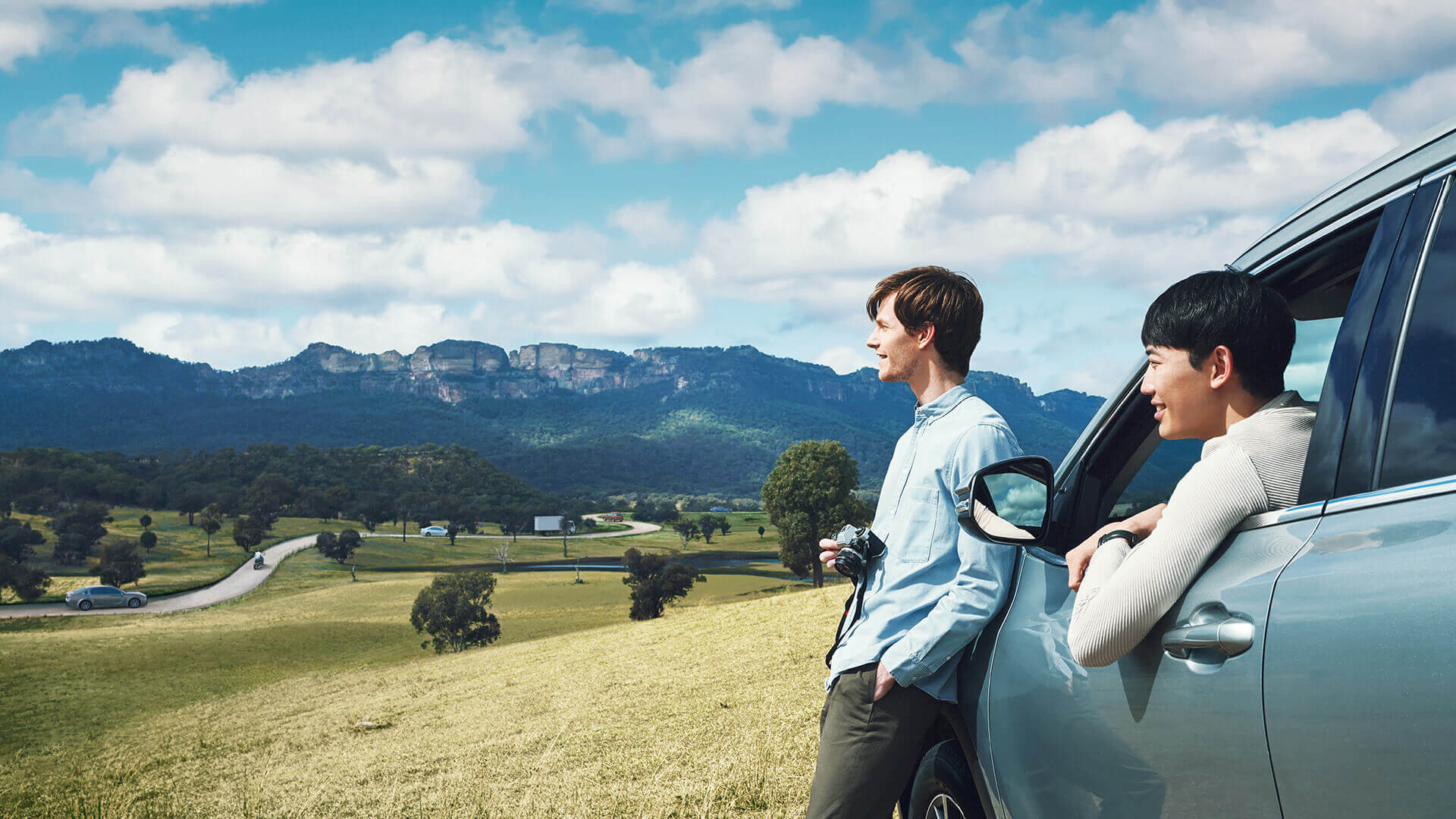
Sustainability
We do our best In order that people and the Earth remain healthy together
DENSO’s Sustainability Management
Here we introduce DENSO’s global Sustainability policy and promotion structure, specific initiatives, among other practices.
Environment
We at DENSO understand the tremendous responsibility of executing and leading in all business areas to do what we can to protect the fragile global environment.
Social
To realize sustainable societies, it is essential to engage in alliances, cooperation, and the sharing of values with many stakeholders.
-
Together with Our Suppliers
The DENSO Group's Procurement Policies
Promoting Sustainability throughout the Supply Chain
-
-
Governance
DENSO recognizes the importance of establishing corporate governance aiming for transparent and efficient corporate management and is engaged in highly sound, efficient, and transparent management.