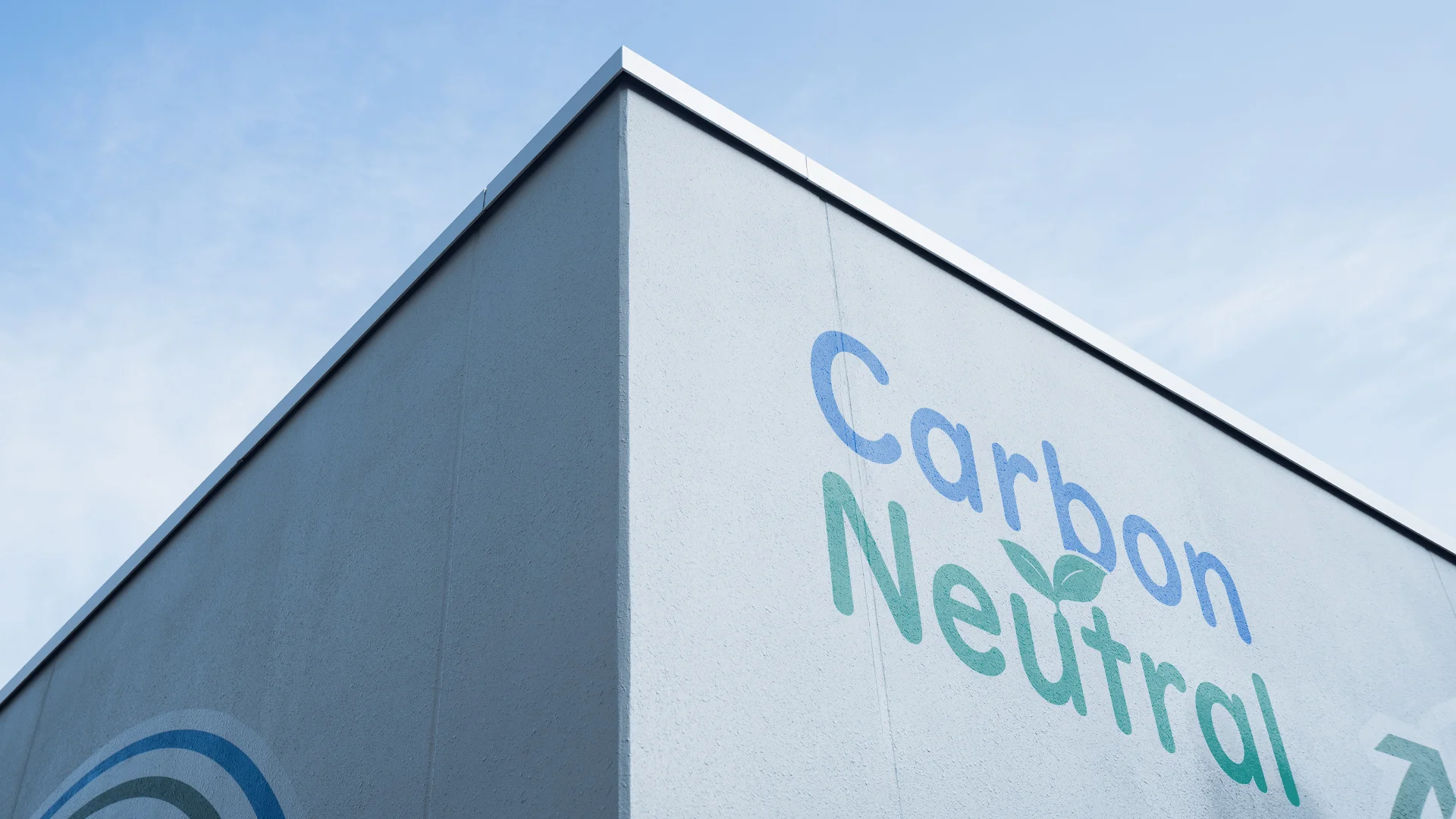
May 31, 2021
VISION & IDEAWorking for a better future: zero CO2 emissions as the norm for manufacturing
DENSO aims to become the leader in CO2 emissions capture and reuse through the development of CO2 recycling plant technologies.
Manufacturing operations inevitably generate CO2emissions. In order to alter this seemingly undeniable reality, DENSO came up with the idea of converting CO2back into an energy resource, thus transforming emissions from a problem into an asset. Let’s take a look at the amazing system that makes it possible.
Contents of this article
CO2is not the problem
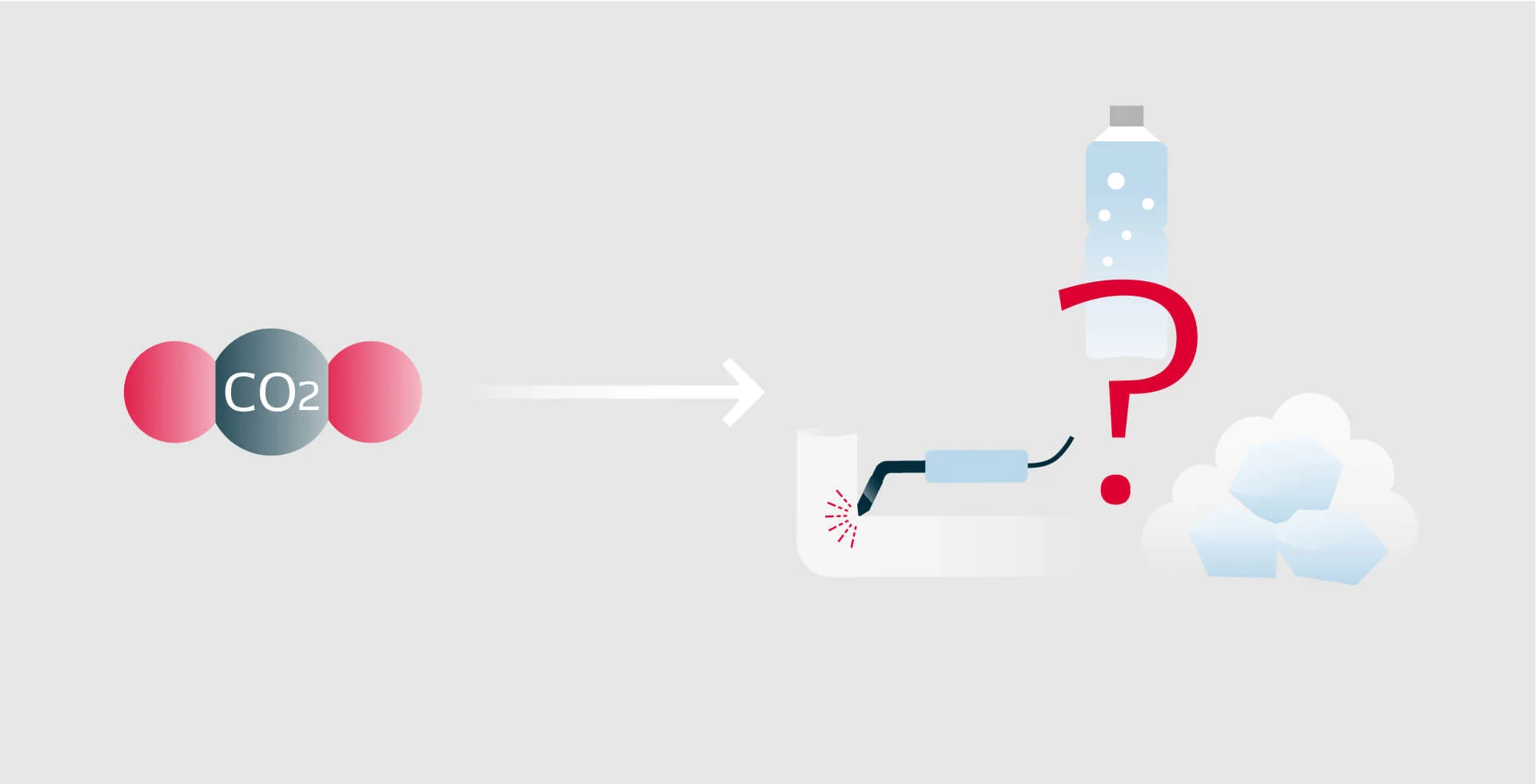
People tend to have negative perceptions of carbon dioxide (CO2). We all learn in school that it is a cause of global warming, and daily TV news often emphasizes the need to reduce CO2emissions as a means of solving environmental problems. In recent years, companies have placed increasing importance on the achievement of the Sustainable Development Goals (SDGs), and to this end they have proactively pursued measures to reduce their CO2emmisions.
All of the above indicate that CO2is the problem, but in reality it is used in our everyday life. Take carbonated beverages or dry ice, for example—both of these use CO2as a base ingredient. In manufacturing operations, meanwhile, CO2is important for preventing oxidation in metal welding and steelmaking. Furthermore, continuing research on CO2-based material applications shows the potential for using CO2to create plastic and concrete materials.
It goes without saying that reducing the growing volumes of CO2emissions throughout our society is vital, but we must remember that CO2itself is not the problem. In fact, making wise use of CO2can surely transform it into an asset. But how does one accomplish this?
The importance of CO2 recycling in the future
The Paris Agreement, adopted by the United Nations in 2015, is part of an international framework for measures against climate change. The Agreement includes a pledge by more than 120 countries and regions to achieve “carbon neutrality” by the year 2050.
Carbon neutrality refers to net-zero CO2emissions into the atmosphere, achieved through absorption of the same amounts of CO2that are output as emissions. In order to accomplish this, it is generally considered necessary to (1) save energy by improving energy efficiency, (2) change energy from fossil fuels to renewable energy, and (3) capture and recycle any CO2emissions that still occur despite the previous two improvements.
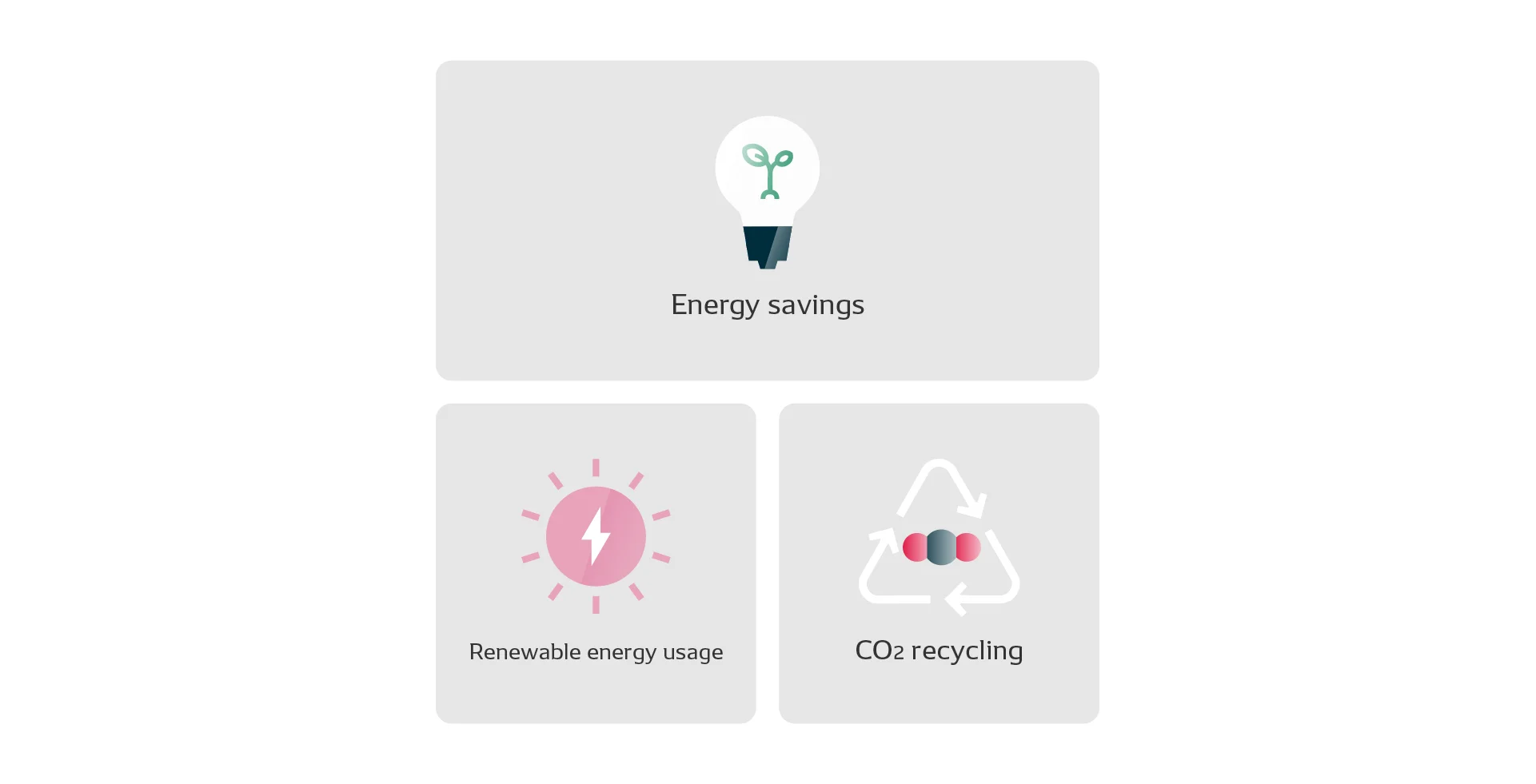
Among these, the development of CO2recycling technologies is expected to be particularly important.
Over the last tens of years, Japan has refined and improved its energy-saving technologies and thus reduced CO2emissions, but it is impossible to completely eliminate CO2emissions if we are to continue living our lives and our companies are to continue their business. In other words, there is a limit to how much we can reduce emissions.
We want to pursue better lives for humankind while also protecting the global environment, which means developing methods for recycling and reusing CO2emissions. With this in mind, DENSO is blazing a new trail with the end goal of carbon neutrality.
If we don’t do it, who will?
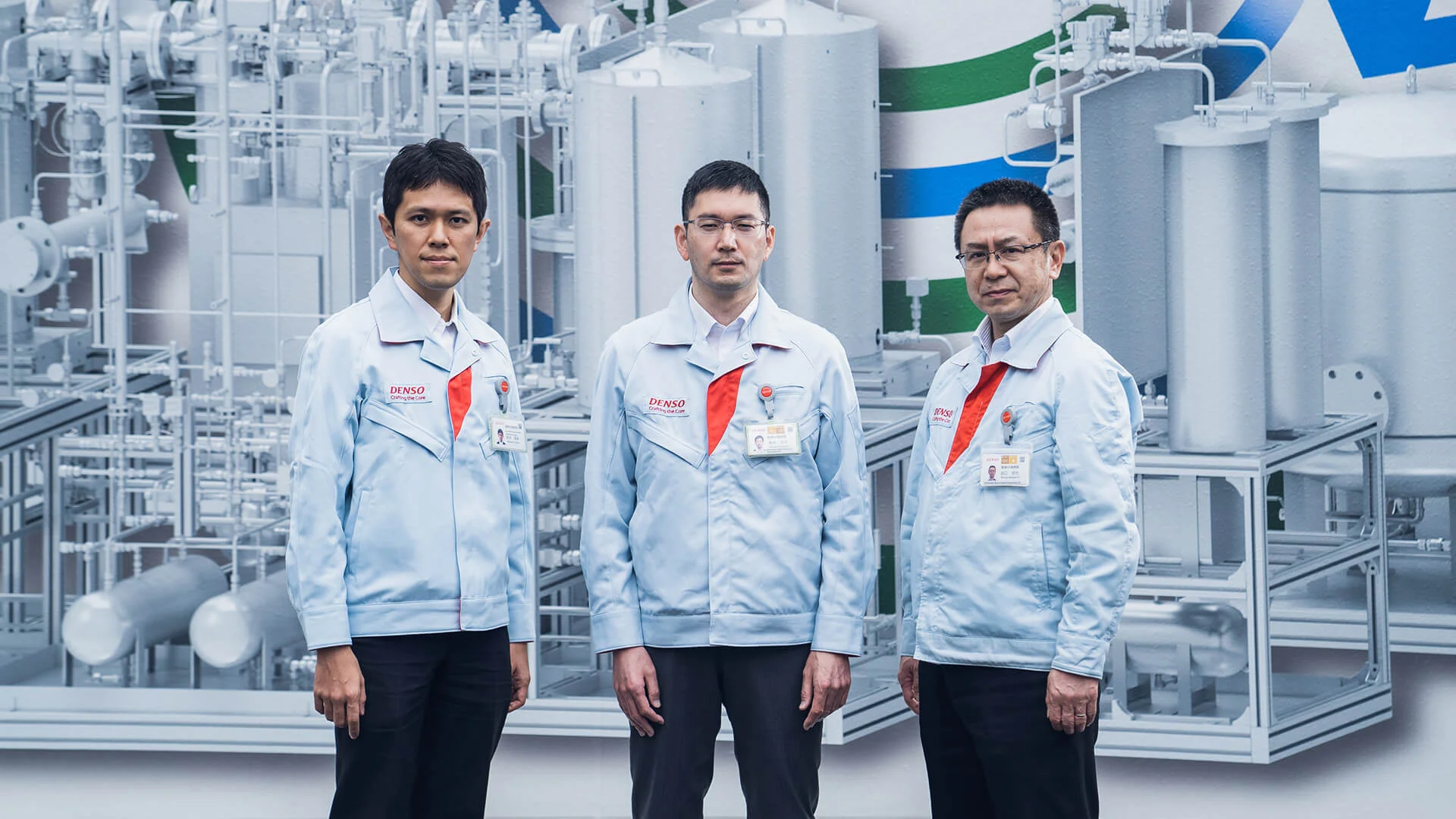
In 2020, DENSO pledged to achieve carbon neutrality in corporate activities by the year 2035. This is an earlier deadline than that stated in the Paris Agreement, and in order to reach this goal DENSO has been undertaking various measures in existing mobility product operations, manufacturing and other such areas, as well as in new energy-use fields. Among these efforts, one of the company’s central undertakings has been a project to develop a CO2recycling plant.
In accordance with the aforementioned three means of achieving carbon neutrality, DENSO has placed high priority on, and already implements numerous measures related to, the first two through measures to increase energy efficiency and expand electrification at production facilities, and through switching our energy to renewable energy sources in operations. In these ways, the company has made great efforts to eliminate CO2emissions wherever possible. However, electrification is impossible in certain operations, and the use of renewable energy can sometimes prove difficult—such as furnaces, which inevitably generate CO2.
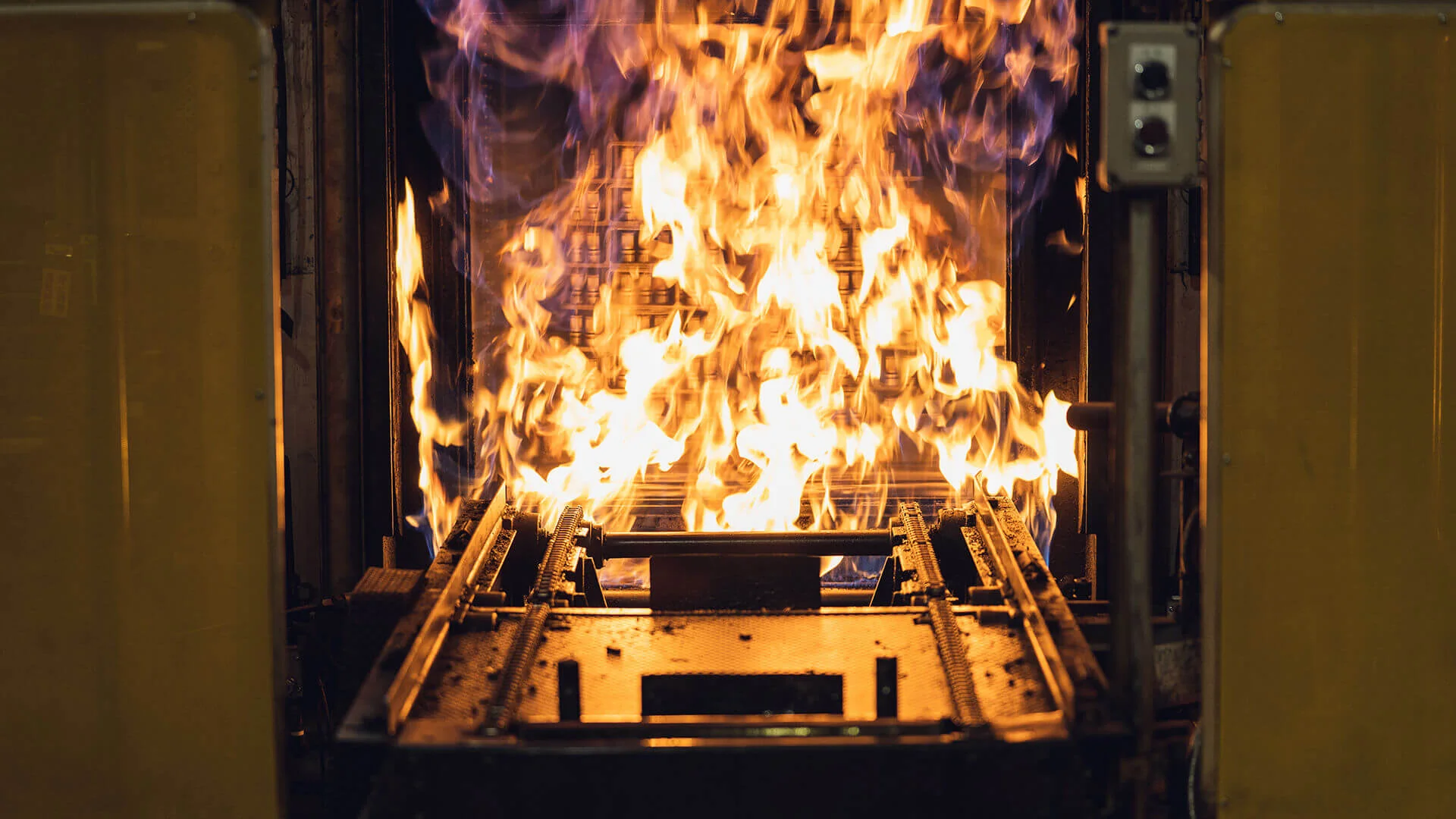
Even if such emissions are kept small, they cannot be overlooked if the company is to achieve true carbon neutrality. That’s where the CO2recycling plant concept comes in: this type of facility captures CO2gas emissions from production operations and binds the CO2with hydrogen (H2) to synthesize methane gas (CH4), which can then be used as fuel by production facilities. The result is a sustainable system in which the CO4exhaust gas produced by combusting fuel is not released to the outside, but instead is captured and used as a material to produce more fuel.
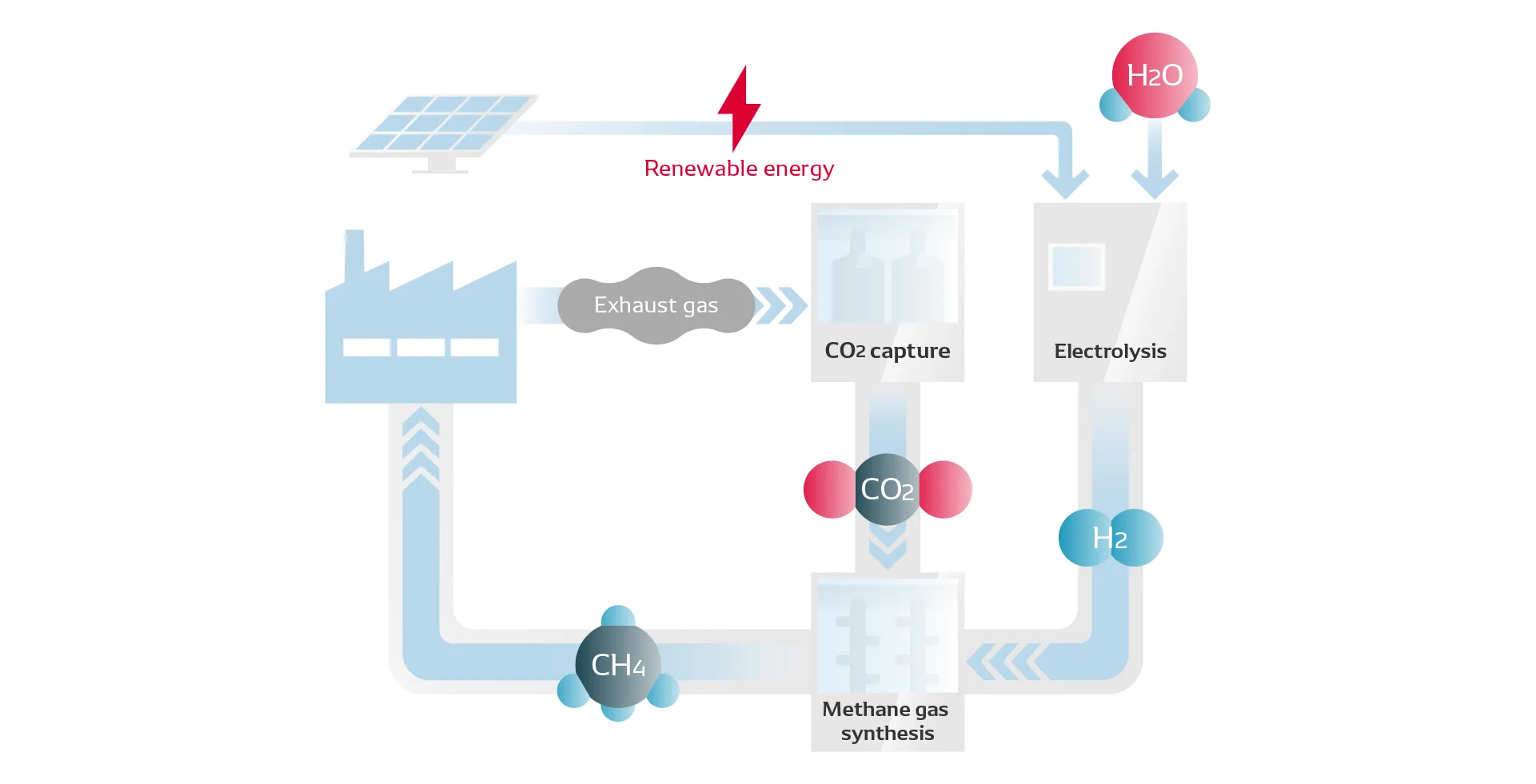
None of DENSO’s existing divisions had the experience or technologies necessary to build this plant, but project members were still determined to make it themselves. Shinya Sakaguchi, a member of the Environment Neutral Systems Development Div. and that of the project, explained,
Currently, CO2capture and recycling technology development has already been at the demonstration testing phase. But it is available only in the large-scale facilities with high CO2-rich emissions, such as thermal power plants and steelworks.
It’s because current CO2capture technologies have poor efficiency and they are available only for CO2-rich emissions. Compact solutions that capture CO2efficiently from the emissions of ordinary manufacturing facilities with the lower CO2level does not exist.
DENSO, a member of the manufacturing industry, has the tough challenge of achieving carbon neutrality by 2035, and we can’t wait for outside help to give us the advanced technologies we need. We must develop them ourselves. That’s why DENSO determined to become the leader in CO2capture technologies for the manufacturing industry.
Project members had the strong will that they must be more proactive and self-motivated in order to realize carbon neutrality for the company, and had kept the plant project moving forward. In July 2020, just 20 months or so after the initial project conception, DENSO completed its first-ever plant capable of recycling CO2.
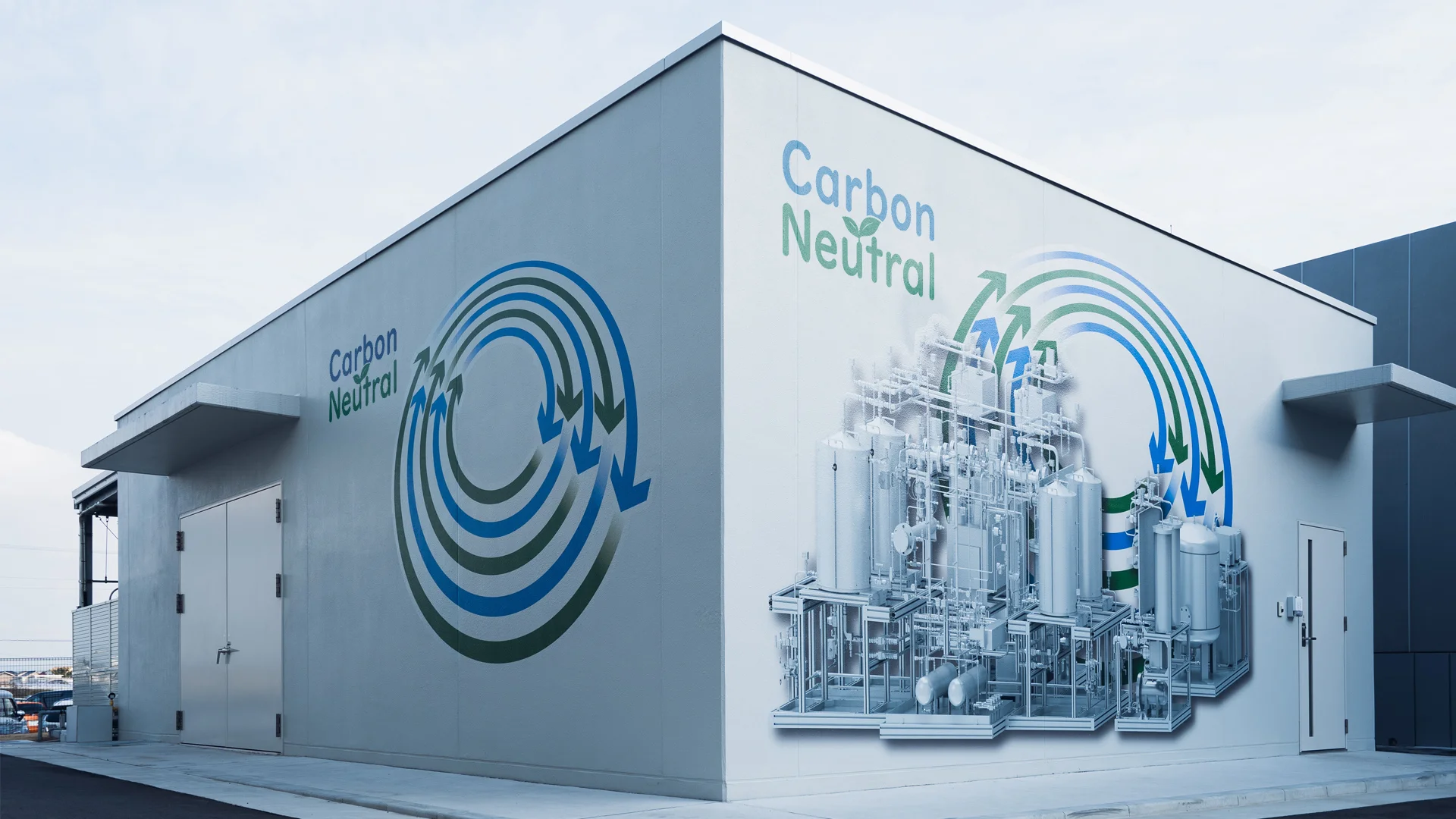
However, the current plant is still a prototype. Masayuki Suzuki, another member of the Environment Neutral Systems Development Div. and project member, believes that the completion of this first plant has enabled the team to understand what they should improve in the plant to make it more realistic to be introduced to manufacturing facilities. “We have two main challenges to make the plant available in the manufacturing facilities.” said Suzuki.
One is how small we can make the plant. In the extreme case, current CO2plants may require its site area as same as that of manufacturing facilities which the plants are attached to. If so, almost all manufacturers will give it up to introduce the plants to their facilities because they do not have enough area to do it. That’s why it’s so important to minimize the size of the recycling plant so that it can be introduced to existing manufacturing facilities.
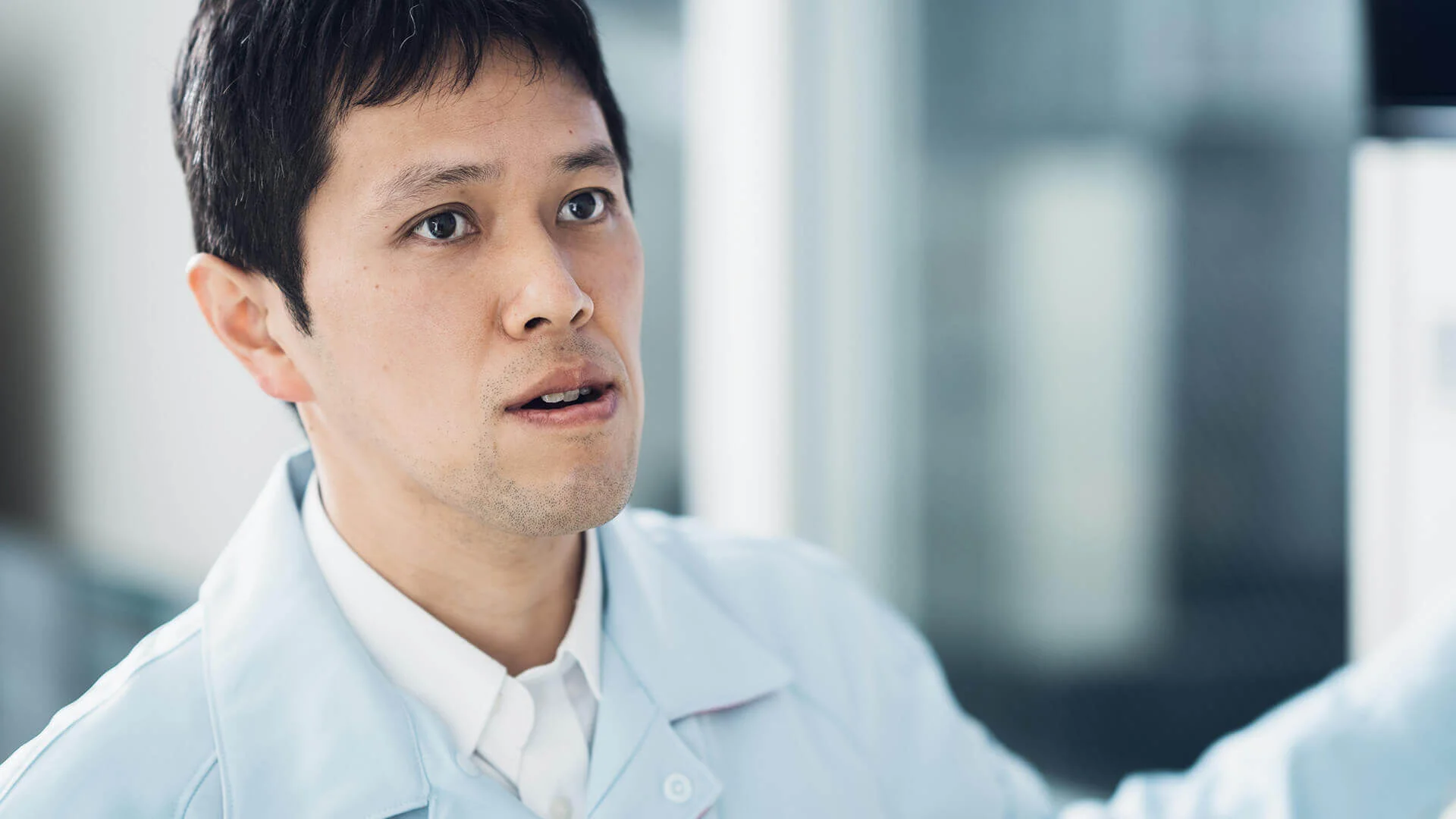
The other is how energy-efficient it can be made. Large amounts of energy are required to capture CO2and to synthesize fuel. If the recycling process requires as much energy as it produces, the approach is pointless. It’s a challenge of how few energy we can capture CO2and synthesize methane gas with. In order to promote the widespread adoption of this type of CO2recycling system, it is crucial that we boost energy efficiency and reduce operational energy costs to attain a positive net balance, because energy costs directly affect overall energy efficiency.
We cannot clear all of our challenges with the current plant that has been built through trial and error without efficient knowledge and experience. But DENSO is developing new technologies with it to put CO2recycling plants into practical use.
Automotive technologies at the core of CO2 recovery
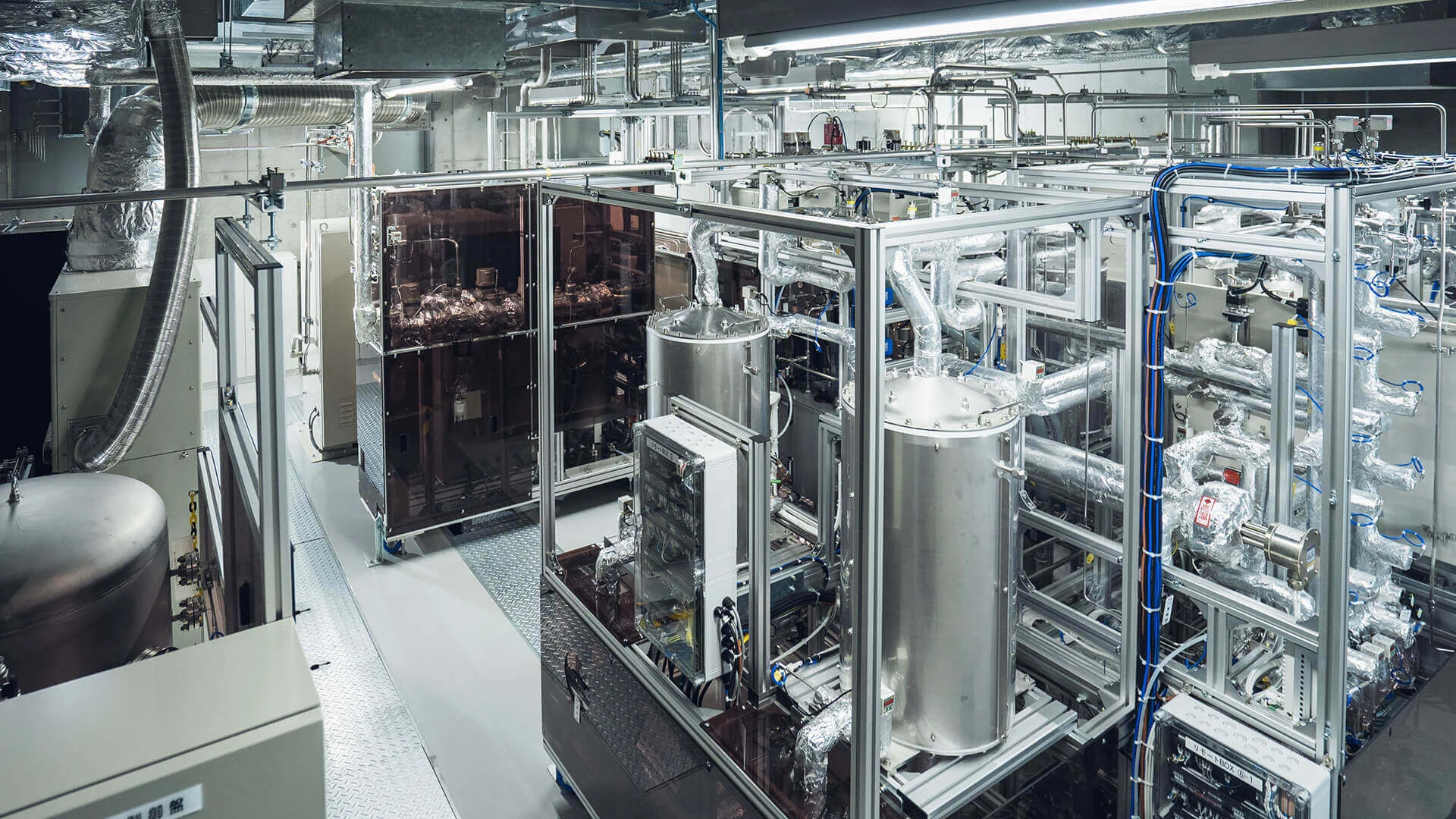
Project members are currently developing technologies that will help them clear the hurdles of plant size reductions and efficiency improvements to realize a sustainable CO2recycling plant.
The key factor in these efforts is the development of new materials. Yohei Morimoto, also from the Environment Neutral Systems Development Div. and a project member, excitedly explained that such materials are the key to plant size reductions and efficiency optimization.
In general, the CO2capture process uses large amounts of heat, so the heat loss must be minimized to increase efficiency. My team, however, is researching a CO2capture process that does not use heat. Our approach requires CO2-absorbing materials.
, said Morimoto.
Previous development efforts involved few changes to absorptive materials while finding ways to minimize heat requirements. However, this approach cannot attain the operating efficiency the world demands. In response, we came up with an entirely new approach of creating new absorbent materials that capture CO2with “available energy with less loss to the outside of system”, such as pressure.
The absorption efficiency of our current materials is not high, so we have to use a large capture device in order to capture large amounts of CO2.It means that better absorption efficiency makes the capture device smaller, and it also makes the plant more downsized.
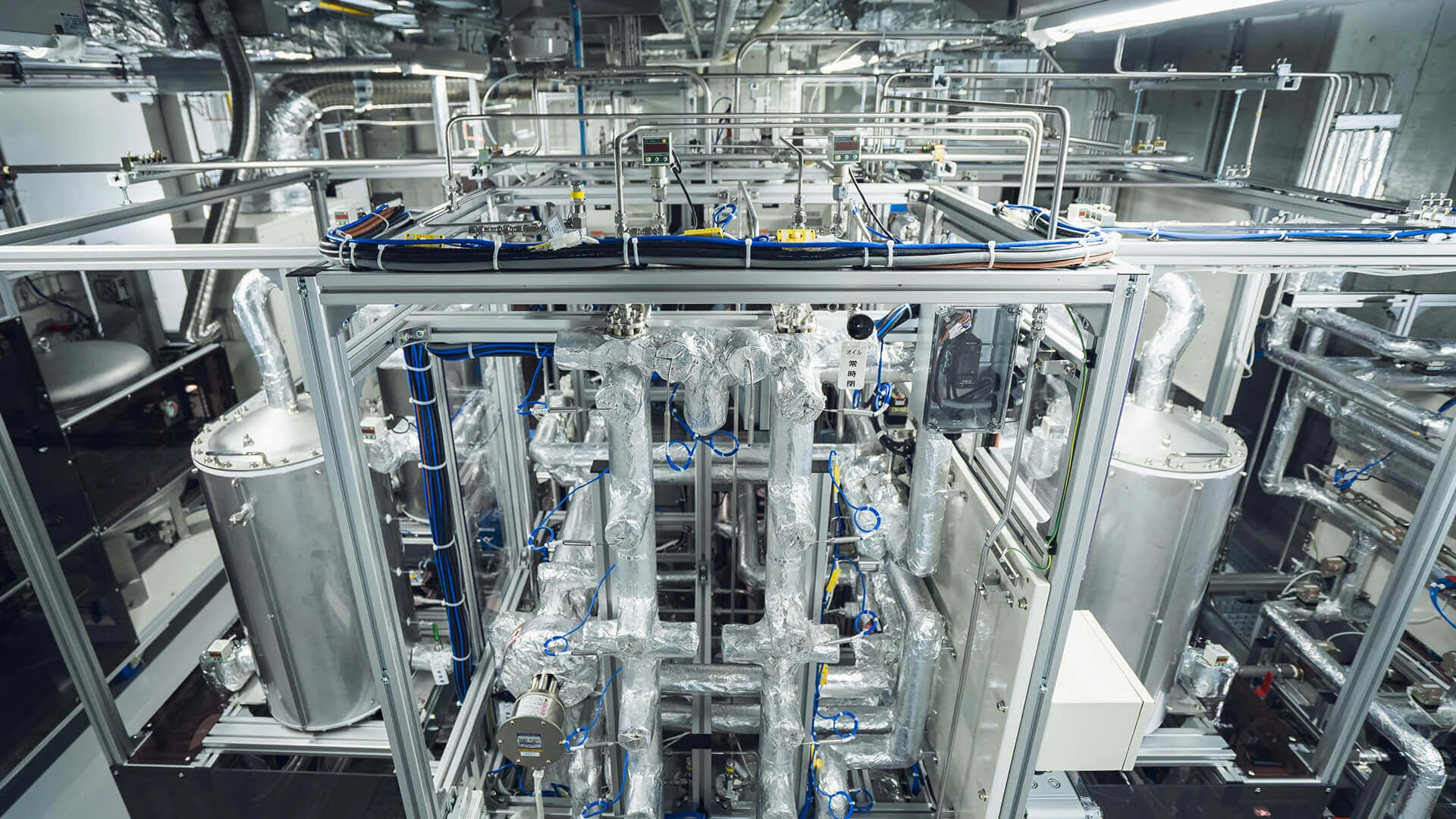
DENSO has developed technologies for absorbing nitrogen oxides (NOx) and other harmful substances via catalysts in the post-processing of car exhaust gases. Project members believed that these harmful car-exhaust substances and CO2are same in the absorption mechanism, and they could improve the existing CO2absorption materials radically by applying the existing absorption technology although objects of the technology are different.
We haven’t achieved our target yet, but we can say for certain when we create an absorbent material with ten times the absorptive capacity of existing materials. Materials development is out of our fields, so we have been working with partners outside of DENSO.
We believe that the core of realizing carbon-neutral for DENSO is the achievement of small-sized, high-efficiency CO2capture devices. By further refining the relevant technologies, we should be able to capture not only CO2from factory emissions, but also low-concentration CO2emissions from the air, which would enable capture operations in an even wider range of locations.
, said Morimoto.
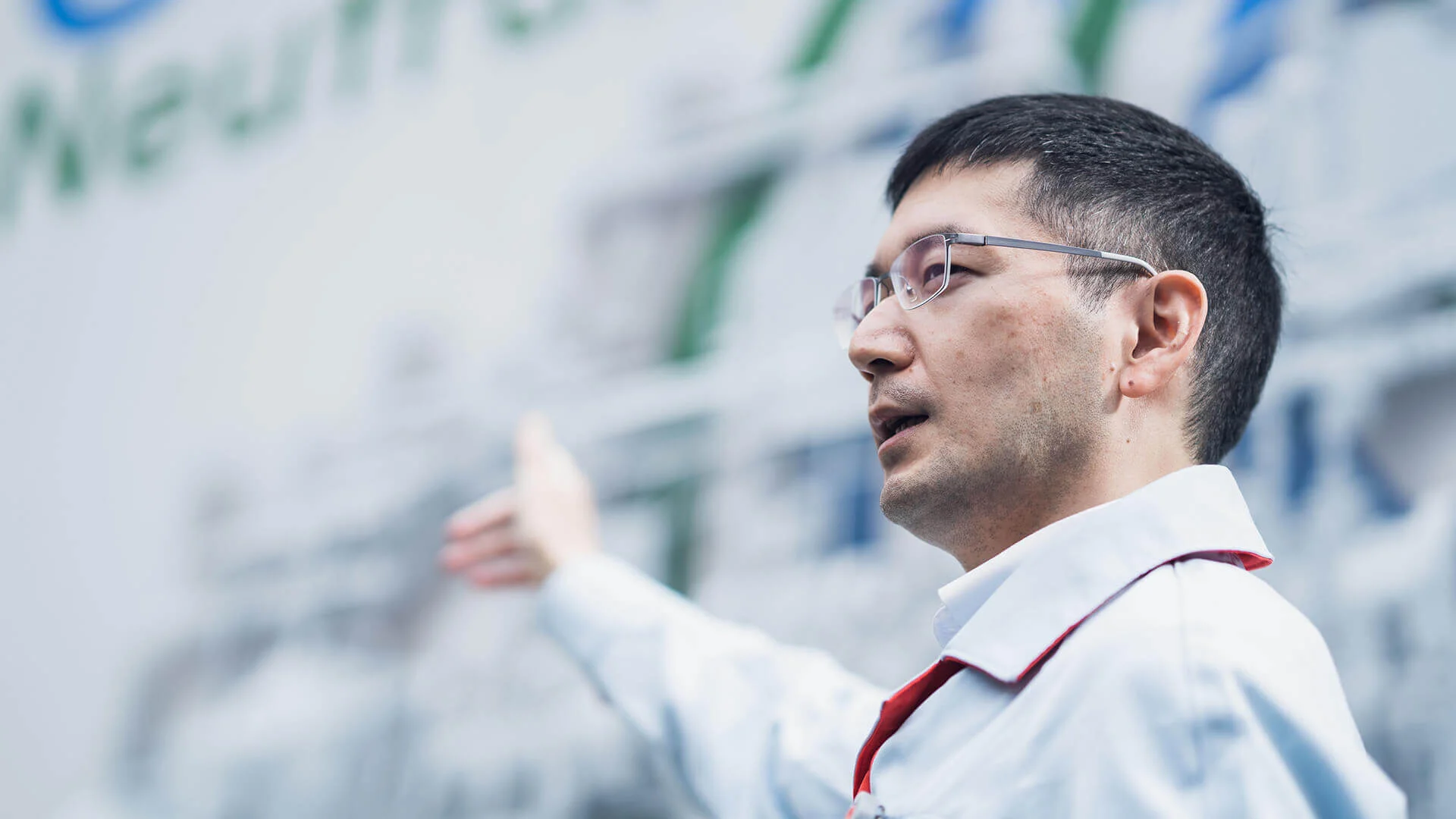
In addition to equipment miniaturization, DENSO aims to apply existing technologies to improve efficiency as well.
Morimoto elaborated:
The stereotypical approach cannot achieve economic rationality due to its theoretical limit of chemical reaction. In order to resolve the imbalance between economic efficiency and physical realities, we must collect heat and utilize its energy through recycling rather than throwing it away as was previously done. DENSO has long focused on thermal management in automobiles and excels in this area.
Added Sakaguchi,
As a systems supplier, DENSO is highly experienced in system management technologies. CO2capture and recycling involves multiple types of equipment operating together—CO2capture equipment, methane production equipment, hydrogen production equipment and so forth—and by controlling all of these as one system, rather than individually, it becomes possible to achieve optimal results.
This perspective is important not only within the CO 2recycling plants, but also in the cooperation between CO2plants and factories. It is pointless that CO2plant cannot supply energy whenever and however much factories demand them. We have to work on the overall management to synthesize fuel and to supply heat according to demand of factories.
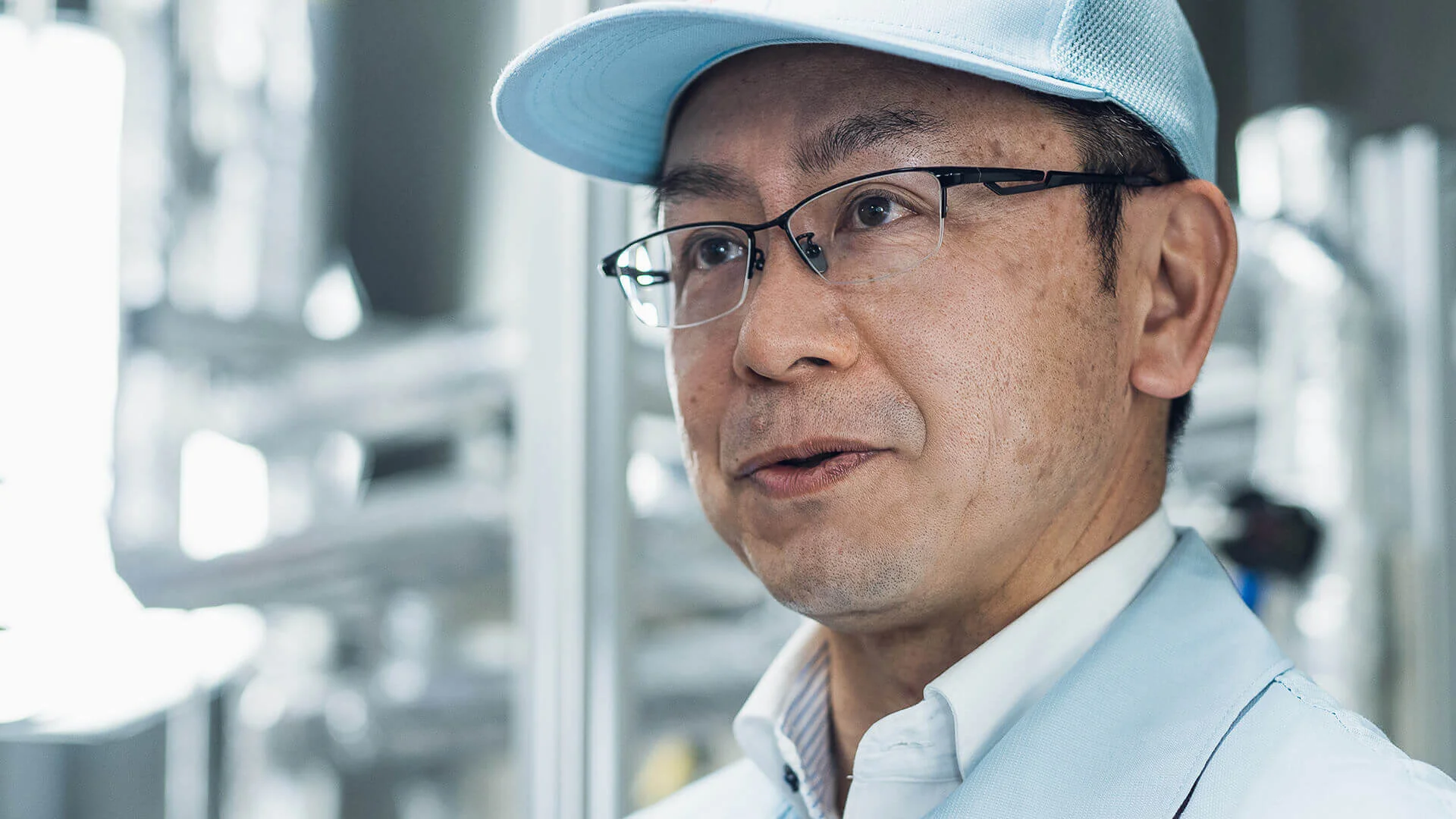
DENSO has polished up many technologies, such as technology to purify the emissions of automobiles, that to recycle the waste-heat of automobiles, and system management technology. They are now changing to the irreplaceable inventions to solve the environment problems. Engineers are now trying to spread CO2plants in many factories.
"In addition to completing the development of our CO2recycling system, we also want to make sure it becomes widely used," explained Sakaguchi.
Because this is a new type of system, a lot of manufacturing facility operators doubt whether it can actually be used at their factories. Therefore, as a first step, we are making continual improvements at the Anjo Plant to firmly prove what we can do, for all to see. After this, we want to install the same types of CO2recycling facilities in other DENSO plants around the world to demonstrate they work in any environments. Through these efforts, we believe we can disseminate the system widely.
"We can’t accomplish a CO2recycling system on our own," added Suzuki.
That’s why it’s so important to work closely with various partner organizations. We are determined to hand over a healthy and comfortable world to the younger generations, who will become our leaders in the future. That’s what motivates us to keep moving forward in this project.
Carbon neutrality for the entire manufacturing industry
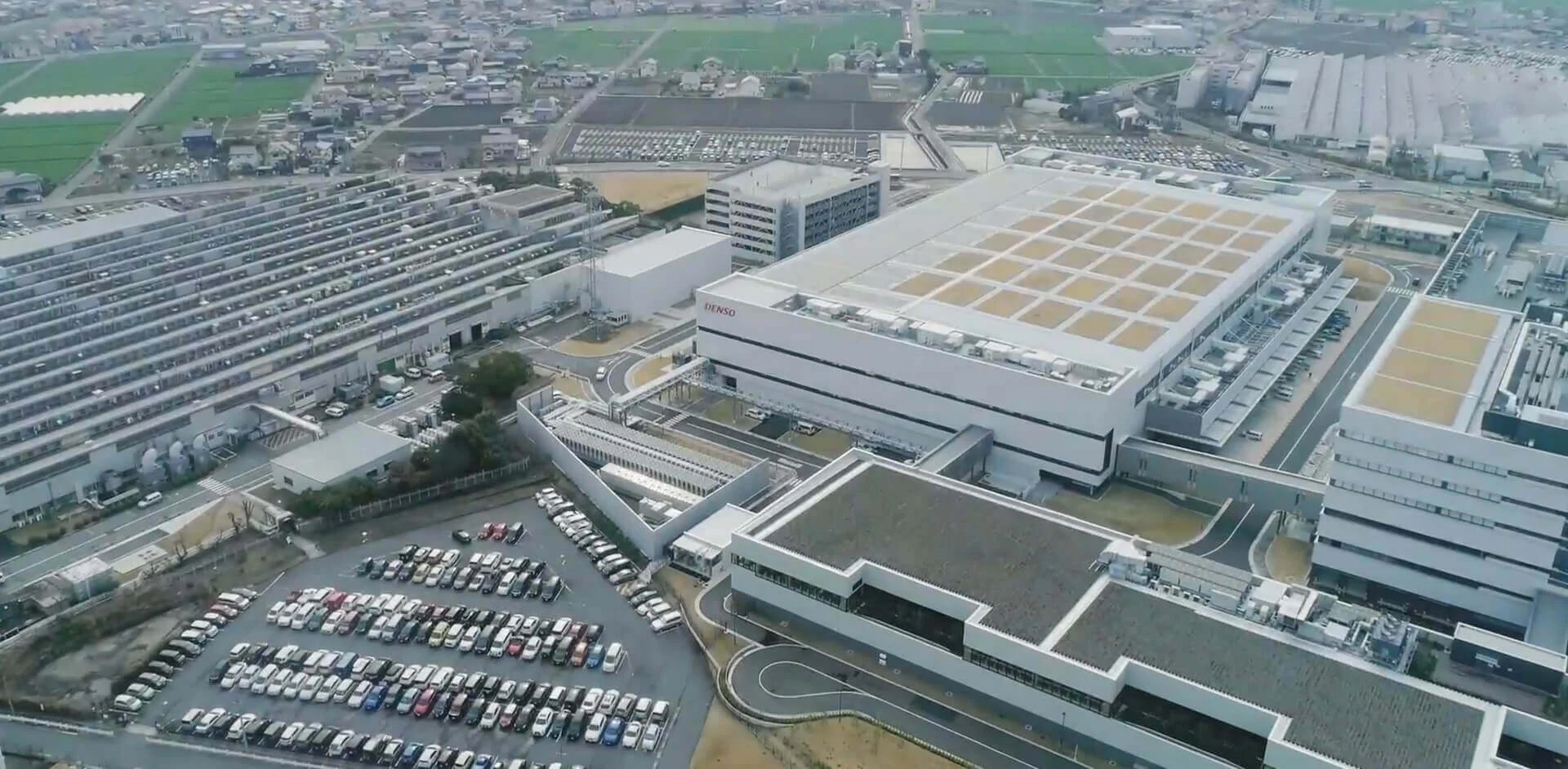
Stating carbon neutrality as a goal is easy. Actually reducing net emissions to zero, however, seems nearly impossible considering the current levels of CO2output. Regardless, DENSO has pledged to achieve this goal and is working toward that promise, despite the daunting challenges involved.
DENSO does not want to pass down the problems of today’s world to future generations. In order to realize a world in which a clean manufacturing industry that produces no CO2emissions is the norm rather than an exception, DENSO will continue to refine and improve its technologies, serving as a leader in the pursuit of global carbon neutrality.
COMMENT
Changing your "Cant's" into "Cans"
Where Knowledge and People Gather.