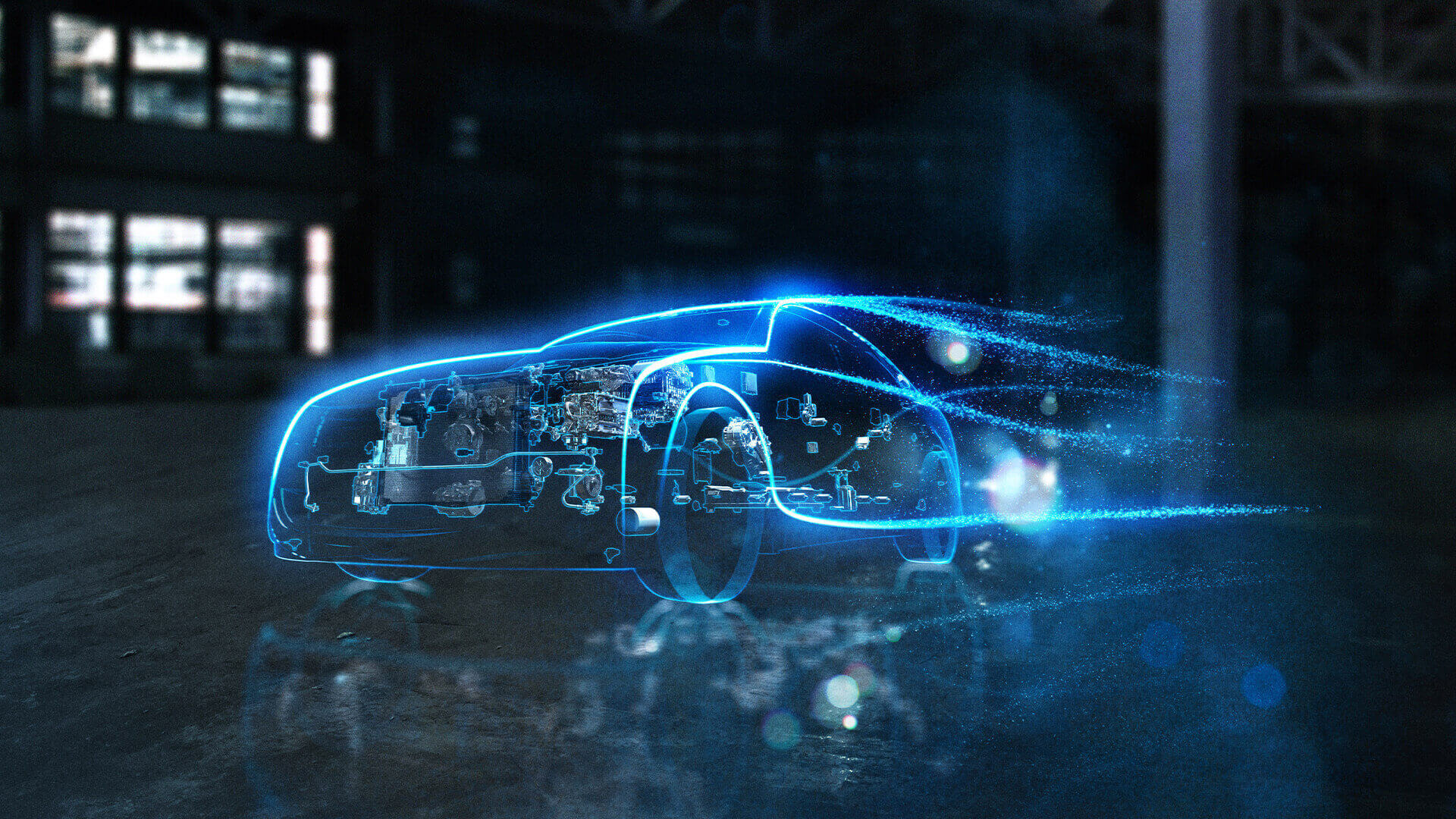
Innovation
Our people imagine new possibilities and create new value for the world.
-
Jul. 4, 2025
DENSO Acquires Axia Vegetable Seeds to Realize Sustainable Agriculture
-
Jun. 30, 2025
Six Companies Establish BlueRebirth Council to Expand Use of Recycled Materials in New Vehicles
-
May. 8, 2025
DENSO and ROHM Reach Basic Agreement to Establish a Strategic Partnership in the Semiconductor Field