Did you find this article helpful for what you want to achieve, learn, or to expand your possibilities? Share your feelings with our editorial team.
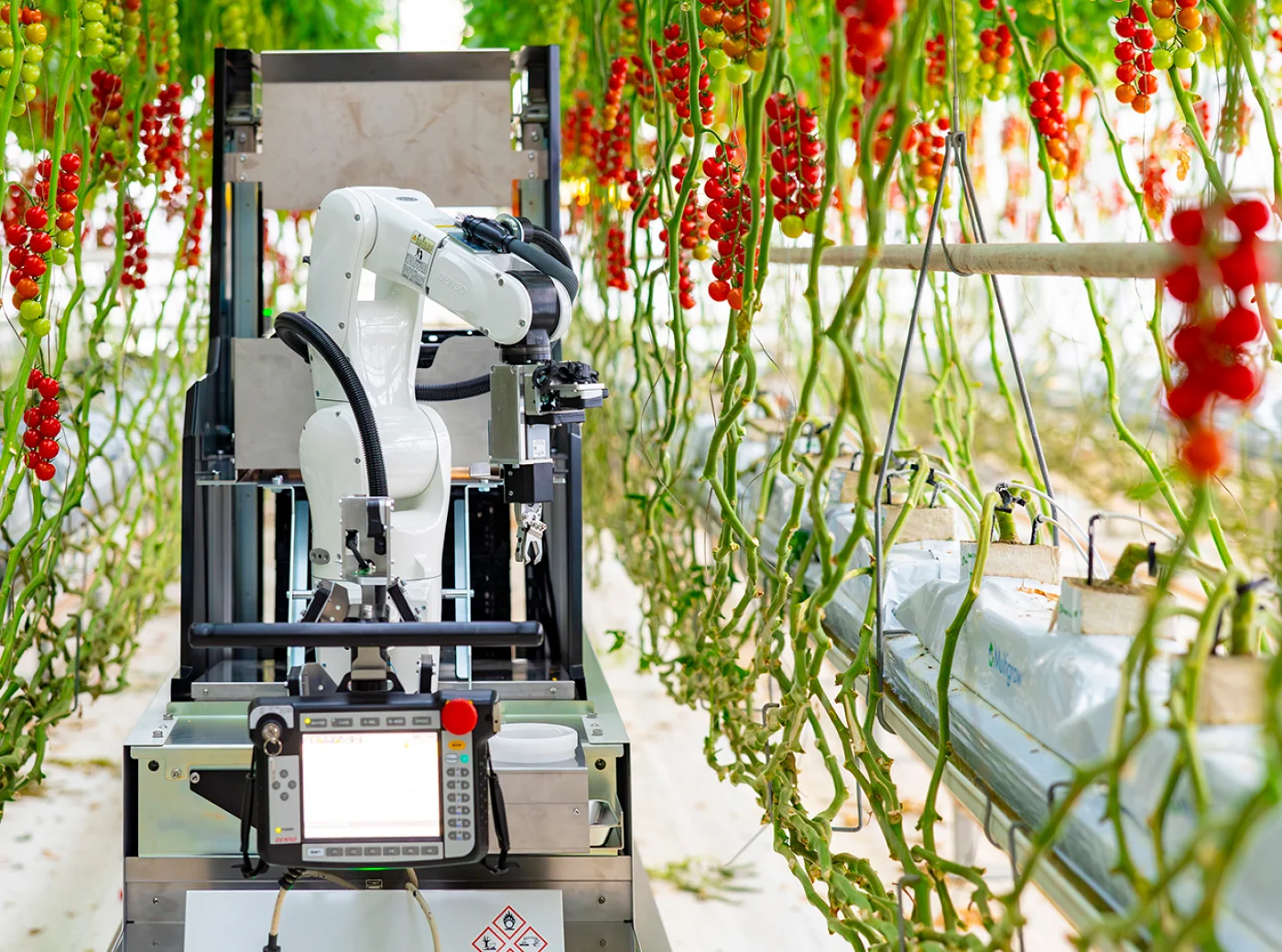
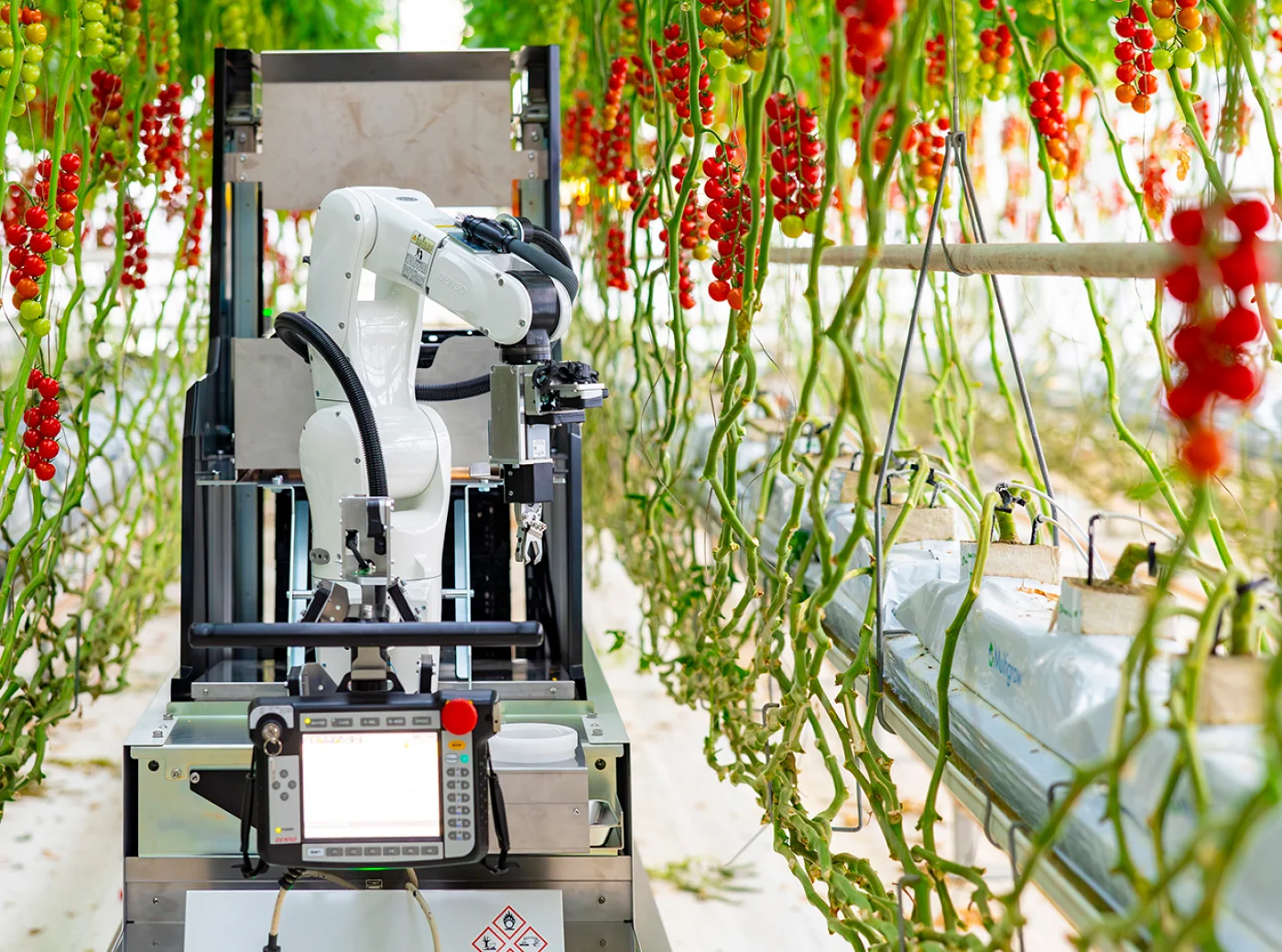
Oct 21, 2024
VISION & IDEARevolutionizing Agriculture: The possibility of Artemy®, the Fully Automated Harvesting Robot
DENSO and Certhon's Pioneering Venture into Automated Cherry Truss Tomato Harvesting
From farm to table, our food supply chain relies on countless individuals. But in the face of global challenges, how can we forge a more sustainable future for food production?
Imagine a world where fewer people could efficiently produce crops, where climate constraints are overcome, and where even seemingly unsuitable land can be transformed into productive farmland. To maintain food security, such perspectives may prove indispensable.
DENSO, confronted with the dual challenges of declining agricultural labor and looming food crises, has been leveraging its automotive expertise to pioneer the industrialization of agriculture.
One of our key focus areas has been addressing the challenges surrounding crop harvesting. In collaboration with Certhon, a DENSO Group company based in the Netherlands, we have launched a fully automated harvesting robot for cherry truss tomatoes, targeting the European market. This article explores our innovative approach to solving the intensifying problem of labor shortages in agriculture.
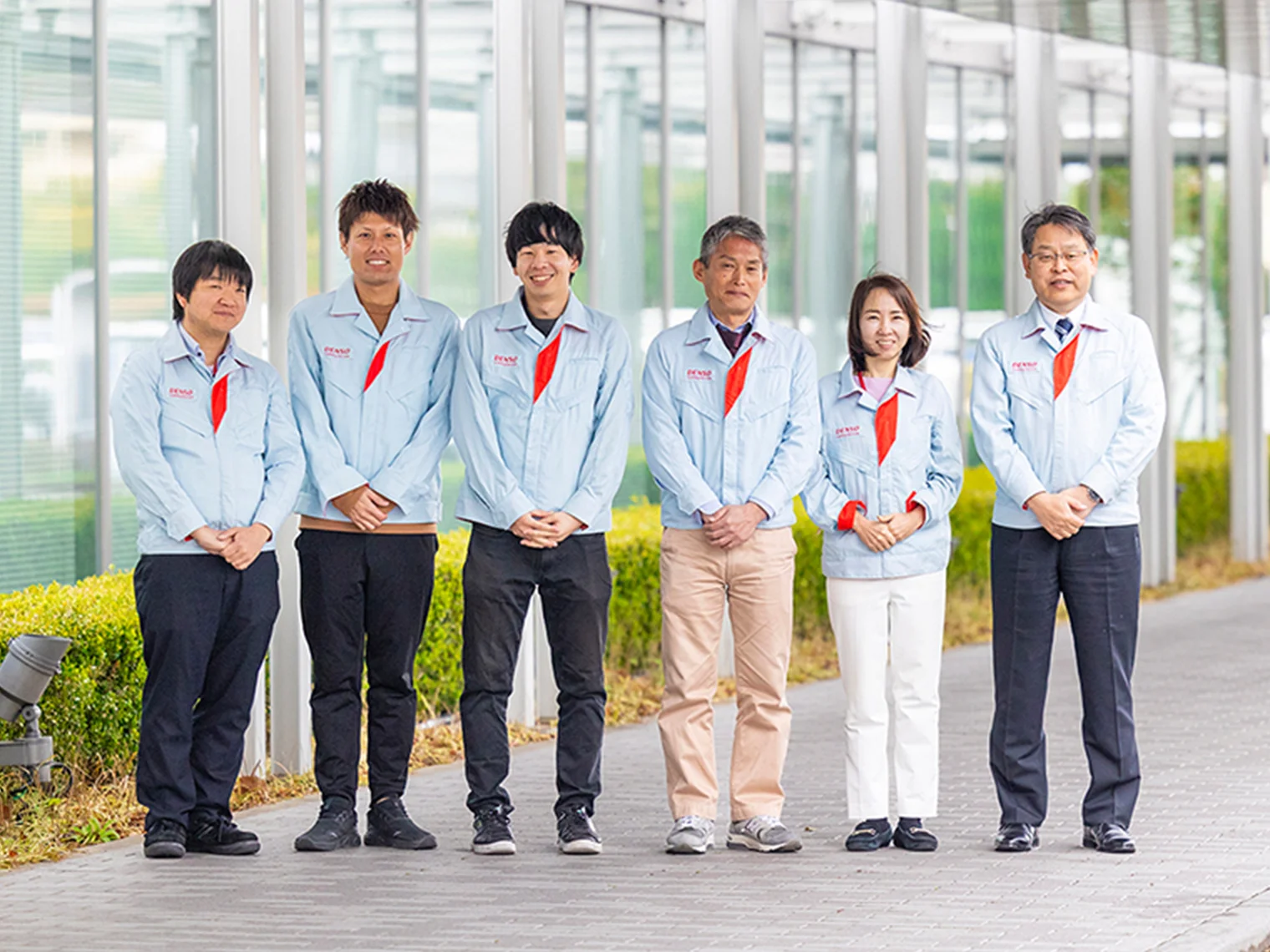
Contents of this article
Industrialization of Agriculture for Stable Food Production
Sustainable food production faces numerous challenges as we strive to meet the increasing food demand driven by global population growth. First and foremost is the instability in agricultural production caused by climate change and extreme weather events.
According toreports from Japan's Ministry of Agriculture,Forestry and Fisheries, rising average temperatures are expected to affect crop yields, increase disease occurrences in livestock and aquaculture, and impact fish catches. Moreover, extreme weather events such as droughts, floods, and severe storms—all exacerbated by climate change—are causing significant damage to crops.
In Japan, for instance, future increases in average temperatures are projected to lower rice quality and shift the suitable cultivation areas for crops like grapes.
Another crucial challenge is the declining agricultural workforce, driven by an aging population of farmers, unstable income, and harsh working conditions.
A 2019 report from the Ministry of Agriculture,Forestry and Fisheries predicts that the world population will reach 8.643 billion by 2050, with food demand increasing to 1.7 times the current level. Meanwhile, the agricultural workforce in the United States, Europe, and Japan continues to decline.
In light of these global challenges, there is an urgent need for agricultural practices that are insulated from the whims of weather and geography, along with innovations in automation and labor-saving technologies that can compensate for the shrinking agricultural workforce.
The Cherry Truss Tomato Fully Automated Harvesting Robot - Enabling Sustainable Agricultural Production
DENSO has identified agriculture as a key focus area in its Long-term Policy 2030. The Food Value Chain (FVC) Business Development Division is working to ensure stable food supply and safety, drawing on decades of technological expertise from the automotive field.
In the production segment, which forms the starting point of the value chain, DENSO has begun initiatives to realize sustainable agricultural production that enables “Growing anything, anywhere. For everyone,” around the world. The first product to hit the market is Artemy®, a fully automated harvesting robot targeting cherry truss tomatoes.
Artemy was born through joint development with Certhon, a DENSO Group company headquartered in the Netherlands that provides large-scale horticultural solutions to more than 20 countries worldwide. Order acceptance for Artemy began in May 2024, initially targeting the European market.
But why cherry truss tomatoes? And why Europe? The answer lies in the current state of large-scale greenhouse in Europe. Europe commands a staggering 66% of the global market for large-scale greenhouse, and tomatoes are its largest crop. Nearly 60% of tomatoes harvested in Europe are cherry truss tomatoes, with harvesting alone accounting for about 30% of the total labor hours in greenhouses. The need for more efficient harvesting solutions is acute.
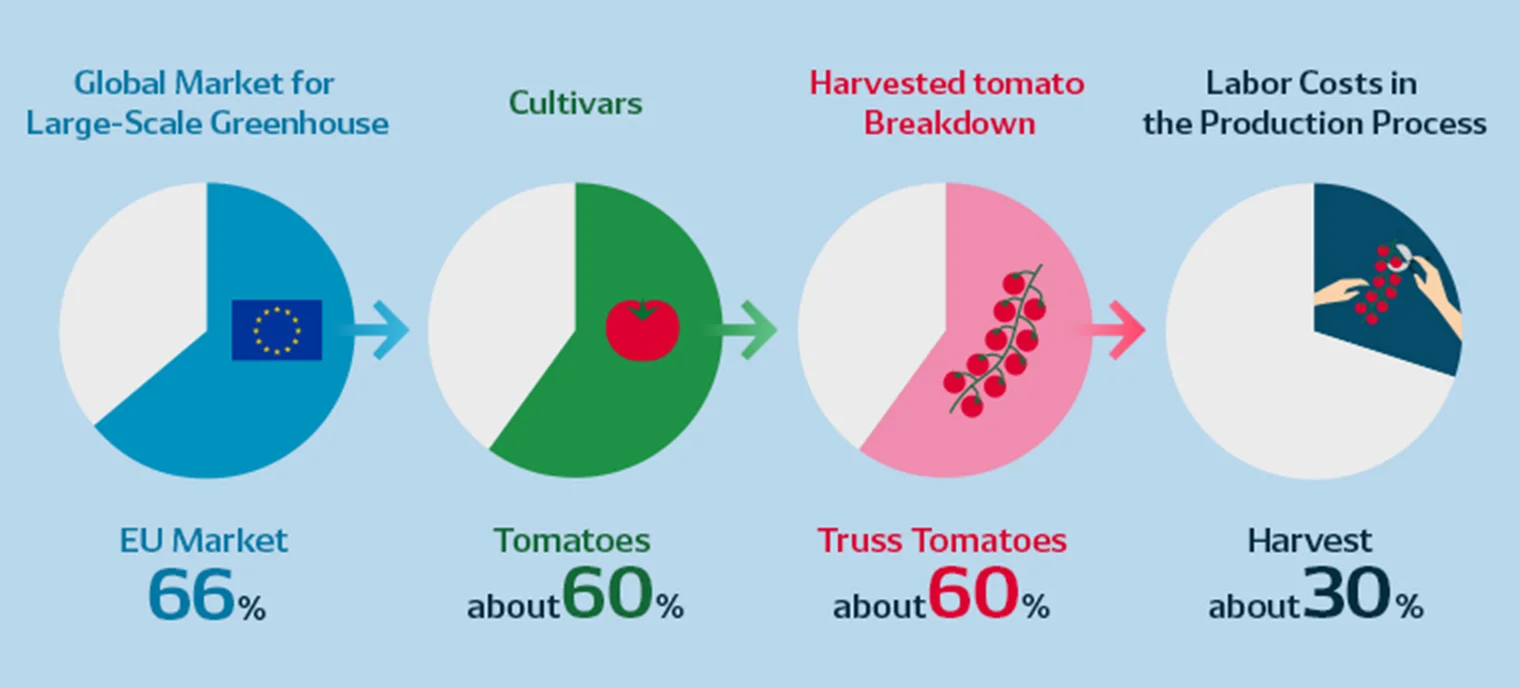
So, how does Artemy improve the efficiency of cherry truss tomato harvesting?
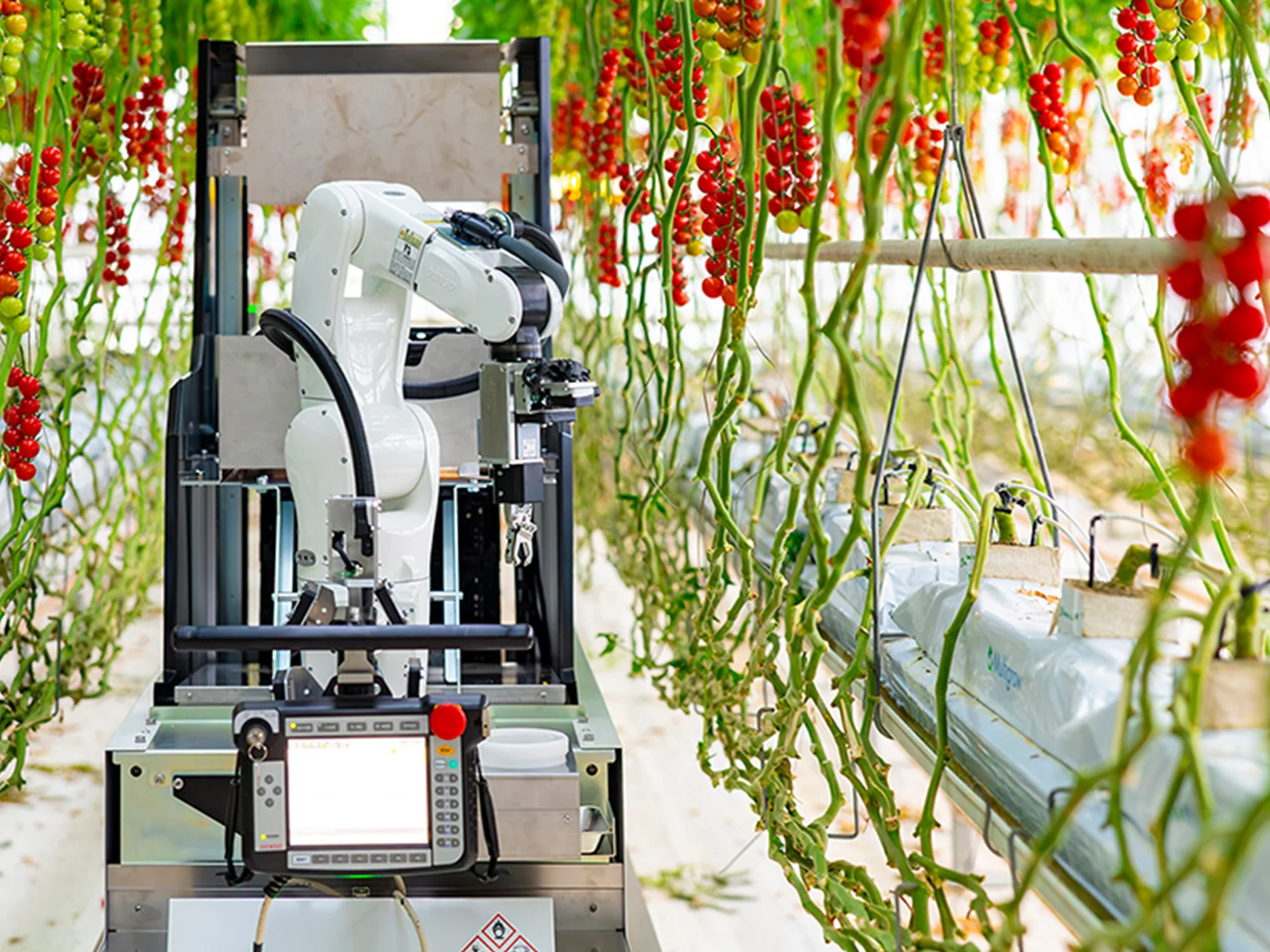
First, Artemy automatically runs on a running lane (a hot water tube installed in a greenhouses). Using peripheral monitoring technology, it recognizes obstacles in the passage and the destination lane, enabling safe and accurate automatic lane changes.
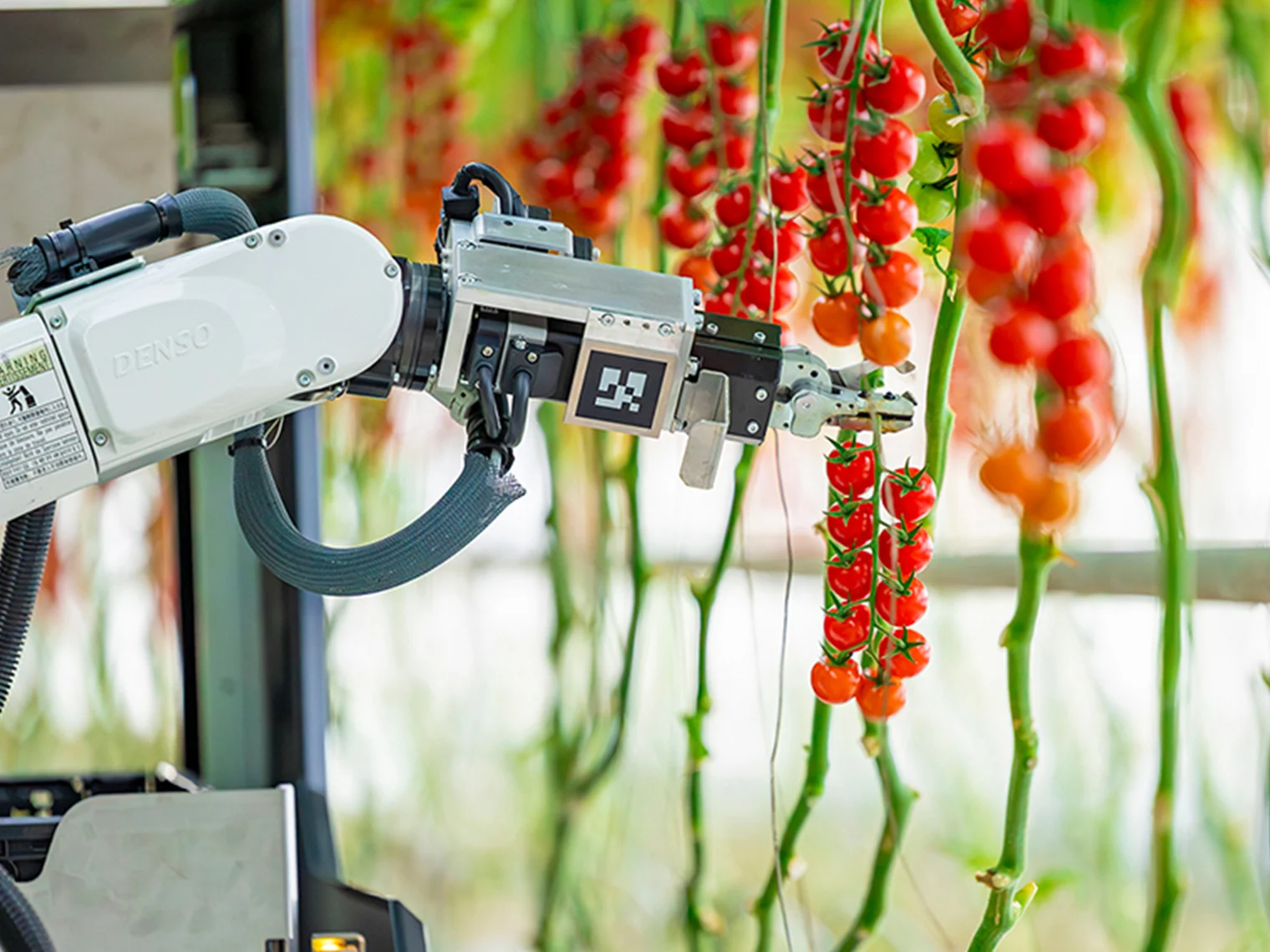
During harvesting, Artemy’s AI analyzes images captured by cameras to assess the ripeness of the tomatoes. Once a ripe cluster is identified, the robot arm uses scissors attached to the tip of the arm to neatly snip the stem and place the tomatoes into harvest crates.
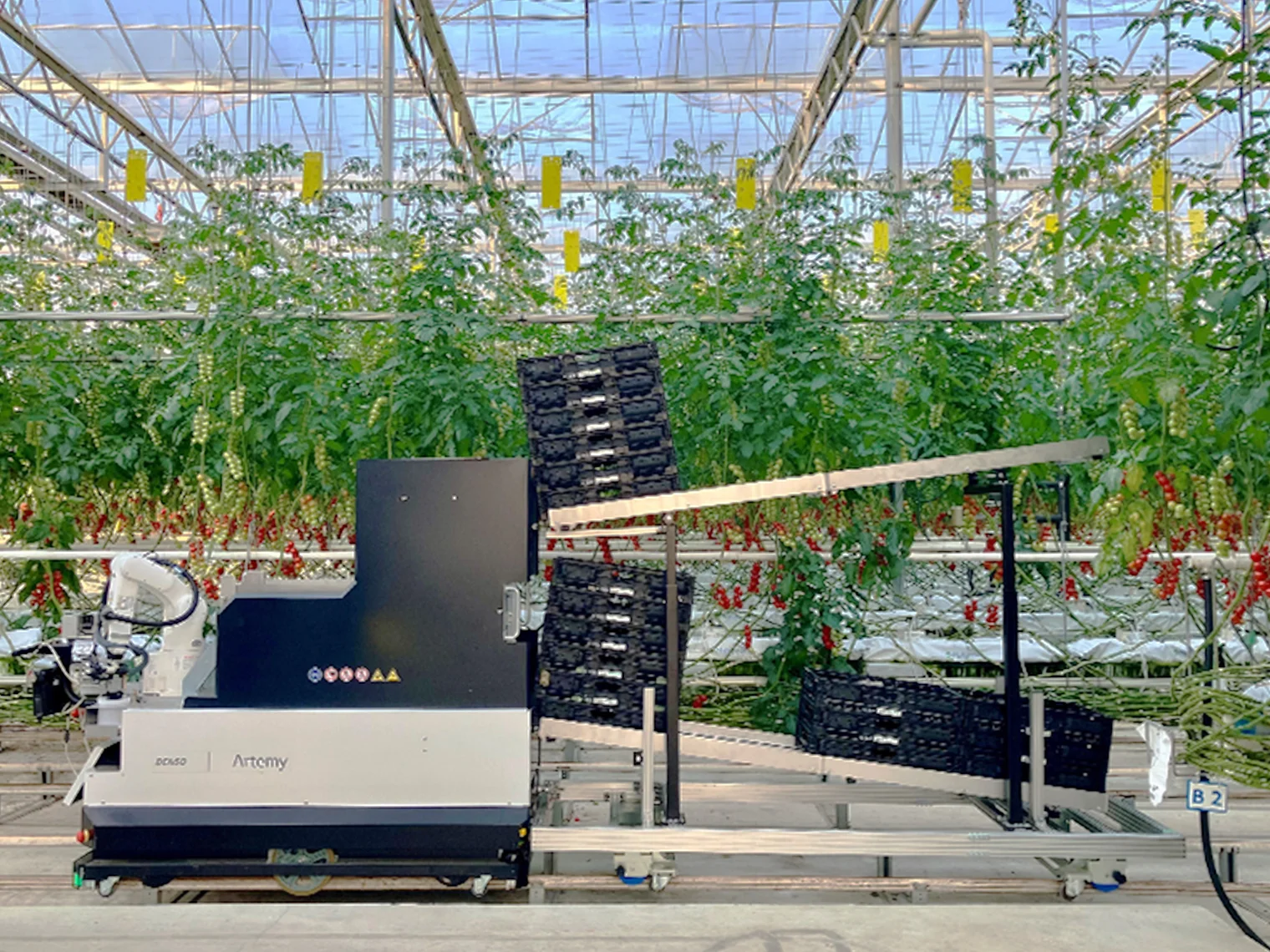
Artemy also features an automatic crate replacement function. It can carry six harvest crates, and when they are all full, it automatically moves to a cart with empty crates and replaces the full crates with empty ones.
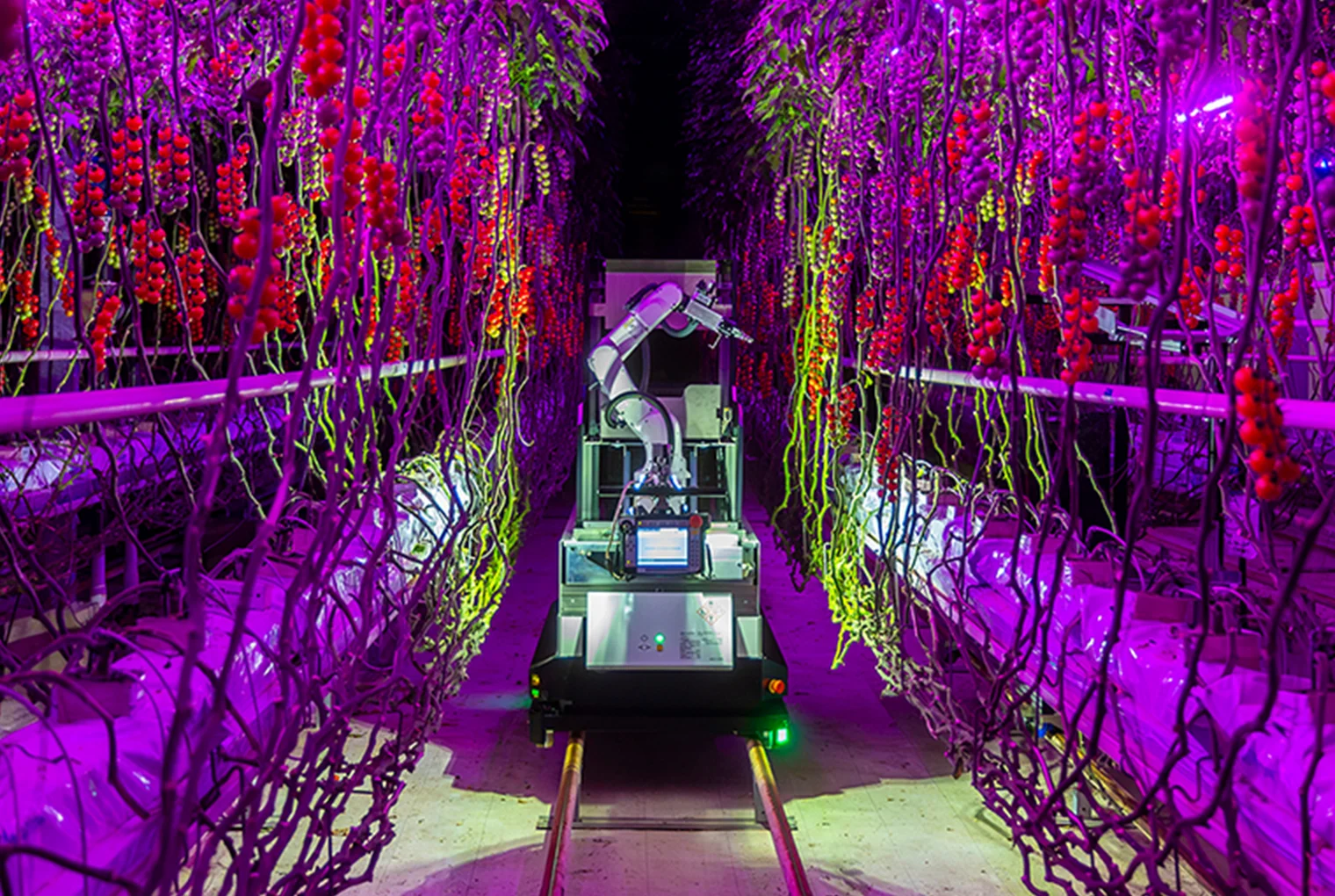
Equipped with LED lights to enhance its ability to detect clusters and stems, Artemy maintains a high degree of accuracy, even under less-than-ideal conditions, such as direct sunlight or supplemental lighting at night. The robot is powered by replaceable batteries, eliminating downtime caused by recharging.
Kouichi Hamashima of the FVC Business Development Division describes the impact Artemy brings to harvesting:
"Artemy doesn't just automate harvesting; it fully automates a series of harvesting-related tasks, including changing harvest crates and disinfecting scissors. Unlike humans, it can operate continuously for over 20 hours, day and night. We estimate that introducing Artemy can reduce harvesting labor by about 40%, contributing significantly to solving agricultural challenges in Europe, where immigrant restrictions and labor shortages are pressing issues."

DENSO x Certhon - Close Collaboration for Customer-Oriented Product Design
In the development and sales of Artemy, DENSO primarily handles product development, while Certhon is responsible for listening to customer needs in the European market, sales, and service implementation support.
The two companies worked closely together throughout the product development process leading up to the start of order acceptance in May 2024. This journey was not without its challenges and iterations.
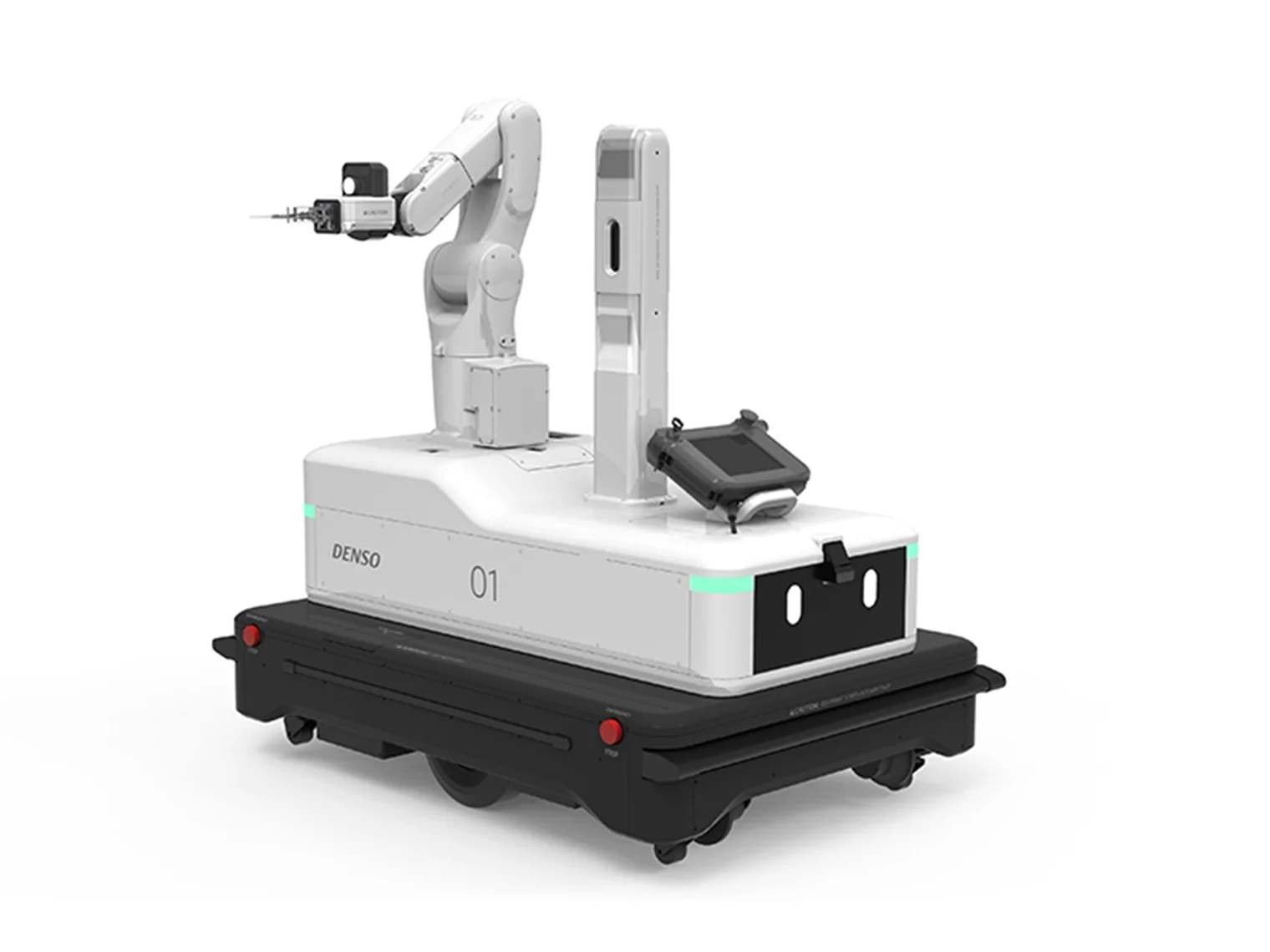
The original prototype for Artemy was a demonstration machine introduced at AgriD, Japan's largest tomato greenhouse, operated in cooperation with Asai Nursery Inc. in Mie Prefecture. While working on developing and demonstrating technologies to improve vegetable cultivation productivity, Certhon's management visited AgriD and expressed a strong desire to introduce this technology to Europe as soon as possible, which became the catalyst for development.
Katsuru Kobayashi from the FVC Business Development Division describes the journey to order acceptance:
"DENSO's partnership with Certhon began in late March 2020 when DENSO invested in Certhon, but remote project promotion presented many challenges. To address this, we dispatched Artemy's technical staff to Certhon, and Certhon's technicians also came on extended business trips to learn about Artemy's product development process and after-sales service. Through these personnel exchanges, development progressed more smoothly."
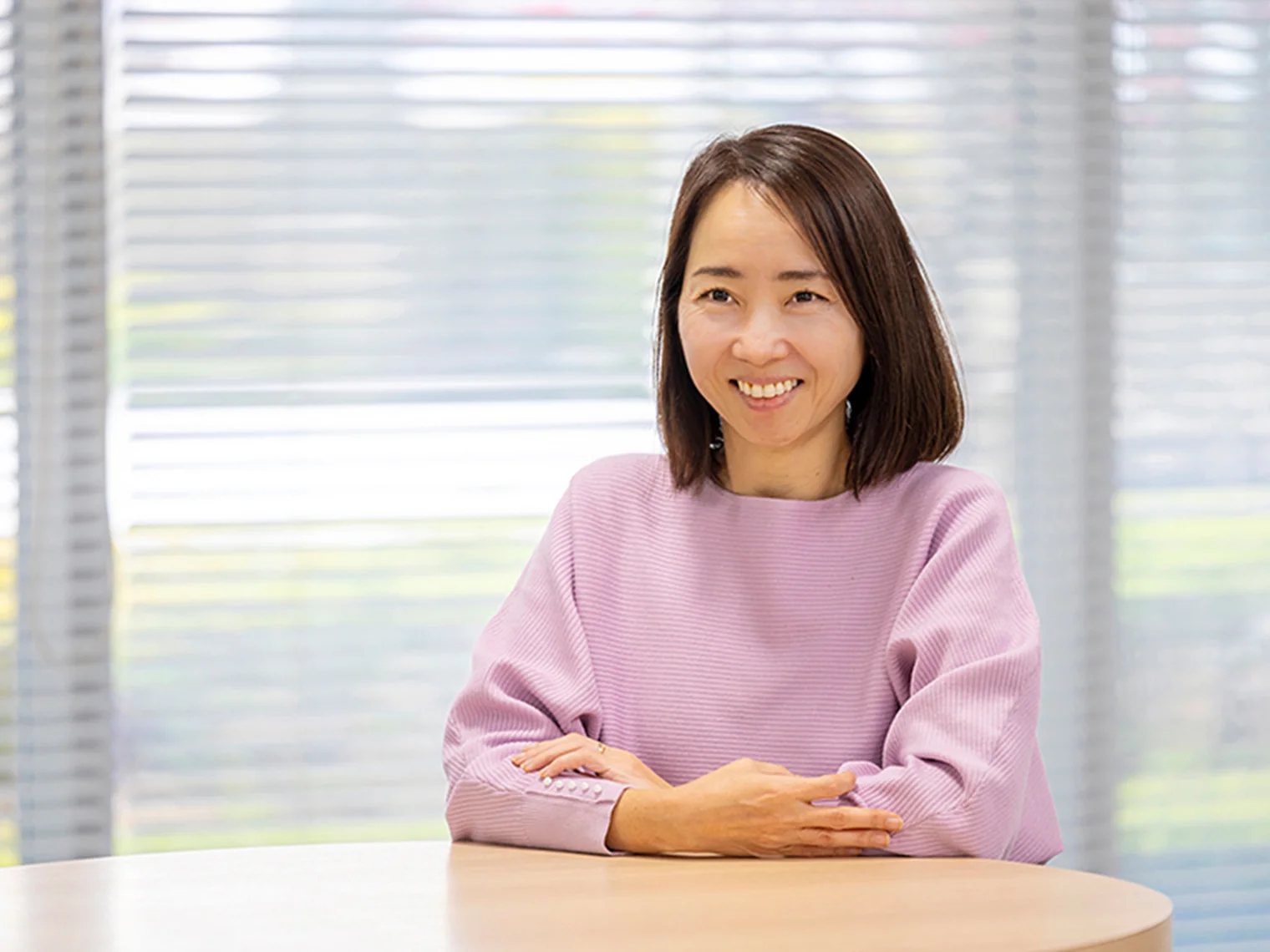
How are the strengths of both companies reflected in Artemy? Various technologies and know-how from DENSO, which has been working on multiple projects aimed at Industrialization of Agriculture, have been integrated into the robot.
Unlike industrial products, tomatoes vary in size, shape, growth rate, and orientation depending on the variety, producer or production method, and season. This presented a challenge in automating harvesting, as the factors to consider are extensive and fluid. Hayato Ishikawa, a software development engineer in the FVC Business Development Division, explains how DENSO's automotive technology and know-how came into play:
"In developing Artemy, we leveraged image recognition technology used in ADAS (Advanced Driver Assistance Systems) for tomato identification. This technology is crucial for vehicles to recognize their surroundings, including pedestrians, oncoming vehicles, and fixed objects.
Additionally, the robot arm used to harvest irregularly shaped agricultural products is based on the arm trajectory generation technology developed by DENSO WAVE for industrial robot arms, which allows the arm to determine its trajectory while avoiding obstacles.
We also applied safety design know-how from AGV (Automated Guided Vehicle) autonomous driving to ensure human safety during automatic lane driving and lane changes. Artemy is truly a culmination of technologies developed across various DENSO departments."
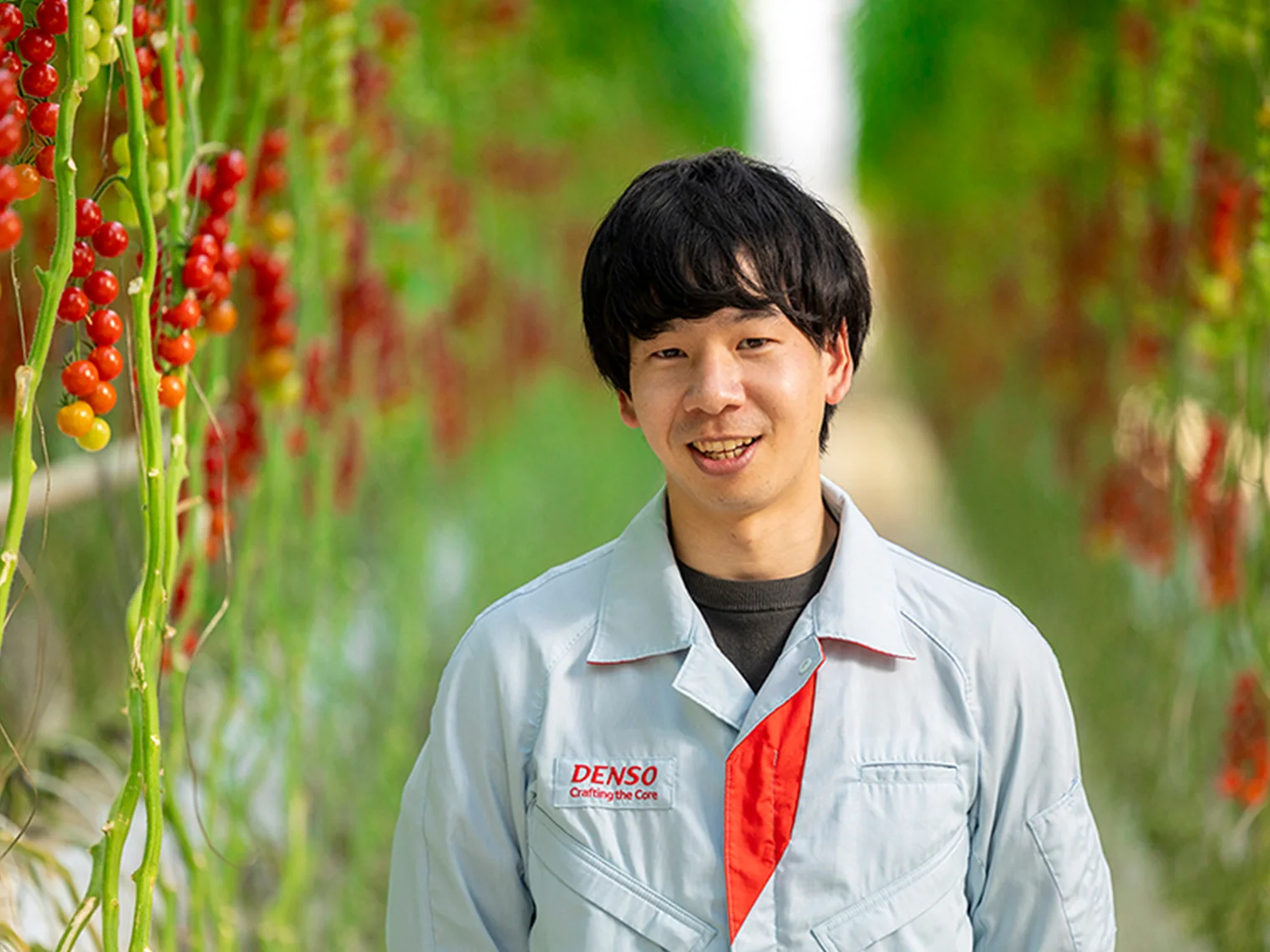
Certhon's involvement was also crucial in determining product specifications. Being at the forefront of the European market, Certhon can collect various customer challenges and needs. Based on this customer feedback, features such as automatic lane changing and automatic harvest crate replacement were incorporated into the specifications.
"Through agriculture, we want to create a world where stable production is possible ‘Growing anything, anywhere. For everyone.' A vision shared by both DENSO and Certhon. It's the synergy of both companies' strengths that has made this realization possible," says Kobayashi.
Balancing Commitment and Compromise to Achieve Rapid Development
While leveraging the strengths of both DENSO and Certhon, the journey to product commercialization was not without its challenges.
One of the major challenges we encountered was the difficulty in parts supply and procurement. During the COVID-19 pandemic, production across various industrial sectors contracted due to worldwide lockdowns, leading to temporary disruptions in the supply of materials and components. Even after the pandemic subsided, we faced ongoing procurement issues. The establishment of new large-scale semiconductor manufacturing plants in Japan meant that components originally intended for Artemy were prioritized for these factories, making it increasingly challenging for us to secure the necessary parts.
Another challenge was obtaining CE certification for product export to the European Union (EU). To sell products in the European market, compliance with EU regulations is required, including the RoHS Directive, which restricts the use of certain hazardous substances in electrical and electronic equipment, and the REACH Regulation, which mandates the declaration of the total content of substances of concern. Artemy has about 2,000 parts, involving many collaborative manufacturers. It was necessary to have these companies share evidence regarding the use of environmentally hazardous substances.
*EU safety directive indicating that a product has passed a specific test, meaning it can be legally sold anywhere in the EU and the European Economic Area
"As we approached mass production, we discovered that some parts did not comply with regulations, or some partners had policies against sharing evidence or lacked experience in this area. We continued to propose and explain to these partners, including providing education on regulatory compliance. However, some parts remained difficult to address, leading us to switch to alternative components in some cases. Despite these challenges, we managed to proceed to mass production," explains Inada.
Despite facing these challenges, Artemy progressed from the product planning meeting in January 2022, where development and mass production policies were decided, to commercial sales in about two and a half years. The rapid realization of a product consisting of over 2,000 parts was not only due to the connections, technologies, and know-how of each company but also because of a bold step towards transforming the development process.
"Given the need to quickly adapt specifications to various conditions and make rapid improvements, following the existing 'automotive parts development rules' designed for producing millions of cars annually would have resulted in a long development span and enormous development costs. Therefore, we worked on flexibly changing the system, involving the Quality Control Division and addressing internal rules," says Nishino.
In doing so, they strived for a design that balanced DENSO's commitment to quality and safety with necessary compromises.
"The most notable example of compromise was adopting a replaceable battery structure. Instead of making all components in-house, including batteries that wear out quickly, we adopted a design that uses high-quality parts already available in the market for periodic replacement," explains Nishida.
Additionally, agile development through close collaboration between DENSO and Certhon, and the assembly of team members from DENSO with diverse backgrounds—including those with experience in agricultural design, automotive parts, and robotics development—were major factors supporting rapid development.
Artemy's journey doesn't end with product sales. As with the replaceable battery design, there's a need to maintain continuous contact with customers and enhance support systems. In after-sales service, Certhon's dedicated service personnel, who are thoroughly familiar with the product, will conduct regular inspections of purchased products (similar to car inspections) and provide 24/7 repair and parts supply services.
DENSO is responsible for designing systems that allow users to easily perform routine inspections and replacements. They will provide support through manuals and tools, early detection and sharing of anomalies (including precursors), and establish a system for smooth implementation of repairs in Japan and the Netherlands.
Approaching Various Agricultural Production Challenges, Starting with Harvesting
The commencement of order acceptance is just the starting point. Through future sales strategies and market expansion, we must accelerate the resolution of challenges surrounding agriculture.
After establishing a track record in the Netherlands, the plan is to expand to other large-scale greenhouse operators, with an eye on expanding across the European market. For producers without direct connections to DENSO and Certhon, the strategy involves package sales with agricultural greenhouses—Certhon's specialty—to appeal to customers in various countries and regions.
"Following the European market, we envision approaching the North American and Australian markets, where labor shortages are prominent and labor costs are high. While Artemy was initially developed for cherry truss tomatoes, we intend to adapt the knowledge gained to handle a wide range of agricultural products.
Furthermore, we're considering leveraging the data obtained from the robot's image recognition for solution businesses such as pest prediction and yield forecasting. By introducing Artemy to support automation of harvesting in producers' greenhouses, we can gain insight into the diverse challenges faced by producers and address these issues through new solutions," explains Kobayashi.
Hamashima also shares his vision for the future that he hopes to realize through Artemy's development:
"When we started development, the harvesting success rate was less than 10%. Through the development process, we've made numerous design revisions, including functional additions and performance improvements aimed at full automation to meet European market needs. We've finally reached a point where we can confidently mass-produce a product that will satisfy our customers. However, this is just the beginning.
Looking ahead, we aim to develop robots that can perform various tasks beyond harvesting, such as leaf pruning and plant training. Our goal is to launch additional products that will contribute to the industrialization of agriculture and help create a more abundant world.
While automated harvesting robots are still in the phase of gaining social recognition and penetration, I believe Artemy will be a product that significantly changes the industry, starting with this breakthrough."
Changing your "Cant's" into "Cans"
Where Knowledge and People Gather.