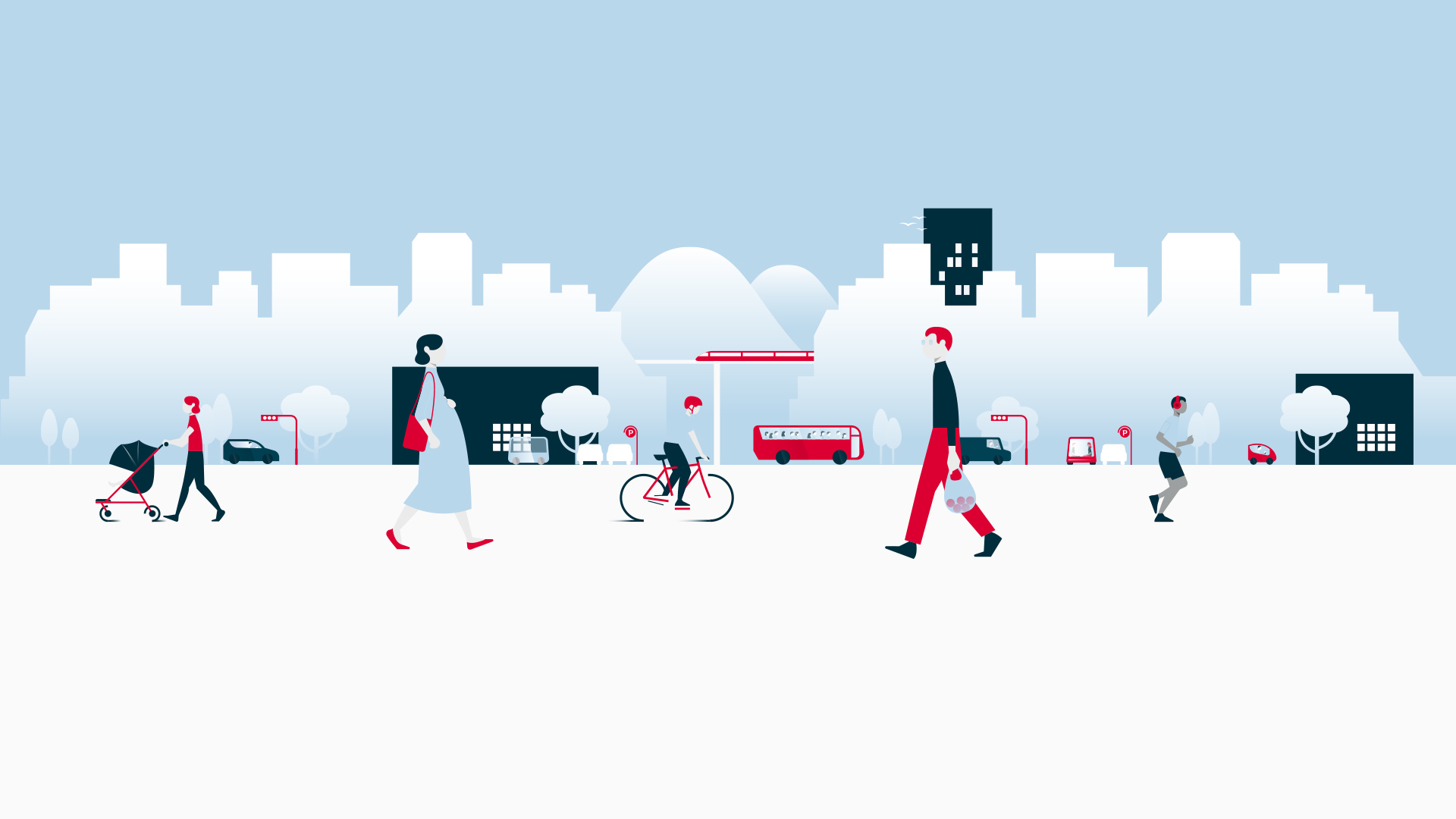
Page Not Found
Sorry, the page you have requested cannot be found.
It may no longer exist or your URL may be incorrect.
Please visit Home or Sitemap via link below.
Or enter keywords in the search field above.
Sorry, the page you have requested cannot be found.
It may no longer exist or your URL may be incorrect.
Please visit Home or Sitemap via link below.
Or enter keywords in the search field above.