Did you find this article helpful for what you want to achieve, learn, or to expand your possibilities? Share your feelings with our editorial team.
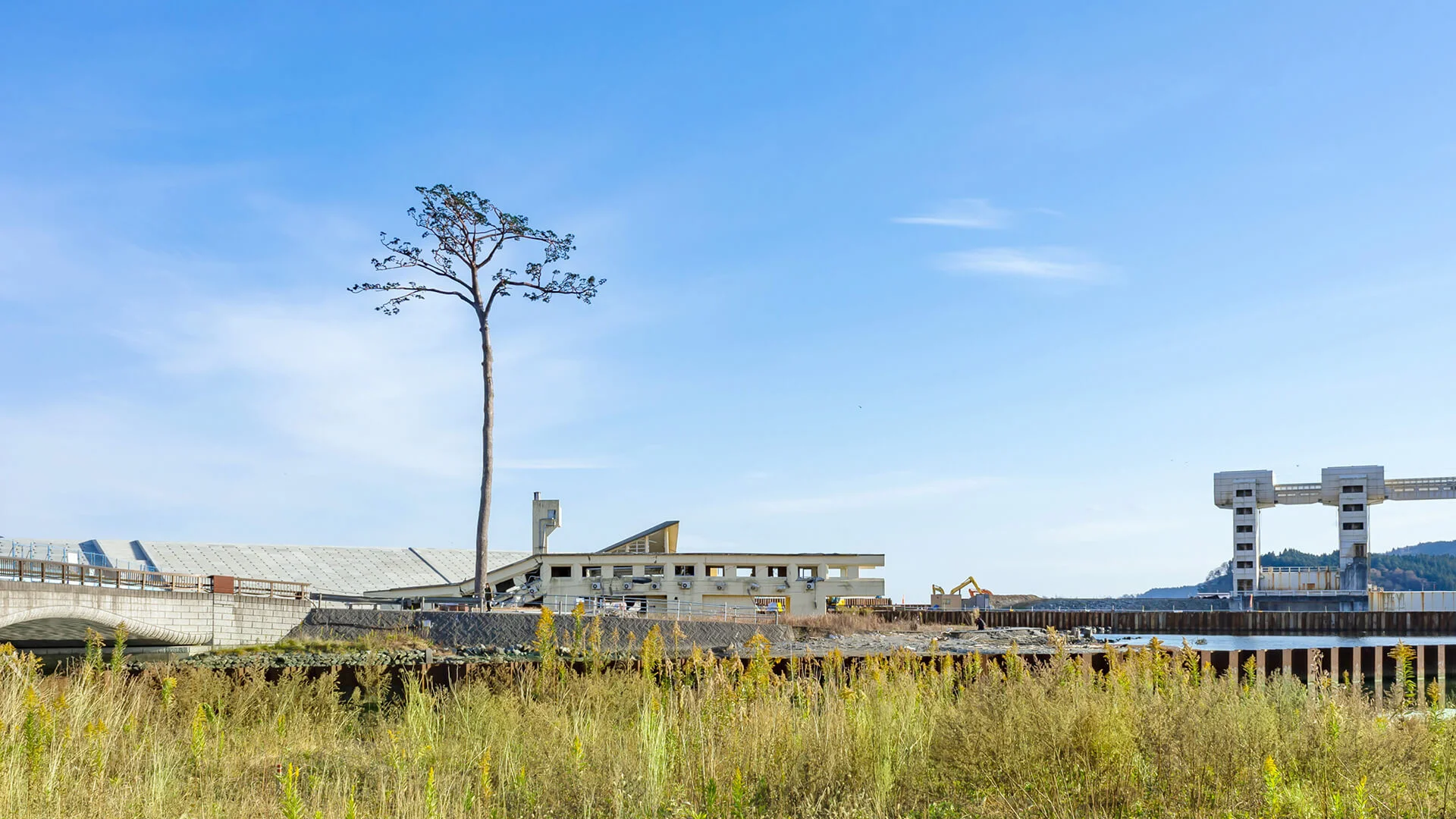
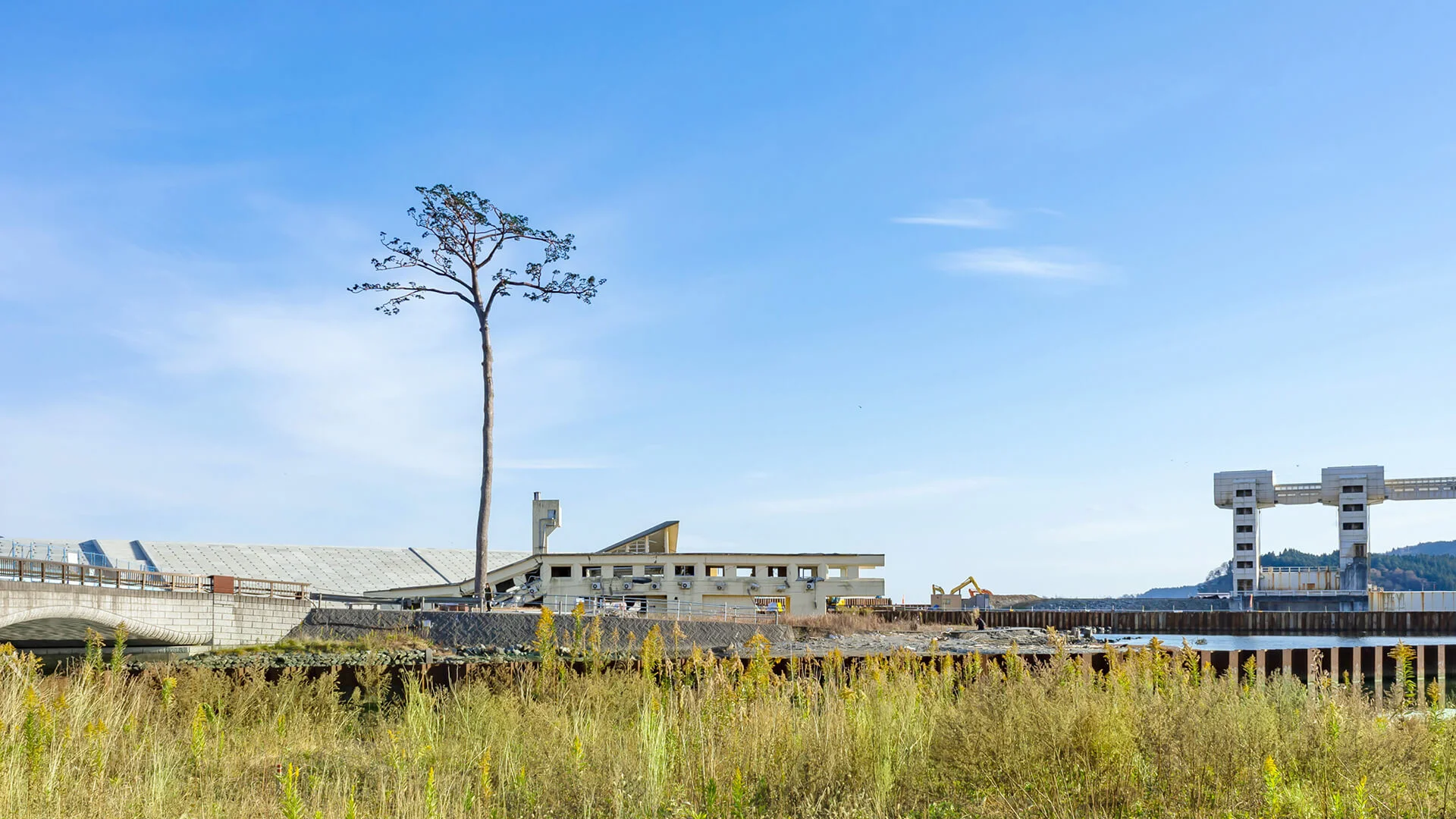
Apr 14, 2021
VISION & IDEAThinking about the future—because nobody knows what might happen next
Reexamining “resilience” in the decade since the earthquake and tsunami disaster
Everyone wants to lead a safe life in good health. However, a global pandemic of Covid-19 struck us in 2020 as if it shutters our little wish. We realized that disaster struck our daily life suddenly.
What should we do to prepare for the sudden disaster, and to respond to it?
Contents of this article
What is necessary for us when our daily life is shaken?
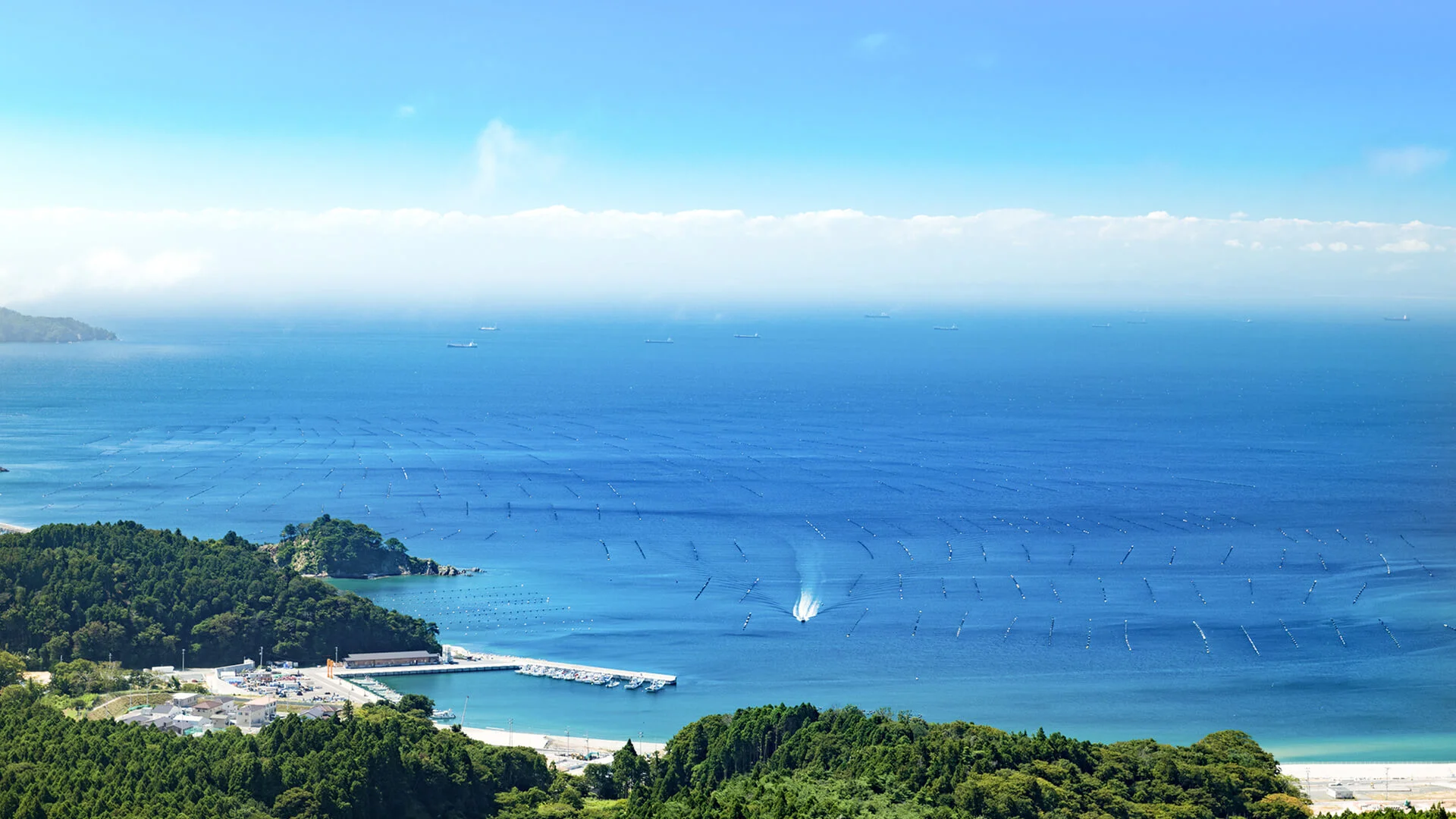
Imagine a typical morning in your local town, going about your daily routine. Then a major disaster strikes out of the blue, turning everything upside down and changing your life. It’s impossible to predict when such a massive calamity may occur—it could be tomorrow. When faces with a disaster and a unacceptable reality, many people are simply dazed and stand in shock.
It has been 10 years since the Great East Japan Earthquake, and the resulting massive tsunamis and more that caused immense damage. The scale of the disaster was unimaginable; in the blink of an eye countless people’s lives were changed forever. The disaster also reshaped the DENSO’s business environment in major ways, but there were actions to recover business even when the earthquake occurred.
We talked with some members at DENSO about their restoration efforts after the earthquakes and tsunamis.
We found some keywords for restoration in their stories from the time right after the earthquake to restoration and the relationship with Tohoku region, which leads to now.
Let’s start with the situation at corporate headquarters just after the disaster struck. The theme that emerges here is acceptance and understanding of what had just happened.
Mental preparation helps accept the situation and respond quickly after a disaster
2:46 p.m., March 11, 2011. A magnitude 9.0 earthquake struck in the Tohoku region, registering 7 on Japan’s shindo seismic intensity scale — the highest possible rating. It was the greatest earthquake ever recorded in Japan, an unprecedented natural disaster no one had ever experienced.
Isao Saito and Kazunori Fukuroi, currently working in the General Admin. Div., told us about their immediate response at DENSO. Both of them became involved in the frontline efforts, setting up the Disaster Response Headquarters.
One hour after the quake, they held a disaster response meeting at the Company headquarters and began trying to contact the roughly 60,000 DENSO employees working throughout Japan to confirm their safety. The next day, the Company began sending relief supplies to disaster-struck areas. Commenting on these initial efforts, both Fukuroi and Saito said that their experience of past disasters had taught them the importance of first accepting what had happened on an emotional and mental level, no matter how bad the disaster, as this helps one to take action more quickly.
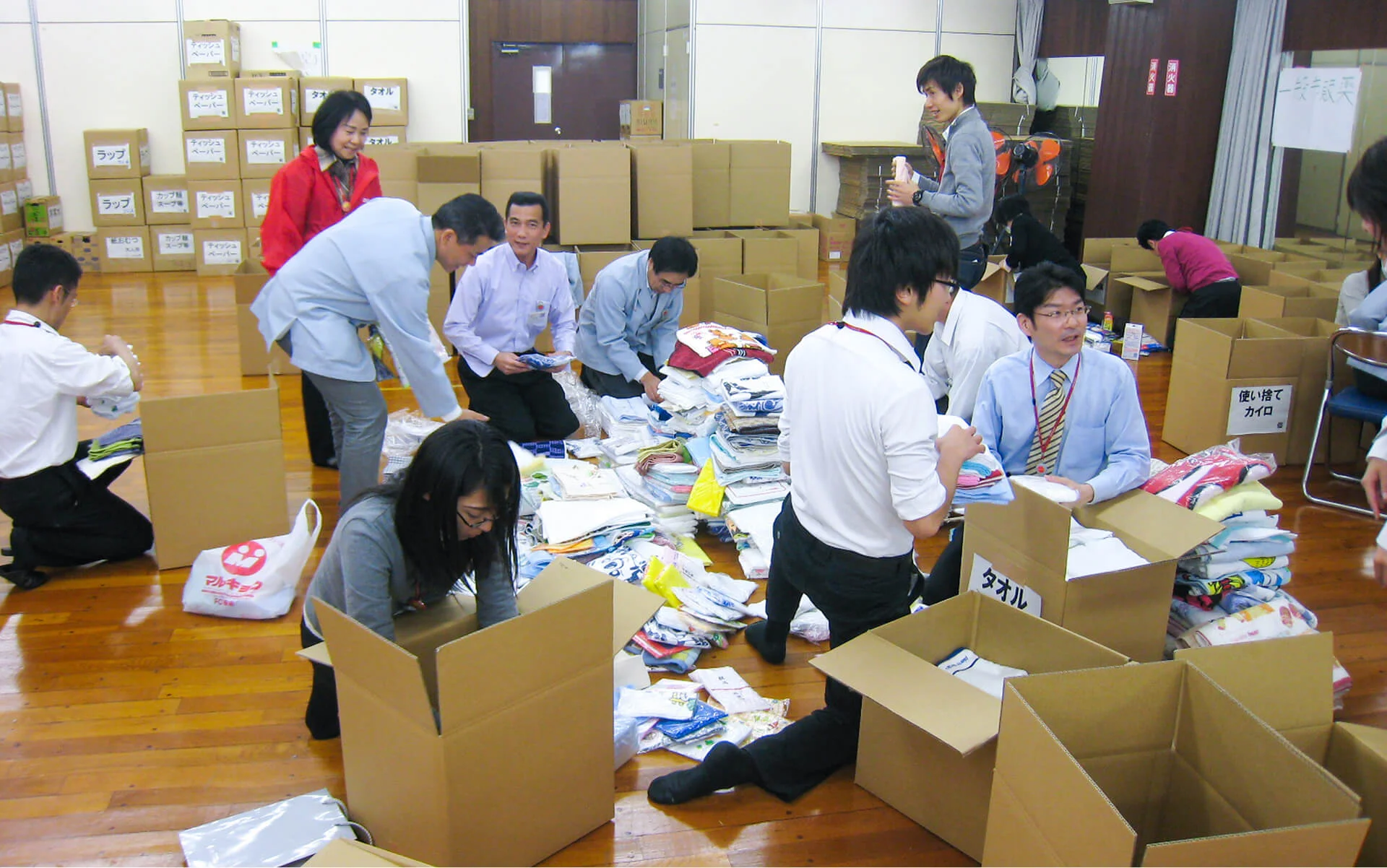
“No matter how large or small, there’s no way to prevent natural disasters,” explained Fukuroi. “A number of disasters have hit Japan over the years, and because DENSO has plants and offices throughout the nation, it has experienced many of them directly. Also, some people have been expecting a major disaster to hit the Tokai region in the near future. Based on past experience, I understand that disasters will occur at any time, and this way of thinking allowed me to take quick action in the event.”
“When the earthquake hit, the first reaction of many of us was, ‘Oh no! Something awful has happened!” said Saito. “However, even if you feel scared and uneasy, and even if you start to panic, the things you have to do in response remain unchanged. If an earthquake measuring upper 5 or higher on the shindo scale occurs, DENSO sets up a Disaster Response Headquarters and begins checking on employees’ safety as well as conditions of DENSO, group companies, customers and suppliers, and so forth. Because we had created the disaster response manuals, we were able to act calmly even though people were distraught in chaos.”
Fully preparing for a disaster, setting up a response framework in advance, and striving to adapt and accept the situation … these are the first steps to recovery from disasters. The next members we talked with showed us the importance of personal connections.
Connections between people are what make business possible
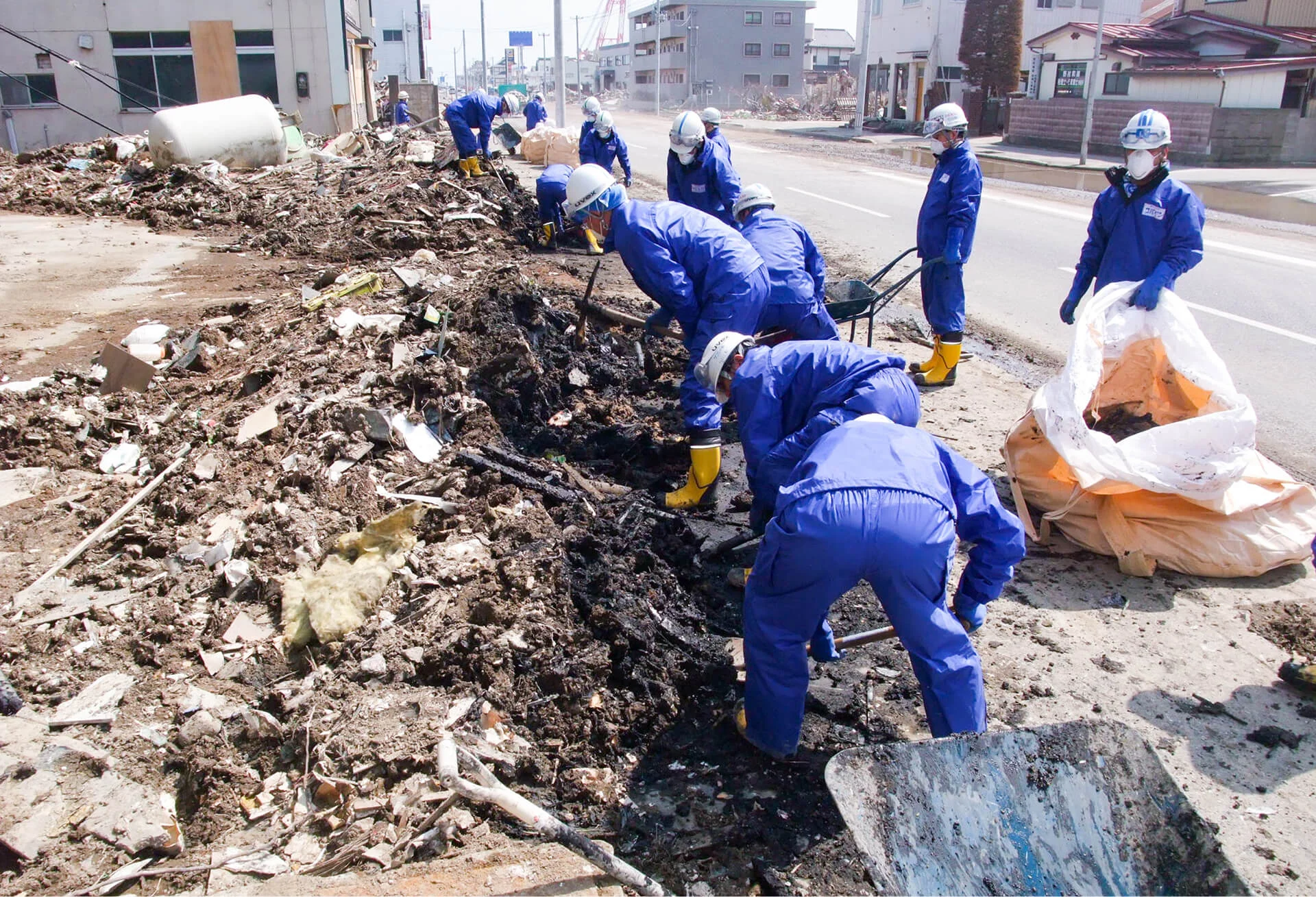
On March 12, the day after the initial earthquake, a hydrogen explosion occurred at reactor 1 at the Fukushima Daiichi Nuclear Power Station. That afternoon, DENSO’s Disaster Response Headquarters received a phone call asking if they could accept evacuees at the Company’s facilities.
The call came from mayor of Tamura City, Fukushima Prefecture, where DENSO had recently built a new plant (now owned by DENSO Fukushima), and the Company immediately agreed. Construction of the plant had just been completed the day before the quake, and the decision to open its grounds for use by local evacuees was made very quickly.
Takahiro Banno, now in the General Admin. Div. like Saito and Fukuroi, took it upon himself to receive the evacuees. “I had a lot of work-related connections with people in Tohoku. They were all really attractive people, and since they were in trouble I wanted to help out in some way,” he explained.
“Snow was still falling in Tohoku and it was too cold inside the plant for people to spend the night comfortably, so we spread styrofoam plates and cardboard to keep everyone warm there. It was difficult to say the evacuation shelter was comfortable for the evacuees, but we improved the temporary living environment together with the local government staff.”
“About 2,000 evacuees came to the plant in total. We introduced evacuees from the nursing home to the canteen because it was relatively warmer than others. We took quick decisions with on-site staff such as the ones above” said Banno.
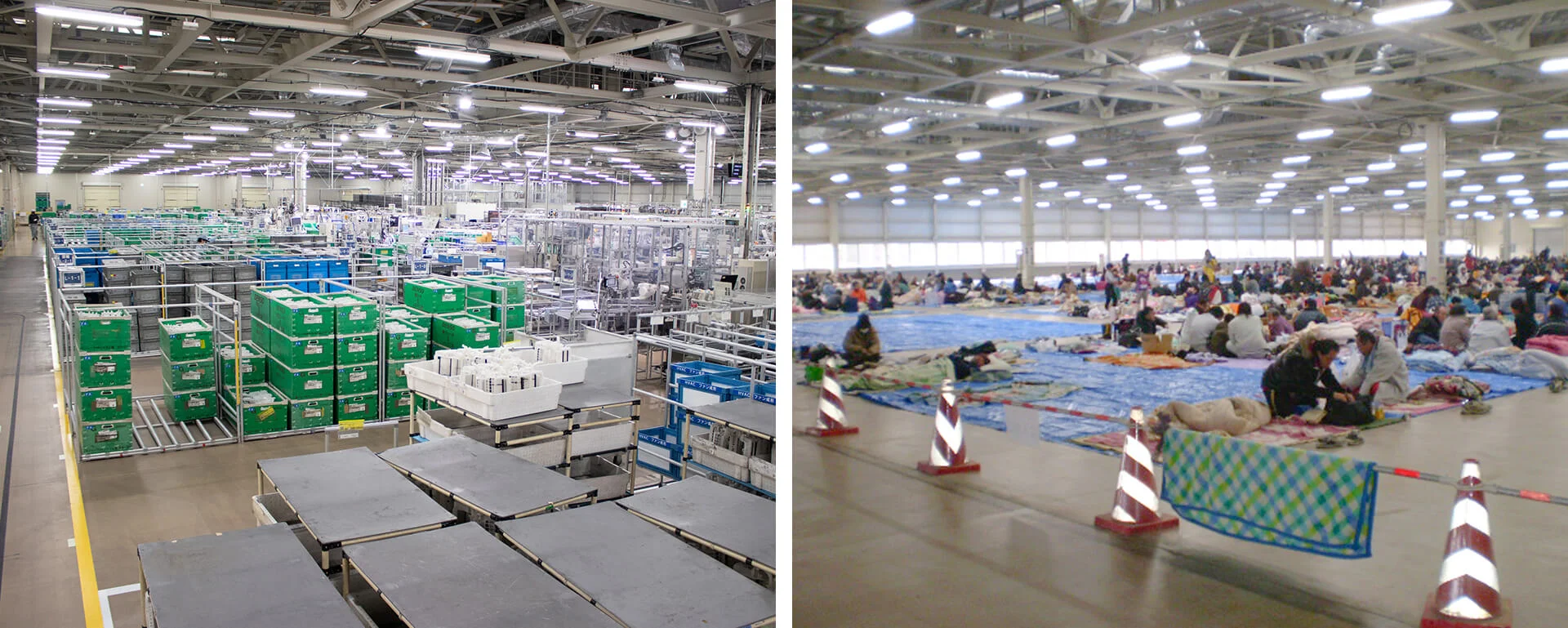
Large numbers of DENSO employees had the same desire as Banno to help the people of Tohoku in some way. To respond to this shared desire, DENSO sent more than 700 employees to disaster-stricken regions in official company capacity right after the quake. They served as volunteers, working in coordination with government organizations and NPOs to deliver relief supplies, and to remove rubble.
Atsushi Kusaka, now in the Machinery & Tools Mfg. Div., was one of such volunteers. He was dispatched to the Oshika Peninsula in Miyagi Prefecture. “When I was looking for some way to volunteer there, I was very surprised to see the recruitment of volunteers within the company” said Kusaka. “DENSO’s decision to send volunteers to disaster-hit areas as company capacity was evidence of their dedication to helping the recovery.”
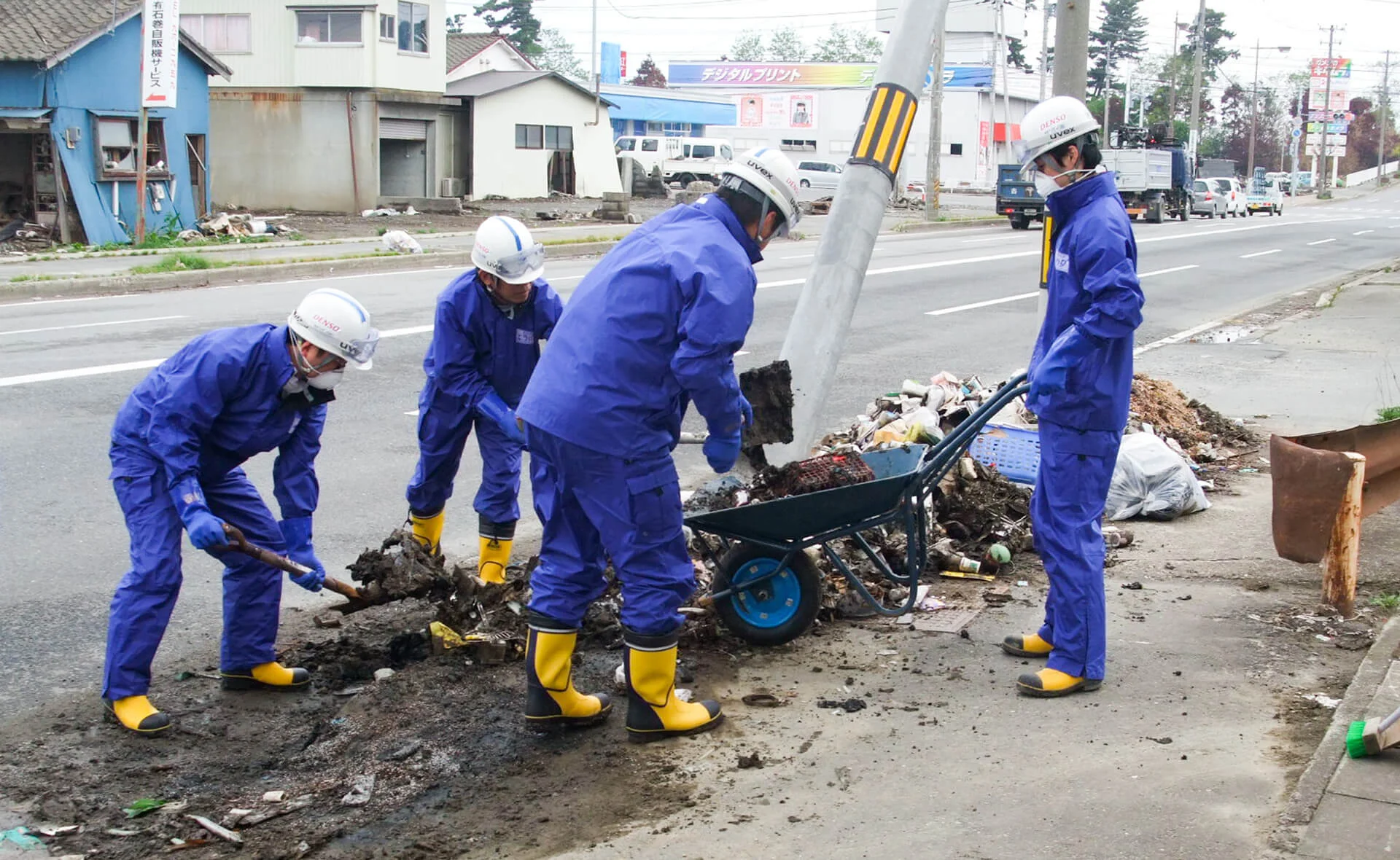
“I’m still in touch with some of the people in Tohoku I met through that volunteer work. I visit local fishermen and help them gather wakame kelp, catch sea squirts and do other work every March. I really enjoy my time with them and look forward to going there every year.”
After opening up the new plant to the public as an evacuation shelter, DENSO sent employees to Tohoku as volunteers. This was not just to help the recovery in the affected areas; DENSO fully understands that it cannot keep our productions running without the support of the locals because it has many plants throughout Japan. DENSO firmly believes that it has a duty to provide help when those locals need help after a disaster, and it’s more important than anything else.
The stories from DENSO employees make it clear that we cannot recovery from disasters without personal connections.
Once you decide to do something, give it your best
In April 2011, evacuees in the newly constructed plant began relocating to temporary housing facilities, and plans for commencing production were at last put into motion. However, it was at this time that DENSO received a call for help from one of its old production partners in the region. Their plant was in the designated danger zone of the damaged nuclear power plant, and they were not allowed even to send people into their own facilities. They needed DENSO’s help, and so DENSO decided to rent a part of the new pant to them for production. However, it required new additional construction to renovate the newly constructed plant, because the partner’s products are fully different from those of the plant.
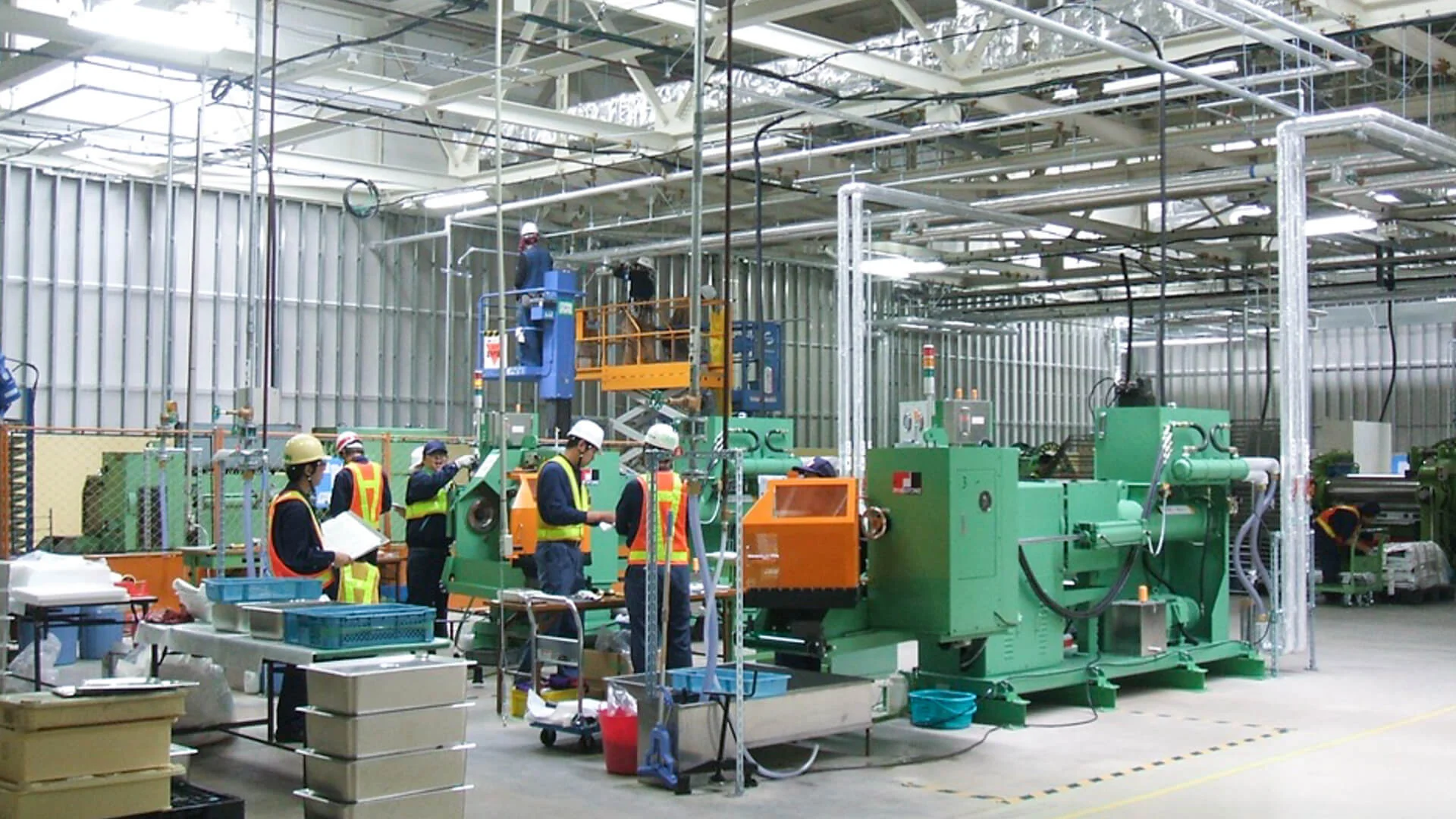
Masato Funahashi, who was in the Facilities Div. at that time, was in charge of this project. “The renovation was something we needed to do, regardless of the cost and effort involved,” said Funahashi. “It didn’t matter whom the construction was for. We had to cooperate with them. Even if DENSO produces its products smoothly, automobiles cannot be produced if any one of our partners products are lacking. That’s why it was inevitable for us to cooperate with them.”
Thinking back on the decision, Funahashi still feels that it was right for DENSO to rent a part of the plant, even if it affected DENSO’s operations. “This may be a little off topic of the Great East Japan Earthquake, but the situation reminds me of a time when I was in charge of construction for an overseas plant. For that project, two of DENSO’s top priorities during preliminary onsite investigations were ensuring that local workers would earn enough to make a decent living, and that we would be able to effectively work in cooperation with local residents. This really showed me that DENSO cares about all members of society as a whole. When the earthquake hit Tohoku, I think all of our staff shared the same spirit of helping society and felt personally motivated to take action.”
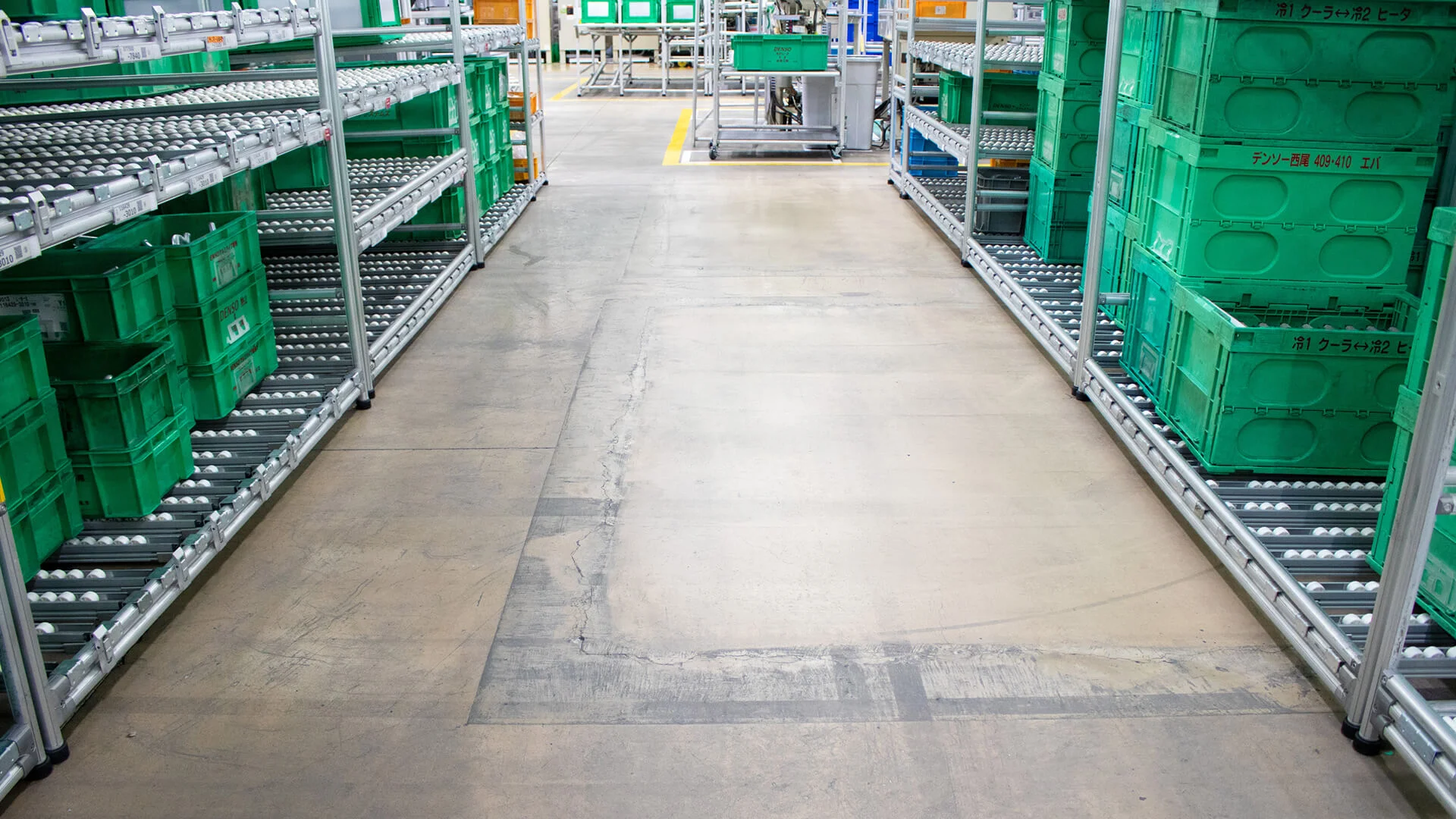
Even today, remnants of the renovation construction project can still be seen in the floors at DENSO Fukushima’s plant. In fact, these were intentionally left visible so that people would never forget what had happened there.
Neither the decision to rent plant facilities, nor the decision to send countless DENSO volunteers to Tohoku, were unusual actions for DENSO. The Company always makes utmost effort to help those in need. This corporate culture is why it was able to respond to recovery as a unified organization in the post-quake recovery efforts.
Once you decide to do something, make sure to give it your best—this is vital for overcoming unforeseen challenges in life.
Acceptance—the first step to overcoming adversity
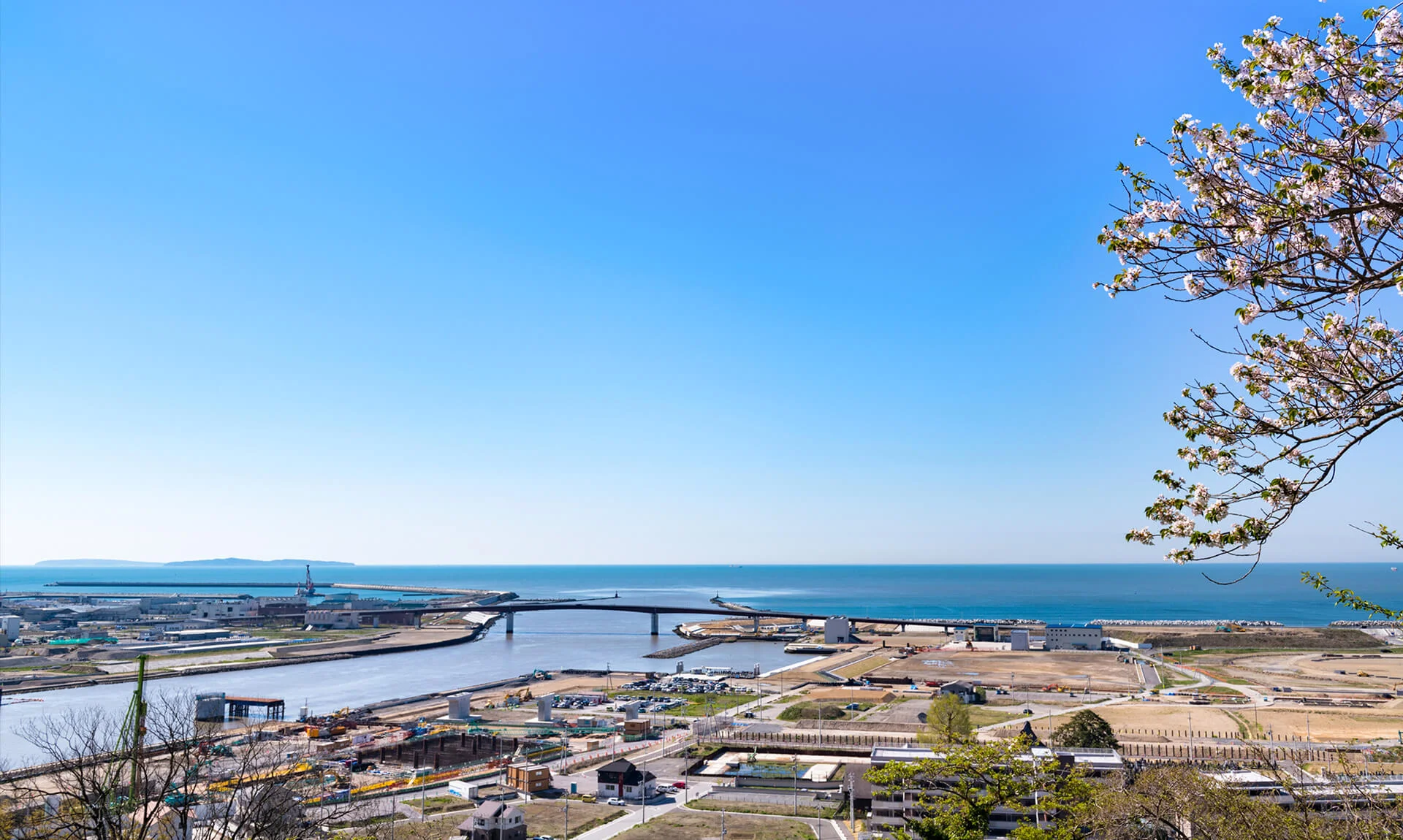
I feel that a clue to being strong in unexpected and challenging situation is hidden in common traits, when I take a look back to the people’s responses to the Great East Japan Earthquake. And that is the flexibility to adapt and accept situations that are inherently hard to accept, and then take action to recover quickly. This idea has come to be expressed by the term of “resilience,” which means the ability to effectively bounce back, rebuild and recover.
Unforeseen global calamities will occur again, and will come out of nowhere. Therefore, we must remain alert and make preparations in advance. However, some things cannot be predicted because they exceed the scope of what we think possible, which is why it’s so important for each and every one of us to be courageous, think of people first, remain adaptable and flexible, and take bold action—no matter what happens.
Whether thinking about the people around us, our society, or the planet as a whole, it’s possible to build a sustainable society through the cycle of sharing both the good and the bad, both joy and grief. This sharing process reminds us that the power to give to others, and the power to accept things, are equally important.
COMMENT
Changing your "Cant's" into "Cans"
Where Knowledge and People Gather.