あなたが実現したいこと、学びたいこと、可能性を広げたいことに、この記事は役に立ちましたか?
ぜひ感じたことを編集部とシェアしてください。
カーボンニュートラルの実現のためには、水素をうまく利活用しなければなりません。水素の中でも、再生可能エネルギーから生成されるグリーン水素を効率よく作り、その水素を適切に活用することが求められています。
デンソーでは、効率よく水素を作り出すための次世代の水電解装置「SOEC(Solid Oxide Electrolysis Cell / 固体酸化物形水電解)」を開発しています。カーボンニュートラルに貢献するために、SOECの消費電力を削減することで水素製造の効率向上に挑戦しています。
この記事の目次
SOECとはなにか? 電解効率が最も高い水電解の仕組み
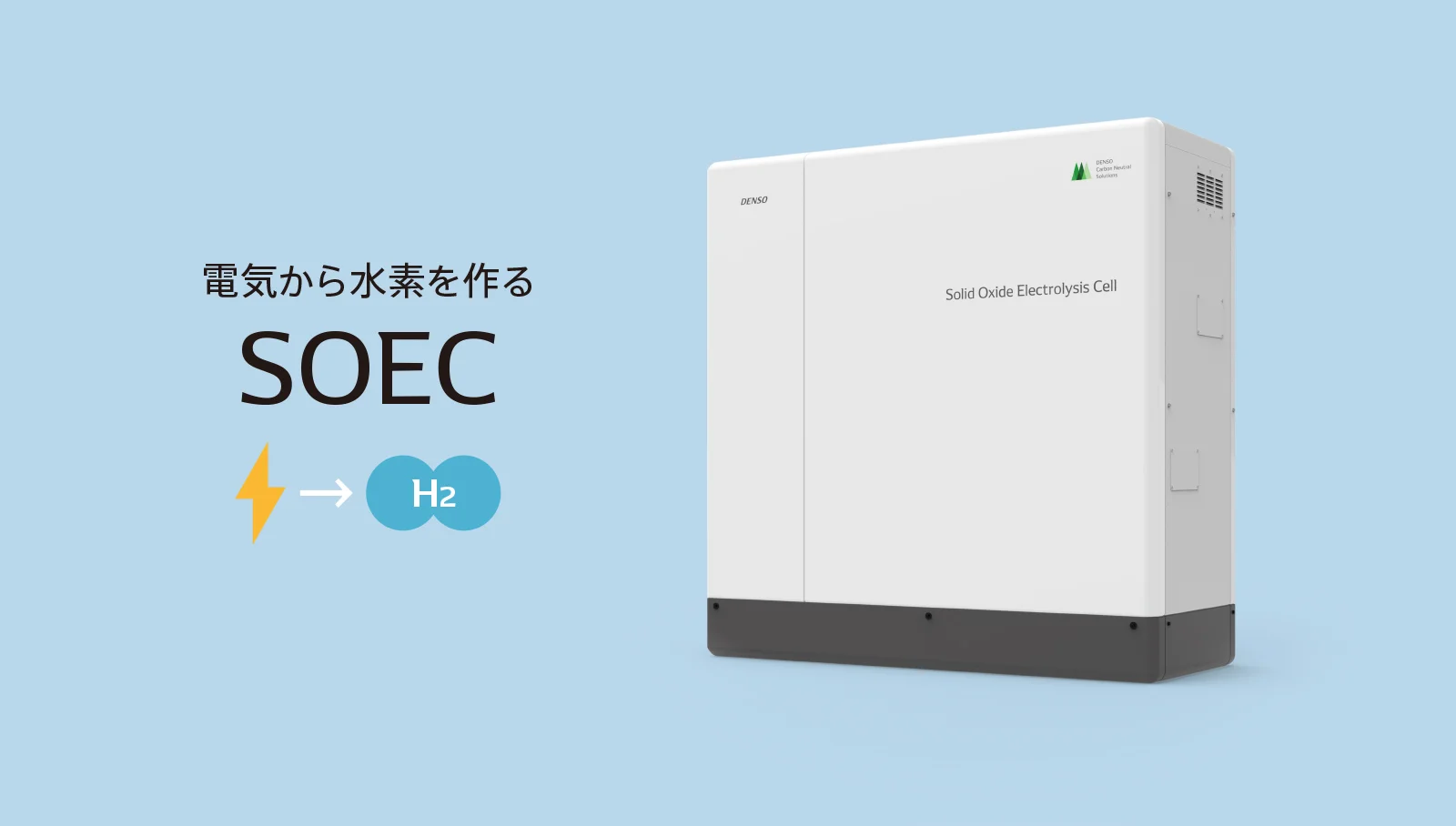
水から水素を作り出す水電解の方法には、アルカリ型、PEM(高分子膜)型など、いくつかの種類があります。
水は高温になるほど低い電圧で分解できる性質があります。そのため、60℃前後で反応するアルカリ型やPEM型と違い、約700℃という高温で動くSOECは水素を作り出すために必要な電力量が少なくなります。
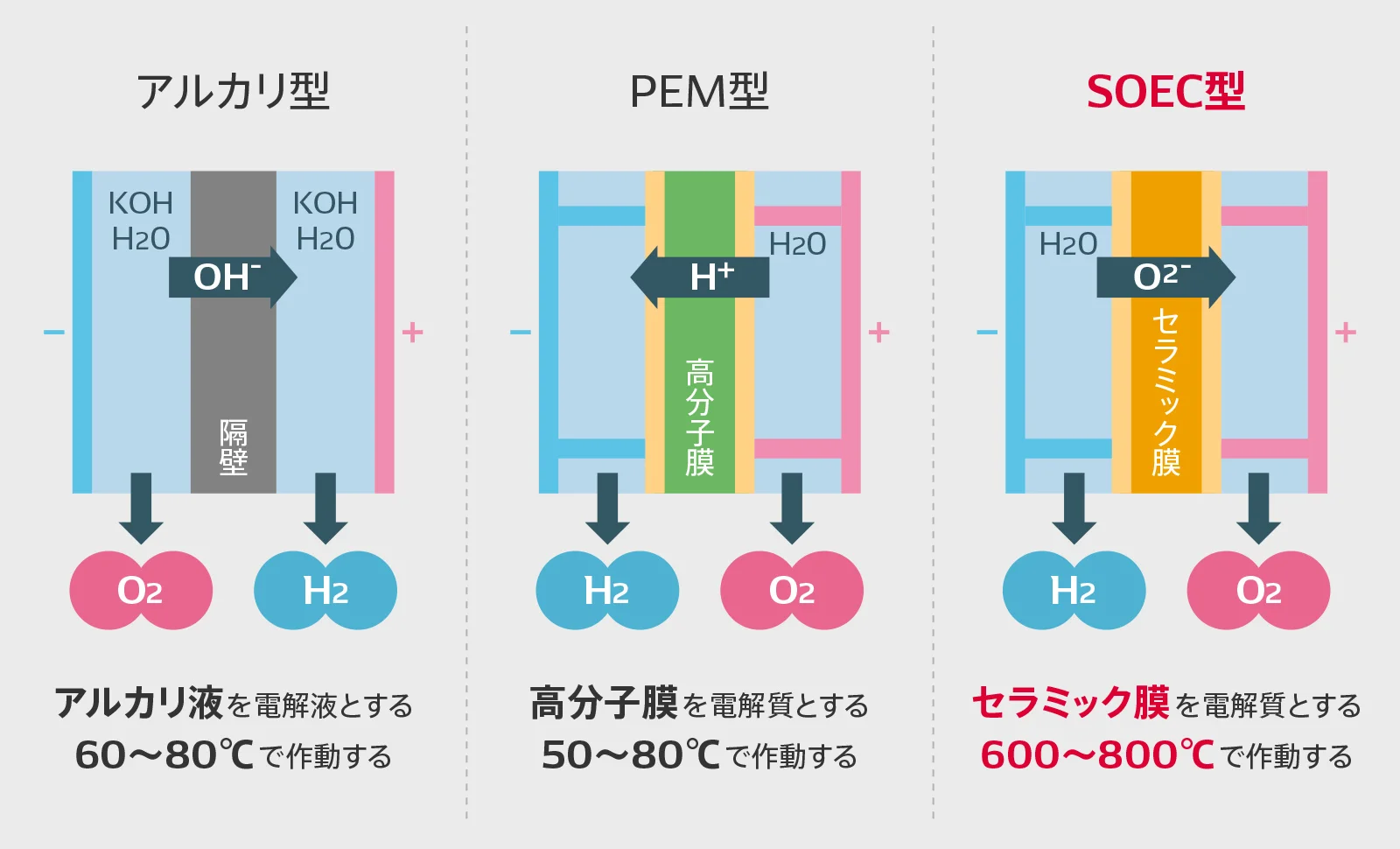
プラスチックや金属などの素材では700℃という高温に耐えられないため、SOECには素材としてセラミックが用いられます。SOECでは、セラミックを使って燃料極、電解質膜、空気極の3層からなる「セル」を作り、さらにセルを積み重ねて「セルスタック」を作ります。
このセルスタックを、断熱材で覆われた高い温度に保つための機器「ホットモジュール」に入れ、そこに700℃の高温となった水蒸気を送り込んで電気分解を行うのがSOECの仕組みです。
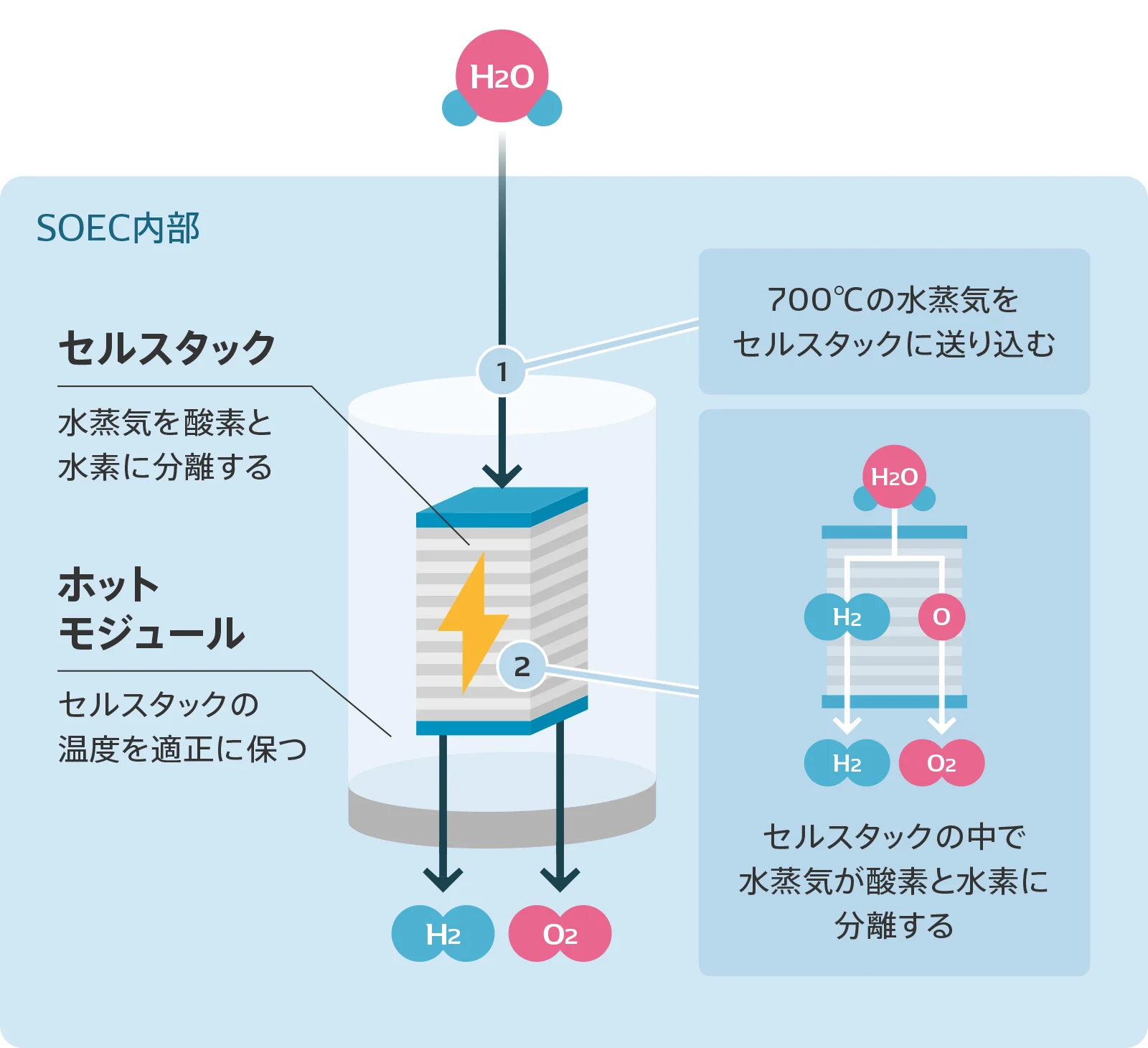
SOECは、次世代の水電解装置として期待が寄せられているシステムです。なぜなら、低炭素電力が常に供給される環境や排熱が利用できる環境では、低温で水電解する方式と比較して、原理的に水素製造の効率が高いためです。しかし、技術的なハードルが高く、まだ広く普及するには至っていません。デンソーは、培ってきた技術を活かし、SOECの技術課題の解決に取り組んでいます。
SOECの課題を乗り越えるための熱マネジメントとシステム化の技術
水素の利活用を広めていくための課題のひとつが、少しのエネルギーで効率的にグリーン水素を製造できるようになること。SOECの場合、グリーン水素を製造するために必要な再生可能エネルギーの消費電力量をいかに減らすかが課題です。環境ニュートラルシステム開発部の中島敦士はデンソーの開発方針について、このように語ります。
「私たちは、グリーン水素の製造効率を上げることが、水素の利活用を広げるための重要なポイントのひとつだと考えています。製造効率が上がれば、グリーン水素のコストが下がる。すると、水素活用の需要拡大につながり、カーボンニュートラルな社会に近づいていくでしょう。
SOECは、現在主流となっている水電解の方法に比べて電解効率が優れているとはいえ、消費電力量を増やしてしまう要因がいくつか存在しており、本来のポテンシャルの発揮を妨げています。モビリティの製品開発で培ってきた独自の技術を活用し、SOECの消費電力量を極限まで減らすという挑戦を通じて、グリーン水素製造の効率向上に貢献したいと考えています」(中島)
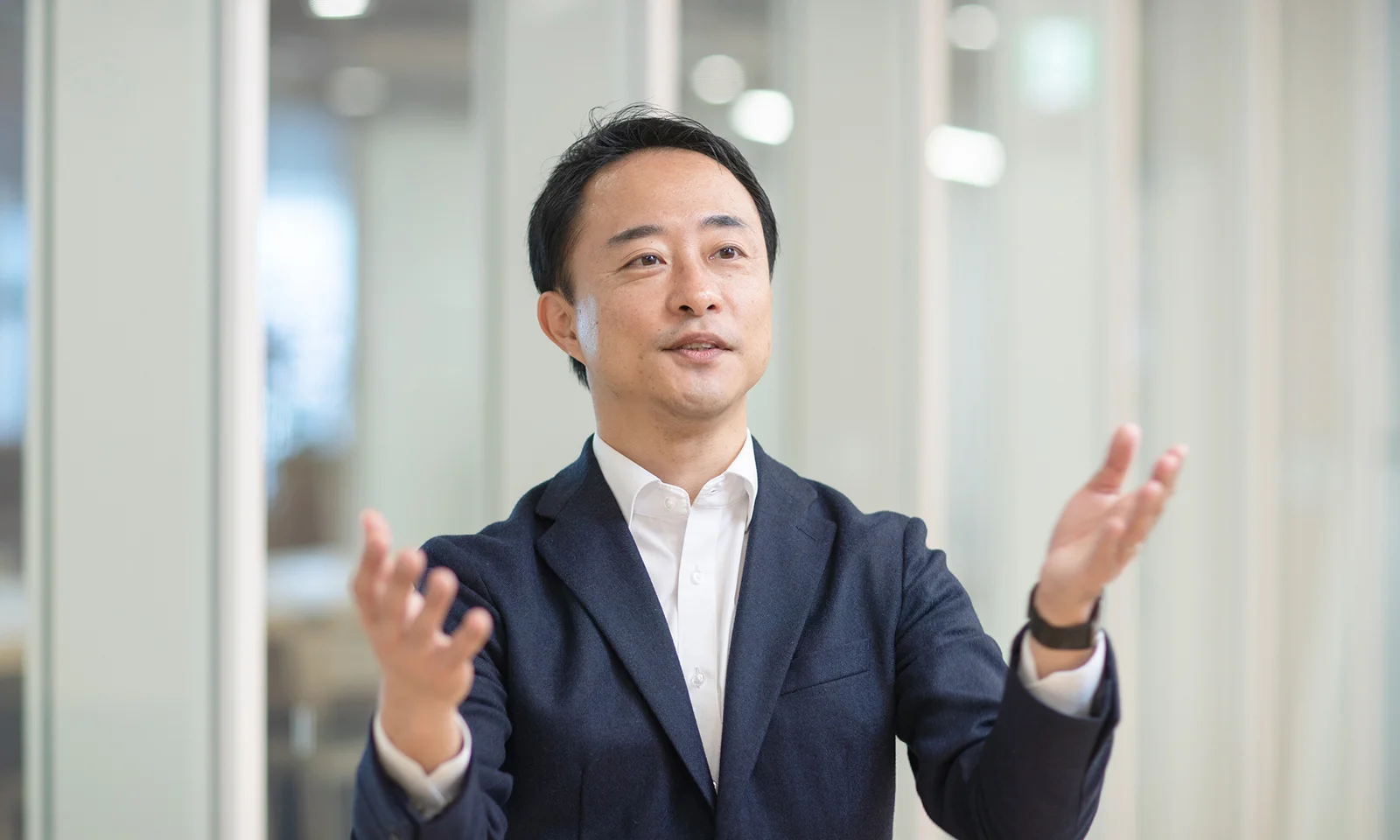
まず、SOECの課題として挙げられるのが熱の扱い方。ホットモジュールの700℃という高温を維持しようとすると、周囲との温度差から放熱が起こりやすく、放熱分を追加で加熱するとなるとエネルギーが余分にかかってしまいます。また、ホットモジュールに送り込んだ水蒸気は、すべてが水素の製造に活用できるわけではなく、未反応のまま放出されてしまうこともあります。そうすると、水蒸気にするための熱エネルギーが無駄になってしまい、効率が下がってしまいます。
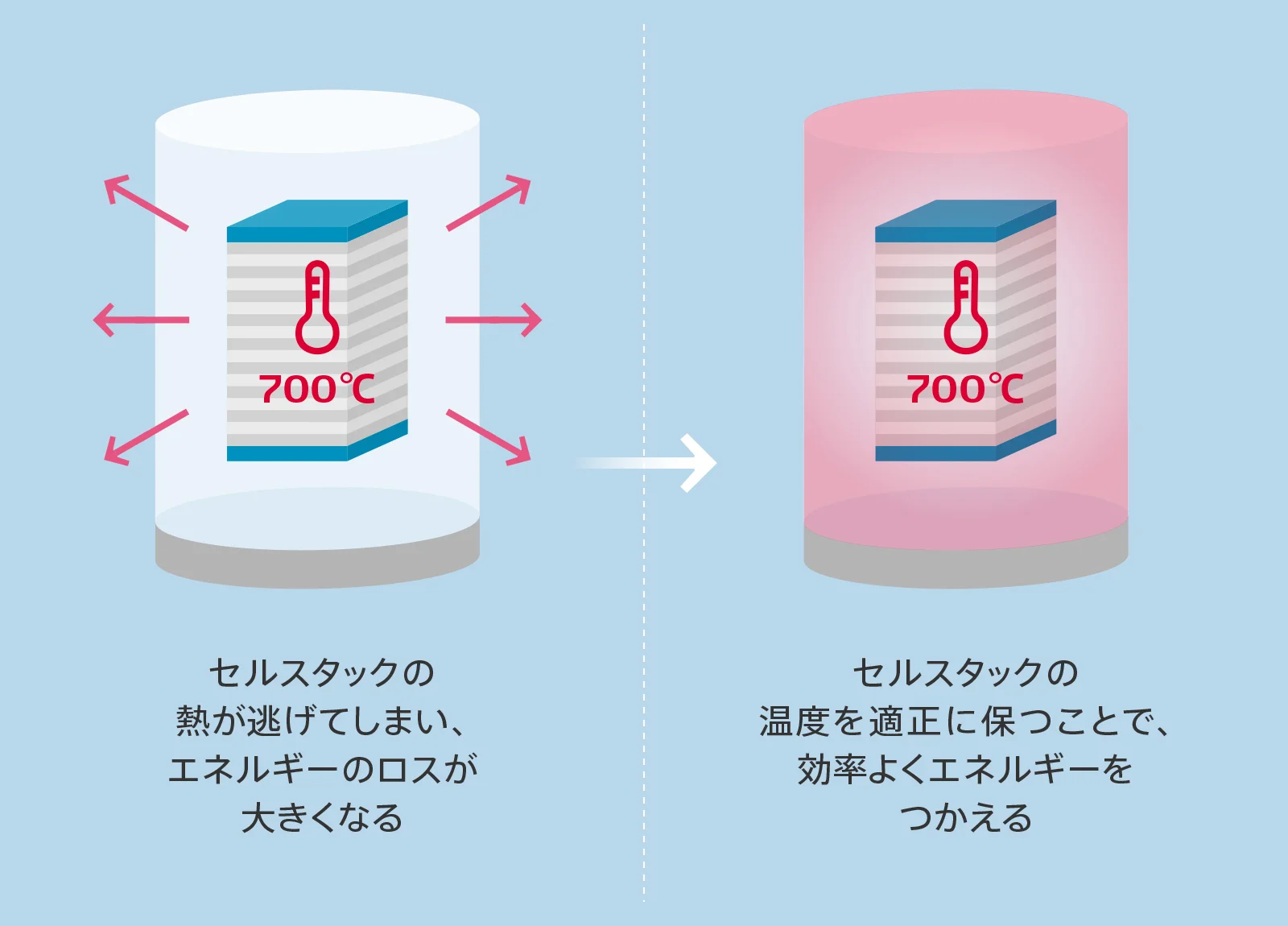
デンソーでは、これらのSOECの課題を解決するために、モビリティ製品開発で培った技術を応用して技術開発に取り組んでいます。
まず、ホットモジュールの放熱量を低減するために、装置内の排熱を回収して利用できるようにしています。
そのために、車載用熱交換器の技術をベースとして、熱交換器表面からの放熱を抑えながら効率よく排熱を回収できる構造を実現。ホットモジュールの開発に関わる環境ニュートラルシステム開発部の渡邊晴彦は、SOECの技術的な難しさについて、こう語ります。
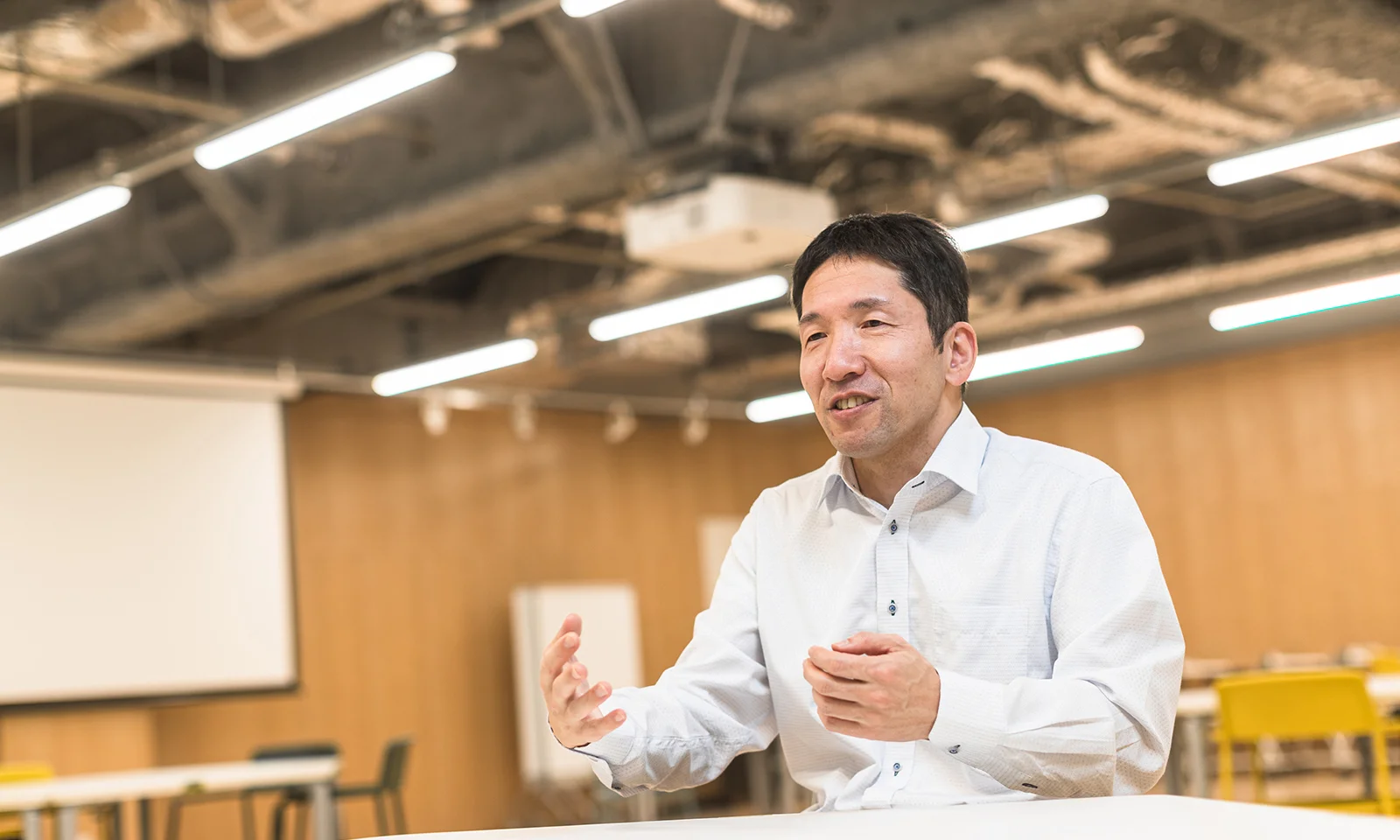
「セルスタックを適正な温度に保てないと、電解効率が下がって生み出す水素の量が減ってしまいます。それだけでなく、ホットモジュール内で熱の伝わり方にばらつきが生じると、セルスタックの稼働にもばらつきが生じてしまい、やはり効率は下がってしまいます。
熱をコントロールするだけでなく、適正な温度に保たなければいけませんが、熱は熱い方から冷たい方へと移動するので、熱を回収して再利用しようとすると温度勾配が発生します。相反する課題をうまくバランスさせながら解決するのが技術的に難しい。自動車の部品開発で培ってきた熱流体の技術や熱流体のシミュレーション技術などを活かして乗り越えるべく、開発に取り組んでいます」(渡邊)
また、未反応水蒸気を排出してしまうことによるエネルギーロスの課題を解決するために、デンソーのSOECではエジェクターを活用したシステムを構成しています。エジェクターとは、ポンプなどの機械的駆動に頼らずに、高圧の流体のエネルギーを活用して、低圧の流体を吸い込み、排出することができる装置です。
SOECでは、水素と酸素に分解されず排出されてしまった水蒸気を回収して、再度セルスタックに循環させる役割を担っています。
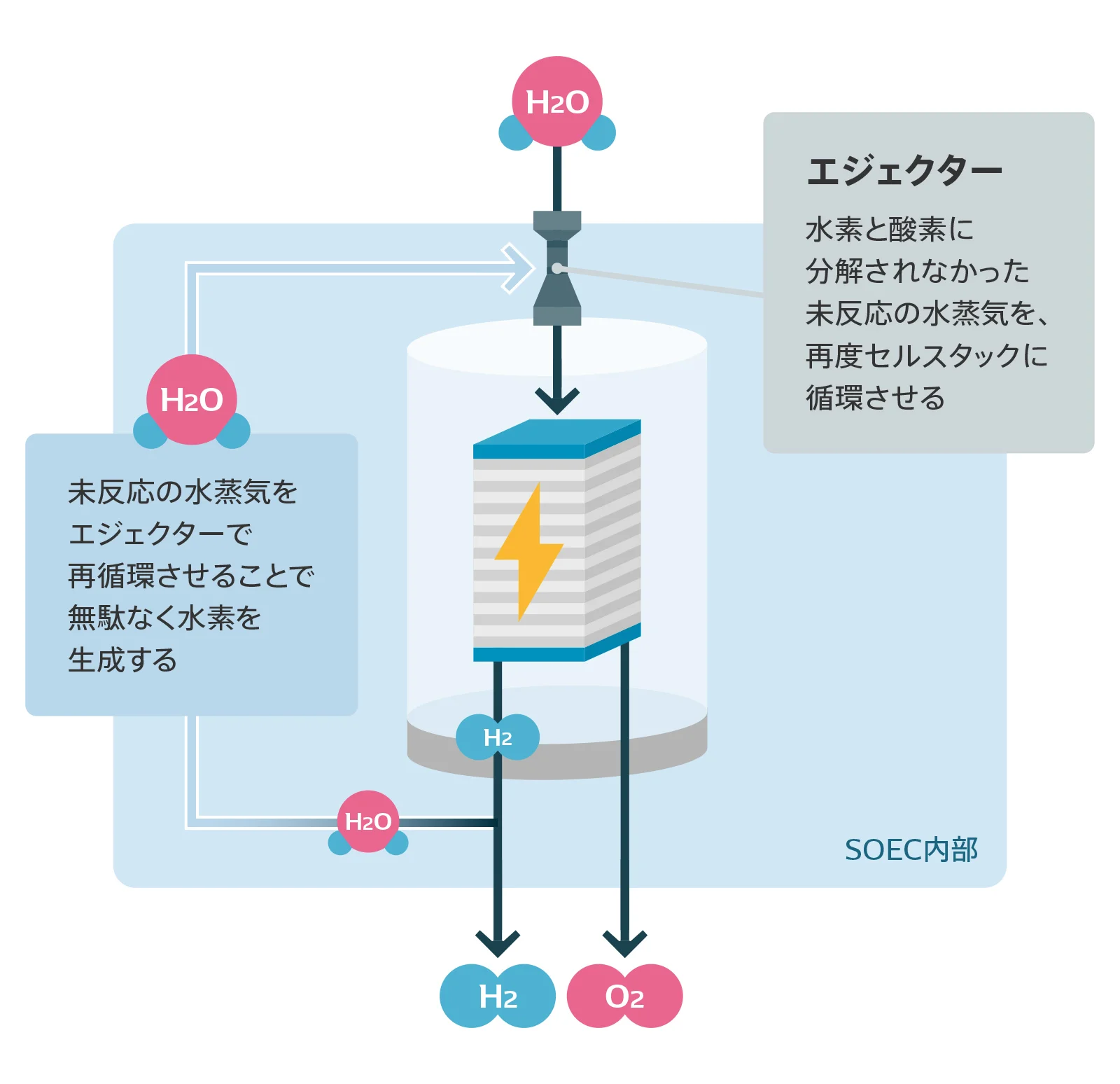
「デンソーのエジェクターをSOECに利用すると、未反応水蒸気のリサイクルができるだけでなく、必要な動力も節約できるため、電解効率を高めることができます。既製品のポンプで水蒸気のリサイクルを実現しようとすると、動力が多く必要となります。それだけでなく、高温で長時間作動できるポンプはまだ存在しておらず、頻繁に交換が必要になるため、メンテナンスコストが高くなります。デンソーのエジェクターは高温に強い上に、使用部品が少なく、壊れにくい。結果、SOECのコアな部品の寿命が延び、メンテナンスコストが下がると考えられます。
また、とにかく水蒸気を多く回収し循環させれば、セルスタックの効率を最大限発揮できるわけではなく、最適な水蒸気の『循環率』があります。これはセルスタックのことが詳細にわかっていないと設計できません。ホットモジュールと同様に、セルスタックも社内で一貫して開発を手掛けているからこそ、デンソーのSOECは効率を最大化できます」(渡邊)
こういった技術の強みを最大限活かすことができるのは、ホットモジュールやセルスタックなどのコア部品を社内で開発し、さらにそれらをひとつの製品として最適な形でシステム設計をすることができるからだ、と渡邊は言います。
「一般的なSOECでは、ホットモジュールとセルスタックを別々で開発したり、外部から調達して組み上げたりするケースが多いですが、デンソーでは一体のシステムとして一貫して社内で開発を進めています。
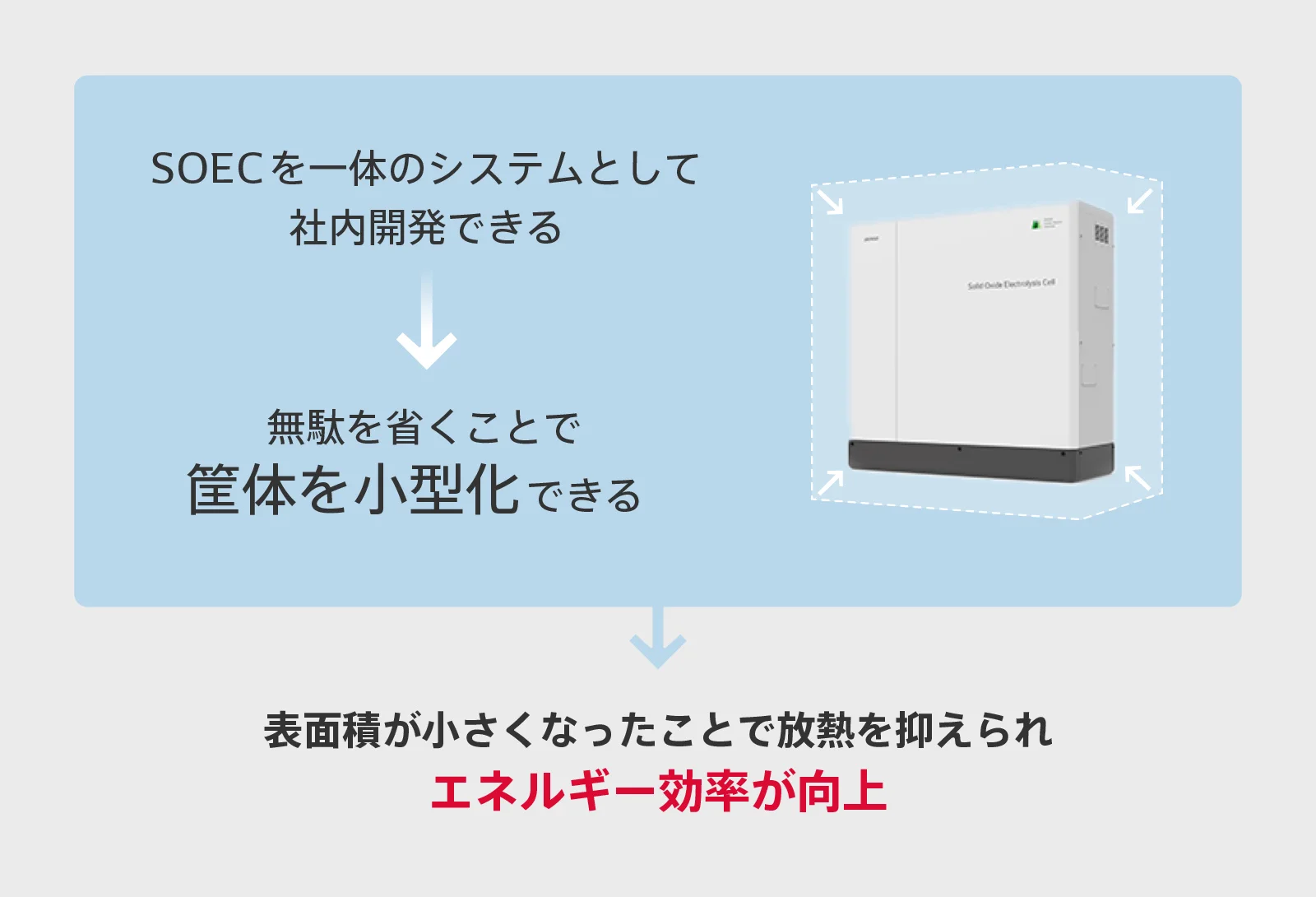
そうすることで、機能的に重複するものを統合して、無駄な部分をどんどん削り、筐体をコンパクトにできます。全体の表面積が小さくなると、熱が逃げにくくなるので、エネルギーを無駄にせず、消費電力をさらに減らせます。
このように、個別の部品や、技術の特性を理解しながら、ひとつの製品として最適に設計することができるのが、デンソーのシステム化技術の強みです。この強みがあるからこそ、性能面でのブレイクスルーを起こすことができます」(渡邊)
SOECのセルを磨き上げる、デンソーの生産技術と先端技術
セル自体の開発を行う先端技術もデンソーの強みです。セルの中で反応が起こり、燃料極から空気極へとイオンが移動する際、電気抵抗と同じ仕組みで距離に応じて電力損失が増加してしまいます。
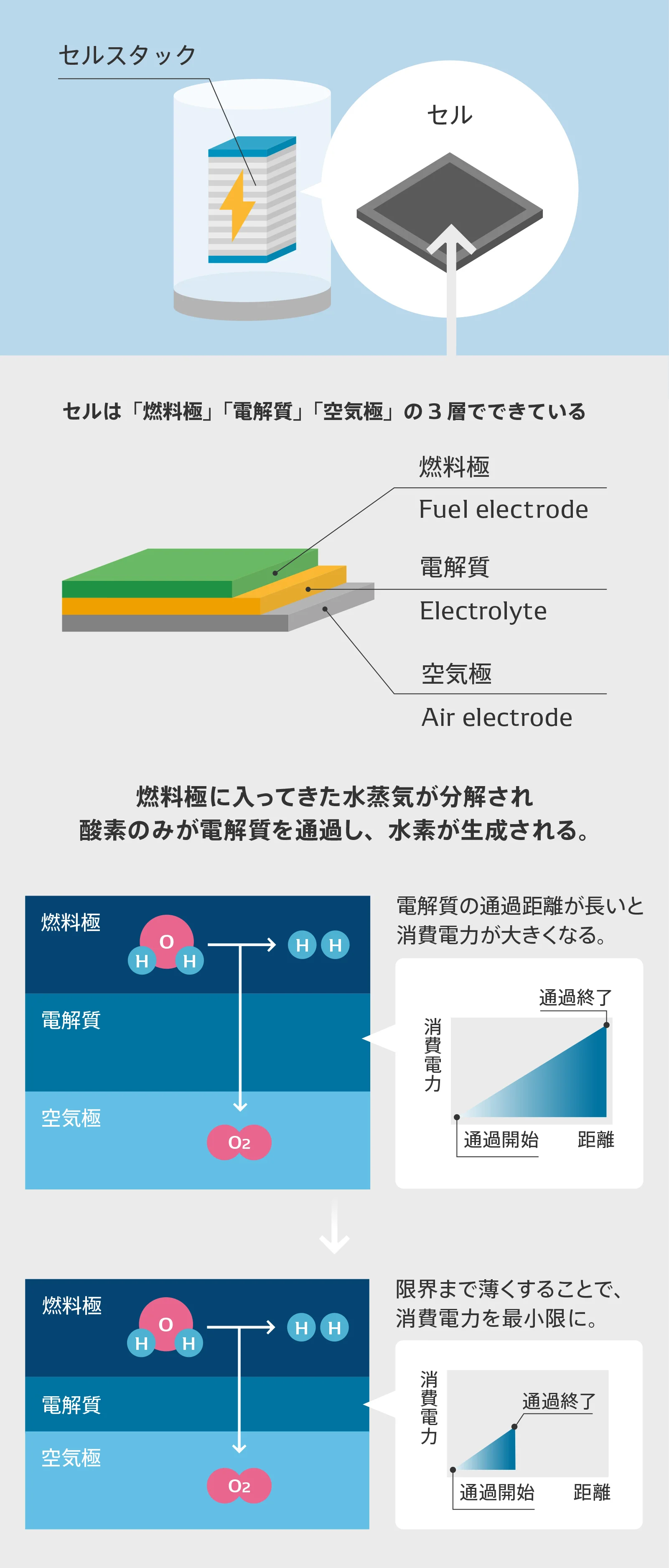
イオンの移動に伴う電力損失を低減させるために、SOECのセラミック積層体の薄さと緻密さを両立させなければなりません。デンソーはベース技術である排気センサーの部品もセラミック積層体で製造している強みを活かして、電力損失の低減と欠陥レスを実現させようとしています。「薄くする」というシンプルな目標ではありますが、そこに難しさがあると、セルの開発に関わる環境ニュートラルシステム開発部の人見卓磨は言います。
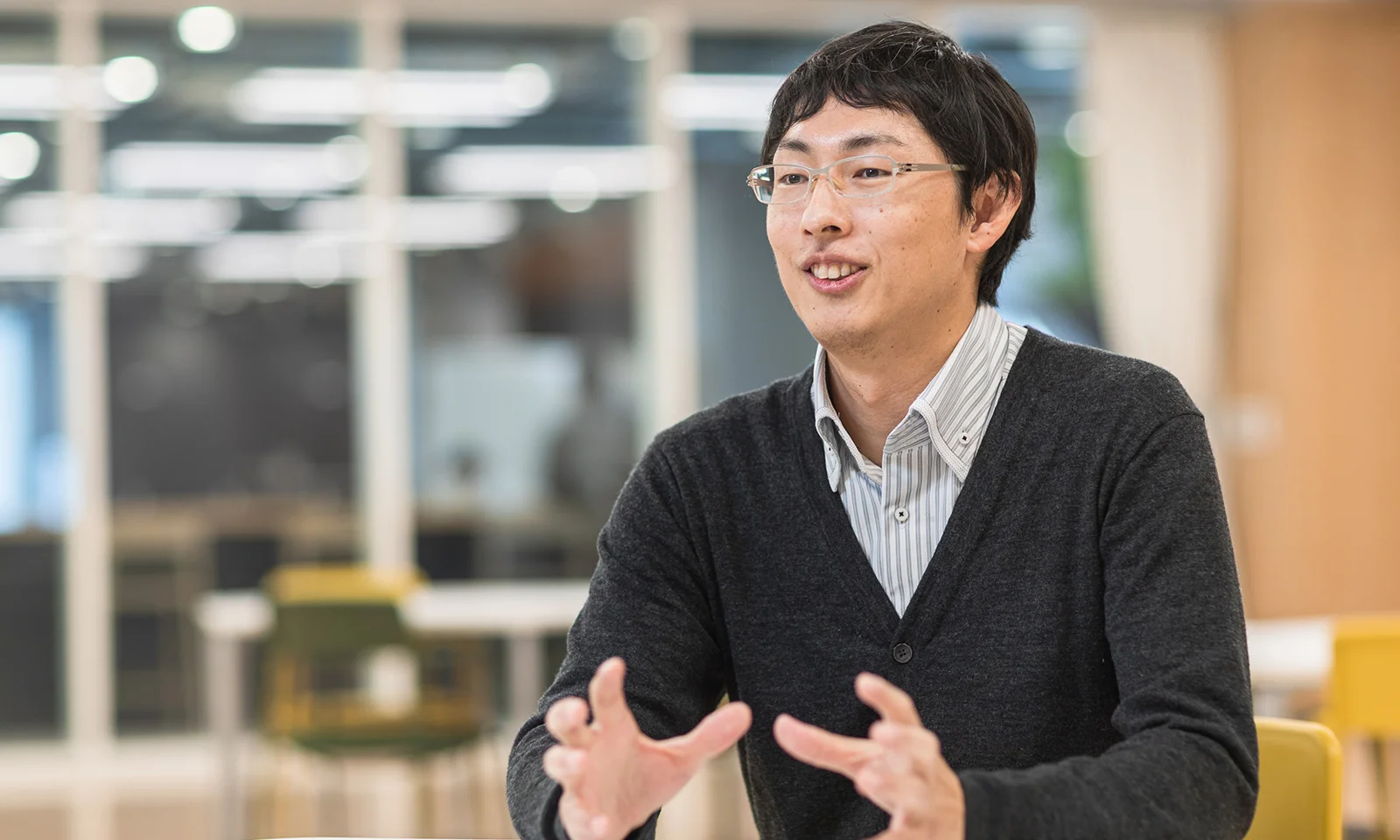
「セルを薄くすると電力の損失は減りますが、薄くすると穴が空きやすくなります。小さな穴でも、空いてしまうと反対側の電極にダメージを与えてしまいます。
そのセラミックの構造が緻密になるように並べるのですが、薄くすると手で持つことができないほど強度が下がってしまいます。そのため、セルを重ねて多層構造にした上で焼成します。ただ、重ねて焼くと層と層の間が変化し、抵抗成分ができてしまうという課題があります。
そのため、デンソーではセラミックを焼くことで生じる変化も分析しながら、様々なトレードオフのなかで、いかに薄く緻密な層にできるかというシンプルかつ難解な課題に挑戦しています」(人見)
こうした難度の高い開発を可能にしているのが、デンソーの持つ先端技術です。あいちシンクロトロン光センターにあるデンソー専用のビームラインなどを活用し、セラミックが出来上がるプロセスのなかで、元素レベルでなにが起きるのかという分析を行っています。
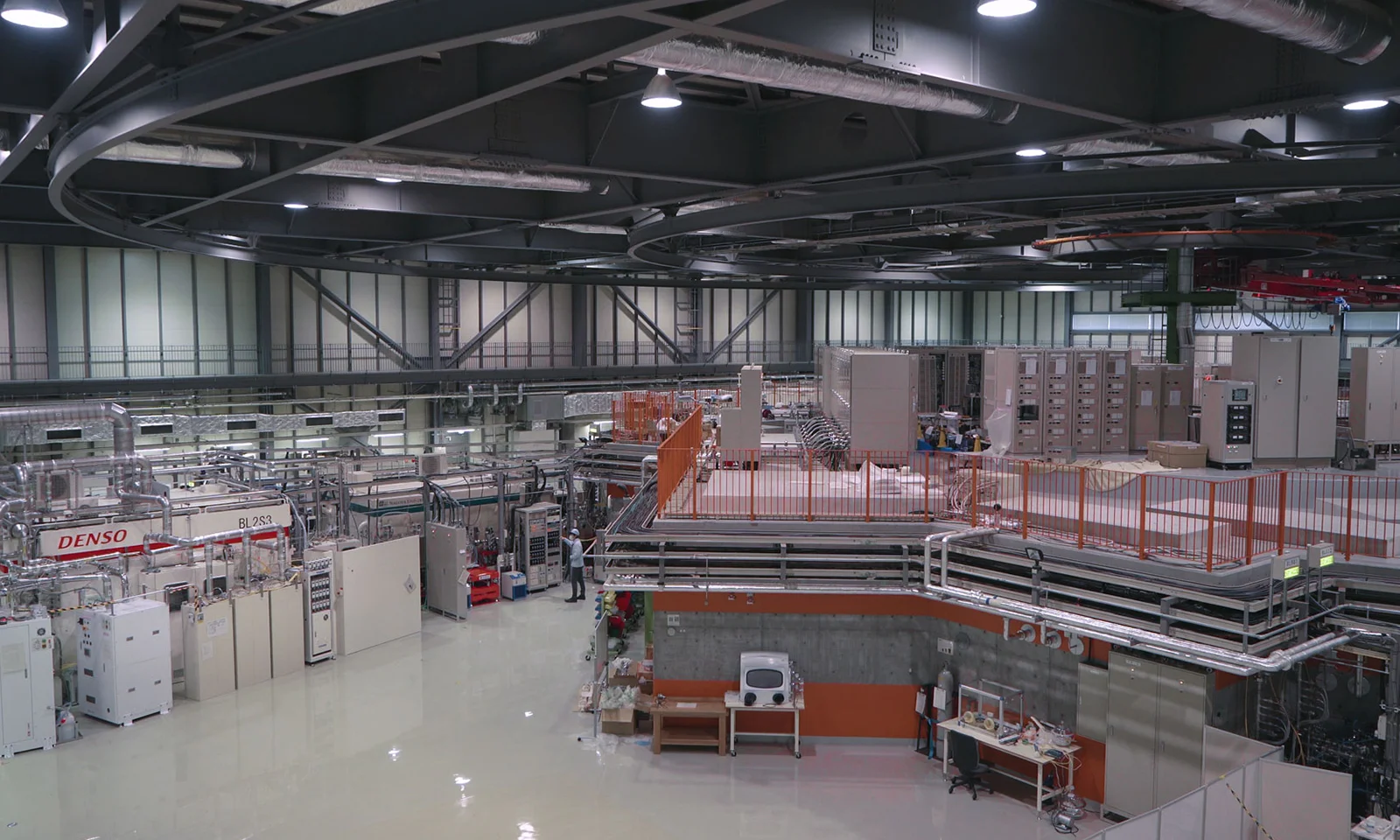
これに加えて、デンソーはセラミックの原料の調達、焼成、そして部品として組み立てるところまで一貫して生産を手掛けており、先端技術から生産技術まで備えていることがセルスタックの性能につながっています。
こうした強みを活かすと、現在のセルスタックのさらにその先も目指すことができると、人見は言います。
「SOECの温度がなぜ700℃なのかというと、イオン伝導体が700℃以下では急激に性能が落ちてしまうからです。それは、世の中で広く用いられているセラミック素材が持つ特性です。従来材料をベースに考えると700℃が目安になるのですが、デンソーは新たな材料を扱うことでさらに先を目指しています。
セラミックの材料を変えると、焼く工程ひとつとっても条件が変わってしまうので、普通は「材料変更をする」と意思決定を行うには大きなハードルがあります。
ただ、材料が変わっても、変わらない原理原則があります。デンソーは、ビームラインのように見えないものを可視化し、分析できる技術をいくつか持っているので、材料が変わってもある程度の指針が立てられるという強みがある。
デンソーの研究開発では、原理原則に則ったチャレンジが後押しされる文化があるので、通常の会社であれば拒否されるような材料変更というハードルにも挑めます」(人見)
カーボンニュートラルな未来を見つめ、SOECのさらなる進化を目指す
もちろん、こうした先端の開発はデンソーだけの力で実現できるものではありません。デンソーは、大学の研究室とも連携しながら、素材の開発に取り組んでいます。材料技術が進化すれば、水素製造と燃料電池が融合した新たな装置「SORC」の開発も視野に入ります。
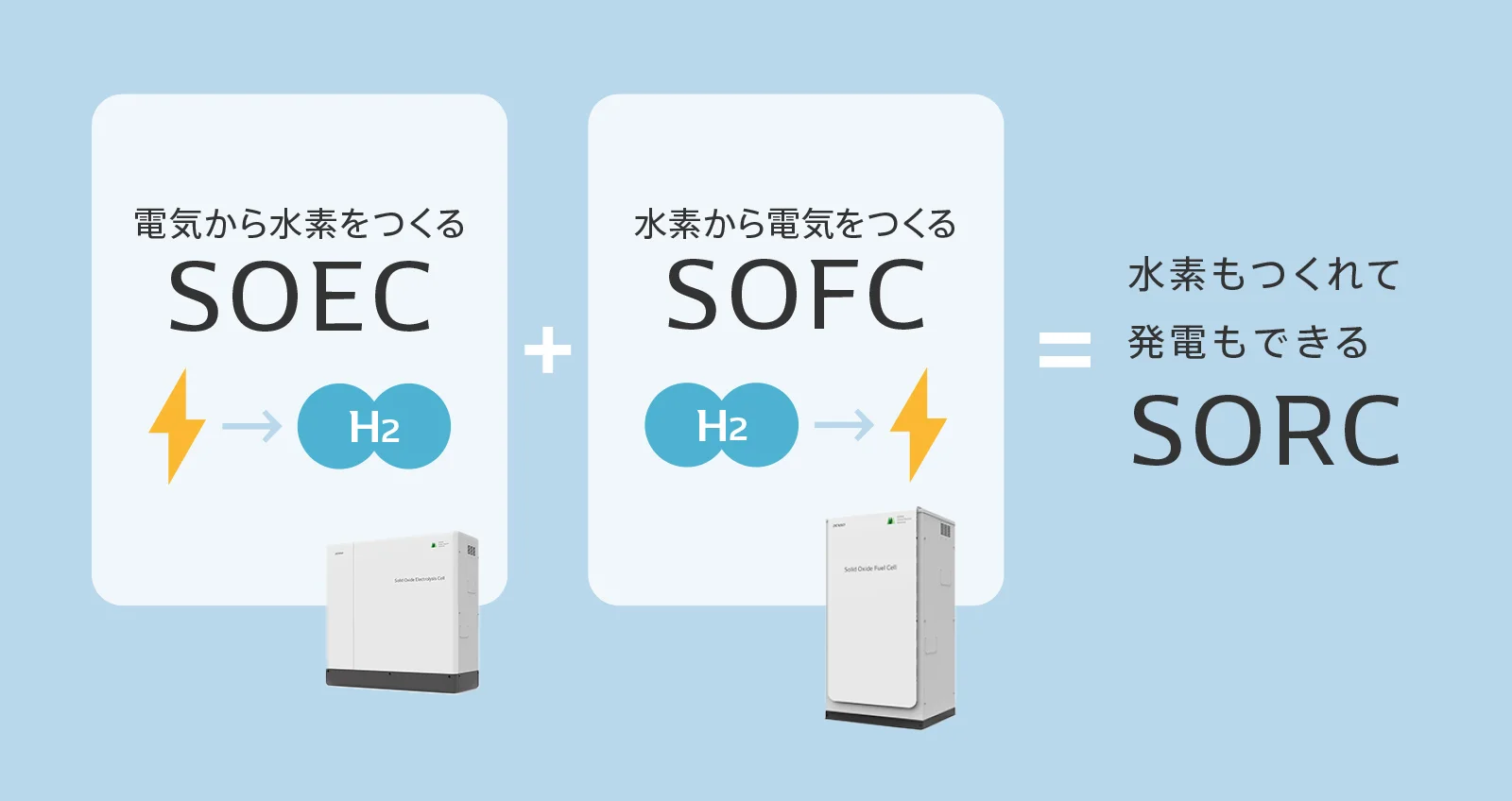
SOECを用いた共電解によって水素とCOを生成し、メタンを合成する技術もありますが、現在はまだ研究開発の段階です。SORCや共電解によるメタン合成などのSOECの未来を拓くには、材料技術は絶えず進化させる必要があり、様々なパートナーの皆さんとの連携は欠かせません。
デンソーでは、SOECの可能性を信じて、車載用セラミック製品、サーマル製品での開発・量産の知見や実績をベースに、技術課題の解決を目指しています。
「水素の利活用はカーボンニュートラルを実現していくには絶対に必要なものです。そのためには、水素の利活用が経済合理性のあるものにならなくてはいけません。SOECの開発を通じて、水素製造の経済合理性を実現して、地球規模の課題の解決に貢献したいという思いで開発に取り組んでいます」(渡邊)
SOECの可能性を引き出す挑戦はまだ始まったばかり。デンソーは、パートナーの皆さんと共に、SOECの技術課題を乗り越え、カーボンニュートラル実現に貢献していきます。
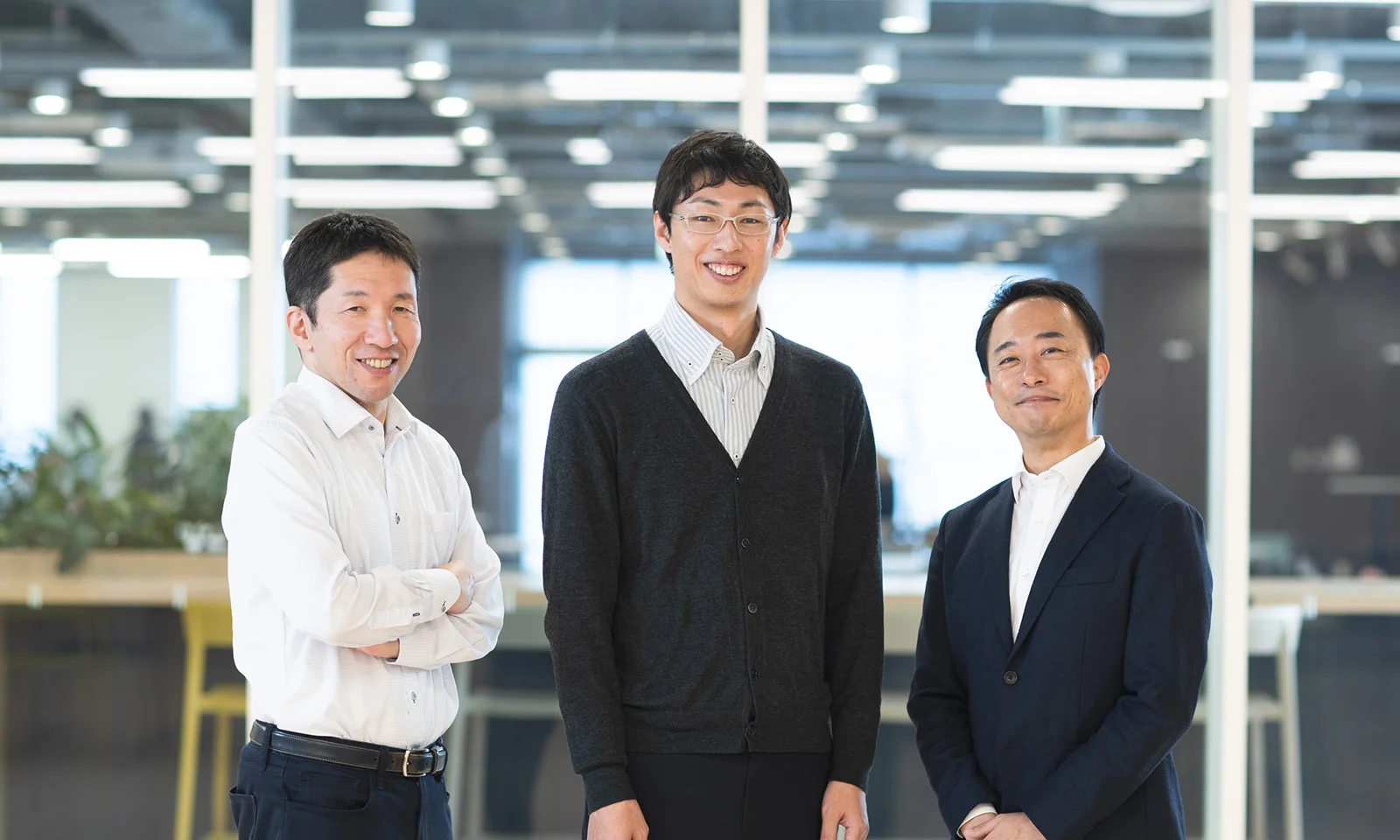
2023年1月25日から27日にかけて東京ビッグサイトにて開催する「グリーンファクトリーEXPO」にSOECを出展予定です。SOECの詳細について知りたい方は、ぜひ現地にお越しください。
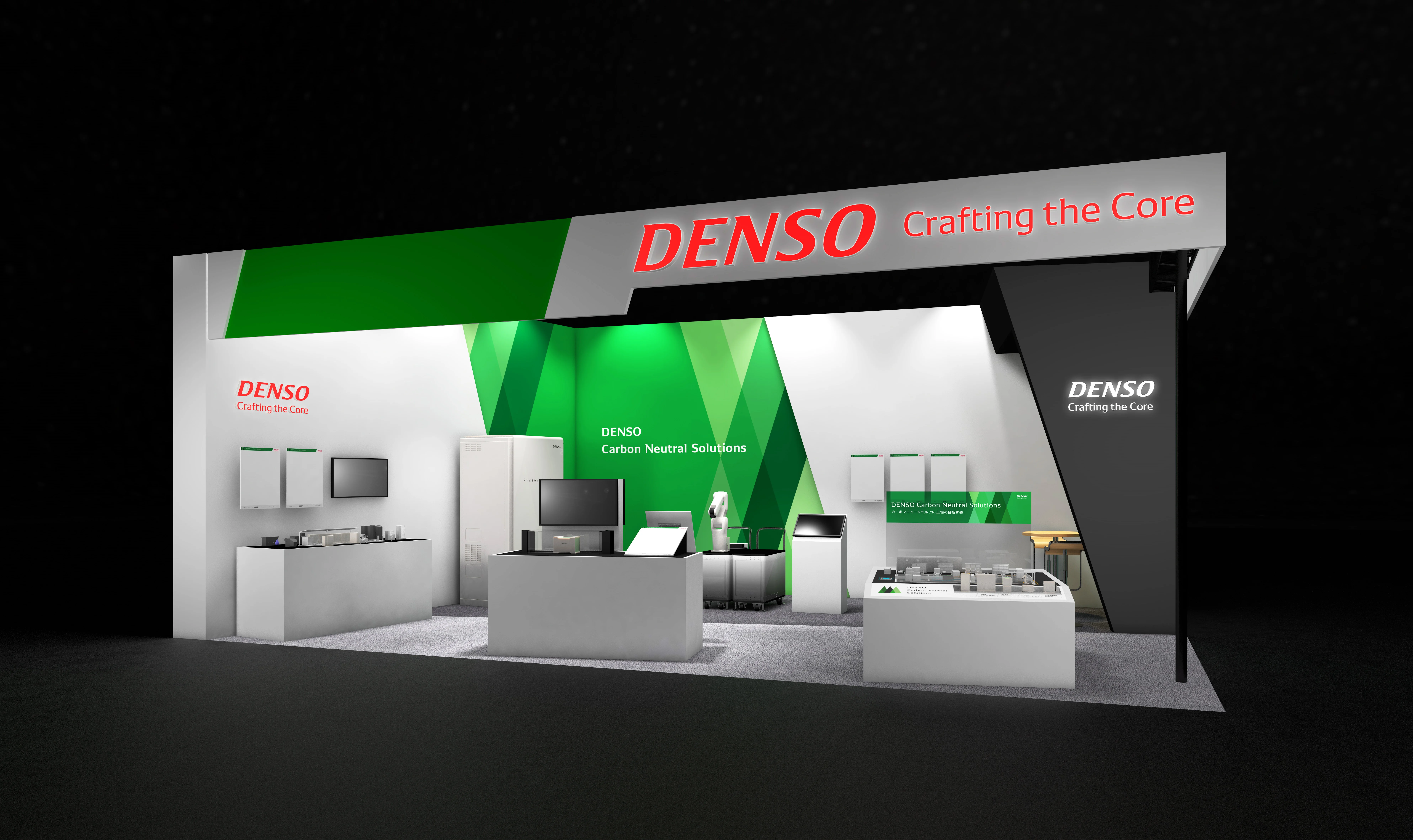
「できてない」 を 「できる」に。
知と人が集まる場所。