Did you find this article helpful for what you want to achieve, learn, or to expand your possibilities? Share your feelings with our editorial team.
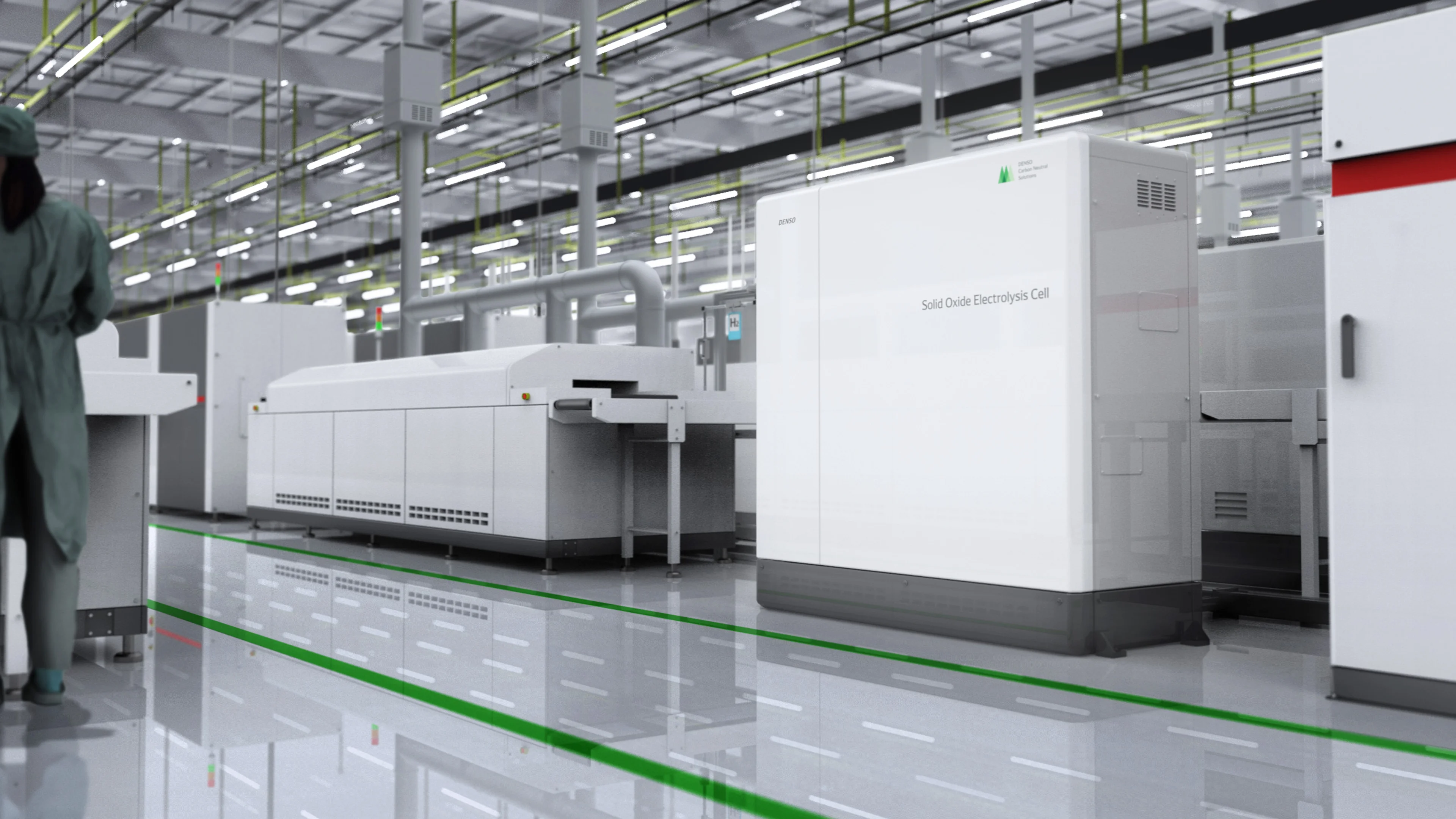
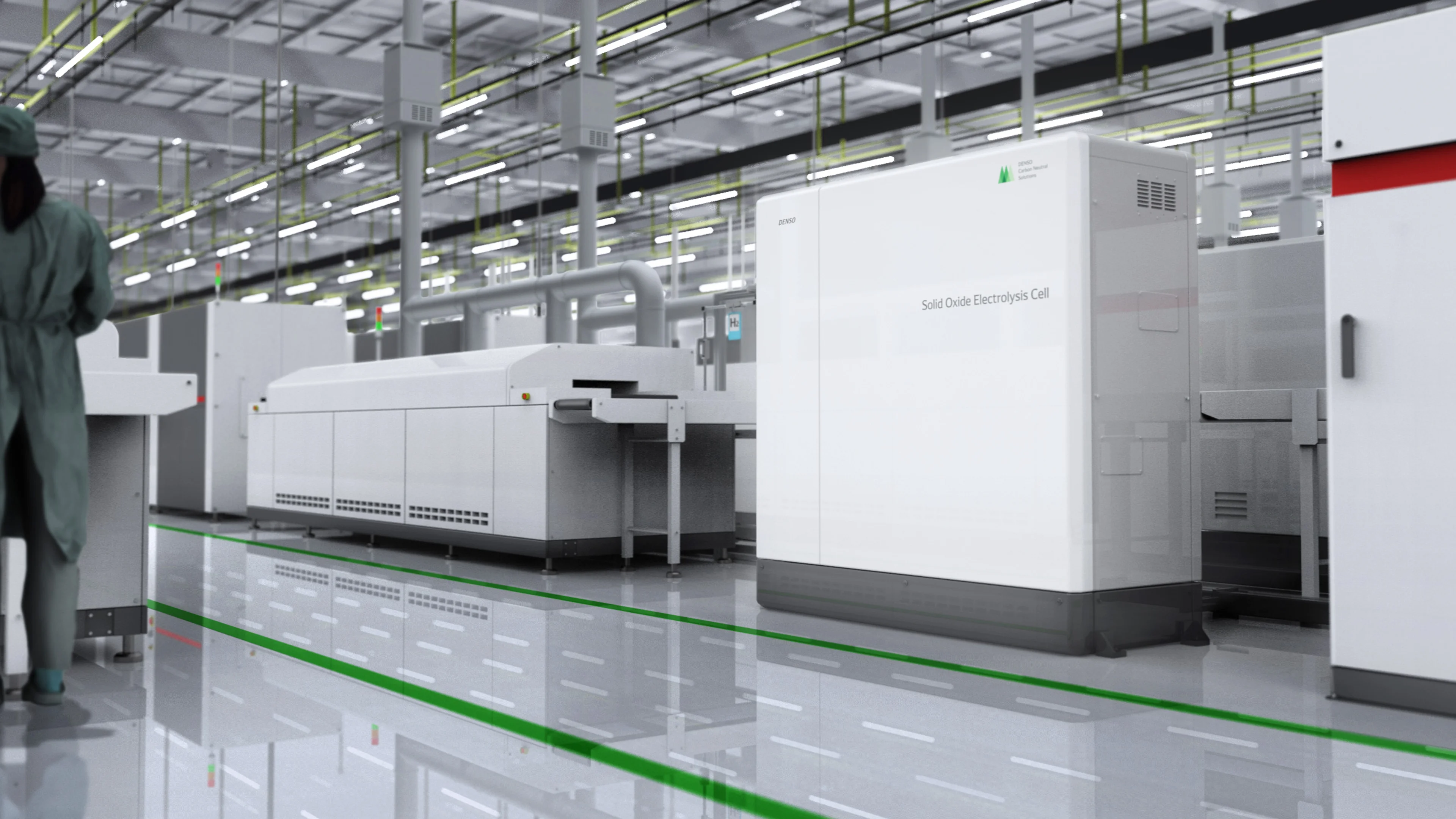
Mar 7, 2023
TECH & DESIGNDENSO is challenging itself to develop a solid oxide electrolysis cell system looking ahead to a future of hydrogen society
Leveraging automotive technologies to generate hydrogen using renewable energy sources
Hydrogen is gathering attention as a carbon-free energy carrier, and is a key solution to reduce greenhouse gas emissions. The hydrogen is currently produced from fossil fuels. To achieve widespread carbon neutrality, green hydrogen – the hydrogen generated from renewable energy through electrolysis of water – is strongly required.
That’s why DENSO is developing a solid oxide electrolysis cell (SOEC) system, which is a next-generation water electrolysis system with significantly high efficiency.
Contents of this article
SOECs: the most efficient water electrolysis possible
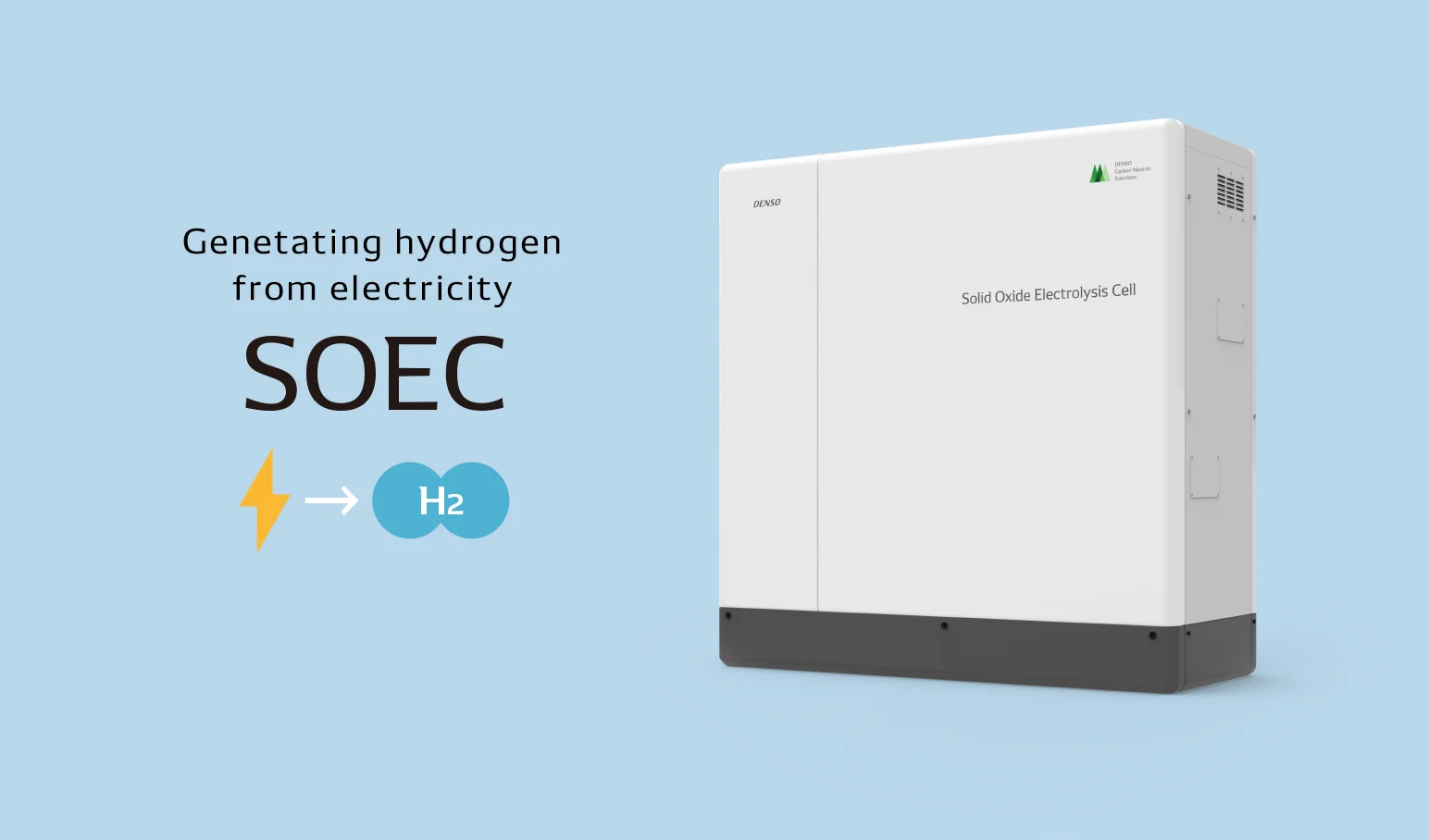
There are several kinds of water electrolysis to generate hydrogen from water, such as alkaline water electrolysis and PEM (Polymer Electrolyte Membranes) water electrolysis.
Water is electrolyzed at a lower voltage as the temperature increases. The operation temperature of SOEC is around 700°C, which is much higher than that of Alkaline or PEM (around 60°C), enable to produce hydrogen with less electricity.
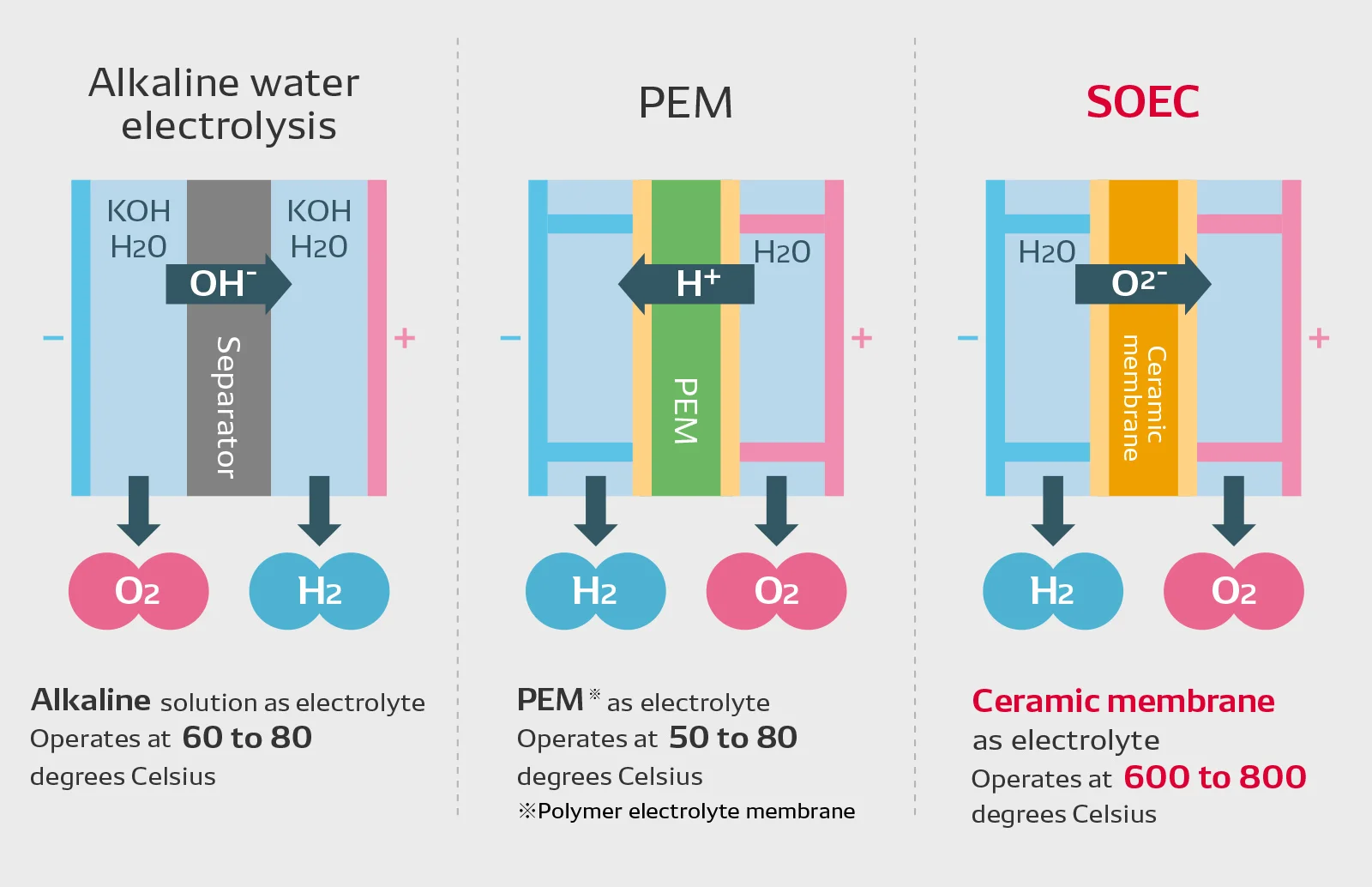
Because polymer electrolyte membrane or alkaline solution cannot withstand high temperatures of around 700°C SOEC cells are made of ceramic material. The cell consists of three layers: fuel electrode, an electrolyte membrane and an air electrode, and cells are stacked to make “cell stack”.
A cell stack is put in “hot module”. The role of hot module is to keep the cell stack at operating temperature with thermal insulation and heat exchanger of inlet steam / outlet hydrogen. This is the basic operating mechanism of an SOEC system.
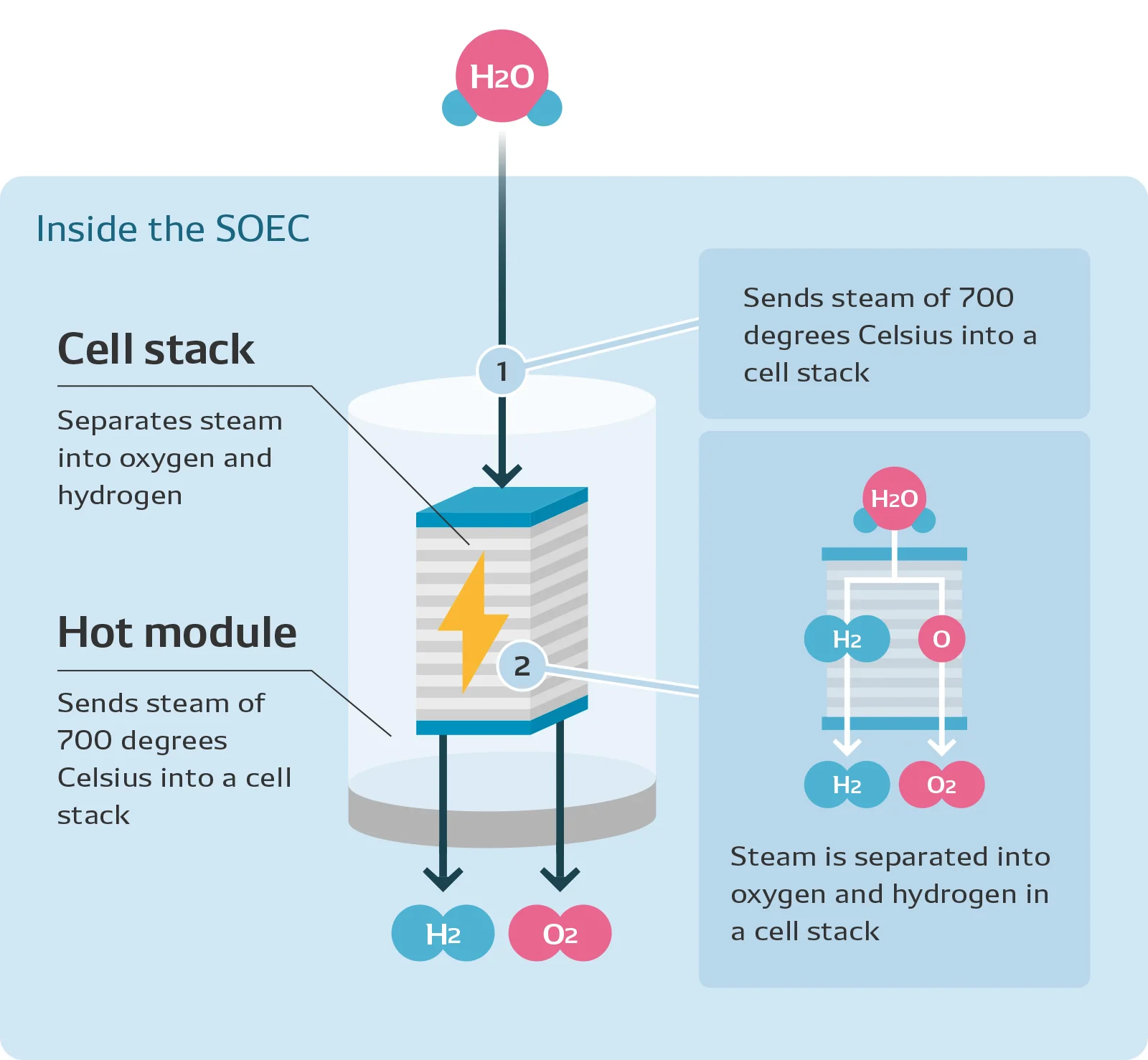
SOEC products are highly expected as next-generation water electrolysis systems, because it generates hydrogen with more efficiency in principle than low-temperature water electrolysisand it is even higher efficiency when waste heat is provided to SOEC system, A lot of technological breakthrough is required to commercialize SOEC system; this is the reason why SOEC has not been widely used yet . DENSO is looking to make use of its technologies built up over the years in order to solve these technical challenges.
Heat management and systemization technologies to overcome SOEC technical challenges
One challenge is realizing a high efficiency; producing green hydrogen using less energy.
Atsushi Nakajima from the Environment Neutral Systems Development Div. explains their approach.
“We consider the higher efficiency to be one of the most important factors in realizing a hydrogen society. The cost of green hydrogen can be reduced by increasing production efficiency, and it will boost demand for hydrogen and bring us one step closer to a carbon-neutral society.
Compared with current mainstream electrolysis methods, SOEC systems offer higher efficiency. However, there are some factors to increase power consumption of SOEC, and it prevents the system from realizing its true potential. By using technologies cultivated through automotive product development, we are searching for ways to minimize the power consumption of SOECs, which will bolster the overall efficiency of producing green hydrogen.”
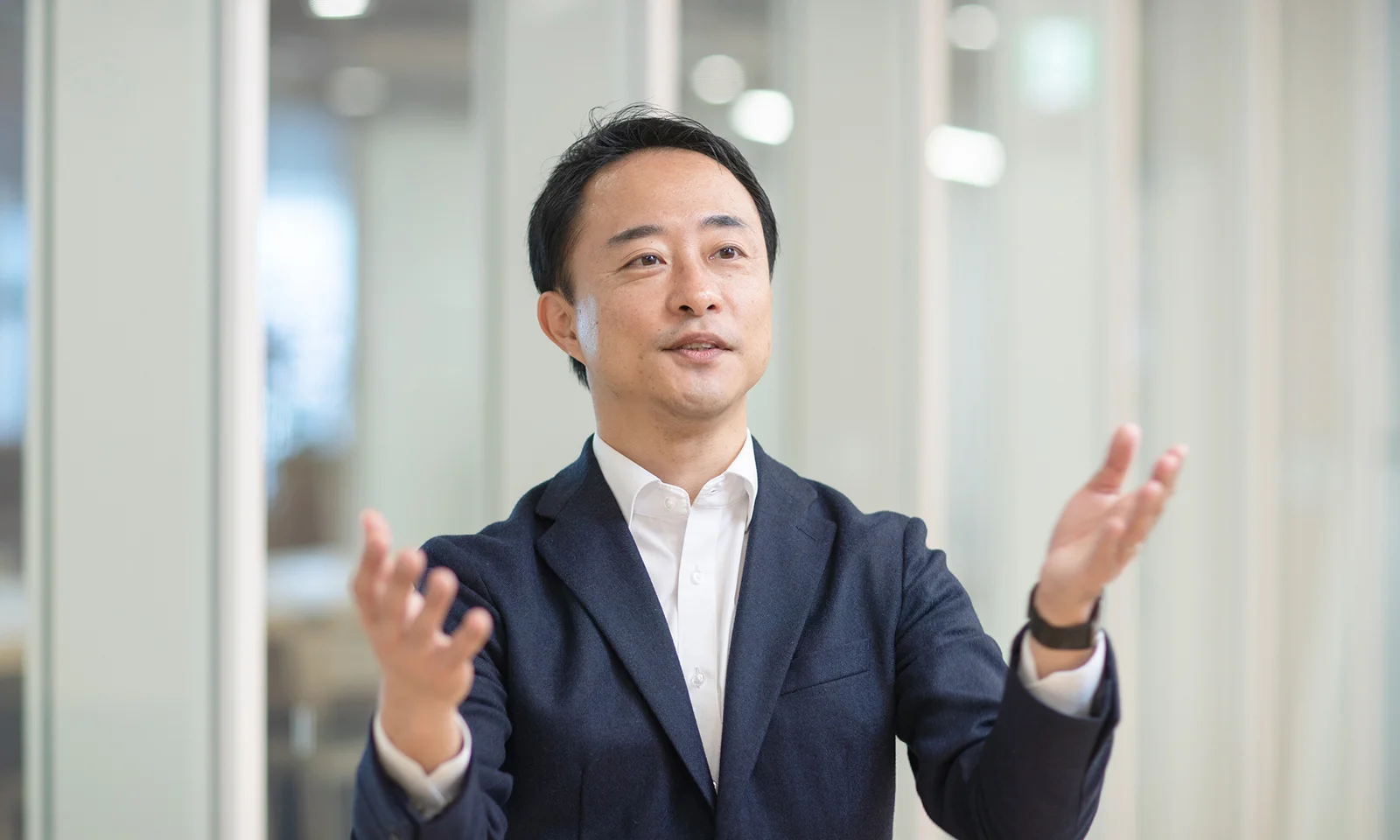
One of the main challenges in developing SOEC products is managing heat properly. At the conventional hot module, when we try to keep the temperature of 700°C within the hot module, heat is often dissipated from the module into the surrounding area To compensate for the heat dissipation, additional energy must be provided, resulting in lowering system efficiency. In addition, not all the steam supplied to the module is used to generate hydrogen, and the unreacted steam is released. It means that the heat energy to generate the released steam is wasted, which lowers the overall process efficiency.
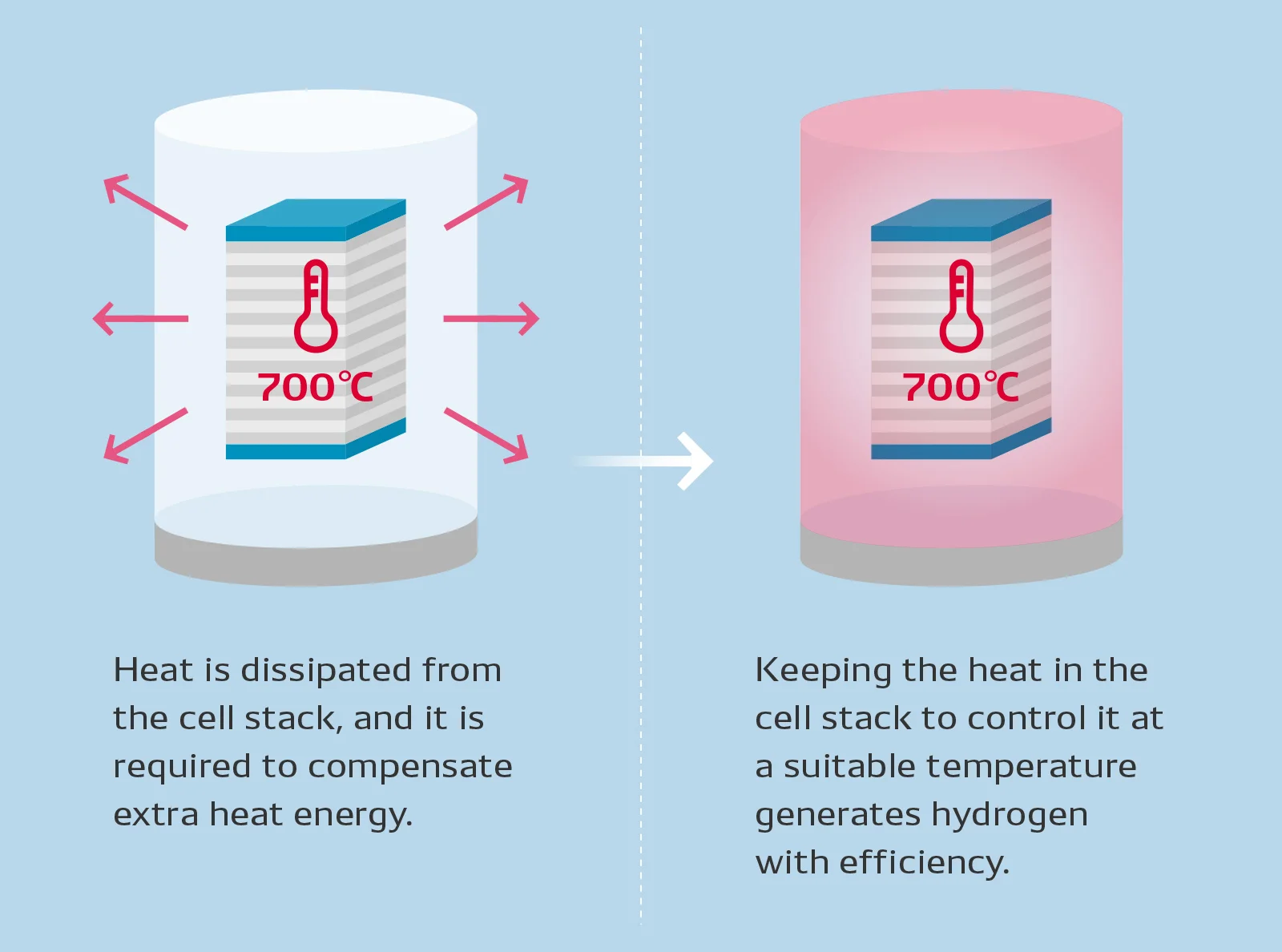
In order to solve these problems, DENSO is working on the technology development utilizing years of technological development in the automotive field.
Hot module has a heat exchange unit to reduce the heat loss from the hot module.
Based on its automotive heat exchange technologies, we reduce the heat dissipated from heat exchanger surfaces while simultaneously collecting waste heat efficiently. Haruhiko Watanabe, who is involved in hot module development in the Environment Neutral Systems Development Div., explains the technical challenges of SOEC systems.
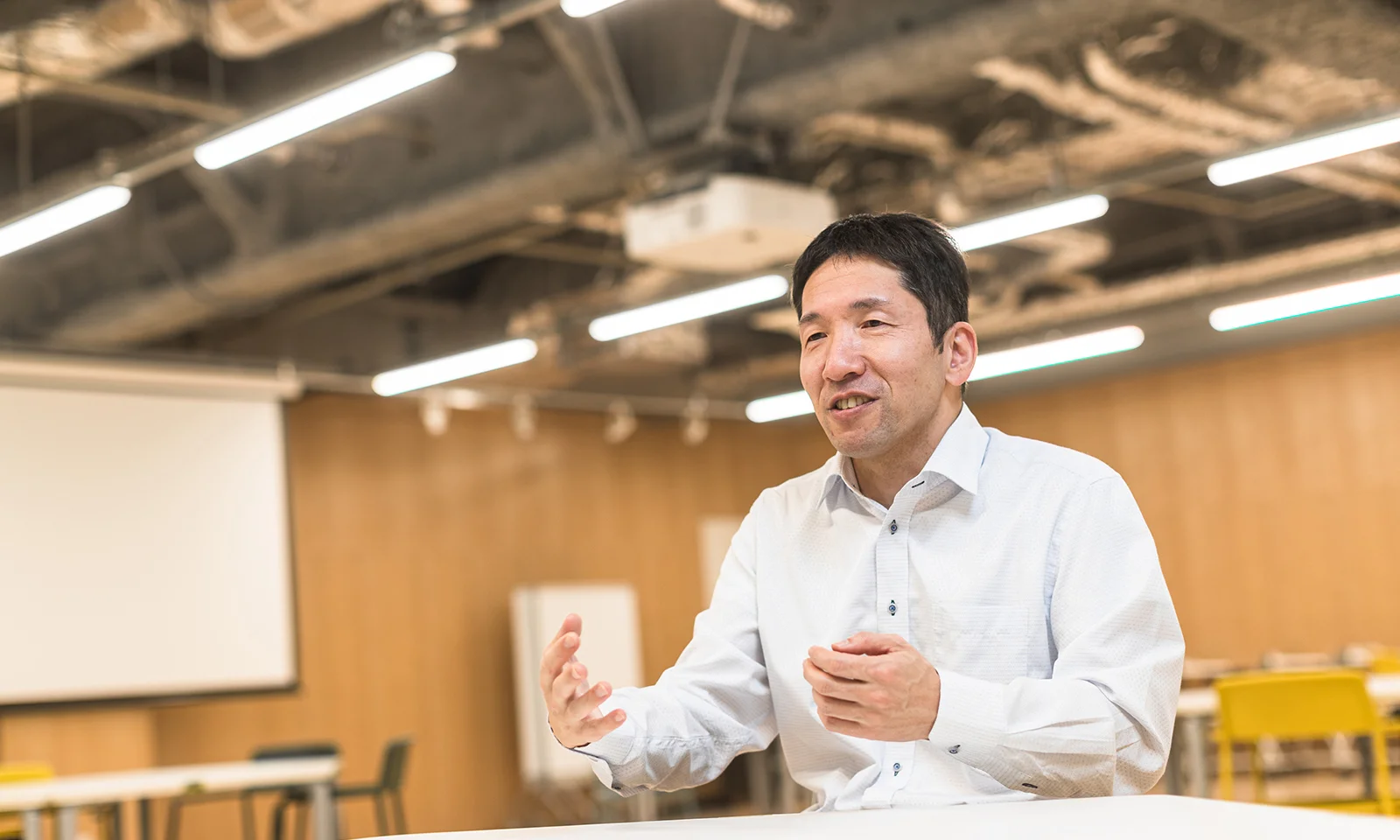
“Failure to maintain the proper temperature within the cell stack results in lowering the efficiency of the electrolytic process, which in turn reduces hydrogen production. In addition, the variation of the heat transmission in the hot module have an adverse effect on performance of cell stack, and the process efficiency is reduced as a result.
Both high-efficiency heat exchange and temperature distribution control must be achieved in the hot module. However, because heat naturally moves from hotter to colder areas, temperature gradient is generated when heat is recovered for reuse. It is very challenging to successfully solve both problems in a balanced manner, so we are working on the development in order to overcome them utilizing our heat-flow technologies, heat-flow simulations technologies and so forth developed through automobile components development.”
DENSO is also integrating an ejector into the SOEC system to recirculate unreacted steam and feed it back into the cell stack. An ejector utilizes the energy of high-pressure fluid flows, without relying on mechanical driving force of pumps and so forth, in order to suction and discharge low-pressure fluids.

“DENSO’s ejectors in SOEC systems enable to recirculate unreacted steam with lower energy consumption, , which boosts the efficiency of electrolysis. Attempting to recycle steam using existing pumps would require greater driving force. Moreover, no pump could withstand the high temperatures and long operating at present, and thus frequent pump replacement would be necessary to operate the system properly, which would drive up maintenance costs. DENSO’s ejectors, in contrast, are hard to break, because they are high-temperature resistant and consists of small number of parts. As a result, it extends the service lives of SOEC-system core components and reduces maintenance costs.
Moreover, collecting and recirculating large amounts of steam does not maximize the efficiency of the cell stack, and it is necessary to understand the most suitable “steam recirculation efficiency”. It is not possible to design the suitable efficiency without a detailed understanding of cell stack technology. Because DENSO is developing not only hot modules but also cell stacks in-house, we are able to attain maximum efficiency in the final SOEC products.”
Watanabe explains that the one of the strengths is that DENSO develops core components such as hot modules and cell stacks by ourselves and design them optimally and systematically as one product.
“In most cases, hot modules and cell stacks are developed separately or outsourced, but DENSO develops them in-house as one system.”

“In this approach we are able to integrate redundant functions and eliminate wasteful elements to downsize cabinets. And as reducing overall surface area prevents more heat from dissipating, we are able to eliminate energy waste and reduce power consumption.
It is the advantage of DENSO’s systematization technologies to understand the characteristics of each component and technology and to optimally design them as one product. This advantage enables us to achieve breakthroughs in SOEC product performance.”
Manufacturing technologies and cutting-edge technologies of DENSO to improve SOECs
DENSO has the advantage of cutting-edge technologies to develop the cells of SOEC systems. When ions move from the fuel electrode to the oxygen electrode in the reactions in the cell, there is electric power loss according to the distance that is the same principle as that of electrical resistance.
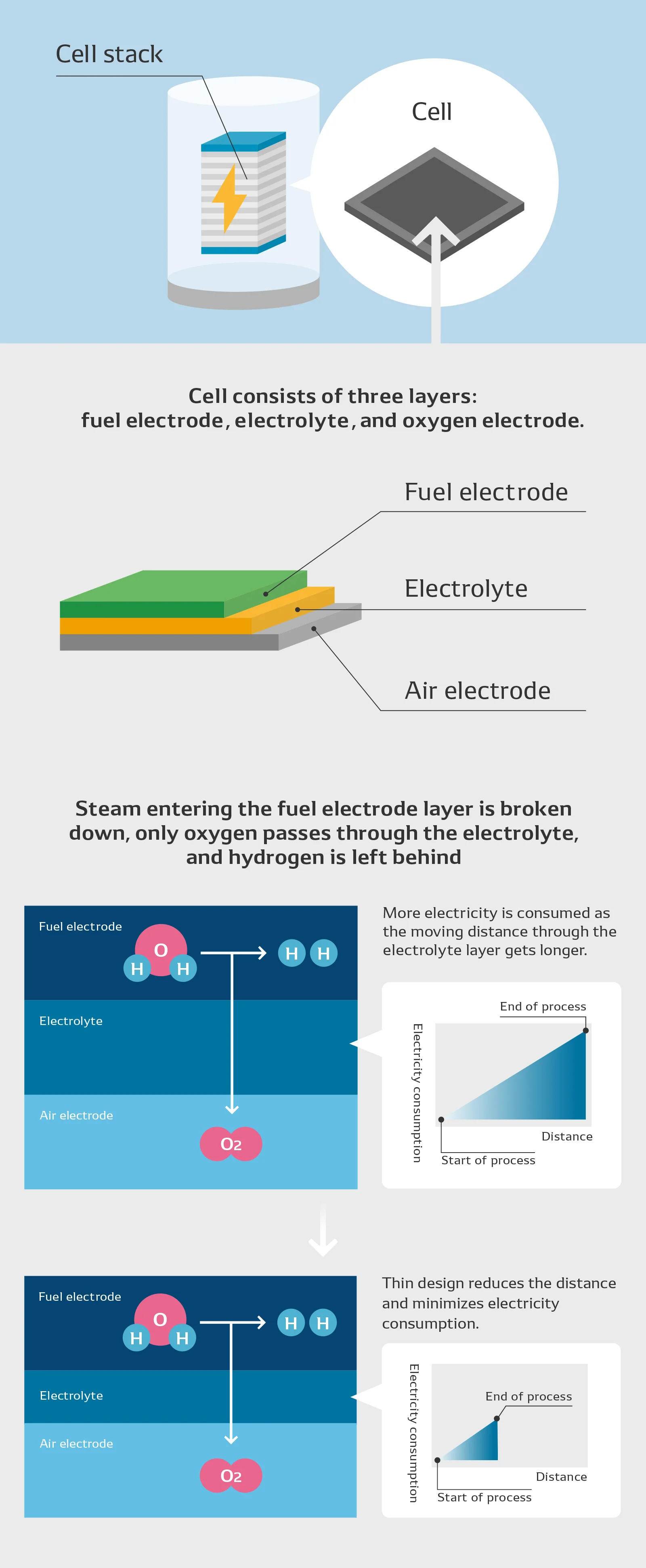
In order to reduce the electric power loss by the movement of ion, thickness of ceramic body must be decreasing with maintaining ceramic densifications. DENSO already possesses the necessary core technologies, originally developed for its exhaust sensors which similarly use ceramic layering. This enables the power loss in SOECs to be successfully reduced while also eliminating defects. Takuma Hitomi of the Environment Neutral Systems Development Div. cell developer explains although the goal of making layers “as thin as possible” may sound simple, just how difficult this is:
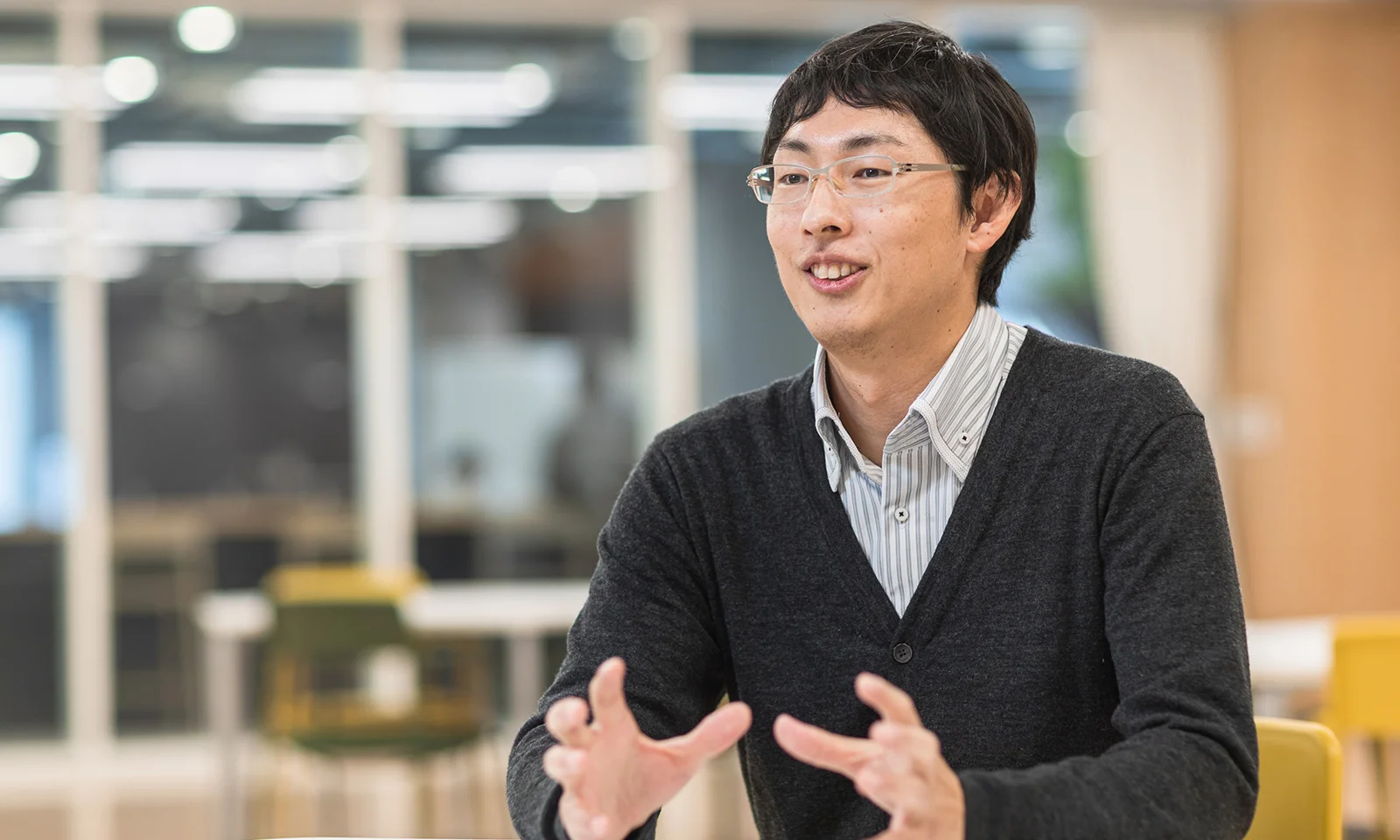
“Thinner cell reduces power loss, but the problem is that it causes to generate pinholes are easily developed. Even a small pinholes can result in damage to the other side of electrode layer.
Ceramic material layering is generally dense, but when the component is reduced to such an extreme thinness, it becomes so fragile that you can’t even hold it in your hand without breaking it. Therefore, the cells are sintered after stacking multiple layer. However, during the sintering process, high resistance intermediate layer is produced between different layer by element interdiffusion.
Therefore, we are striving to overcome the seemingly simple, yet deceptively difficult challenge of achieving thin and dense layers in various trade-offs while analyzing changes in the ceramic firing process.”
These tough development challenges can be overcome thanks to DENSO’s leading-edge technologies. The SOEC team utilizes a beamline dedicated to DENSO at the Aichi Synchrotron Radiation Center to analyze changes at the elemental level in the ceramic production process.
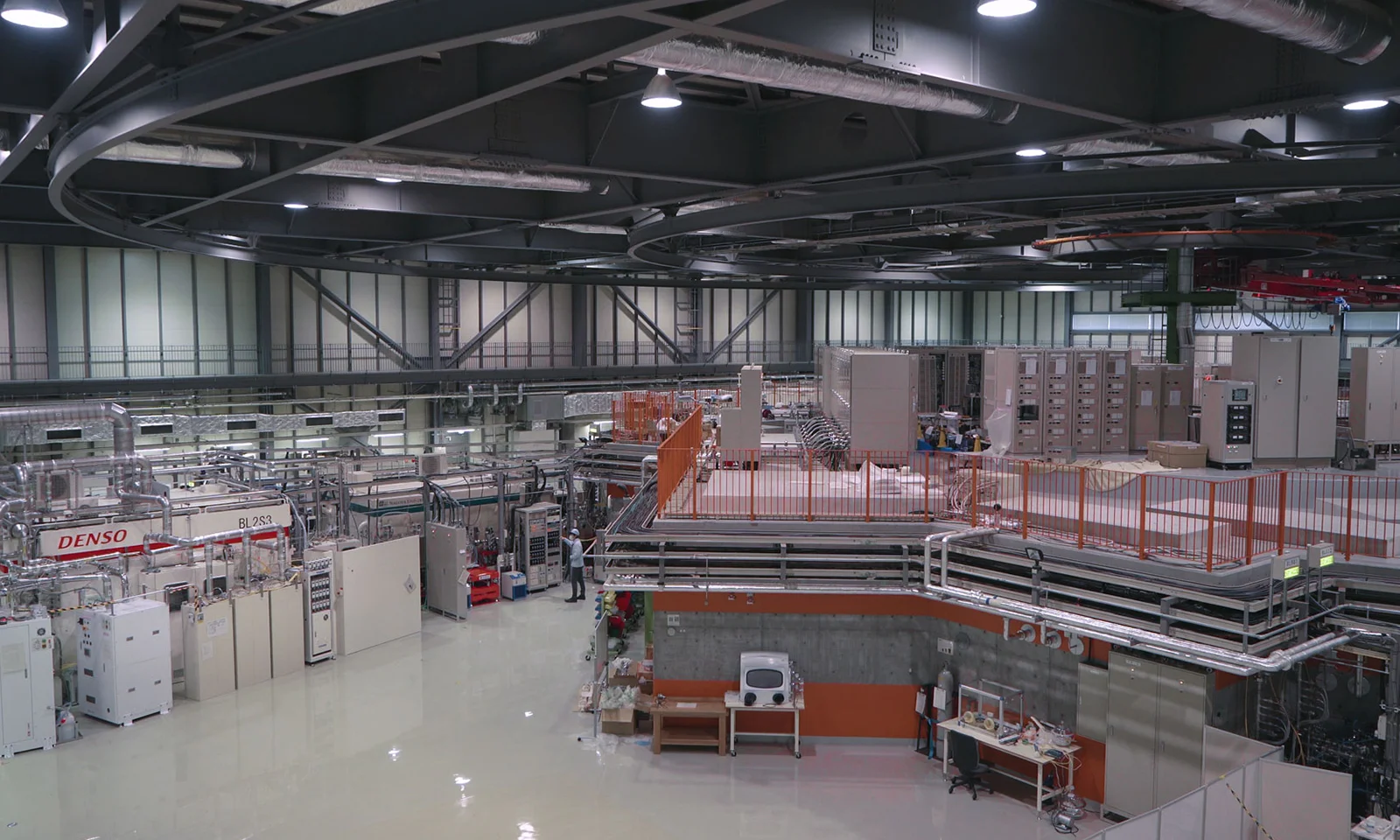
Furthermore, because DENSO handles all steps of the manufacturing process, from ceramic material procurement and sintering through to final component assembly, it is able to achieve cell stack performance only with its sophisticated manufacturing and other cutting-edge technologies.
Hitomi explains how these strengths are being used to develop even better cell stacks:
“The reason why SOEC operates at the temperature of 700 oC is that the performance of the ion conductor drops down at the temperature of 700 oC or less. This is a common characteristic of ceramic materials used throughout the industry. 700 °C is standard for existing materials in general, but DENSO is aiming further with new materials.
As changing ceramic materials also changes the conditions of even one process of sintering, it is very difficult to “change the materials” in general.
But no matter what material is used, the underlying principles remain the same. As DENSO has some technologies to visualize and analyze the invisible things, such as beamline technologies, we have our strength that we can establish guidelines to some extent even when materials are changed.
We have a culture of strongly supporting new R&D endeavors, as long as they are based on solid rules and principles. This allows us to take on the challenge of material changes that may not be permitted at other companies.”
Further advancements in SOEC systems for a carbon-neutral future
Such leading-edge developments cannot be accomplished by DENSO alone, that is why DENSO collaborates with university researchers to develop materials. Advance in material technologies makes it come into view to develop SORC, a new combined system of hydrogen production devices and fuel cells.
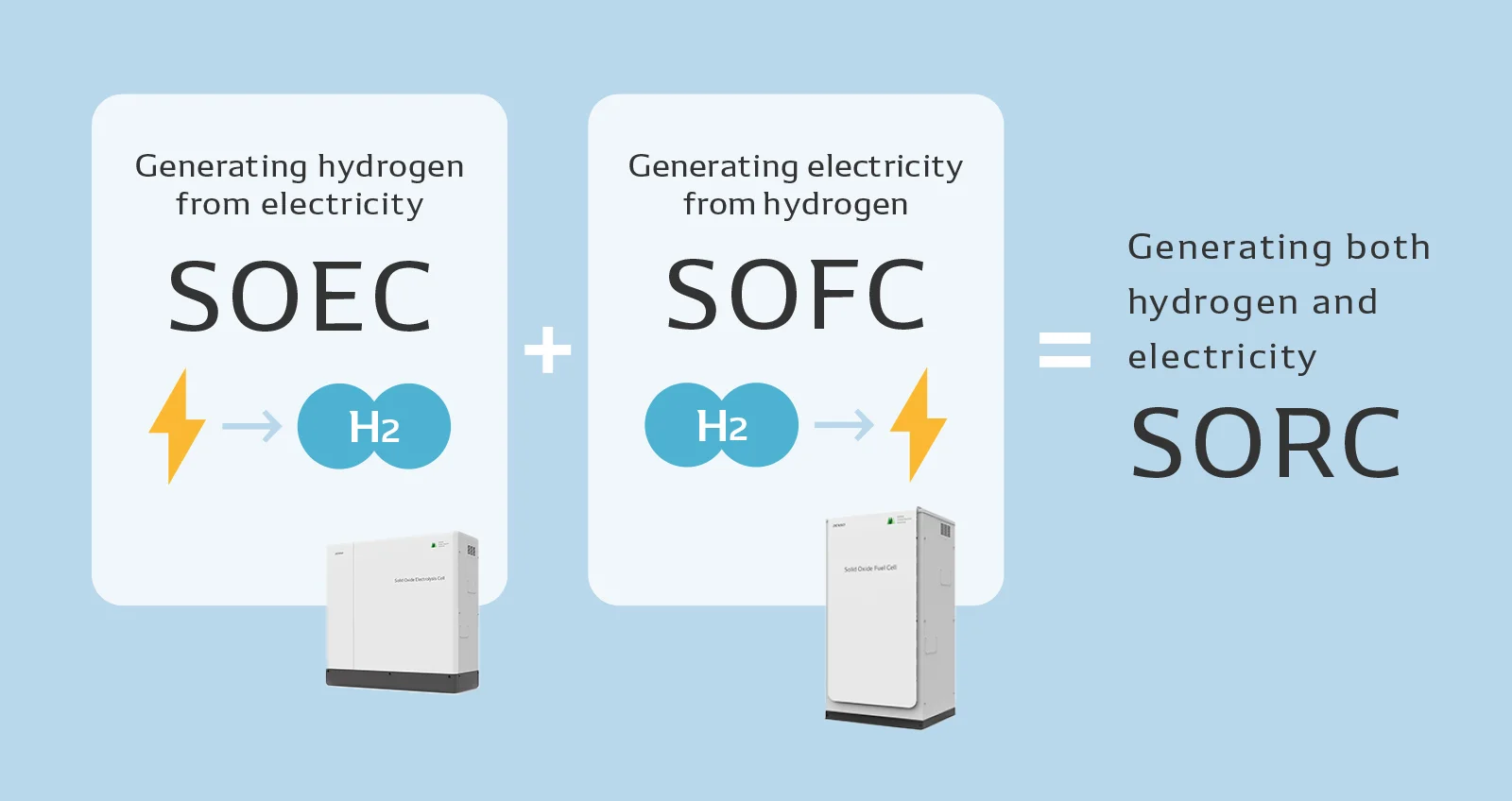
There is a technology to generate hydrogen and CO with co-electrolysis and produce methane, but it is still in the R&D stage. In order to create the future of SOEC, such as methane production by SORC and co-electrolysis, it is necessary to constantly evolve the material technology, and it is essential to cooperate with various partners.
DENSO believes in the potential of SOECs, and is working to solve technological challenges based on the development and mass production know-how and experience built up over the years through the manufacture of ceramic and thermal components for automobiles. Watanabe shares his view:
“Utilization of hydrogen is essential to achieve carbon neutrality in the future, and it must be economical. We work on the development with the hope of making hydrogen production economically viable and helping solve global problems.”
DENSO has only just begun to uncover the potential of SOECs. By working together with various partners, we will overcome technological obstacles and help the world achieve carbon neutrality.
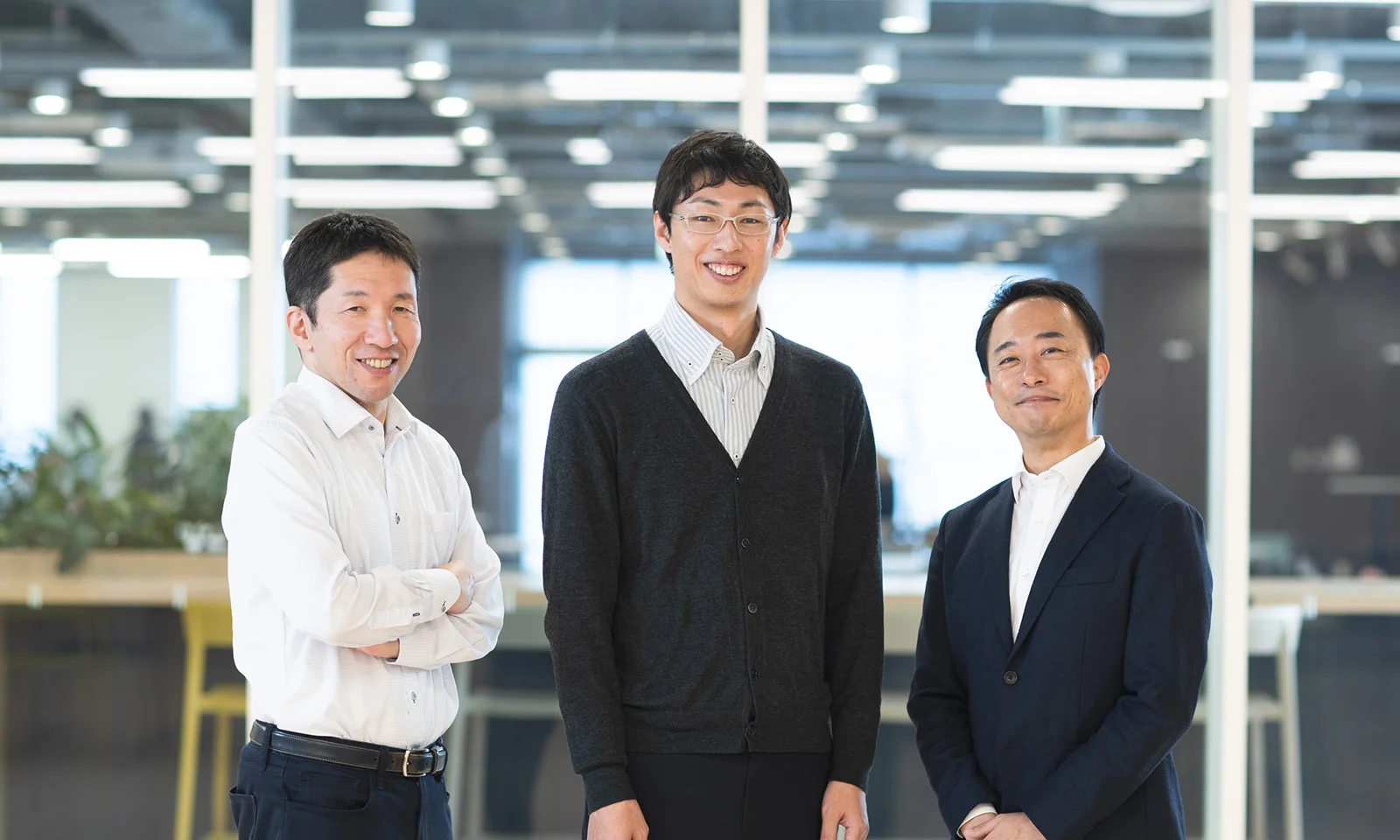
COMMENT
Changing your "Cant's" into "Cans"
Where Knowledge and People Gather.