Did you find this article helpful for what you want to achieve, learn, or to expand your possibilities? Share your feelings with our editorial team.
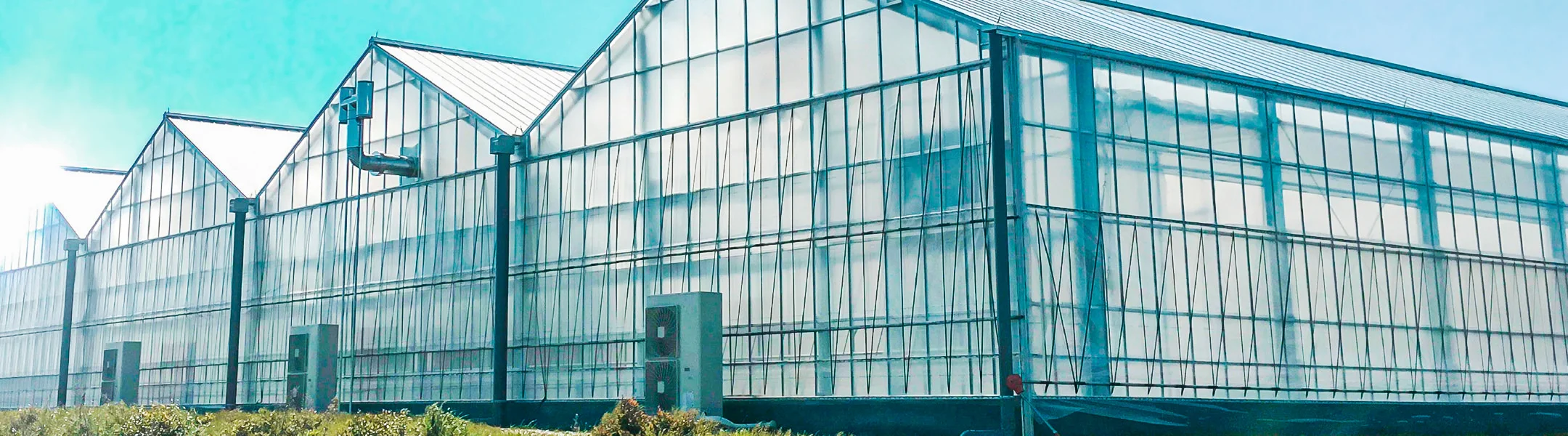
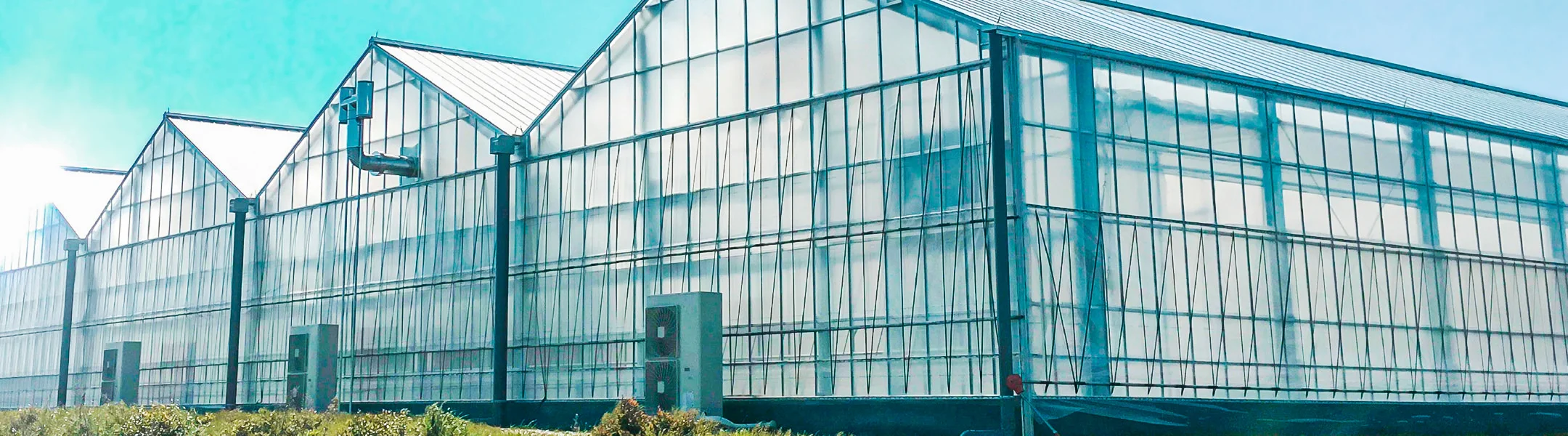
Sep 07, 2022
TECH & DESIGNActive-ventilation greenhouses for a new type of agriculture
Utilizing the Profarm T-cube for agricultural production less affected by the weather
-
Food Value Chain Business Development Div.Hiroshi Tamura
Hiroshi Tamura joined DENSO in 1984. He initially worked in design and development for air conditioning systems on large sightseeing buses. In 2011, Tamura moved to his current division to work in the food and distribution fields. He previously spent time in China, Indonesia, Turkey and other parts of the world searching for new business partners in the field of cold chain systems, and today he is developing and commercializing comprehensive agricultural greenhouse systems.
-
Food Value Chain Business Development Div.Shokichi Hosoe
Shokichi Hosoe joined DENSO in 1997 and majored in software development at an in-house junior college. He was assigned to automobile-engine electronic control unit (ECU) software development, and in 2015 he transferred to the Food Value Chain Business Development Div. Hosoe has taken part in software development for the Integrated Climate Control System integrated environmental control system, Semi-closed Greenhouse active-ventilation agricultural greenhouses, integrated production management systems, automated guided vehicle (AGV) operation management systems and more.
In recent years, global climate change has made agricultural production using current methods increasingly difficult. In order to overcome this social issue, it’s necessary for us to develop technologies that ensure stable crop production. DENSO Corporation has used air conditioning technologies from the automotive industry to develop Semi-closed greenhouses with active-ventilation system without roof windows.
In place of roof windows for natural ventilation, DENSO’s greenhouses use large ventilation fans attached to the gable wall to perform active ventilation based on automated control. This enables stable and reproducible cultivation, not dependent on the prevailing weather, and represents an evolution of agricultural greenhouses utilizing software-based technologies.
Contents of this article
Air conditioning technology: common features between cars and greenhouses
I’m surprised that DENSO, automotive technology company, develops greenhouses. Why did you choose this particular field? Is there some common element between the two industries?
Hiroshi Tamura:In 2011, DENSO started searching for new business fields, and one of those was food. Human beings require food to live, and there is a global need to produce food and deliver it to people everywhere. We thought we could carve out a role for ourselves in the food value chain.
Food production in particular, or agriculture, is an potential area for applying our knowledge. I originally worked for a business unit at DENSO that handled air conditioning technologies and products, where I was involved in designing and developing commercial vehicle AC systems primarily for large sightseeing buses. When I focused on agricultural growing environments, I considered about ways to comprehensively control and adjust the temperature, humidity and CO2 density.
With vehicles, we aim to create environments that are comfortable for human passengers. With crops, we figured we could create climate control system that ensured the optimal growing environment for crops in large greenhouses. That’s why we started developing equipment for controlling the environment in greenhouses.
Agricultural producers are often all called “growers,” but in actual greenhouses come in many different sizes and growers’ needs vary greatly. Which types of growers did you have in mind with this project?
Tamura: Our targets were small- and medium-scale growers. About a decade ago, we saw some real advances in automation technologies on large-scale greenhouses of over a hectare in size, but small- and medium-scale growers could not easily use these technologies. When we talked with the growers, a lot of them said they wanted automation technologies so they could take more time off work, and they also wanted to produce more efficiently.
The large greenhouses I mentioned used climate control system imported from the Netherlands, which is a global leader in agriculture. Such system is designed specifically for large-scale greenhouses and is extremely expensive. Medium- and small-scale growers, however, felt such system was too difficult to control and operate, and did not think introducing it was realistic.
Therefore, DENSO wanted to develop and sell new types of automation system at lower price points which smaller greenhouses could afford and use easily. Through these products, we hoped to make automation more widespread in Japanese farming and help evolve the industry.
We started out by developing climate control system for tomato production. It might be considered that crops like strawberries or melons would be more profitable, but those crops are difficult to grow year-round. Furthermore, in horticulture, roughly 80 percent of facilities using climate control system are growing tomatoes. So we focused on this crop, which offers stable, year-round production and consistent market demand.
But DENSO didn’t have any experience or knowledge in agriculture, right?
Tamura: Well, when we looked into regions of Japan where horticulture was most profitable, we found that Toyohashi City in Aichi Prefecture, which is close to DENSO’s head office, is a leading area. So we asked a Toyohashi-based nursery company to teach us about the growing conditions necessary for tomato production and then set out to develop the hardware and software for the climate control system. Then, we integrated information on optimal sunlight amounts for leaves into the climate control system software to optimize the photosynthesis process, which is vital for ensuring photosynthesis.
Through sustained R&D, we were able to commercialize our idea in 2015 as the Integrated Climate Control System. With this system, sensors installed both inside and outside of the greenhouse are used to control greenhouse roof windows and side-wall windows, curtains, heaters, heat pumps, CO2 production equipment, mist devices, circulation fans and other such equipment to create an ideal cultivation environment.
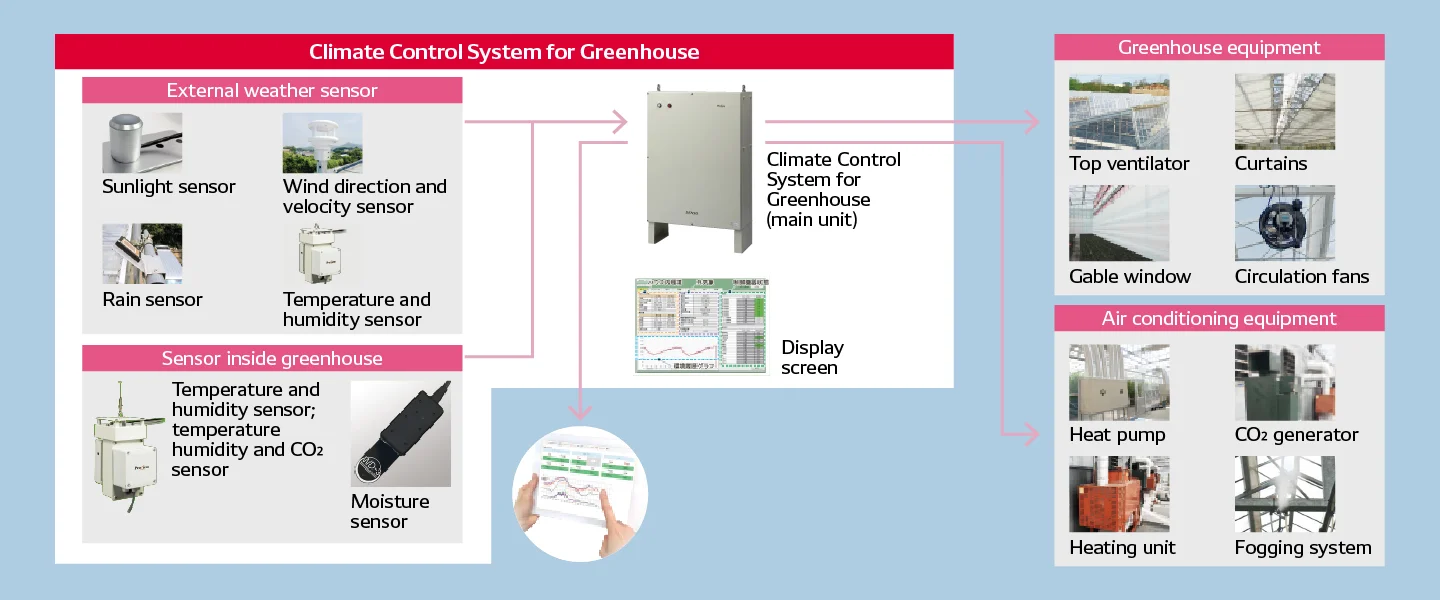
Tamura: After finishing the Integrated Climate Control System, we got to work creating our next product, the Semi-closed Greenhouse with active-ventilation system, which can control airflow throughout the entire greenhouse.
Why did you add active-ventilation feature to greenhouses?
Tamura: Standard-type greenhouses have numerous roof windows to enable natural ventilation. During the summer, these windows are opened when the grower wants to lower the temperature inside the greenhouse. However, depending on the wind speed and direction, this approach sometimes cannot cool the facility.
Rather than this passive approach with natural ventilation, DENSO’s system uses active circulation via large ventilation fans installed on the gable wall to ensure airflow patterns that maintain optimal temperatures inside the greenhouse. This setup has various other benefits as well. It does not have a roof window, which eliminates the need for machinery at high locations used to open and close the windows. The design also prevents crops from getting wet in the rain and eliminates the need to install nets to keep out pests, while also avoiding maintenance work at high locations.
During development, I carried out airflow analyses using greenhouse models and found that we could eliminate the roof window and optimize large gable ventilation fans to achieve good ventilation throughout the facility. Although other types of greenhouses in horticulture have their own ventilation control techniques, DENSO was the first to try building an in-facility environmental control system that both eliminates roof windows and uses ventilation fans alone to control airflow.
Could you describe the types of large ventilation fans that you use for the Semi-closed Greenhouse?
Tamura: Each greenhouse has a gable frontage of 8 meters across, an post height of 3.5 meters and a width of 50 meters. For each greenhouse, we install three ventilation fans each with a diameter of 1 meter on the gable of the building. These three large fans together move a whopping 77,000 cubic meters or so of air each hour through the Semi-closed Greenhouse growing environment, and temperature and humidity sensor data is used to optimize the number of fans used at any given time.
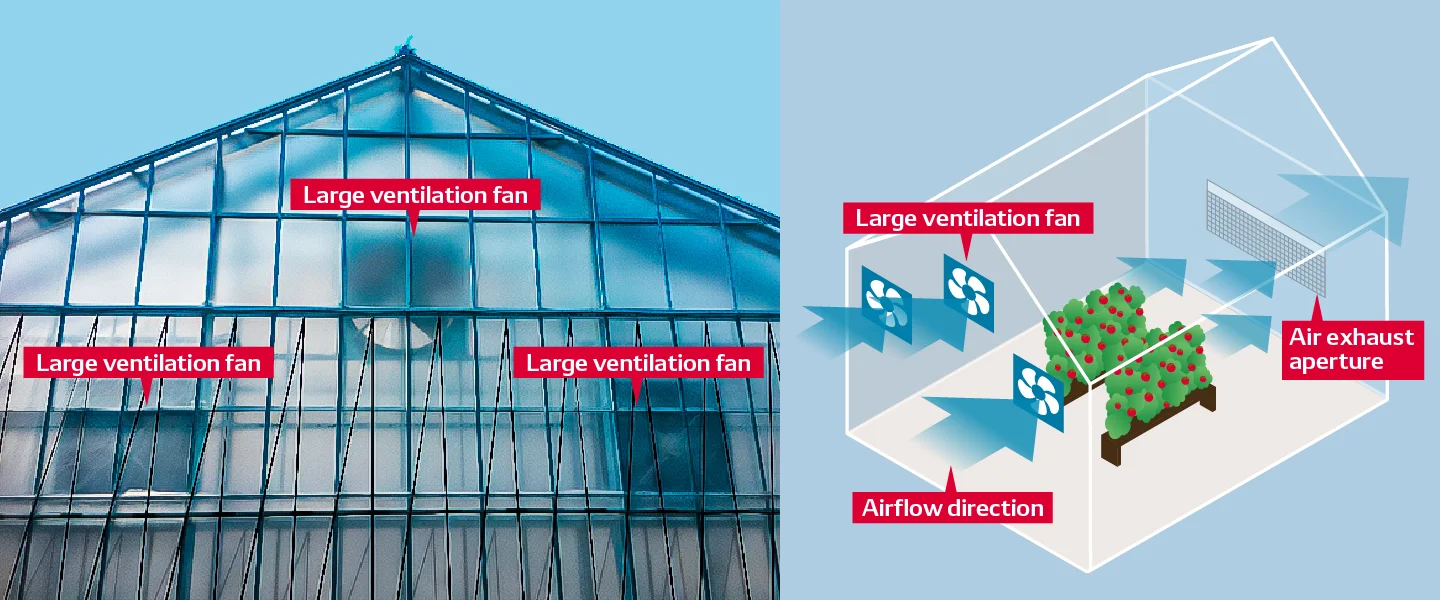
Right: A diagram showing active ventilation operations within the greenhouse.
Differences between automotive and agricultural development processes
Is the development process for climate control system for agriculture different from that for automotive products?
Shokichi Hosoe: Agricultural and industrial manufacturing have some major differences, which gave us a lot of trouble.
What was different?
Hosoe: Greenhouses are manufactured in differing sizes and shapes depending on the needs of individual growers, and the inside environment varies from greenhouse to greenhouse. In industrial manufacturing, there is a very strong tendency to pursue standardization in production. We want to establish firm standards, create specifications based on those, and then carry out mass production to make products with consistent forms and quality levels. This approach also enables us to use data from an existing product as a basis for making other products later on. Therefore, when DENSO first began working on greenhouses, we started by working on visualization of information and achieving standardization.
We started out by using an in-house greenhouse designed for R&D, equipping it with numerous sensors to measure temperature, humidity, CO2 density, sunlight amount, wind speed, moisture level, and more. With temperature and humidity measurements, we divided the greenhouse interior space into nine horizontal sections and three vertical height levels, and distributed 27 sensors among these.
Using this approach, we were able to generate visualizations of changes in temperature and humidity levels within the greenhouse when large ventilation fans were in operation. Then, based on these measurements, we worked on standardizing equipment and sensor installation positions so that the Semi-closed Greenhouse system could be prevailed in various regions throughout Japan and still realize the same interior growing environment.
More stable climate control for improved productivity
Did these changes affect crop yields?
Tamura: Under normal circumstances, yield is significantly affected by weather conditions, diseases, pest outbreaks and other such factors, making it hard to quantify yield in any general manner. By using active ventilation for airflow control, however, it’s possible to create an environment where production volumes can be increased easily.
One common problem encountered in tomato cultivation is the accumulation of humidity caused by poor ventilation, which helps pests to proliferate. We have seen that active ventilation improves ventilation and thus minimizes the types of air conditions that lead to pest damage. Furthermore, by maintaining uniform temperatures throughout the greenhouse while providing constant air movement to promote photosynthesis, our system fosters an environment that makes it easier to increase production output.
Does the system offer any other advantages in terms of the greenhouse building structure itself?
Tamura: Because existing greenhouses use a roof window that opens and closes. The Semi-closed Greenhouse has no need for opening and closing mechanisms—which themselves actually block sunlight—and as a result the plants inside our greenhouses receive approximately four percent more light. Increasing the sunlight is key to promoting healthy photosynthesis, and can boost yields.
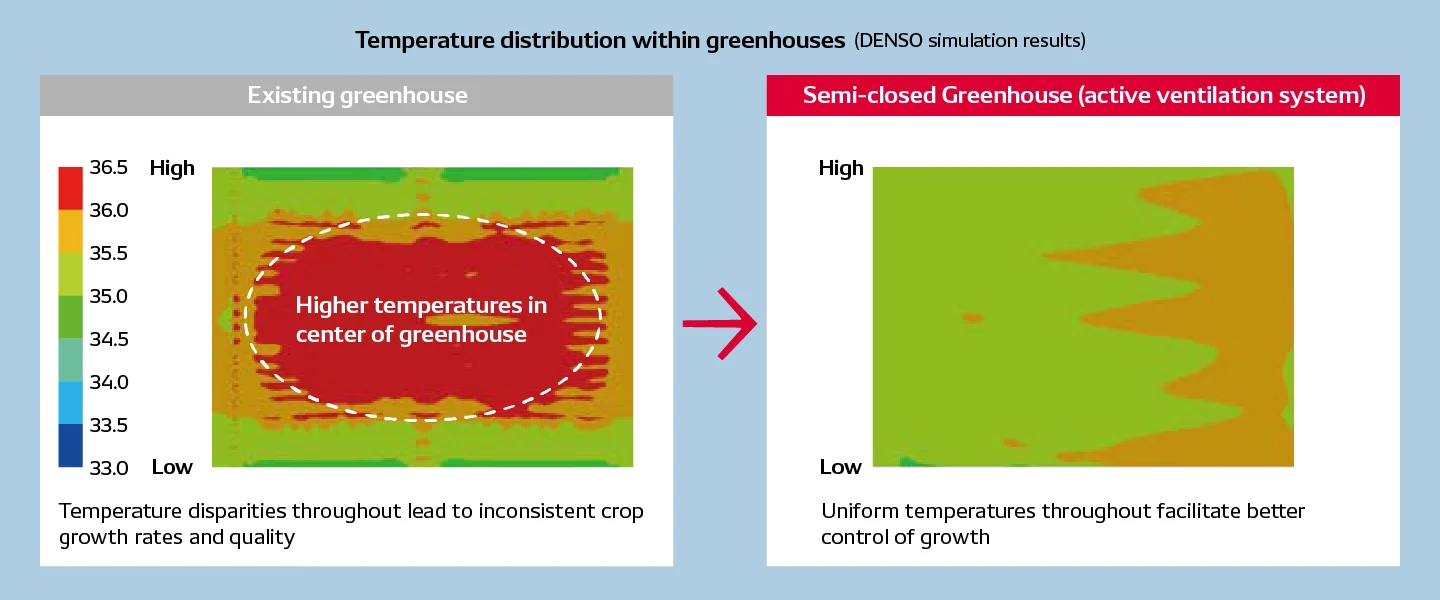
Hosoe: In addition to active-ventilation fans, the Semi-closed Greenhouse is equipped with mist generating equipment. Mist devices are generally used to manage stoma conditions for crops by adjusting humidity levels, but with our system this equipment works alongside airflow control to collect the heat resulting from vaporization, which lowers the temperature inside the greenhouse. This, in turn, can help lower the wet-bulb globe temperature, or WBGT, and make the environment more comfortable for growers to work.
Tamura: Some growers who worked with us on developing Semi-closed Greenhouse mentioned that the system provides more stable, consistent temperatures even during summer, along with better yields. They also told us that there seemed to be fewer pests. These are all examples of real-world improvements seen by growers in the field.
Could you explain the structural design advantages of the Semi-closed Greenhouse?
Tamura: One advantage of the Semi-closed Greenhouse’s structural design is its use of standardized functional and performance specifications, in contrast to current greenhouses which are made to order for each customer. By enabling the growing area to be expanded by adding new greenhouse units while incorporating standardization approaches into the product, we allow customers to decide on greenhouse specifications from the initial construction stage without confusion or worry.
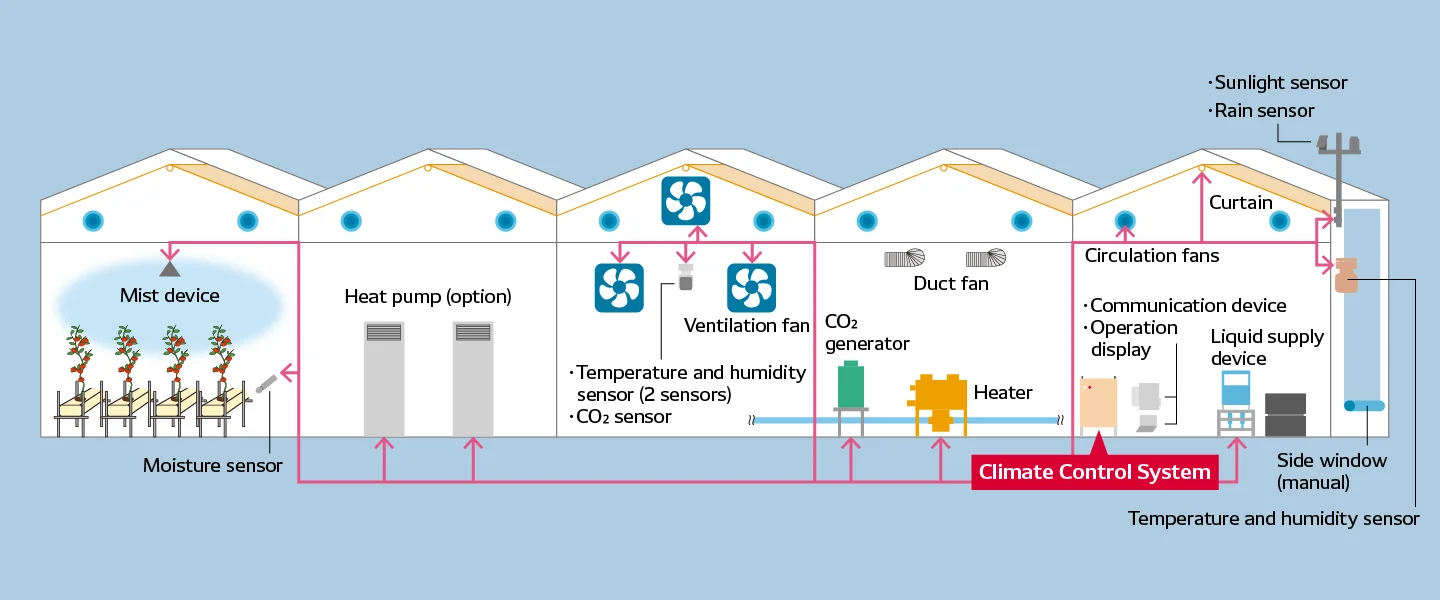
Do you plan to further develop and improve the Semi-closed Greenhouse?
Tamura: We want to promote and expand the scope of Semi-closed Greenhouse usage in small- and medium-scale greenhouse. It may prove useful for agricultural production in hot regions where roof-window ventilation is insufficient for greenhouse cultivation. In addition to growers in Japan, we hope to serve potential customers in other parts of Asia and beyond.
Our goal is to evolve greenhouses to provide better temperature and humidity control with as few hardware additions and changes as possible, all in line with local needs.
In other words, this is a software-driven evolution of the greenhouse?
Tamura: Growing environments as well as crop types and varieties vary from region to region. By providing greenhouses that offer ideal growing environments and minimize production failures, we think we can make life better for growers everywhere. From a business standpoint, there are great benefits of a framework that uses existing hardware but improves the software functions by using information to achieve optimal crop-growing environments.
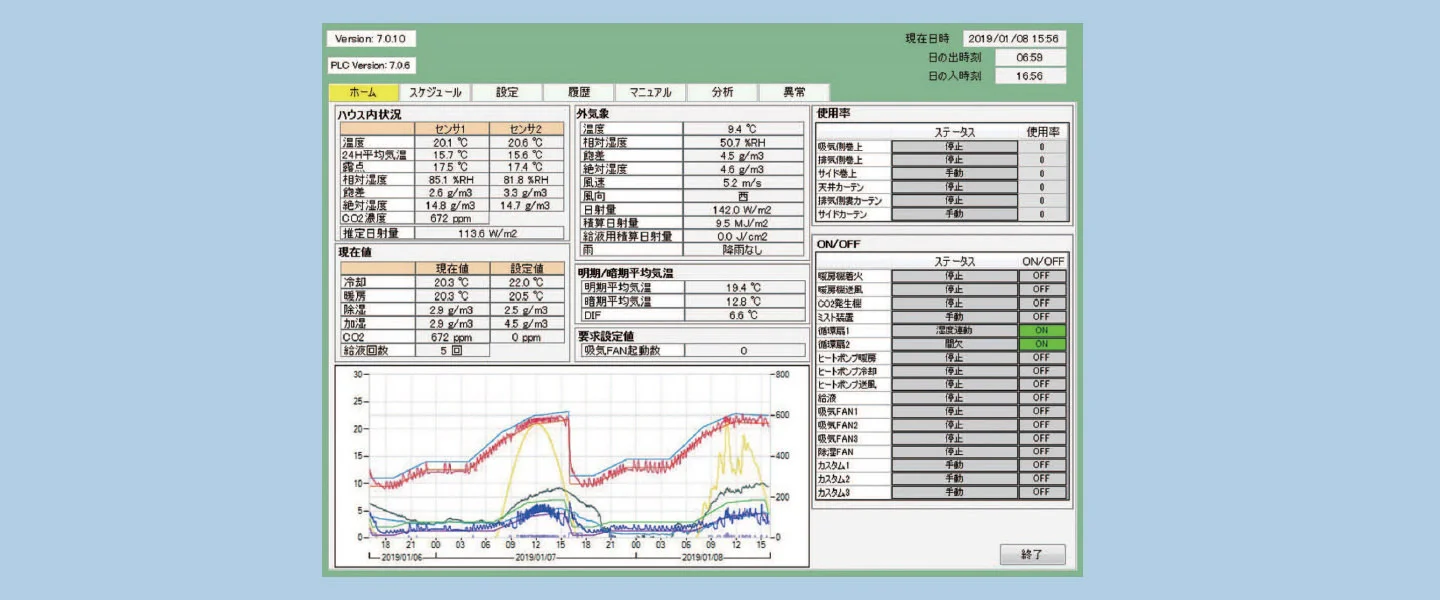
What are your impressions so far regarding your experience in agriculture?
Tamura: With tomato growing, I learned that using smaller amounts of water and temporarily lowering the temperature at night increases the sugar content in the fruit and makes the final product sweeter. I also found that bees like to fly around in greenhouses in order to pollinate.
I discovered all this by working in agriculture, and by exposing myself to a new field like this, I keep coming up with new ideas for ways to apply our technologies. There’s still a lot of potential waiting to be discovered—it’s been a truly fascinating experience.
I’m sure there are many more great things to come!
Hosoe: In addition to the Semi-closed Greenhouse, DENSO is pursuing other verification tests and experiments in areas such as large-scale smart greenhouses. I think we can apply the technologies and knowledge built up at our company over the years to make meaningful contributions in the agricultural industry.
We are currently carrying out tests on introducing the harvest robot into farming operations. By bringing together agricultural and industrial approaches, I think we can come up with many more useful technologies to please our customers.
DENSO’s website has a wide range of interesting articles on the agricultural industry!
COMMENT
Changing your "Can'ts" into "Cans"
Where Knowledge and People Gather.