Did you find this article helpful for what you want to achieve, learn, or to expand your possibilities? Share your feelings with our editorial team.
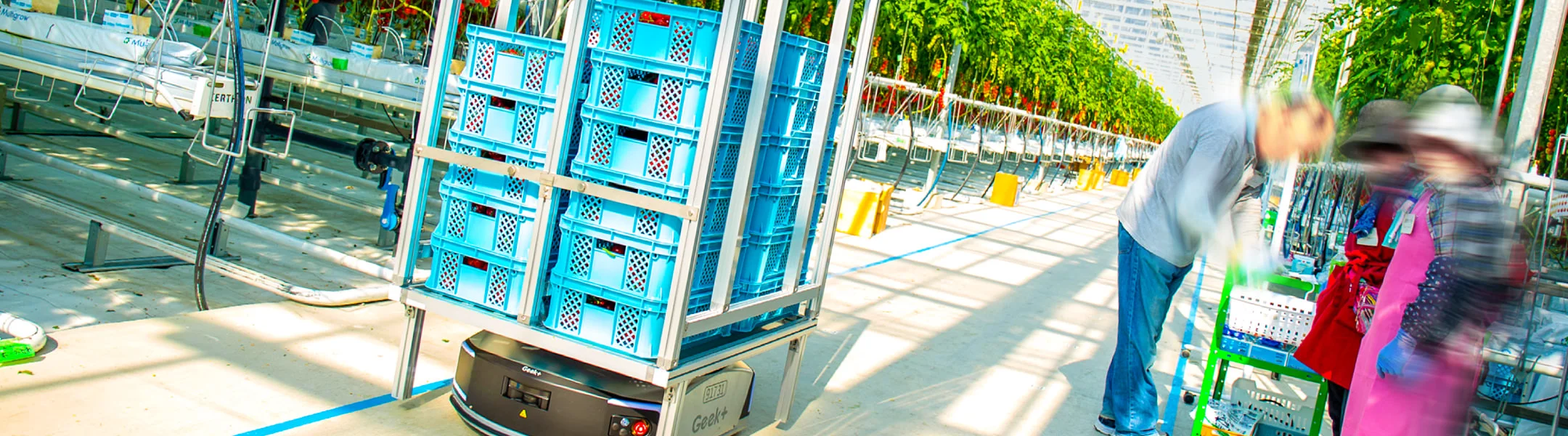
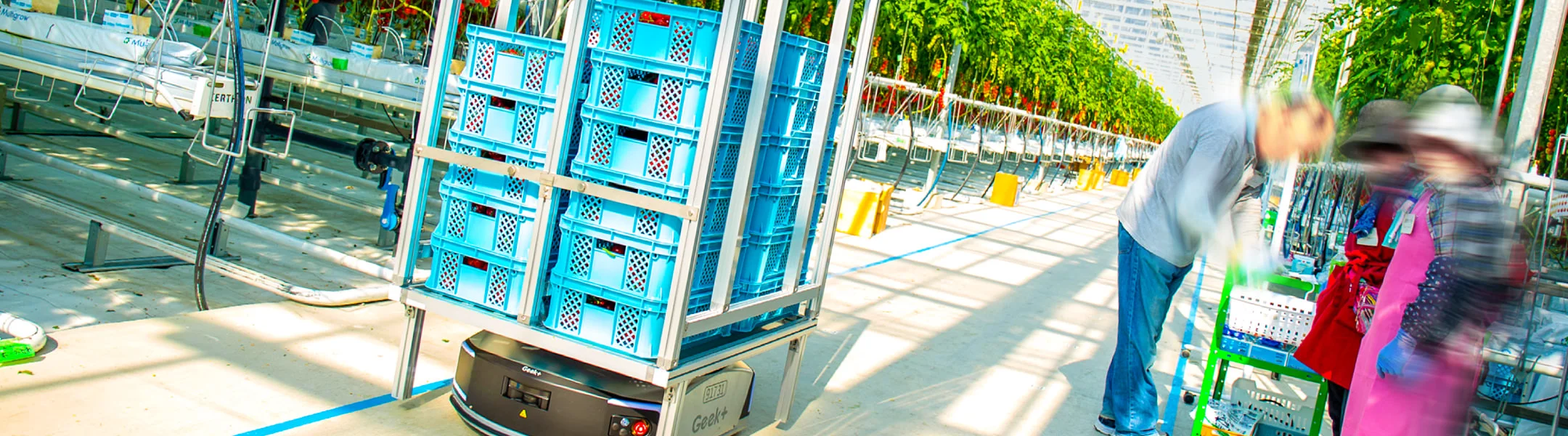
Aug 22, 2022
TECH & DESIGNLarge-scale smart greenhouse fo livery everyone
Sustainable farming without overburden, waste and irregularity at the AgriD of the large-scale smart farm
-
Food Value Chain Business Development Div.Daisuke Sakurai
Daisuke Sakurai majored in aerospace engineering at university and then used this knowledge to develop and design automotive air conditioning systems after joining DENSO. Responding to an in-house ad for job openings, Sakurai transferred to the Food Value Chain Business Development Div. in 2018, after which he was sent to work and learn agriculture at Asai Nursery, Inc. in Tsu City and helped found AgriD Inc. in Inabe City.He served as general manager onsite at AgriD for two years, helping it to achieve stable operations. Today, Sakurai works for DENSO AgriTech Solutions, Inc. in Minato-ku, Tokyo, where he is involved in sales engineer for greenhouse businesses.
-
Food Value Chain Business Development Div.Shokichi Hosoe
Shokichi Hosoe joined DENSO in 1997 and majored in software development at an in-house junior college. He was assigned to electronic control unit (ECU) software development, and in 2015 he responded to an in-house ad and joined the Food Value Chain Business Development Div.Hosoe has taken part in software development for the Integrated climate control system, Medium-scale semi-closed greenhouse, Integrated production management systems, Automatic transport system and more.
The society issue of the declining number of growers worldwide marks a turning point. It’s up to us to overcome this challenge by making agriculture a more attractive profession, thus attracting more people into the industry.
DENSO Corporation is leveraging its manufacturing technologies, cultivated in the auto industry, to optimize farming operations while creating an agricultural system that boosts production efficiency and enables more flexible working styles. Thanks to these efforts, a new kind of agriculture is emerging in which human-robot collaboration.
Contents of this article
Utilizing manufacturing technologies to solve issues related to overburden, wastefulness and unevenness
I once read a DENSO article about the automated harvest robot, which mentioned the company AgriD Inc. What kinds of efforts are under way at AgriD?
Daisuke Sakurai: DENSO collaborated with Asai Nursery to establish AgriD, a large-scale smart greenhouse. We have also been conducting verification tests at AgriD to solve issues related to what we call the “Three Ms” in Japanese: muri, meaning overburden; muda, meaning wastefulness; and mura, meaning unevenness.
Agriculture involves working with plants, which are living organisms, and also with Mother Nature, and so various unforeseeable problems related to the Three Ms often occur. One example of muri, or overburden, is how growers are forced to constantly monitor and respond to the changing growth patterns and conditions of their crops, which do not always turn out as planned, in order to produce the intended results. As for muda—wastefulness—it may be necessary to hire more staff than planned during the harvest season, sometimes resulting in multiple people handling the same tasks. Finally, unevenness, or mura, may occur in the quality of harvested products due to nonuniform operations, caused by differing experience and skill levels among workers.
By eliminating issues related to the Three Ms, it’s possible to achieve a more sustainable agricultural business with less financial pressure on management.
Through discussions with Asai Nursery, a company with many advanced agricultural technologies, we were able to identify a range of problems like those I have just mentioned. We believed we could use DENSO’s manufacturing technologies and approaches such as kaizen and automation to eliminate issues related to the Three Ms. And by working together with Asai Nursery to create a next-generation horticulture model for the world, we hoped to increase the appeal of agriculture as an industry and occupation. To this end, we built a large-scale smart greenhouse in Inabe City, Mie Prefecture in 2020, marking the start of AgriD’s efforts.
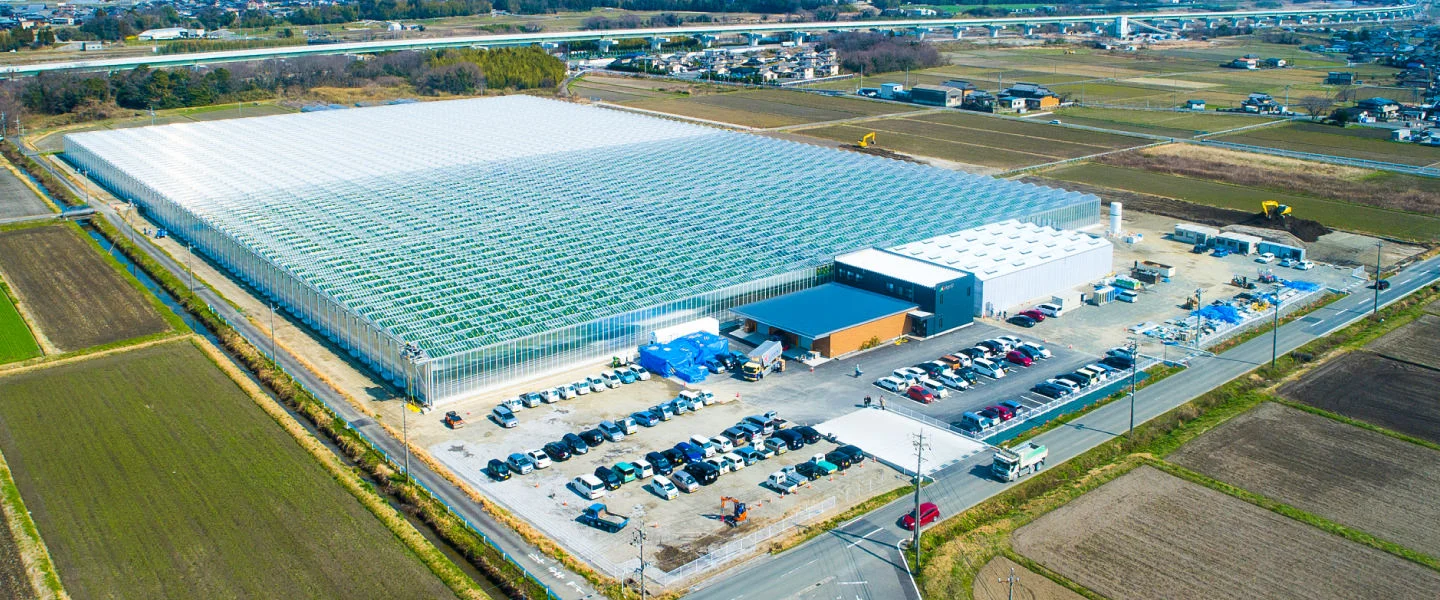
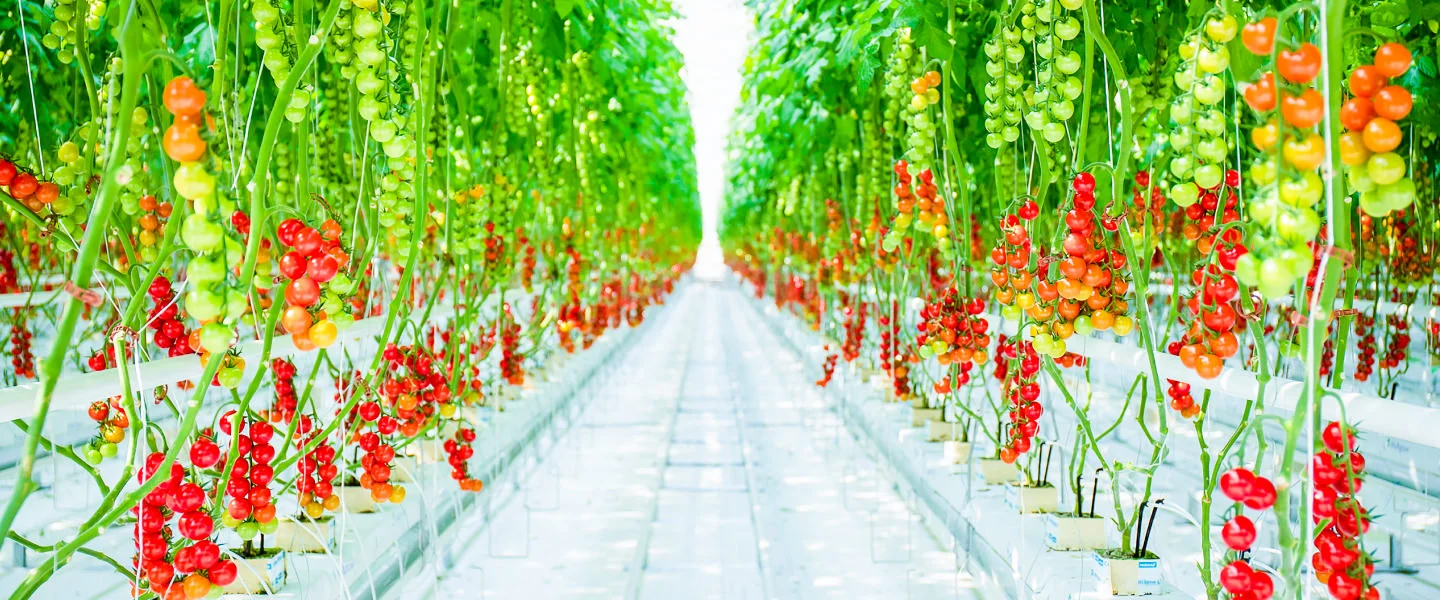
Bottom: interior view of AgriD’s facilities
How did you try to eliminate the three Ms?
Sakurai: To start with, I visited Asai Nursery to participate in their daily farming operations, and the worker taught me in great detail about how they cultivate and harvest crops. With tomatoes, for example, one important task for worker is to guide the growth direction of the tomato plant stems. We videoed worker as they attached clips to the plants to orient the stems, and thus measured the time required to complete the task. This revealed some unevenness among the worker in this task.
Hosoe: In addition, we observed wastefulness in how they managed information. AgriD’s greenhouse facility is divided into rows, with specific worker assigned to each, and each worker used to record their start and end times on paper. However, tabulating these figures for the approximately 50 workers onsite was time-consuming, and therefore AgriD only did this a few times each month. This made it difficult to manage the work in detail based on data analysis, and so number of workers required were roughly estimated instead.
Another type of wastefulness was the paths of movement taken by workers. Workers harvested tons of tomatoes every day. After picking the fruit, the worker would load them onto a hand-operated cart, and then take them to a nearby pallet and transfer them. Then, after a temporary stop at this waypoint, each pallet was transported using a pallet jack to another location, where all of the pallets were then transported by forklift to yet another location.
Sakurai: In addition, production yields vary during different times of the year, and the facility would just hire more people when things got busy. Then, when the busy period was over, many of the workers were told to go home because there was no work for them. This failure to standardize labor amounts consistently for each worker was a problem; actually, this is a challenge faced by all agricultural growers.
Moreover, because the plants being cultivated are living things, their shapes and growth patterns vary widely, and some workers struggle to adapt when they encounter unexpected crop shapes. Automobiles can be produced based on consistent quality conditions and then checked afterward for defects and issues, but this does not work for agricultural products.
Hosoe: In order to overcome these challenges, we had to change our way of thinking. Workers were previously responsible for writing down information such as tasks and locations on their own, but we changed this so that managers now issue instructions to worker and then collect data on results and analyze it automatically. In addition, we created an integrated production management system for managing operations overall in the greenhouse, including worker attendance, work instructions for cooperative work robots, and other such aspects of operations.
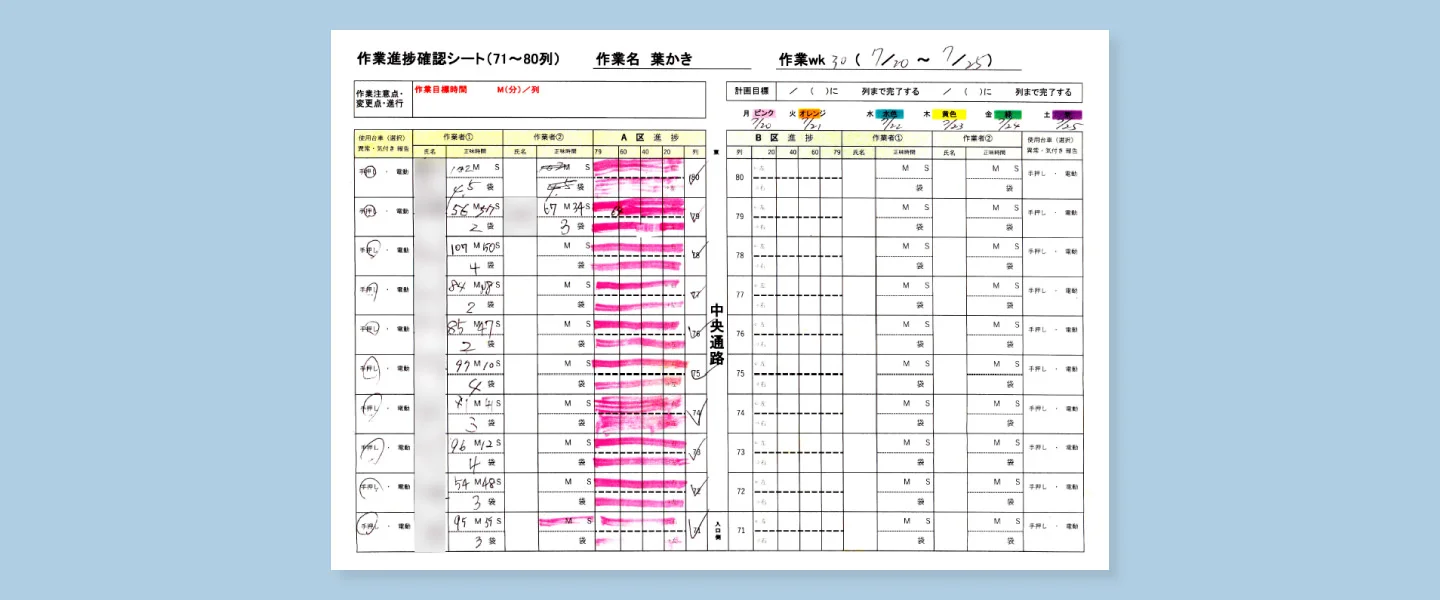
Creating an optimized work environment to bring out the best in every employee
How did AgriD conduct production using the newly developed, integrated production management system?
Hosoe: When an employee arrives at the large-scale smart greenhouse, they first pick up a tablet device and log in using their assigned ID. The tablet then tells them which row they will be working on that day, as well as their assigned tasks. When they reach the specified row, notifications and precautions regarding the day’s work are displayed on-screen, and the staff checks these while proceeding with their tasks.
During the course of the day, if they find a pest in the crops or a similar issue, they can take a photo using the tablet’s camera and use one of its software functions to communicate with a manager. In the past, whenever a worker encountered a problem, they had to walk around the huge facility searching for a manager. But now, the system facilitates communication between the two parties as well as faster solutions to problems.
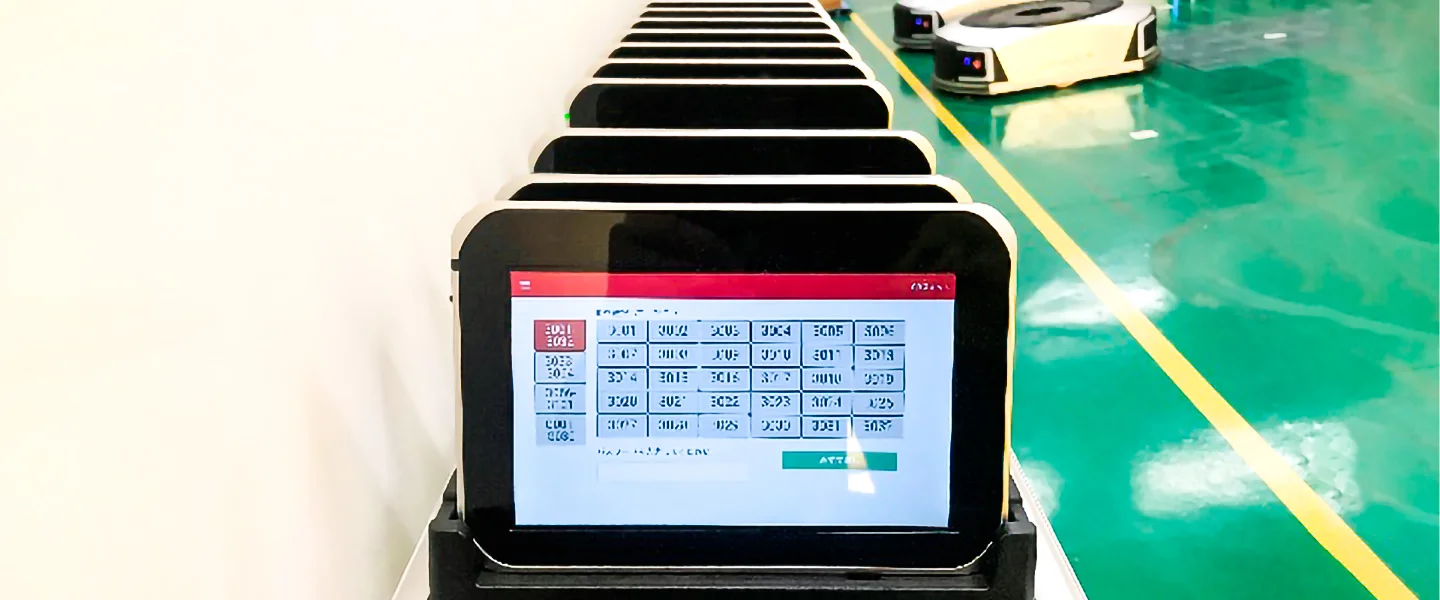
Sakurai: In regard to attendance management, it’s important to remember that many of the staff working at AgriD are mothers with young children, which means their availability varies greatly from person to person. We have designed the system to include more than 10 preset shift types—mornings only, afternoons only, full-day shifts, and so forth—from which the worker can choose and sign up for as needed. Normally it would be very difficult for a manager to keep track of so many different shift types, but with AgriD’s newly system it’s possible to calculate how many work hours are required to complete operations, and to look ahead more than a month in advance at the available labor force and work demand information.
Additionally, the system includes a function that automatically assigns tasks to available staff. When there are not enough worker to handle the required tasks, managers typically talk to employees individually about working additional hours. But thanks to the predictive functions of the system, it’s easier than ever to manage worker and their tasks.
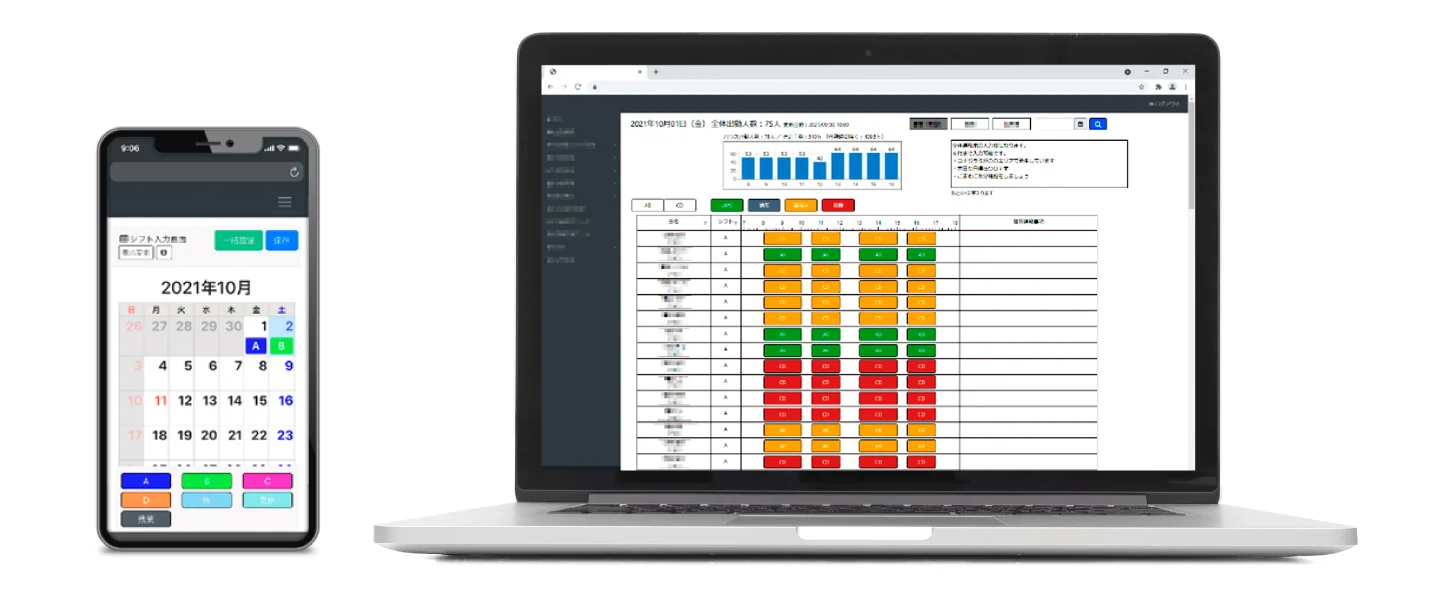
Right: managers use the integrated production management system to confirm working hours and attendance in detail
Sakurai: In the evening, managers check work records for employees that day. They confirm the levels of progress for each row, check whether any employees encountered problems in their work, and make adjustments as necessary to the next day’s schedule. This approach enables more accurate prediction of labor requirements and also increasing productivity.
For automatically assigned tasks, are all workers capable of carrying out the same tasks equally well?
Sakurai: Yes. We aim to ensure consistent quality in work results no matter who carries out the work, which is possible mostly due to assistance from Asai Nursery. Based on their deep knowledge of tomato cultivation, we are working to create and standardize optimal work procedures.
As a company, DENSO tends to take an industry view when tackling problems related to the Three Ms. We usually try to eliminate them by deploying rational work processes. In the agricultural industry, however, the products are living organisms and therefore some unevenness is unavoidable. That’s why worker regularly verify crop conditions as they go; this approach is more flexible than an industrial approach. Our time spent working in agriculture has taught us that it’s not always best to blindly try to eliminate all waste and unevenness.
I understand that AgriD uses automated harvest robots and other types of robot designed to assist humans in their tasks. How do they make use of automated guided vehicles (AGVs)?
Hosoe: During the busy seasons, AgriD uses up to seven AGVs to transport harvested crops. The farthest parts of the greenhouse are about 300 meters [984 feet] from the cargo shipping area, and based on the picking schedule AGVs fitted with empty racks are dispatched to distant parts of the facility in order to collect the harvests. Worker load boxes filled with picked crops onto these AGVs’ racks, and when a rack is full they send a notification that harvesting has been completed. The AGV then automatically transports the crop-filled shelves to the shipping area, where crops brought in are handled on a first-harvested, first-processed basis—meaning those brought in first are sent out first. This enables smooth operations on the subsequent packaging line.
Sakurai: When an AGV arrives at the shipping area with a rack of products, a scale built into the floor automatically weighs the yield, and based on this information managers can remotely check progress toward their target yield for the day. This ability to quickly check up on progress at any time allows them to end a certain type of work for the day once the target has been reached and send staff onto their next task as necessary, with no wasted time or labor.
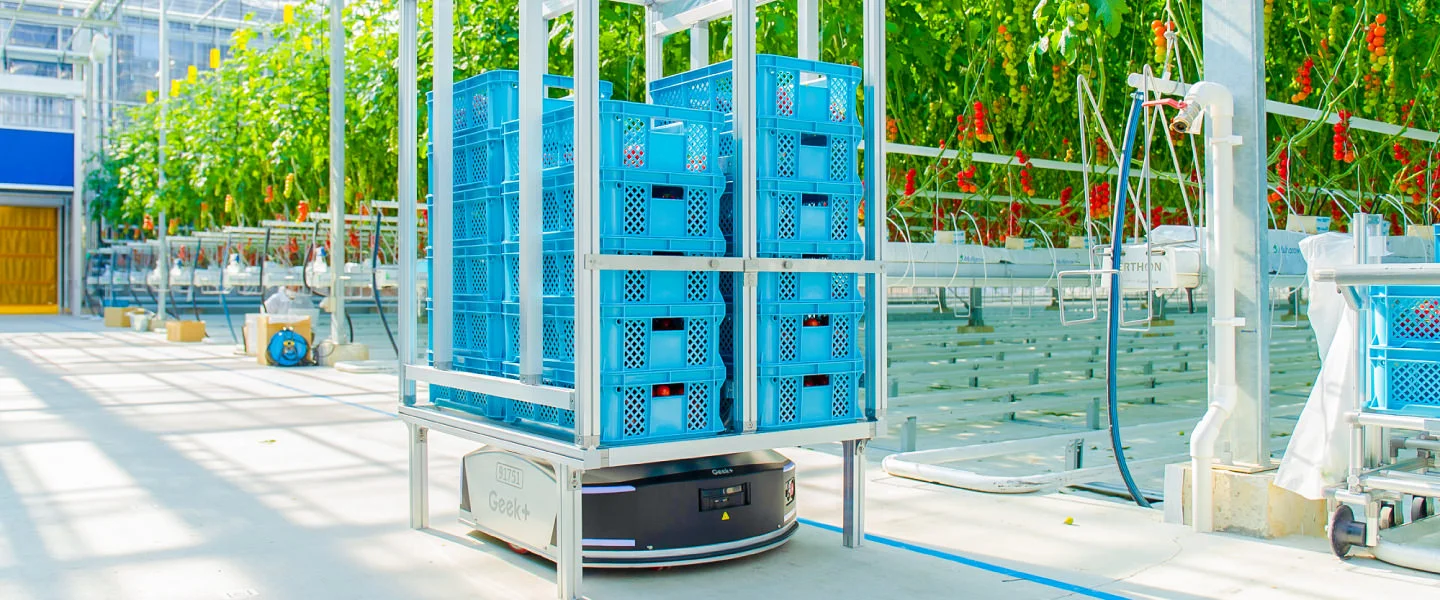
How does AgriD use the work-record data from employees that is collected and stored on their server?
Sakurai: Managers use it to monitor work progress, work speed and other such details. This enables them to assist any employee who is working slower than the others, or to go and check certain sections of plants for problems if irregularities are seen in multiple adjacent rows.
Hosoe: In most cases, this data is used to easily check progress toward operational targets. We are considering adding a new feature that allows managers to provide personalized instructions to individual employees.
The future of agriculture: Human-robot collaboration
Have you noticed any changes as a result of introducing work management systems, AGVs and other such technologies in agricultural work?
Hosoe: A lot of the employees at AgriD are part-time workers. In countries such as the Netherlands, we often see agricultural experts employed in large-scale greenhouse operations, and of course these experts finish their work at an incredibly quick pace. Here in Japan, AgriD staff are also very quick, going head-to-head with the pros from overseas.
That’s pretty impressive! What has proven most effective so far?
Hosoe: I think our kaizen activities which use work results data from the integrated production management system have proven effective. Through this approach, we can confirm unevenness with each employee based on the data, and then check this against actual work and help worker make changes as necessary. This enables us to standardize work more quickly and reliably and better train the staff as a whole, which improves the speed of work.
Moreover, because we can carry out integrated, interlinked control of work management as well as the harvest robot and AGV robots, it’s possible to increase the productivity of growing and harvesting activities as a whole—this is another strength of the approach.
Also, our ability to formulate plans based on actual work helps us reduce production costs. In the past, AgriD’s approach to hiring was, for example, if we could handle things with 20 employees last year, to hire the same number this year. However, with planning based on past work results, the company can understand things in greater detail and determine, based on past data, whether they need to hire two extra staff at a certain time of the year, or will be one worker short at another time. This enables shifts to be assigned based on actual conditions, which has helped them bring down labor costs by around 10 to 20 percent.
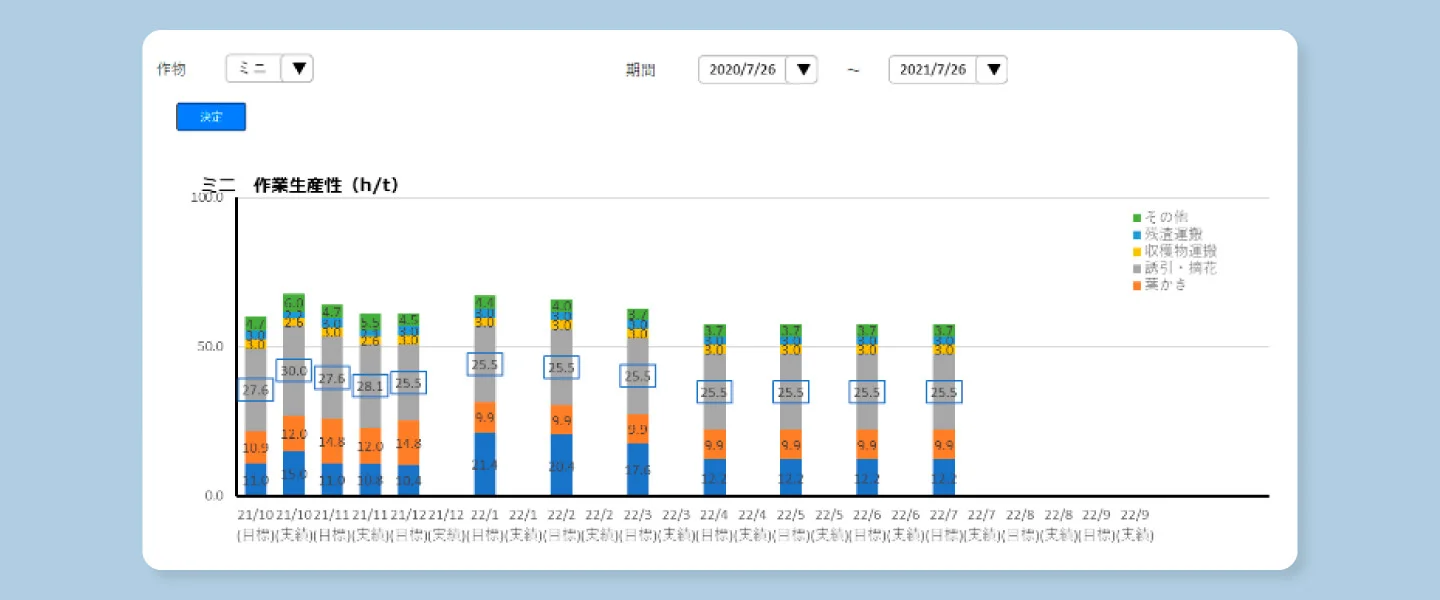
Did any of the staff struggle to use the tablet devices when you introduced them into operations?
Sakurai: Many of the workers have given positive feedback about this change, commenting that tablets are much more convenient than writing things down on paper.
Hosoe: However, some older workers aren’t accustomed to using smartphones and similar devices. In response, we’ve examined feedback from both worker and managers and improved the user interface.
Sakurai: A lot of our effort has been focused on worker training. Asai Nursery has their most experienced worker give demonstrations of how to perform tasks, and videos outlining the basics of these tasks are provided via tablets to help employees learn. This is just one of the ways that we have designed the system for the user.
We don’t simply train worker to carry out tasks discretely in a mechanical manner; rather, we try to foster an understanding of how tomato plants develop and grow throughout the year. This makes employees feel more connected with and personally invested in the crops, and it has inspired an increasing number of workers to share tips they have picked up through their experience.
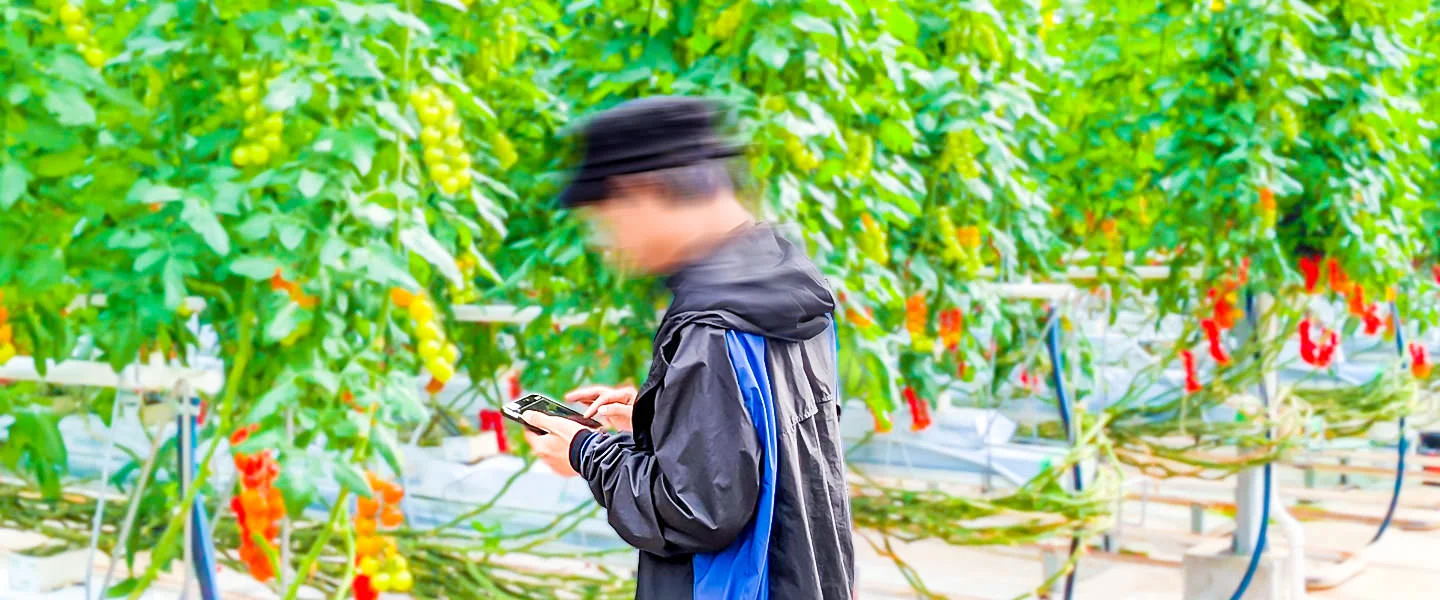
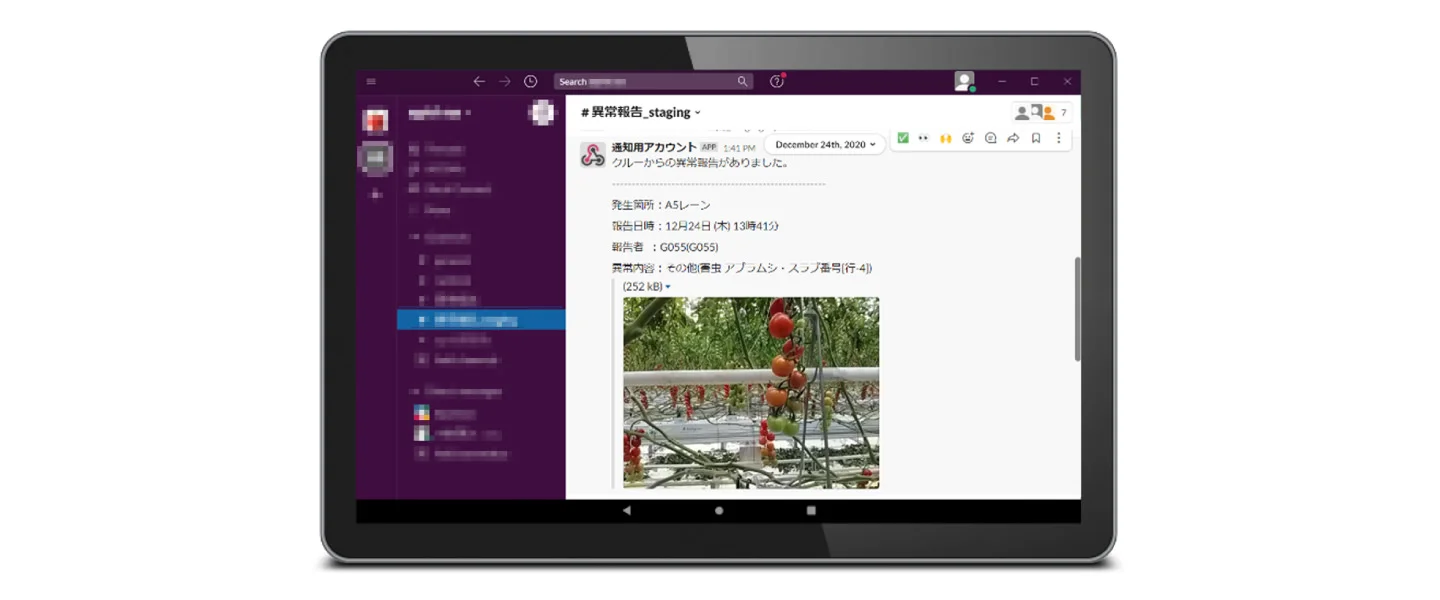
Bottom: the manager can immediately confirm details of the report using the system
You mentioned that standardization of production is a big challenge in agriculture. How was your experience in DENSO useful in agriculture?
Hosoe: The manufacturing industry focuses on the EDER approach, or “Early Detection and Early Resolution,” which entails identifying and solving problems at an early stage, and then giving back to the customer through improvements achieved.
One example is using data on progress toward work goals and so forth to detect problems and irregularities, which can then be addressed and solved quickly. I think this industry-style approach can also be useful in agriculture.
I understand the division you both work for at DENSO initially had nothing to do with agriculture, yet it became involved in collaborating with AgriD. What have you found most interesting about working in agriculture?
Hosoe: I enjoy the fact that we can receive feedback directly from end users and use it to improve our products. We respond to user feedback by applying our own knowledge and experience to develop more standardized, attractive products. As we receive further feedback from users, we continue to make product improvements. I rarely encountered this in the auto industry; it’s been a novel experience for me as a software engineer.
Sakurai: I was previously involved in developing car air conditioning systems at DENSO, but I have always been interested in food and was looking for a way to try working in agriculture. When entering a new field like this, there’s a lot you don’t know or understand at first. I had never even thought about orienting plant-stem directions and the like for tomato plants. This work has been a great opportunity to learn new things at a steady pace, and working cooperatively with multiple companies to create something new has been an invaluable experience.
Above all, I love receiving praise and compliments for my hard work from those working in the agricultural industry. Workers have made comments such as “this used to be hard work, but now it’s much easier” and “I no longer envision myself covered in mud and sweat when I think about farm work.” When you work hard at something for the sake of others and begin to see tangible results, it all feels worthwhile.
DENSO’s website has a wide range of interesting articles on the agricultural industry!
COMMENT
Changing your "Can'ts" into "Cans"
Where Knowledge and People Gather.